While a wide range of products can be designated as adhesives, there are critical differences between them. High-temperature (HT) adhesives are complex, highly durable, and the product of choice for service environments over 100 °C. Meanwhile, fast-drying glues commonly found on store shelves will only function at ambient temperature (10-30 °C), up to approximately 50 °C.
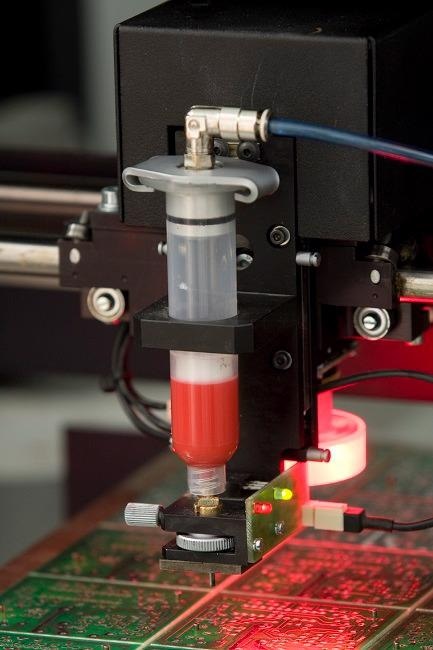
Image Credit: Jayhawk Fine Chemicals Corporation
HT adhesives’ heat-withstanding properties make them an ideal solution for transportation, technology, aerospace, and energy applications. Their capacity to perform under temperatures as high as 300 °C means that polymer HT adhesives are also suitable for use in space-bound satellites.
HT adhesives are classified as either one component (1K) or two (2K) components. 2K adhesives are common (particularly those based on epoxy resins) and are typically manufactured using a dianhydride thermal curing agent.
Cured adhesives are highly heat resistant due to the combination of a dianhydride, an epoxy resin, and the heat necessary for curing. These adhesives also weigh considerably less than mechanical fasteners such as nuts and bolts, distributing joining forces uniformly across substrates and ensuring efficiency in the joint design.
This article explores six key factors that make HT adhesives unique.
1. High-Temperature Adhesives are not Available at Big Box Stores.
HT adhesives are generally only available from business-to-business providers. Big box stores offer retail products including Krazy Glue, Elmer’s Glue, and 5-Minute Epoxy, but fast-drying, ambient-cure adhesives such as these are only designed for the home consumer market. This market places value on ease-of-use, but these products are not robust enough for use in demanding industrial settings that require more heat-resistant alternatives.
HT adhesives’ sophisticated chemistry means that they require a great deal more care in handling than ambient-cure adhesives, with personnel often requiring specific training in substrate preparation and surface cleaning both prior to and during application.
2. High-Temperature Adhesives are Found in Many Familiar Applications, Despite Their Specialist Nature.
While the design of HT adhesives may be challenging, these adhesives are vitally important to many industrial, commercial, and manufacturing applications. HT adhesives are employed in a wide range of electronic devices, including watches, phones, televisions, and computers, with specific applications ranging from semiconductors, sensors, and circuit boards to glass display screens.
HT adhesives are also essential to the development of transportation, including cars, boats, motorcycles, trucks, and most recently, e-mobility.
HT adhesives are also commonplace throughout the aerospace industry, with application areas including rockets, missiles, satellites, planes, and drones.
HT adhesives can be designed to incorporate additional features through proper formulating. Their ability to be either electrically insulative or conductive and their extreme temperature resistance make these adhesives essential for use in motors, batteries, and a variety of electrical components.
HT adhesives are also widely used in the energy sector, for example, binding the components of photovoltaic cells - a central component of solar panels.
3. Ambient-Cured Adhesives are not Designed for Use at High Temperatures.
General-purpose adhesives do not perform well at high temperatures because their chemistry is only designed to cure at ambient temperatures - they will lose their strength and fail to hold the adhesive joint as service temperature increases.
HT adhesives are designed differently, however. Curing HT adhesives with heat causes them to reach a high level of chemical crosslink density, affording them high-temperature performance. This is often denoted by their glass-transition temperature.
4. High-Temperature Adhesives Have the Potential to be Surprisingly Durable.
HT adhesives’ high chemical crosslink density makes them suitable for even the most challenging applications and conditions. As well as retaining their strength while being exposed to extreme service temperatures, HT adhesives are also able to resist chemical degradation from long-term exposure to environmental factors such as oxygen, heat, corrosive chemicals, water or moisture in the air.
When appropriately designed and cured, HT adhesives are able to withstand these aggressive environments due to their excellent thermo-oxidative stability (TOS). They are also highly resistant to chemical attack or hydrolysis.
Through careful customization of the HT adhesives’ specific formulation, designers can ensure they have adequate strength, durability and stiffness for their intended application.
5. High-Temperature Adhesives are Versatile.
HT adhesives are extremely versatile, not least because of their ability to be either electrical conductors or insulators. HT adhesives can be formulated to conduct electricity, allowing for sensitive and durable interconnections when employed in printed circuit boards (PCB).
In contrast, flexible, copper-clad laminates (FCCLs) used in smartphones require layers of electrical circuitry to be kept separate. HT adhesives can be designed to provide electrical insulation in these applications and in both of these examples, HT adhesives are able to withstand exposure to electrical voltage.
The same principle applies to heat management, particularly in smartphones and computers, where limiting internal heat build-up is essential. Thermally conductive adhesives can help dissipate warmth to air or the device’s external surfaces, facilitating uninterrupted operation and extending the lifespan of these always-on devices.
In instances where heat must be prevented from reaching a specific area of the adhesive assembly, the use of a thermally insulative adhesive can effectively block heat flow while tolerating the high heat itself.
6. Ad-Hoc Remedies are not Suitable Substitutes for High-Temperature Adhesives.
Properly engineered 2K HT adhesives are formulated using carefully chosen raw materials in exact proportions; for example, a combination of an epoxy resin and dianhydride curing agent. The effectiveness of each HT adhesive will also depend upon a proper combination of curing time and temperature.
Formulators that are not sufficiently experienced in HT adhesive chemistries may underestimate the amount of detail required in the design of such products. While a product may appear to perform well initially, the bond's endurance cannot be confirmed without adequate stress testing.
Formulators are often tempted to add new ingredients into a known formulation, but this approach often results in avoidable complexities and a suboptimal solution. A more optimal approach would be to start from scratch, selecting the most appropriate materials for the adhesive application in question.
Jayhawk Fine Chemicals Corporation team possesses an in-depth understanding of both the science behind high-temperature adhesives and experience in formulating them to accommodate the highest performance standards.
N.B. All product names, logos, brands, and trademarks are the property of their respective owners.

This information has been sourced, reviewed and adapted from materials provided by Jayhawk Fine Chemicals Corporation.
For more information on this source, please visit Jayhawk Fine Chemicals Corporation.