Petrochemical and petroleum refining industries continue to be crucial to the global economy. They provide products like gasoline, heating fuel, diesel, fertilizers, solvents, rubber, plastic, detergents, cosmetics and a number of other indispensable consumables.
Petrochemical plants and refineries may be considered among the most prized industrial assets in the world. The hydrocarbon processing business is also an industry with high numbers of hazards; there are potential exposures to risk in all operations because of the nature of the materials being extracted, transported and processed.
Health and safety continue to be paramount for the petrochemical and petroleum refining industry, and the emphasis for process safety management (PSM) and asset integrity is to stop any unplanned releases which could lead to a major accident.
A huge effort has been focused on minimizing the risk of personnel exposure and equipment loss in the global oil and gas industry by stopping the release of toxic substances and highly hazardous chemicals.
At refineries, chemical plants and gas processing facilities, fatal accidents and injuries, in addition to loss of property, premature pipe replacements, leaks and unplanned outages can usually be traced back to inadvertent substitution of construction materials. Equipment failures are the main cause for losses at chemical plants, refineries, pipeline networks and gas processing facilities.
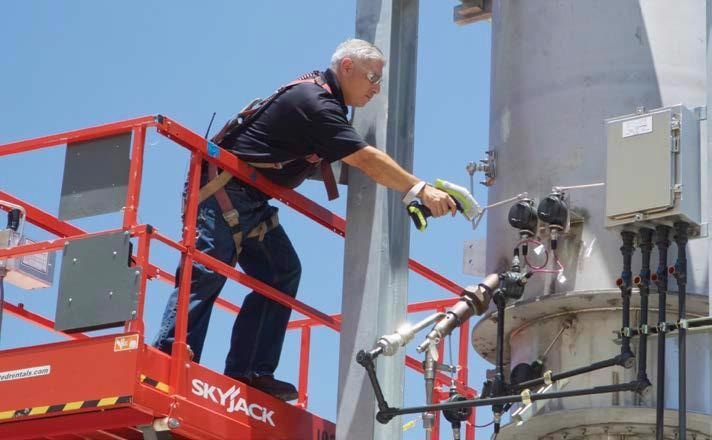
A technician performs positive material identification on pressure vessel components using the Thermo Scientific Niton XL5 Plus analyzer. Image Credit: Thermo Fisher Scientific - Elemental Analyzers and Phase Analyzers
Mechanical Integrity (MI) is always a contributing factor and enforcement policies like 29 CFR 1910.119 “Process Safety Management of Highly Hazardous Chemicals” issued by the United States Occupational Health and Safety Administration (OSHA) outline certain requirements for minimizing or preventing the consequences of catastrophic releases.
Policies were launched to safeguard against catastrophic releases under OSHA’s National Emphasis Program (NEP):
- Enforcement Directive Number CPL 03-00-004 effective June 7, 2007
- Petroleum Refinery Process Safety Management National Emphasis Program and Directive Number CPL 03-00-014 effective November 29, 2011
Application
Industry-reported data indicates that as much as 3% of rogue material will make its way into the field as part of a final piping circuit, fabricated assembly, pressure vessel or other critical process equipment.
There are numerous undesirable paths of travel that an inadvertent material substitution may have as routes of entry, such as:
- A welder using the incorrect filler metal by choosing the wrong rod box, improper stocking or labeling of inventory or borrowing weld rods from someone else
- Material traceability is not maintained during fabrication when a number of pieces are created from a single stock (i.e., stiffener rings, gussets, lift lugs, support clips, gasket rings, pipe pups)
- Component manufacturer uses the wrong material to stamp the finished part
- During the fabrication process, the fabricator utilizes unmarked, unknown material (i.e., loose stock, cutouts, drops)
- Maintenance that happens outside normal operating hours is not subjected to usual QA/QC inspection practice
- Warehouse stocks inventory in the wrong location and the error gets carried forward
- Incorrect tagging or marking of materials during maintenance removal and lack of verification prior to re-installation
- A pipefitter or welder chooses the wrong component during the fabrication process
- As ownerships exchanges and data is transposed or even manipulated, the integrity of the original mill test report (MTR) is compromised during the procurement and supply cycle
The U.S. Chemical Safety and Hazardous Investigation Board (CSB) report No. 2005-04-B provides a lesson learned after an incident investigation of a major fire at one of the nation’s largest refining complexes, which caused a reported $ 30 million in property damage and minor injuries.
Positive Material Verification Programs
An inexpensive, accurate and fast PMI test technique is in-situ alloy steel material verification via X-ray fluorescence or other non-destructive material testing.
Facility owners, operators and maintenance contractors must make sure that the verification program requires PMI testing, as specified in American Petroleum Institute Recommended Practice (API RP) 5781, or other suitable verification process, for all critical service alloy steel piping components which are removed and reinstalled during maintenance.2
The inadequacy of material composition was discovered to be the key component of failure in 9 of 99 significant refinery accidents, as found in one study which explored corrosion-related accidents in petroleum refineries in both the European Union (EU) and Organization for Economic Cooperation and Development (OECD) countries’.
Experience and history demonstrate that inadvertent material substitutions are still a considerable problem in the refining and petrochemical industry. However, applying the principles and guidelines published in recommended practice API RP 578 “Material Verification Program for New and Existing Alloy Piping Systems” supports applying Recognized and Generally Accepted Good Engineering Practices (RAGAGEP) in instituting an effective material verification program (MVP).
Owner-users who use a 100% PMI practice for pressure-containing components and welds for new construction materials, in-service equipment, or during maintenance activities can decrease the likelihood of material mix-up significantly and avoid the consequences of failure while mitigating corporate risk.
Sulfidation corrosion continues to be a significant cause of leaks in the refining industry as it affects steel piping and equipment. Carbon steels with low silicon content (<0.10%) can corrode at an accelerated rate when exposed to hydrocarbons containing sulfur compounds at elevated temperatures.
Sulfidation thins the pressure boundary wall and can lead to a leak that releases highly hazardous chemicals into the atmosphere.
API RP 939C “Guidelines for Avoiding Sulfidation (Sulfidic) Corrosion Failures in Oil Refineries” recognizes implementing Retrospective PMI into a Material Verification Program (per API RP 578) as an inspection technique that can be used to detect and track sulfidation corrosion.3
In the refining industry, HF alkylation is becoming a more popular process for the production of petrochemical products. The main materials of construction are copper-nickel, carbon steel, Monel™ 400 (trademark of Special Metals Corporation) and other nickel-based alloys like Hastelloy™ C-276 and B-2 (trademark of Haynes International).
The correct selection, application and placement of the alloys within the process piping envelope is vital in order to avoid unexpected corrosion and deterioration of pressure equipment components.
When residual element (RE) content is controlled, carbon steel in the HF alkylation process has shown satisfactory corrosion resistance to HF corrosion. Case studies have demonstrated that REs in carbon steel can add to accelerated HF corrosion, particularly elements Cu, Cr, and Ni.
One guideline which is recognized is that for base metal of C> 0.18% wt% and Cu + Ni + Cr, 0.15% wt% is optimum. As the concentrations and type to be measured will directly influence the analytical technique operations to use, these values are critical.4
One quick and accurate non-destructive testing technique that supplies confirmation of alloy composition to material specifications and positive grade identification is handheld X-ray fluorescence (HHXRF).
HHXRF confirms QA/QC for in-process fabrication; provides positive proof that the right materials are received; meets end-user material needs for outgoing products and that installed components and welds match the engineering design and application for which they are intended.
For the most reliable data and best performance, the operator should carefully consider the most suitable surface preparation techniques, grinding media and tools for the task.
Thermo ScientificTM NitonTM XL5 Plus XRF Analyzer
The new Niton XL5 Plus is the lightest and smallest high performance XRF alloy analyzer in the market. It couples world-class performance with its lightweight and smaller size, allowing access to more test points that are usually inaccessible to larger HHXRF equipment while minimizing operator fatigue.
A new, powerful mini X-ray tube and a compact measurement geometry supply the highest performance and best light element sensitivity for the most demanding applications like low silicon measurement.
Niton XL5 Plus Analyzer supplies quick and accurate elemental analysis in demanding refinery environments and provides the refining industry with the key benefits below:
- A flexible user interface permits easy optimization and custom workflow solutions for specific applications like low silicon measurement, residual and trace element analysis
- Even while wearing gloves, tilting, swiping and vivid touch screen display can be utilized
- Best in class miniaturized 5W X-ray tube supplies the highest performance level and best light element sensitivity
- Large, state-of-the-art silicon drift detector high count rate with graphene window gives outstanding light element detection (Si, P, Mg, Al, S)
- Integrated 1.2M micro and 5M macro cameras and small spot analysis for accurate sample positioning and image capture for enhanced reference and data integrity
- Extended field utilization with hot swappable battery and battery life indicator display
- Smallest HHXRF increases productivity by allowing testing in tights spaces and internal components
- Lightest HHXRF at 2.8 lbs (1.3 kg); designed for better user comfort and balance without operator fatigue
- Rugged housing is dustproof and waterproof for harsh environments
- Unparalleled chemistry and grade identification accuracy for confident results every time
The Niton XL5 Plus Analyzer is designed with a rugged aluminum housing, dissipating primary heat sources from within the analyzer. Electronic fail-safe protection is used for internal temperature monitoring and control, preventing the analyzer from overuse by suspending measurement activity until cooled to a safe working temperature.
The Niton XL5 Plus Analyzer takes advantage of its increased component interface and smaller size by providing a new miniature Hot Work Standoff, enabling standard operations at high testing temperatures without impeding the higher value of component accessibility.
Enabling a maximum sample temperature of 900 °F (480 °C) as it is equipped with a KaptonTM window (Kaption is a trademark of E. I. du Pont de Nemours and Company), the new Hot Work Standoff easily snaps in place with an improved, toolless window bracket design.
It is crucial to consider that the user should wear appropriate personal protective equipment (PPE) when performing sample measurements and surface preparation at high temperatures.
Ideally suited for rope access PMI inspection, the Niton XL5 Plus Analyzer provides technicians with a smaller footprint and decreased weight burden, which usually takes up valuable space whether attached via lanyard or secured in a backpack.
Conclusion
Aging infrastructure usually brings with it the challenge of in-situ or retro-PMI testing to confirm existing assets are fit for service.
Usually, this requires carrying out measurements at higher temperatures under normal process operating conditions between 200 °F and 900 °F. Conditions such as these require an analyzer that meets all of the demanding aspects of retro-PMI testing.
The Niton XL5 Plus XRF Analyzer is purpose-built and designed specifically to perform in this harsh environment with a feature set that makes it the instrument of choice for petrochemical, refinery and all other process facility inspectors who need the best tool for the job.
With the highest analytical performance available in a rugged, well-balanced package, together with a considerable reduction in size and weight, the Niton XL5 Plus Analyzer is a product driven by industry demand and client input. It is designed to meet the requirements of asset owners from all industry segments, from refining and petrochemical to gas processing, power generation, offshore and pipeline transportation.
References
- API RP 578 – Material Verification Program for New and Existing Alloy Piping Systems
- “Safety Bulletin,” U.S. Chemical and Safety Hazard Investigation Board, CSB report No. 2005-04-B, October 12, 2006, page 7.
- API RP 939C – Guidelines for Avoiding Sulfidation (Sulfidic) Corrosion Failures in Oil Refineries
- API RP 751 – Safe Operation of Hydrofluoric Acid Alkylation Units
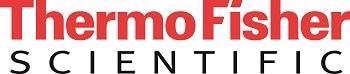
This information has been sourced, reviewed and adapted from materials provided by Thermo Fisher Scientific - Elemental Analyzers and Phase Analyzers.
For more information on this source, please visit Thermo Fisher Scientific - Elemental Analyzers and Phase Analyzers.