Metal coatings are applied on all kinds of items made of alloys, metals and plastics. These are used either for decorative platings or to enhance the chemical and physical properties of their surface (wear and heat resistance, corrosion, hardness, electrical conductivity, solderability, adhesion, or lubricity).
Undercoating can lead to dramatic product failure and overcoating can increase the cost of manufacturing significantly. Controlling the coating thickness or coat weight is vital for metal finishing, fabrication, aerospace and automotive industries.
Among available technologies for the measurement of metal coat weight, X-ray fluorescence (XRF) spectrometry has a number of benefits: it is element specific and non-destructive, and it gives extremely accurate results.1
While XRF is able to measure the coat weight of metal layers, the technology is generally not suitable to measure the thickness of organic coatings, as elements such as carbon, oxygen or hydrogen can't be detected. For a number of years, this was addressed by bringing the specimen to be analyzed inside or close to the analyzer chamber so that it could be analyzed by benchtop XRF.
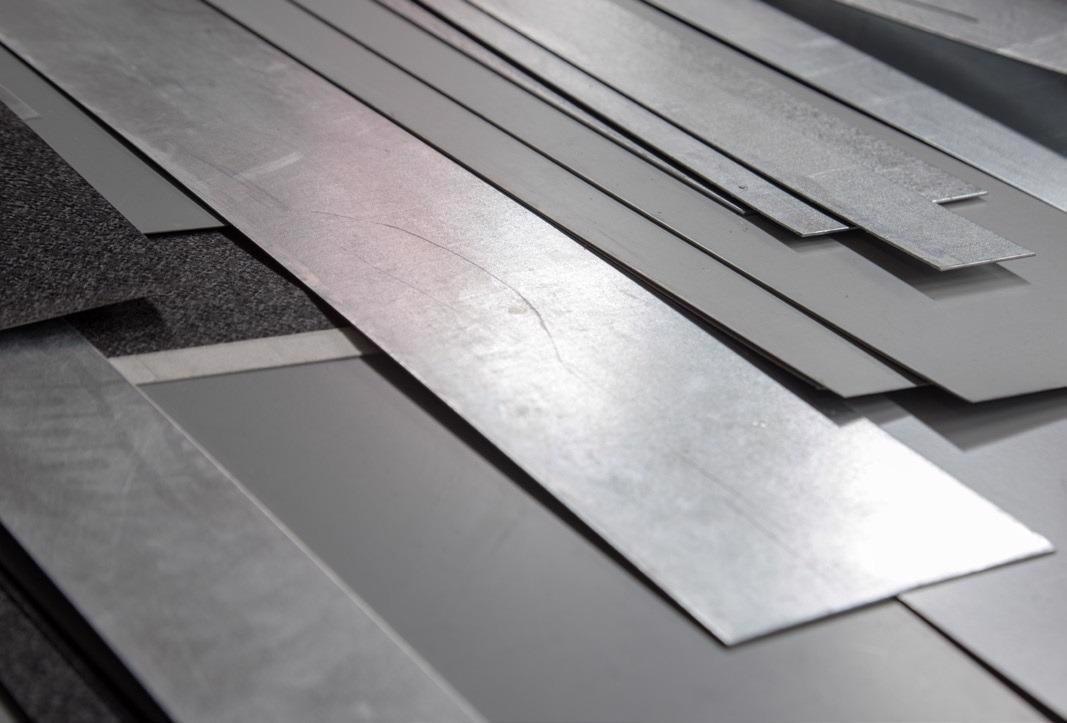
Image Credit: Thermo Fisher Scientific - Elemental Analyzers and Phase Analyzers
Without cutting samples, measuring coating thickness on heavy or large parts is impractical, and handheld XRF can be used to overcome this limitation. The lightest, smallest and most powerful tube-based handheld XRF analyzer, the Thermo Scientific™ Niton™ XL5 Plus, measures the coat weight or coating thickness of metals accurately in seconds.
The non-destructive analysis is performed directly at-line for process control or on-site for finished products. Operators are able to directly analyze heavy and large parts, improving efficiency and increasing productivity.
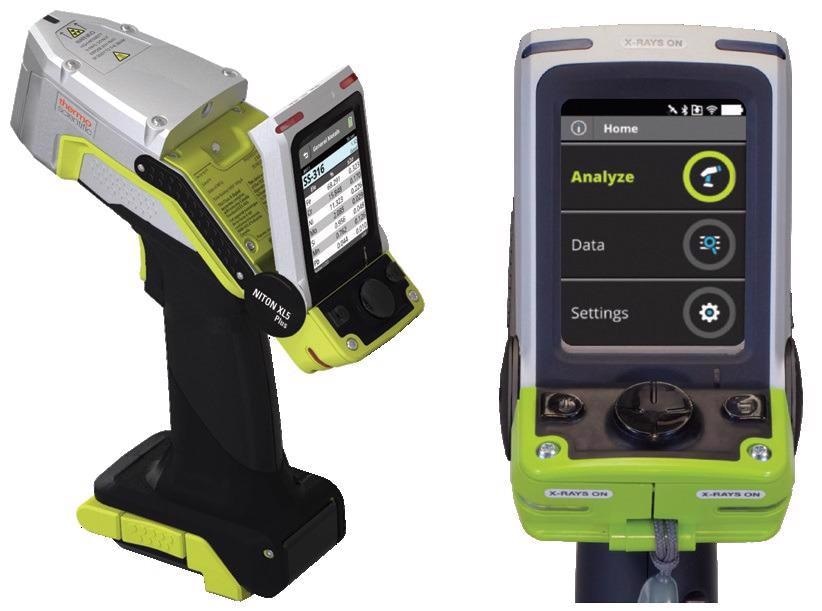
The Niton XL5 Plus Handheld XRF Analyzer. Image Credit: Thermo Fisher Scientific - Elemental Analyzers and Phase Analyzers
Instrument Features & Analytical Technique Set Up
The Niton XL5 Plus is an advanced handheld energy dispersive XRF analyzer which has:
- A proprietary miniaturized 5W (5-50 kv/5-500 µA) Ag-anode X-ray tube
- A large silicon drift detector with graphene window for enhanced light element detection
- An optional 3 mm small spot collimator to analyze small sized samples
- A standard spot size of 8 mm to analyze large areas and compensate for micro heterogeneities
- A micro camera to visualize and document the analyzed area
- A macro camera to take a sample image for enhanced record keeping
- ProGuard detector protection to stop window puncture
By utilizing a proprietary fundamental parameter (FP) based algorithm, the Niton XL5 Plus analyzer is versatile and handles an infinite amount of situations without having to calibrate the analyzer using reference standards.1,2
The Niton XL5 Plus analyzer can measure the coating thickness or coat weight of up to four layers over one substrate. The substrate can be defined as either alloy, metal, wood or plastic, while the layers can be defined as alloy, pure element, or compound (via pseudo element).
For coatings analysis, the analytical technique development with the Niton XL5 Plus analyzer is intuitive and simple. The user chooses the number of layers and enters the composition of layers and substrates by utilizing a list of elements or available alloy libraries according to AISI/ASTM, DIN or GB standards, as seen in figure 1.
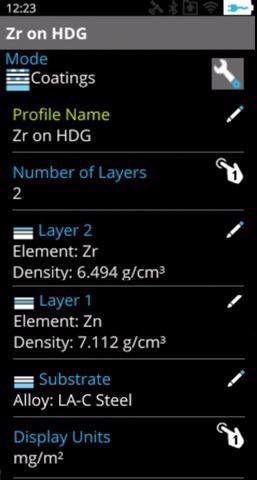
Figure 1. Excerpt of a user-defined profile (analytical method). Image Credit: Thermo Fisher Scientific - Elemental Analyzers and Phase Analyzers
The instrument is ready to be used after this analytical technique is stored in a profile. The Niton XL5 Plus analyzer enables operators to configure, store and call as many profiles as required.
Capabilities and Examples of the Application of the Niton XL5 Plus Coatings Mode
Table 1 shows the capabilities of the Niton XL5 Plus Coatings Mode with coated materials employed for numerous purposes in different applications and industries.
Table 1. Measurement capability examples and applications of Coatings Mode on the Niton XL5 Plus analyzer. Source: Thermo Fisher Scientific - Elemental Analyzers and Phase Analyzers
Measurement Capability |
Coating Example |
Purpose or Improved Property |
Industries, Application |
Single mono-elemental layer over pure metal* or a non-metal substrate |
Ag / Cu
Zn / [Steel]
Cd / [Steel]
Cu / [Plastic] |
Electrical conductivity
Corrosion resistance
Corrosion resistance
Metal coating primer |
Electrification products
Various metal fabrication
Aerospace, Military
Various metal fabrication |
Multiple mono-elemental layers over
a pure metal* or a non-metal substrate |
Au / Ni / Cu/ [Zn]
Cr/ Ni / Cu / [Plastic]
Ti / Zn / [Steel]
Zr / Zn / [Steel] |
Decorative
Decorative
Corrosion resistance
Corrosion resistance |
Accessories and apparel
Fabrication, fixtures
Fabrication, automotive
Fabrication, automotive |
Single mono-elemental layer over alloys |
Cr / [Stainless steel]
Rh / [White gold]
Rh / [Brass]
Ti / [Al alloy]
Zr / [Al alloy]
Cr (VI) / [Alloys**] |
Wear and corrosion resistance
Decorative
Decorative
Corrosion resistance, paint primer
Corrosion resistance, paint primer
Corrosion resistance, paint primer |
Various metal fabrication
Jewelry
Accessories
Fabrication, Automotive
Fabrication, Automotive
Various metal fabrication |
Multiple layers over alloys |
Cr /Ni/ [Brass] |
Decorative |
|
Alloys as coatings over pure metals |
NiP / [Steel]
NiP / [Al]
ZnNi / [Steel] |
Wear and corrosion resistance
Wear and corrosion resistance
Corrosion resistance |
General fabrication
General fabrication
Automotive, Aerospace |
Alloys as coatings over alloys |
NiP / [Kovar] |
Wear and corrosion resistance |
Glass sealing |
Compound layers using tracer elements |
P2O5 / [Steel]
TiN / [Tool steel] |
Corrosion, paint primer
Hardness, wear resistance |
Fabrication, Automotive
Cutting tools |
*In many cases for electroplated items, low alloy steel can be approximated as pure iron **Al, steel, Cu, Zn alloys
Any combination of metal coating can be analyzed using the Niton XL5 Plus analyzer; the list of examples is not exhaustive. It can be analyzed as long as the composition of the coating layer(s) and the substrate are not identical and the thickness of the coating layers does not exceed a critical value, known as infinite thickness.1,2,3
When the signal from the substrate or a layer is totally absorbed by an intermediate layer or the layer itself, the infinite thickness is reached. Results of analysis from three real-world examples can be seen in Figure 2.
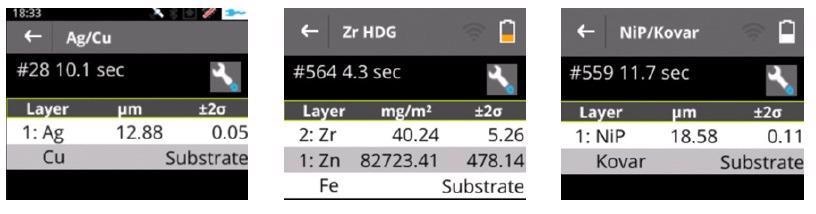
Figure 2. Examples of measurements obtained “out of the box” using Niton XL5 Plus Coatings Mode. a) Silver over Copper. Lab value for Ag: 13 μm. b) Zirconium over galvanized steel. Lab value for Zr: 38 mg/m2. Expected Zn value: ca. 80 g/m2. c) Electroless Ni coating (NiP) over KovarTM alloy (Kovar is a trademark of CRS Holdings, Inc.) Certified thickness of NiP: 20 μm. Image Credit: Thermo Fisher Scientific - Elemental Analyzers and Phase Analyzers
All three results were obtained without any empirical adjustments based on coating reference samples and straight from the box. The first example is the analysis of samples made of copper utilized in electrification products. In order to enhance the electrical conductivity at high frequency, the product is coated with silver.
This is a simple coating system of a mono-elemental layer over a pure metal. Figure 2a exhibits the analysis results that were gathered using the Niton XL5 Plus analyzer of 12.88 µm versus the 13 µm measured in a laboratory, which constitutes great accuracy.
The second example is the analysis of a zirconium conversion coating over hot-dip galvanized steel, which is utilized in the automotive industry, among others. This is a two-layered coating system that is made up of a quite thick layer of zinc, which protects steel from rusting, and a second layer of zirconium to stop ‘white rusting’ of zinc; the layer containing zirconium ensures a better adhesion of paint layers by preventing the formation of zinc hydroxide.
The layer of zirconium does not exceed the equivalent of several atomic layers, so it is extremely thin. The measured value for zirconium (40.24 mg/m2 ) is extremely near to the lab value (38 mg/m2), whereas the measured value for zinc is also near to the expected value.
An electroless nickel coating over Kovar alloy is the third example. Kovar alloy is employed in industry when a reliable glass to metal seal is required. The alloy is made up of around 17 % cobalt, 29 % nickel, a few other elements which are at levels below 1 %, and a balance of iron.
Electroless nickel is a nickel-phosphorus alloy (NIP) that is chemically applied on a substrate to enhance the corrosion and wear resistance of a surface. As it is an alloy coated over another alloy as substrate and both alloys contain high concentrations of nickel, this type of sample is fairly difficult to analyze.
In this instance, the analytical results (18.58 µm) are also very close to the certified values (20.0 µm). The Niton XL5 Plus Analyzer in Coatings Mode is extremely versatile and provides accurate, ‘out of the box’ results without any adjustment for the simplest to the most complex coating samples.
The accuracy of the measurement can be enhanced further when required by utilizing reference samples (standards or in-house characterized reference materials) in a type standardization process.
Conclusion
To make sure that customer coating specifications are adhered to, quality control online, at-line, or during final product inspection is vital. The Niton XL5 Plus analyzer helps the operator to:
- Decrease production costs by minimizing production errors such as:
- Coatings that are too thick increase costs by using more product than is necessary
- Coatings that are too thin can lead to high warranty costs, poor corrosion resistance, and/or product failure
- Non-destructive analysis means there is no need to damage or cut high-value product
- Produce certificates and quality reports via simple report generation tools
- Measure metal grade and composition to ensure goods received match purchase orders
- Produce audit trails of product from goods incoming inspection to products out the door
- Achieve peace of mind with compliance to international methods ISO 3497 and ASTM B568
- Ensure consistent coating across a product via numerous measurements and automatic averaging to enhance quality
- Supply quick turnaround with immediate results and no sample preparation (versus statistical sampling followed by lab analysis, which is time-consuming)
The Niton XL5 Plus Analyzer and Coatings Mode supply a significant step forward from the traditional process of metal identification and composition measurement.
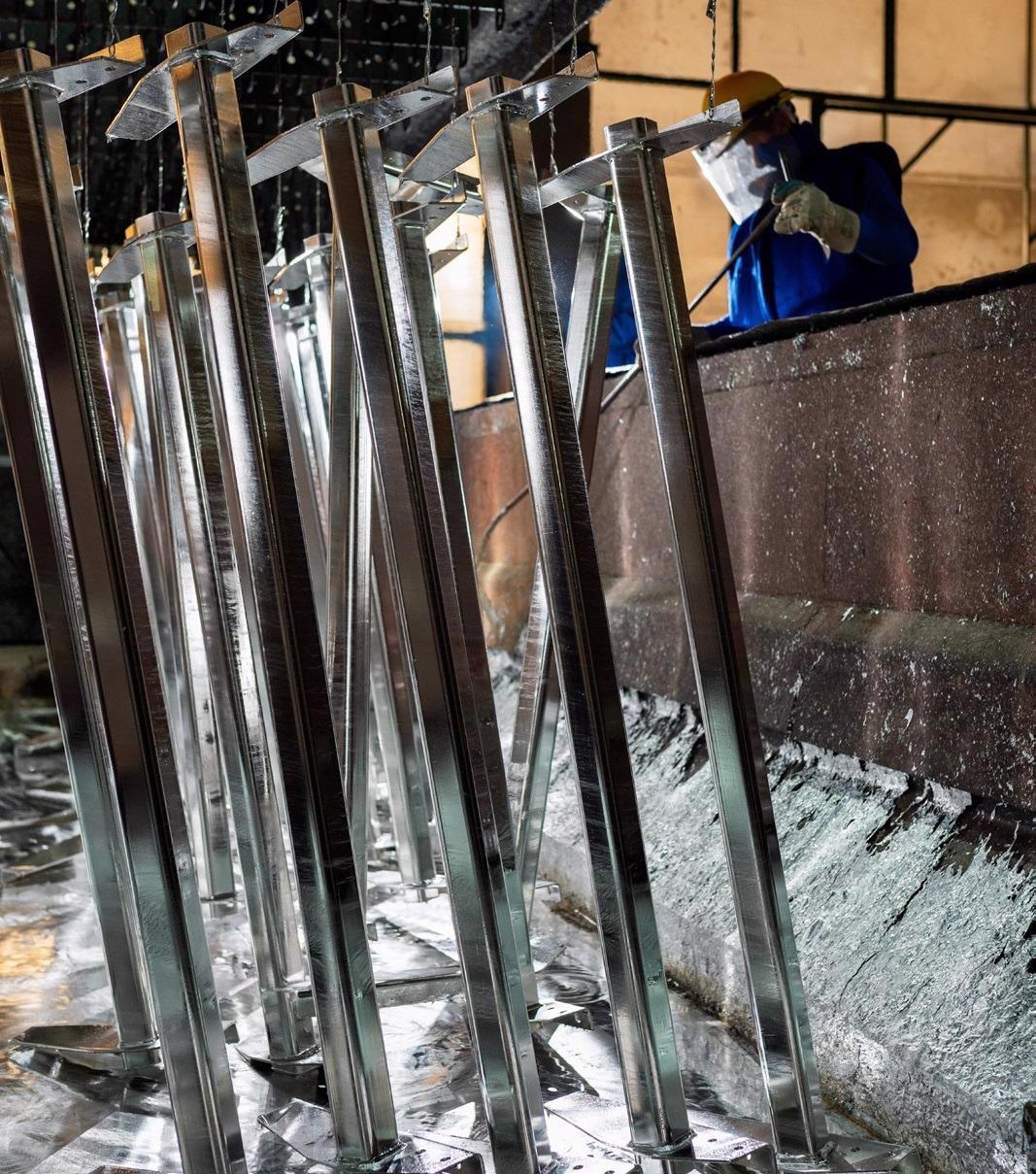
Image Credit: Thermo Fisher Scientific - Elemental Analyzers and Phase Analyzers
References and Further Reading
- S. Piorek, Coatings, Paint and Thin Film Deposits, Chapter 4 in Portable X-ray Fluorescence Spectrometry Capabilities for In Situ Analysis, Edited by Philip Potts and Margaret West, RSC Publishing 2008
- ASTM B568-98 (2009) Standard Test Method for Measurement of Coating Thickness by X-Ray Spectrometry.
- ISO 3497-2000-Measurements of coating thickness – X-ray spectrometric methods.
Acknowledgements
Produced from materials originally authored by Bauer from Thermo Fisher Scientific.
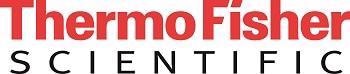
This information has been sourced, reviewed and adapted from materials provided by Thermo Fisher Scientific - Elemental Analyzers and Phase Analyzers.
For more information on this source, please visit Thermo Fisher Scientific - Elemental Analyzers and Phase Analyzers.