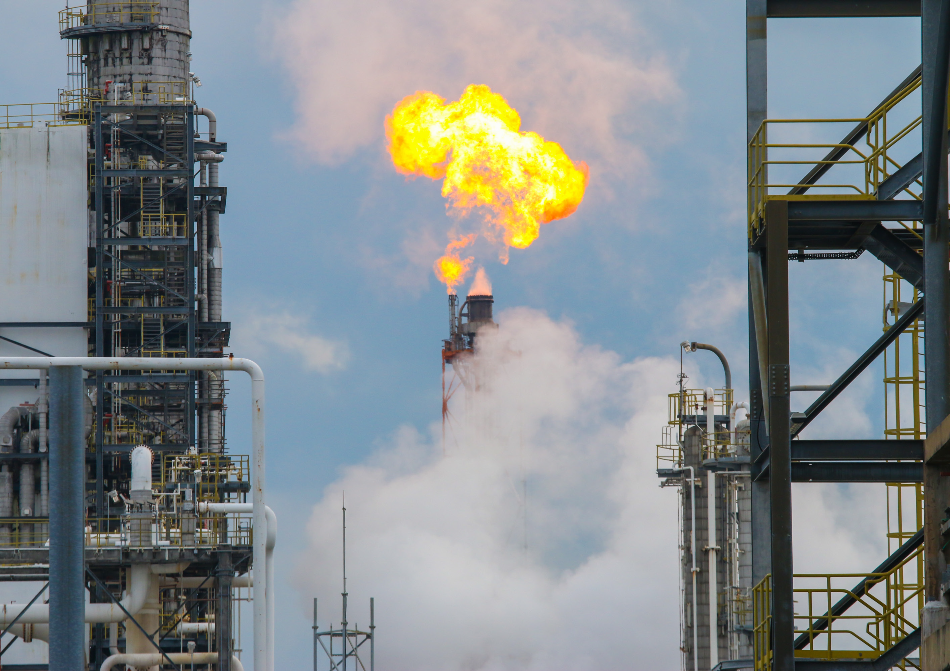
Image Credit: Thermo Fisher Scientific – Environmental and Process Monitoring Instruments
Local and national government bodies are telling processing companies to monitor the various emissions from their flares and plant stacks to decrease the amount of pollution entering the atmosphere at a growing rate.
The focus was initially on oil refinery flares and more recently the focus was on petrochemical and chemical plant flares receiving attention as possible sources of hazardous air pollutants.
Petrochemical Plants
In March 2020, EPA signed numerous Risk and Technology Review (RTR) rules, including National Emission Standards for Hazardous Air Pollutants (NESHAP): Generic Maximum Achievable Control Technology Standards for Ethylene Production (EMACT).
EPA decided that requirements currently in place for EMACT flares are not adequate to ensure 98% destruction efficiency required to meet standards. EMACT flares are subject to the same flare requirements and definitions as refineries as a result and must be monitored continuously.
Existing ethylene crackers must comply three years after the publication of the final rule in the Federal Register, facilities that started construction after October 9, 2019, or new crackers must comply on initial start-up or date of publication of the final rule, whichever is later.
Organic Chemicals Manufacturer
EPA finalized amendments to the 2003 Miscellaneous Organic Chemical Manufacturing National Emission Standards for Hazardous Air Pollutants (NESHAP), known as MON, in May 2020.
This adds monitoring and operational needs for flares, which are utilized to control emissions from processes that generate olefins and polyolefins and flares which control ethylene oxide emissions.
It also enables facilities outside of this subset to opt into these flare requirements in lieu of complying with the current flare standards.
EPA estimates these finalized amendments will decrease hazardous air pollutant (HAP) emissions by 107 tons per year, with reductions in ethylene oxide emissions of ~0.76 tons per year. EPA also estimates that emissions of HAP from flares will be decreased by around another 260 tons per year.
Oil Refineries
The rules referenced above follow those of November 2018 when the US Environmental Protection Agency (EPA) published amendments to Refinery Sector Rule (RSR) 40 CFR Part 63 affecting flares; by January 30, 2019, refineries had to bring flares into compliance with new §63.670 ‘Requirements for Flare Control Devices’.
The new requirements define five flare operating limits:
- Dilution net heating value (NHVdil)
- Combustion zone net heating value (NHVCZ),
- Visible emissions
- Flare tip exit velocity
- Pilot flame presence
It also specifies an NHVCZ minimum operating limit of 270 BTU/scf, based on a 15-minute block period1.
By measuring the net heating value of the vent gas (NHVVG), NHVCZ can be calculated, making flare gas analysis a key part of any compliance strategy. Additional fuel gas such as propane or natural gas has to be added if the NHVCZ approaches 270 BTU/scf. To avoid the production of visible emissions, steam may then need to be added to the flare.
Measurement of Flare Gas Streams by Process Mass Spectrometry
Whatever process they originate from, the Analysis of flare gases brings about a number of challenges. Emissions usually consist of complex mixtures of organic and inorganic species, and as process conditions change, concentrations and compositions are very different over time.
Many regulations only require total sulfur, total heating value, or total hydrocarbon values to be gathered, but measuring the concentrations of individual components helps to identify the source of the emission, pinpointing the problem to a specific part of the plant.
As the heating value of the flare can change quickly, the analysis speed is also vital. Analysis times measured in minutes are more likely to fail to meet emission standards.
As it provides fast, accurate, multicomponent analysis, Process Mass Spectrometry is especially suited to the measurement of flare gas streams. An example of a flare gas stream that contains nitrogen, hydrogen, and hydrocarbons up to C6 is shown in Table 1.
Analysis of these 19 components will usually be carried out in less than 30 seconds, enabling one mass spectrometer to monitor multiple flares, depending on the distances involved.
Advantages of Prima PRO Process Mass Spectrometer
As seen in Figure 1, there is a magnetic sector analyzer at the heart of the Thermo ScientificTM Prima PRO Process Mass Spectrometer. Compared with other mass spectrometers, it provides unrivaled accuracy and precision.
Table 1. Example of flare gas stream composition. Source: Thermo Fisher Scientific – Environmental and Process Monitoring Instruments
Component |
Molecular Weight |
Flare Gas Typical Composition %mol |
Hydrogen |
2 |
0-40 |
Methane |
16 |
15-95 |
Water |
18 |
0-8 |
Carbon
Monoxide |
28 |
0-1 |
Nitrogen |
28 |
0-40 |
Ethylene |
28 |
0-12 |
Ethane |
30 |
2-15 |
Oxygen |
32 |
0-5 |
Hydrogen
Sulfide |
34 |
0-10 |
Propylene |
42 |
0-20 |
Carbon
Dioxide |
44 |
0-10 |
Propane |
44 |
0-5 |
1-3, Butadiene |
54 |
0-0.2 |
Butenes |
56 |
0-15 |
i-Butane |
58 |
0-10 |
n-Butane |
58 |
0-5 |
C5 and C6 |
70+ |
0-15 |
Carbonyl
Sulfide |
60 |
0-10 ppm |
Carbon
Disulfide |
76 |
0-1 ppm |
Thermo Fisher ScientificTM manufactures both quadrupole and magnetic sector mass spectrometers and has more than thirty years of industrial experience. They have demonstrated that the magnetic sector-based analyzer provides the best performance for industrial online gas analysis.
Key advantages of magnetic sector analyzers include:
- Long intervals between calibrations
- Improved precision
- Accuracy
- Resistance to contamination
Depending on the gases analyzed and the complexity of the mixture, analytical precision is generally between 2 and 10 times better than a quadrupole analyzer.
Firstly, neutral gas atoms and molecules are converted into positively charged ions in the Prima PRO Process Mass Spectrometer ion source. This is an enclosed type for minimum background interference, high sensitivity, and maximum contamination resistance.
It is a high-energy (1000 eV) analyzer that provides extremely rugged performance in the presence of vapors and gases that have the potential for contaminating the internal vacuum components.
The Prima PRO Process Mass Spectrometer has a proven track record of monitoring high percent level concentrations of organic compounds without experiencing contamination or drift.
Next, ions are accelerated through a flight tube, where they are separated by their mass to charge ratios in a magnetic field of variable strength. The peak shape produced is ‘flat-topped’ and uniform response is seen over a finite mass width. This is because the magnetic sector mass spectrometer produces a focused ion beam at the detector.
As the height of the peak is directly proportional to the number of ions striking the detector, it is also directly proportional to the concentration of the component being measured. The high precision analysis will be acquired as long as the measurement is taken anywhere on the peak’s flat top.
If the varying composition levels in flare gas are to be measured accurately, the ability of the Prima PRO Process Mass Spectrometer to measure over a wide dynamic range is crucial.
EffecTech UK, an independent specialist company that provides accredited calibration and testing services to the power and energy industries for gas quality, flow, and total energy metering, has evaluated the Prima PRO Process Mass Spectrometer independently.
It is accredited to internationally recognized ISO/IEC 17025:2005 standards; this specifies the general requirements for the competence to perform tests and/or calibrations, including sampling.
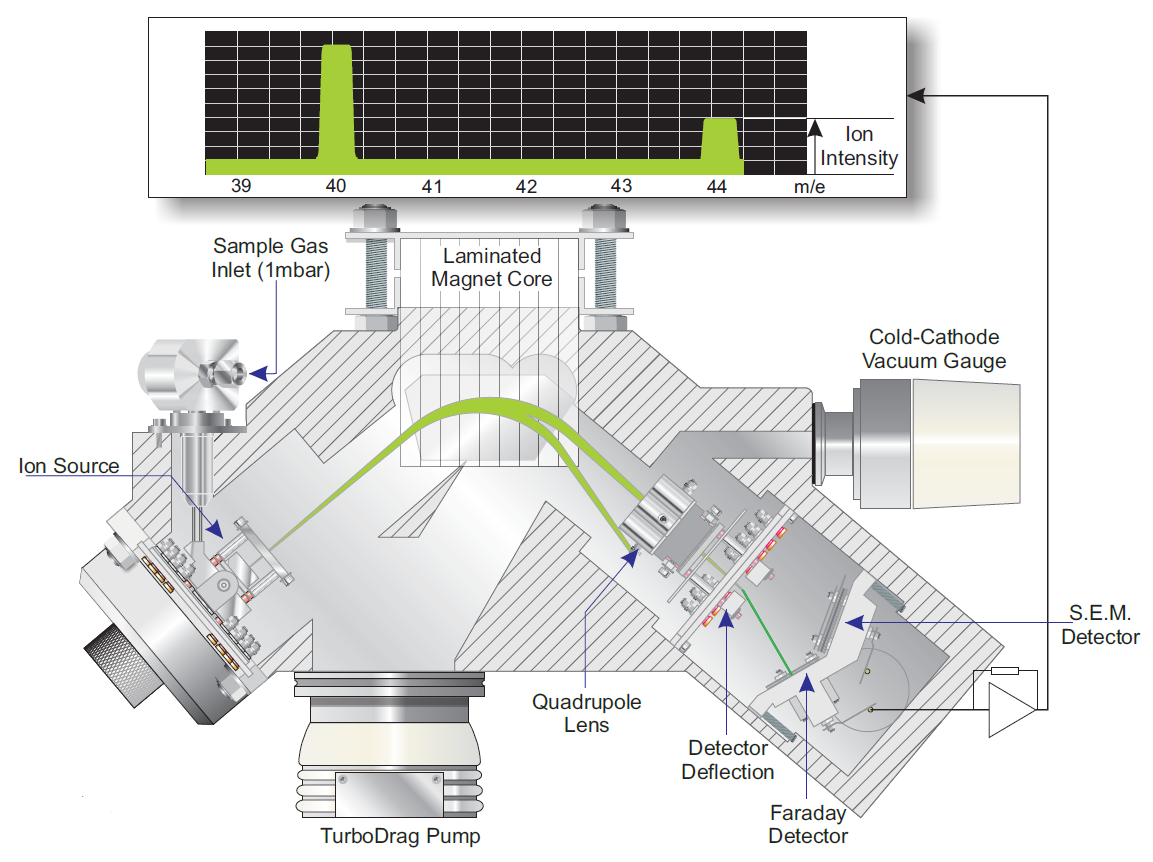
Figure 1. Prima PRO Process Mass Spectrometer magnetic sector analyzer. Image Credit: Thermo Fisher Scientific – Environmental and Process Monitoring Instruments
Rapid Multistream Sampling
A fast, reliable way to switch between streams is needed if the Mass Spectrometer is to monitor multiple flare streams or flare streams and process streams. Rotary valves suffer from poor reliability and solenoid valve manifolds have too much dead volume, so Thermo Fisher Scientific developed the unique Rapid Multistream Sampler (RMS).
It provides an unmatched combination of reliability and sampling speed and enables sample selection from 1 of 32 or 1 of 64 streams. Stream settling times are fully configurable by the user and are application-dependent. The RMS includes digital sample flow recording for each stream selected.
If the sample flow drops, this can be utilized to trigger an alarm, for example, if a filter in the sample conditioning system becomes blocked. The position of the stream selector is optically encoded and the RMS can be heated to 120 °C for reliable, software-controlled stream selection.
The Prima PRO Process Mass Spectrometer’s internal network communicates the temperature and position control signals. The RMS has a three-year warranty as standard and has a proven track record of performing 10 million operations between maintenance. The same level of guaranteed reliability is not provided by any other multi-stream sampling device.
Measuring Fuel Properties with Prima Pro Process Mass Spectrometer
The following fuel properties can routinely be derived by the Prima PRO Process Mass Spectrometer.
Lower Heating Value is calculated by utilizing the value of 1212 BTU/scf for Hydrogen as recommended by EPA 40 CFR Parts 60 and 63, instead of the theoretical value of 274 BTU/scf. This supplies the user with a better indication of flare performance (e.g., meeting the minimum operating limit of 270 BTU/scf).
Source: Thermo Fisher Scientific – Environmental and Process Monitoring Instruments
. |
. |
Lower Heating Value (LHV) |
Also known as Net Heating Value or
Lower Calorific Value |
Higher Heating Value (HHV) |
Also known as Gross Heating Value or
Higher Calorific Value |
Compressibility |
|
Actual Lower Heating Value |
Ideal Lower Heating Value
--------------------------------------
Compressibility |
Density |
|
Specific Gravity |
|
Lower Wobbe Index |
Lower Heating Value
--------------------------------
√(Specific Gravity) |
Higher Wobbe Index |
Higher Heating Value
----------------------------------
√(Specific Gravity) |
Air Requirement |
|
Combustion Air Requirement Index (CARI) |
Air Requirement
-----------------------------
√(Specific Gravity) |
Due to its high combustion potential, accurate analysis of hydrogen across a wide dynamic range is vital; the Prima PRO Process Mass Spectrometer’s magnetic sector analyzer is ideally suited to hydrogen analysis as it does not suffer from the ‘zero blast’ which renders the analysis of light molecules problematic on many quadrupole analyzers.
HHV is different from LHV in that it considers the latent heat of vaporization of water in the combustion products. The precision of these measurements with the Prima PRO Process Mass Spectrometer is usually better than 0.1% relative.
How the Ideal LHV of the flare gas stream is calculated by Thermo ScientificTM GasWorks software Derived Values, based on the individual components’ Ideal LHVs is shown in Figure 2.
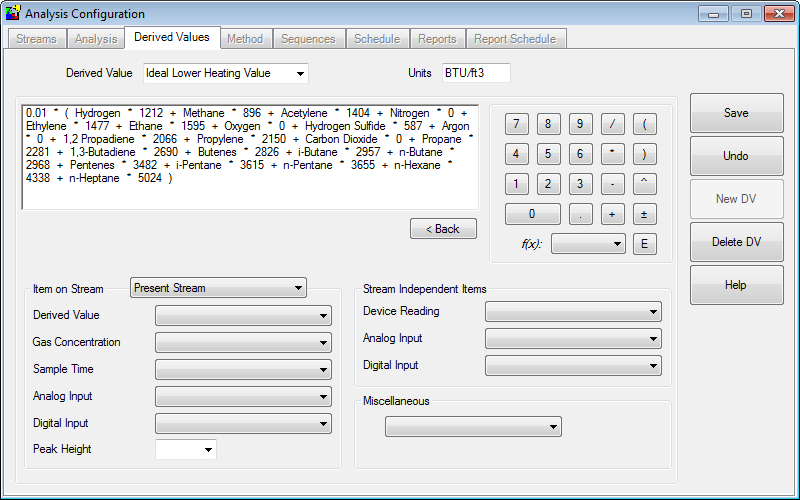
Figure 2. GasWorks Derived Value for Ideal Lower Heating Value. Image Credit: Thermo Fisher Scientific – Environmental and Process Monitoring Instruments
Analysis times are usually 30 seconds or less, which includes settling time. As they are measured by various techniques available, e.g., 4-20 mA or 0-10 V analog outputs, Profibus, Modbus, or OPC, Data are communicated to the plant host computer.
Analytical Set-up
An unlimited number of analysis techniques are supported by GasWorks software; this allows the analysis to be optimized on a per-stream basis. Depending on process control requirements, the most efficient peak measurements and the most appropriate speed versus precision settings can be chosen for each gas stream.
Figures 3 and 4 demonstrate some examples of different analysis techniques. Figure 3 exhibits an example of the analytical technique for a flare gas stream and Figure 4 demonstrates that for a process stream.
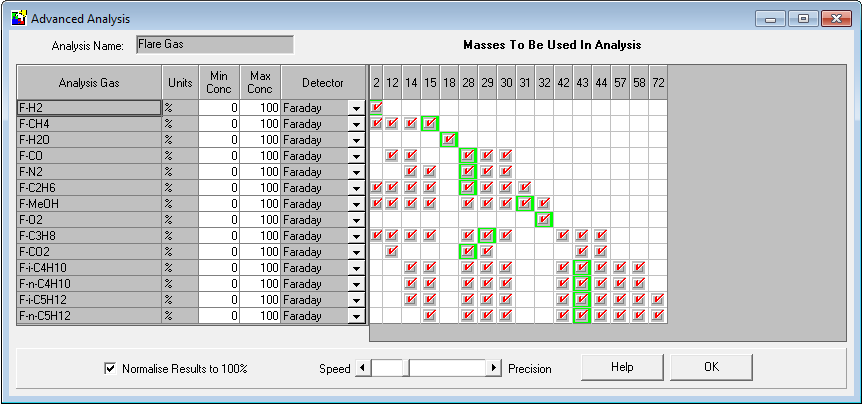
Figure 3. Example of flare stream method. Image Credit: Thermo Fisher Scientific – Environmental and Process Monitoring Instruments
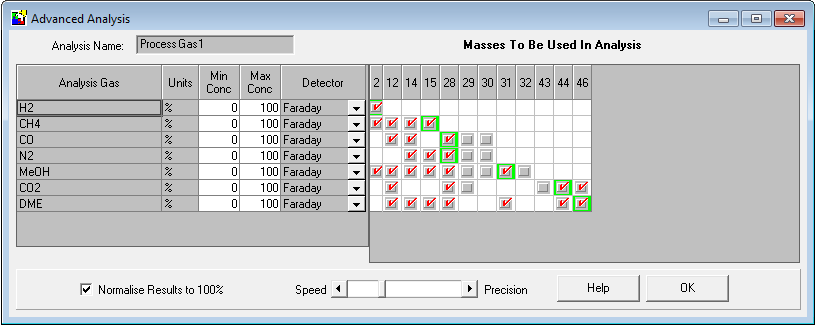
Figure 4. Example of process stream method. Image Credit: Thermo Fisher Scientific – Environmental and Process Monitoring Instruments
Along with additional process techniques, both approaches are being used on a single Prima PRO Process Mass Spectrometer measuring a combination of process streams and flare gas.
These two techniques clearly demonstrate the amount of spectral overlap in the MS fragmentation patterns. It is crucial to measure these fragmentation patterns from the actual components of interest as the utilization of surrogate compounds may simplify the calibration process but will inevitably result in decreased accuracy.
Flare Gas Test Data
The Prima PRO Process Mass Spectrometer was subjected to a factory test on a gravimetric cylinder containing 21 components, including inorganics and hydrocarbons, from C1 to C6 in order to check the performance on a refinery flare gas application.
Table 2. Factory test on a gravimetric cylinder containing 21 inorganic and hydrocarbon compounds, analyzed over 18 hours. Source: Thermo Fisher Scientific – Environmental and Process Monitoring Instruments
Component |
Concentration
%mol |
Prima PRO Specification
for Standard Deviation
%mol (8 hours) |
FAT test Ave
%mol (8 hours) |
FAT Test
Actual Standard Deviation
%mol (8 hours) |
Hydrogen |
10 |
≤0.02 |
9.8835 |
0.0077 |
Methane |
64.53 |
≤0.05 |
64.6662 |
0.0125 |
Carbon
Monoxide |
5 |
≤0.05 |
5.0829 |
0.0264 |
Nitrogen |
10 |
≤0.05 |
9.8557 |
0.0469 |
Ethylene |
2 |
≤0.02 |
1.9867 |
0.0010 |
Ethane |
2 |
≤0.02 |
2.0367 |
0.0012 |
Oxygen |
1 |
≤0.001 |
0.9941 |
0.0006 |
Hydrogen
Sulfide |
0.05 |
≤0.0005 |
0.0484 |
0.0003 |
Propylene |
1 |
≤0.001 |
0.9961 |
0.0011 |
Carbon
Dioxide |
1 |
≤0.001 |
0.9597 |
0.0007 |
Propane |
1 |
≤0.001 |
1.0910 |
0.0007 |
1,3 Butadiene |
0.1 |
≤0.005 |
0.0992 |
0.0003 |
Butenes |
0.5 |
≤0.005 |
0.5023 |
0.0005 |
i-Butane |
0.5 |
≤0.005 |
0.4892 |
0.0011 |
n-Butane |
0.5 |
≤0.005 |
0.5059 |
0.0026 |
Carbonyl
Sulfide |
100 ppm |
≤1 ppm |
100.5319 |
0.4470 |
Pentenes |
0.1 |
≤0.005 |
0.0992 |
0.0004 |
i-Pentane |
0.3 |
≤0.005 |
0.3083 |
0.0012 |
n-Pentane |
0.3 |
≤0.005 |
0.2792 |
0.0042 |
Carbon
Disulfide |
100 ppm |
≤1 ppm |
100.4589 |
0.2733 |
n-Hexane |
0.1 |
≤0.005 |
0.0957 |
0.0010 |
NHV (BTU/scf) |
|
≤0.1% relative |
899.5394 |
0.07% |
Table 2 demonstrates the Prima PRO Process Mass Spectrometer’s quoted performance (standard deviation over 8 hours), the composition of the cylinder, and the results gathered from the test. Over 8 hours, the measured standard deviations for all 21 components were less than the specified standard deviations.
In addition to the composition data, the Prima PRO Process Mass Spectrometer calculated the Net Heating Value over the 8 hours of the test; as with the component concentrations, the measured NHV standard deviations are far less than the specified 8-hour standard deviations.
Trend data for minor components, major components, sulfur components, and NHV over the 8 hours of the test are shown in Figures 5a to 5d.
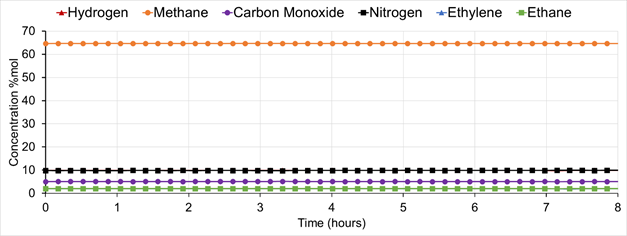
Figure 5a. Major component concentrations obtained during factory test on a gravimetric cylinder containing 21 inorganic and hydrocarbon compounds, analyzed over 8 hours. Image Credit: Thermo Fisher Scientific – Environmental and Process Monitoring Instruments
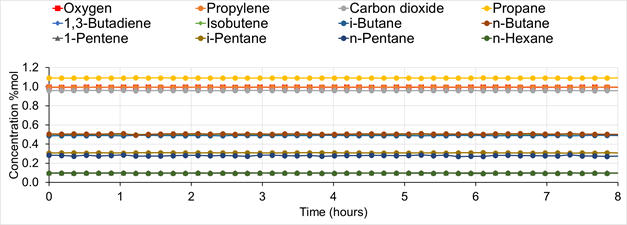
Figure 5b. Major component concentrations obtained during factory test on a gravimetric cylinder containing 21 inorganic & hydrocarbon compounds, analyzed over 8 hours. Image Credit: Thermo Fisher Scientific – Environmental and Process Monitoring Instruments
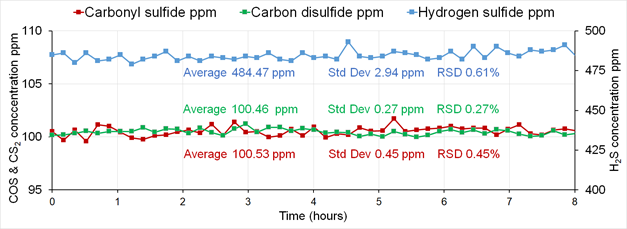
Figure 5c. Sulfur component concentrations obtained during factory test on a gravimetric cylinder containing 21 inorganic & hydrocarbon compounds, analyzed over 8 hours. Image Credit: Thermo Fisher Scientific – Environmental and Process Monitoring Instruments
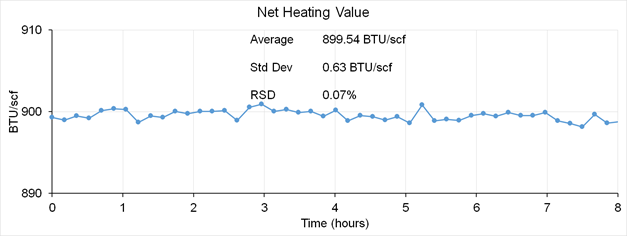
Figure 5d. NHV obtained during factory test on a gravimetric cylinder containing 21 inorganic & hydrocarbon compounds, analyzed over 8 hours. Image Credit: Thermo Fisher Scientific – Environmental and Process Monitoring Instruments
Analysis of Total Sulfur
Typically, refinery regulators are interested in values for Total Reduced Sulfur (TRS) and hydrogen sulfide (H2S), but some divergence on what constitutes TRS exists. In some instances, it is defined as H2S together with carbonyl sulfide (COS) and carbon disulfide (CS2).
It can also be defined as a mixture of compounds that contain a sulfur component in the reduced form, usually dimethyl sulfide (DMS, (CH3)2S), H2S, methanethiol (methyl mercaptan, CH3SH), and dimethyl disulfide (DMDS, CH3S2CH3).
Mass spectrometers are able to quantify a number of sulfur compounds down to ppm levels; Table 3 shows typical Prima PRO Process Mass Spectrometer performance figures. Analysis time is below 30 seconds, including stream switching time and standard deviations measured over 8 hours.
Table 3. Typical Prima PRO Process Mass Spectrometer performance specification for sulfur compounds. Source: Thermo Fisher Scientific – Environmental and Process Monitoring Instruments
Component |
Typical Composition
%mol |
Precision of analysis by
Prima PRO Process MS
(single standard deviation) ≤ |
Hydrogen Sulfide |
3 ppm |
0.5 ppm |
Methyl Mercaptan |
10 ppm |
0.5 ppm |
Ethyl Mercaptan |
10 ppm |
0.5 ppm |
n-Propyl Mercaptan |
10 ppm |
0.5 ppm |
n-Butyl Mercaptan |
10 ppm |
0.5 ppm |
A unit was calibrated for hydrogen sulfide, carbonyl sulfide and carbon disulfide at a single concentration using three cylinders in order to show the Prima PRO Process Mass Spectrometer’s excellent linearity when analyzing sulfur species; then it was utilized to analyze a series of cylinders containing the three sulfur species.
- COS was calibrated at 0.2006%, then MS analyzed COS concentrations from 0% to 0.2006%
- H2S was calibrated at 0.0506%; then MS analyzed H2S concentrations from 0% to 89.88%
- CS2 was calibrated at 0.198%, then MS analyzed COS concentrations from 0% to 0.198%
The test gases utilized to show system linearity are shown in Table 4, with the calibration gases in red. The linearity achieved for the three sulfur species is demonstrated in Figure 6.
This data demonstrates that the Prima PRO Process Mass Spectrometer can measure up to 100% concentrations and can be safely calibrated for hydrogen sulfide at trace levels (0.05% in this instance).
Table 4. Sulfur test gases used to demonstrate Prima PRO Process Mass Spectrometer linearity. Source: Thermo Fisher Scientific – Environmental and Process Monitoring Instruments
H2S Actual
Concentration %mol |
H2S Measured
Concentration %mol |
COS Actual Concentration %mol |
COS Measured Concentration %mol |
CS2 Actual Concentration %mol |
CS2 Measured Concentration %mol |
0 |
0.0001 |
0 |
0 |
0 |
0.0002 |
0.003 |
0.0028 |
0.003 |
0.0029 |
0.003 |
0.0039 |
0.0506 |
0.0503 |
0.0502 |
0.0513 |
0.0498 |
0.0576 |
0.2505 |
0.261 |
0.2006 |
0.2015 |
0.198 |
0.2006 |
0.4997 |
0.526 |
|
|
|
|
2 |
2.08 |
|
|
|
|
50.03 |
51.1 |
|
|
|
|
89.88 |
89.88 |
|
|
|
|
GasWorks software can produce a figure for Total Sulfur by utilizing its Derived Value capability to sum the individual component concentrations.
It is worth noting that the total sulfur value only represents the sum of the sulfur compounds that the MS has analyzed and any unidentified or unknown compounds will not be reported.
Thermo Scientific recommends the Thermo Scientific SOLA iQ Flare System For a true Total Sulfur reading, which gives a solution for accurate and continuous determination of total sulfur in flare gas streams2.
In order to calculate total sulfur, SOLA iQ Flare employs PUVF (pulsed ultraviolet fluorescence) spectrometry. Firstly, all organically bound sulfur is converted to sulfur dioxide (SO2) via sample combustion.
Irradiation of SO2 with ultraviolet light at a specific wavelength forms an excited form of SO2. The emission of light or fluorescence relaxes the excited SO2 to its ground state. The intensity of the emitted light is directly proportional to the SO2 concentration and so the flare stack’s total sulfur concentration.
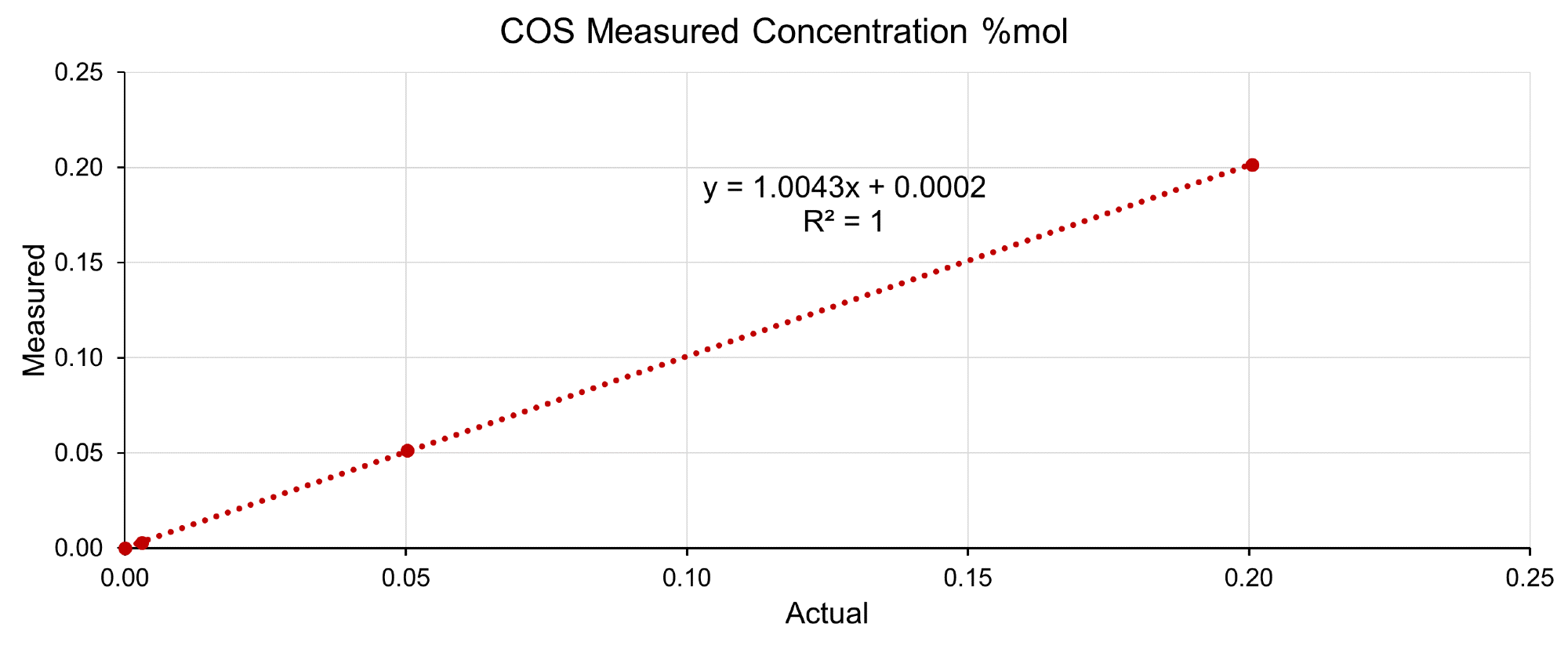
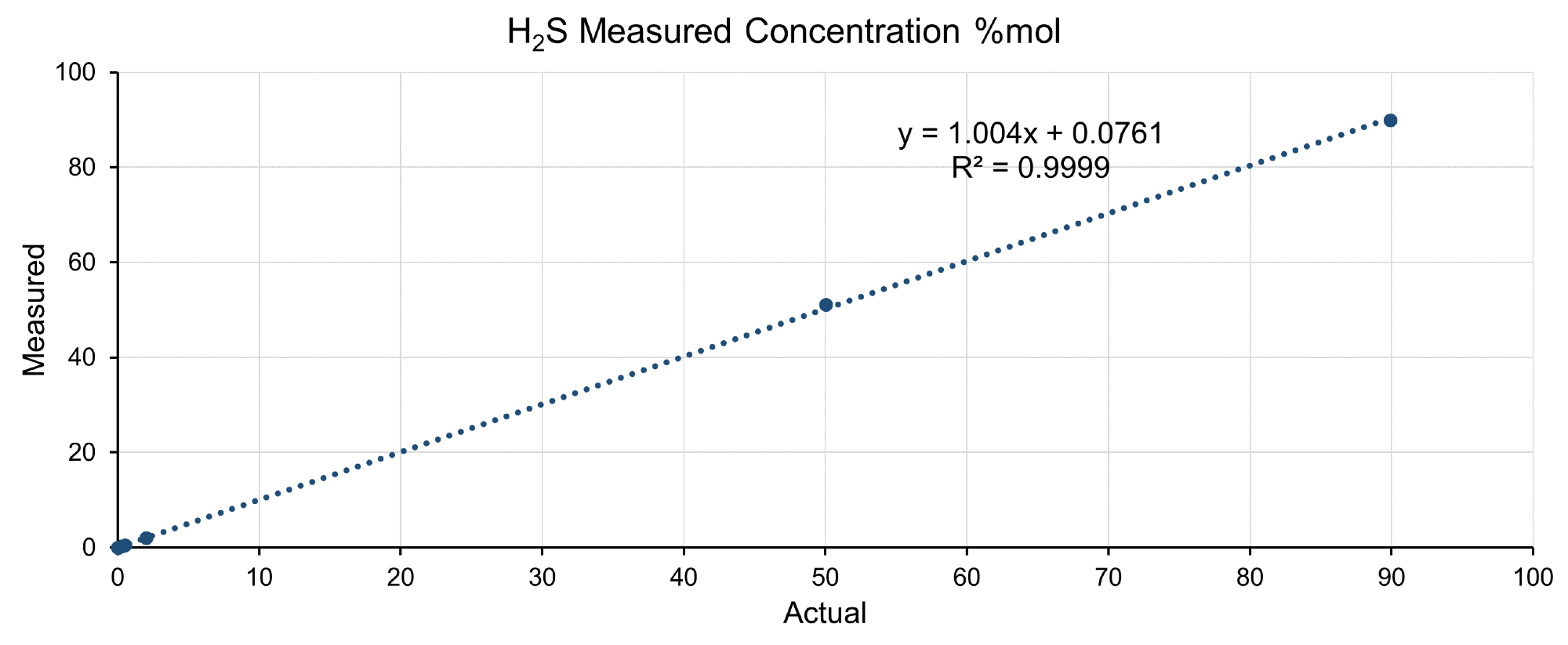
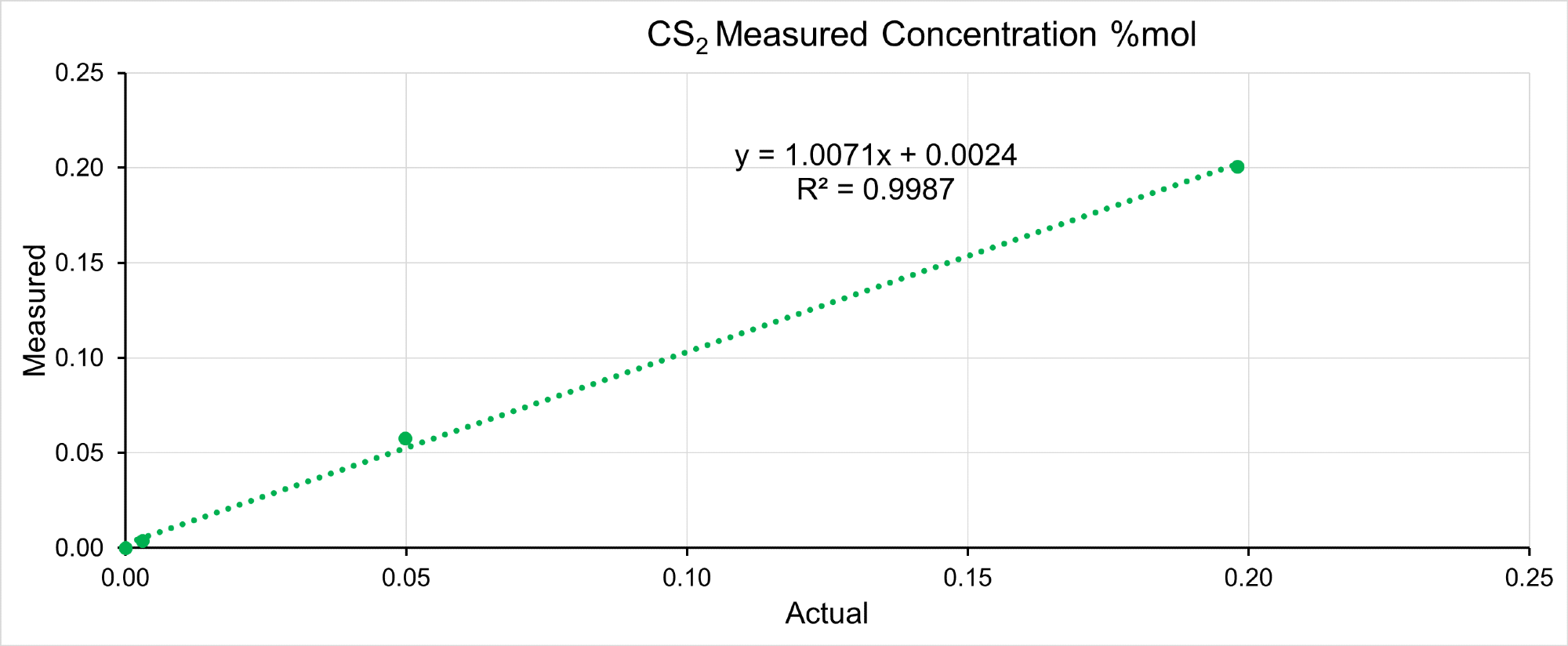
Figure 6. Prima PRO Process Mass Spectrometer linearity for hydrogen sulfide, carbonyl sulfide and carbon disulfide. Image Credit: Thermo Fisher Scientific – Environmental and Process Monitoring Instruments
Summary
The Prima PRO Process Mass Spectrometer supplies quick online accurate analysis of process gas composition and flare gas. The Prima PRO Process Mass Spectrometer has had huge success monitoring refinery flare gases in recent years.
Over many years, it has had a proven track record in monitoring ethylene furnaces3 and ethylene oxide processes4 and is perfect for monitoring flare gas streams from these same processes as they fall under the spotlight of concerns over hazardous emissions more and more.
When combined with the flexibility of GasWorks software, the inherent power of mass spectrometry allows one Prima PRO Process Mass Spectrometer to monitor not only flare gas streams but also multiple process streams.
Therefore, by comparing the detailed composition data from the flare gas stream with that of the multiple process streams, root cause fault analysis is greatly facilitated.
In addition, to complete compositional analysis, the Prima PRO Process Mass Spectrometer supplies accurate fuel gas properties, including specific gravity, HHV, LHV, density, stoichiometric air requirement, Wobbe Index, and CARI.
This ensures that unburned pollutants are not emitted from the flare waste gases are burnt to complete combustion.
References and Further Reading
- EPA 40 CFR § 63.670 – Requirements for Flare Control Devices, US Government Publishing Offices
- Continuous flare stack emission monitoring: Thermo Scientific SOLA iQ Flare Analyzer, Thermo Fisher Scientific Application Note, 2020
- Advancing Process Control and Efficiency During Ethylene Production Using the Thermo Scientific Prima PRO Process Mass Spectrometer, Thermo Fisher Scientific Application Note, 2014
- Thermo Scientific™ Prima PRO Process Mass Spectrometer: Improving ethylene oxide process control, Thermo Fisher Scientific Application Note, 2017
Acknowledgments
Produced from materials originally authored by Daniel Merriman from Thermo Fisher Scientific.
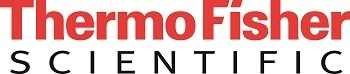
This information has been sourced, reviewed and adapted from materials provided by Thermo Fisher Scientific – Environmental and Process Monitoring Instruments.
For more information on this source, please visit Thermo Fisher Scientific – Environmental and Process Monitoring Instruments.