There are over half a million landfill sites in Europe, and 90% of these have not had to comply with safety regulations. The management of landfill sites has become a mounting concern in many European countries, with the responsibility for landfill sanitation and reclamation increasingly falling to public institutions.
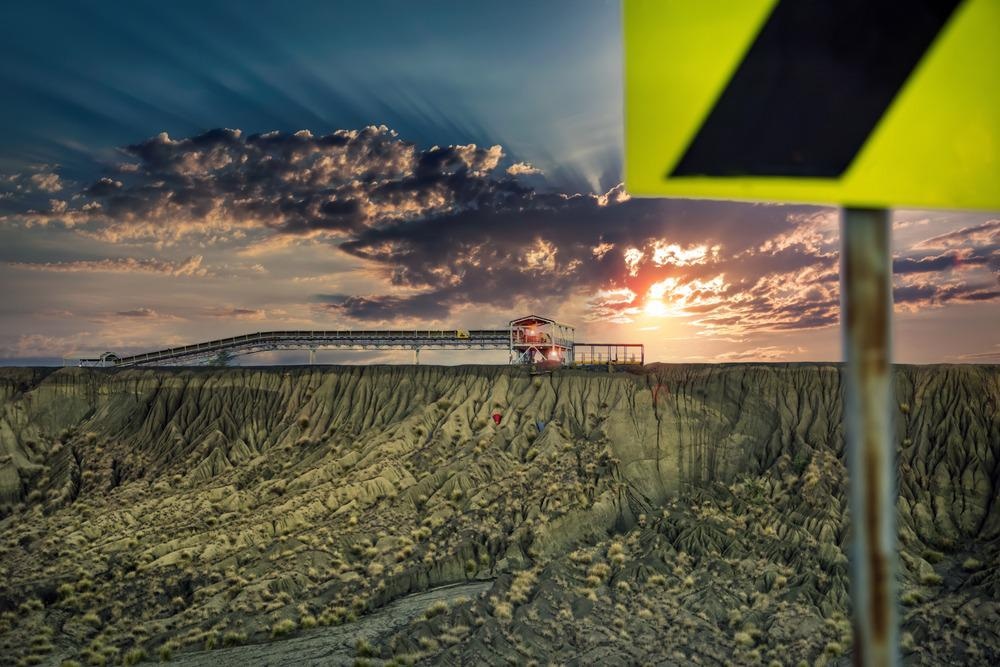
Image Credit:Shutterstock/LucianComan
One approach to waste management of landfills involves the concept of landfill mining, which involves excavating, separating, and treating waste. The idea is that it will allow for the reclamation and improvement of landfill sites, as well as the recovery and recycling of materials. Enhanced Landfill Mining (ELFM) uses innovative technologies and an integrated approach, providing detailed analysis of environmental benefits and burdens.
While plastics are often a major component in landfills, particularly polyolefin materials such as polyethylene (PE) and polypropylene (PP), ELFM studies indicate they are usually converted into fuels rather than recycled into secondary raw materials. Recyclers face several issues such as separating polymers into type, contamination and material degradation.
This study describes an environmental impact assessment using life cycle analysis (LCA) methodology of landfill waste treatment and processing. Using waste plastic materials from an unregulated industrial landfill site in Italy, the team applied a multi-stage waste treatment process, involving a patented wet-processing technology, before processing the waste into a secondary product. They also tested two additives (maleated linear low density polyethylene (MAPE) and low density polyethylene (LDPE)) as adhesion-promoters.
The secondary plastic material was produced as PE granules. One of the analytical techniques used to study their composition included solid state 13C MAS NMR spectroscopy. The team used a Bruker Avance II 400 spectrometer, equipped with a 4 mm MAS probe. This showed that the granules consisted mainly of PE with very small amounts of PP, cellulose, and polystyrene.
The team describes how they achieved this low level of contamination by employing thorough washing in the selection process and adhesion-promotor additives. As a result, the mechanical properties of the granules compared well with the virgin product.
LCA revealed environmental and economic benefits. Compared to the virgin material, the secondary plastic’s main advantage was that it did not require non-renewable resources (crude oil) and therefore avoided emissions from crude oil refining.
The team concludes that the ELFM process could be improved by addressing the treatment of non-recoverable waste such as cathodes and anodes, and sand, which need to be transported by ship for disposal. The researchers suggest further treatment of sand could produce a material that could be used in road-making or construction, turning it into a by-product of the treatment process as well as reducing the energy costs associated with non-recoverable waste transport and disposal.
In summary, the study found that an integrated experimental and LCA approach demonstrated that recovering plastic waste through ELFM is feasible and environmentally sustainable, and that appropriate processing can produce secondary materials with good mechanical properties and value.
Increase Sustainability by Innovation with Integrity
Bruker offers the broadest end-to-end solution portfolio for the polymer value chain from product development via raw material qualification, process control in manufacturing and quality control of finished goods to enhanced methodologies for waste reduction in recycling processes. This approach enables our customers to transfer waste into raw materials and so closes the circle. Circular economies will make our planet a safer and healthier place to live and Bruker is strongly committed to continuously support and share this mission.