Interview conducted by Olivia FrostFeb 25 2021
In this interview, Scott Mittl, the VP Sales at Insaco, talks to AZoM about overcoming technical challenges in advanced materials manufacturing.
Can you tell us about how Insaco has pioneered the technology of precision manufacturing?
Since 1947 we have been machining, grinding, and polishing ultra-hard advanced materials to customer-supplied drawings. These advanced materials include: ceramics, sapphire, glass, quartz, composites, carbides, nitrides, and other “non” metallic, “non” plastic materials
We have the facility and experience to create almost any geometric feature in these “difficult to process ” materials. We also suggest various advanced materials for end-use applications based upon manufacturability and material properties desired.
As a machining and fabrication service organization, Insaco produces parts to meet customer specifications from ultra-hard materials. All part designs are unique to the designer. The designs are in industries where usually common materials like steel or plastic will not stand up to the environmental or process requirements. Ceramics become optimal (sometimes only) material able to meet requirements.
We fabricate anything from a single rod or washer to very complex geometrical shapes while holding extremely tight dimensional tolerances. As a job shop, Insaco will take on quantity requirements from prototype to full series production.
Insaco has pioneered the technology of precision manufacturing parts from difficult to machine advanced materials. Over many decades, customers have recognized Insaco as a valuable resource with unique engineering and machining capabilities allowing us to fabricate everything from simple parts to unusual shapes and forms. Our ability to machine is only exceeded by our ability to measure the parts we are machining which is very critical to meeting customer print requirements.
Our machinists are trained on the grinding machines and inspection equipment needed to get the part completed to the print requirements. We also continually train our workforce with classes in CAD, Robotics, GD&T and we implement LEAN on the manufacturing floor.
Our knowledge of the supply chain for advanced materials allows us to acquire appropriate raw material efficiently. Insaco does not produce materials. We procure material needed for specific jobs in an oversized hard- fired condition. Not producing the material in-house allows Insaco the freedom to offer the designers unbiased guidance on material selection. This guidance is based on the material’s properties, availability, and manufacturability.
What are some examples of tolerances or other quantifiable results that you have achieved with your manufacturing processes?
Insaco has decades of experience creating precision parts in ceramic and sapphire and other advanced materials.
One example would be our ability to make sapphire tubes with polished inside and outside diameters resulting in optically transparent surfaces on all dimensions. We have the ability to polish sapphire to optical figures while holding surface finishes to as low as <10Angstroms.
Many applications require diameter size dimensions to +/- 0.0001” with even tighter roundness and cylindricity. This capability gives us the ability to create matched ceramic piston/ceramic sleeve sets with gap clearances to <.00008” (<0.002mm). This gap allows for the pumping of various solutions without seals so therefore won’t ever wear or degrade during use.
Insaco is also specialized in the volume production of sapphire wafer carriers with tight total thickness variation (TTV <.0001”) while maintaining a see-thru optical finish polish. These requirements are necessary to allow for successful backside thinning and backside via etching for the Compound Semiconductor Industry.
We also have the ability to make ceramic quadrupole collars for the RGA and Mass Spectrometer industries. We can machine to size and locational accuracy on the precision holes to as low as <.00004” (0.001mm).
Can you tell our readers about how a material change prove a winner for NASA?
Deep space-based research by NASA called for a high-energy solar concentrator that could focus from 3.5” to a faceted point over a 12” length Designers had initially tried sapphire as the material best suited to this application. However, it failed under Beta tests so NASA turned to a fused silica material but needed precise machining to ensure accuracy.
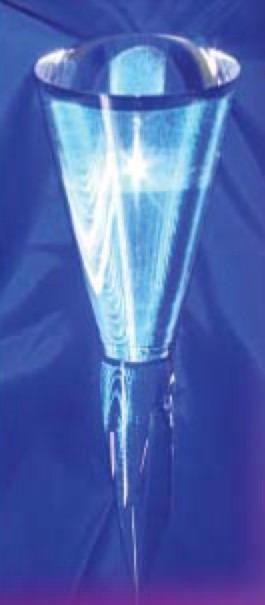
Therefore, for a solution, NASA turned to Insaco. Since 1947 we have extensive experience in diamond grinding and polishing sapphire as well as chemo-mechanically finishing intricate parts from fused silica and quartz. Insaco’s expertise in fabricating to extremely tight tolerances (without bias to a particular material) made the choice simple.
As a result, NASA selected a special grade of fused silica and contracted with Insaco for precision machining. Specifications for the complex polish and edge radii, as well as the production feasibility for this intricate and critical part, were successfully accomplished by Insaco and completed on time and on budget, saving NASA valuable time to get the solar concentrator up in space quickly.
How did a zirconia replacement part solve the wire cutter problem for Crescent Design?
The problem was that a specialized wire cutting machine used a tool-steel funnel to position a steel wire for cutting. In a short period of time, the rubbing of the wire damaged the funnel which then caused damage to the wire. This required shutting down the machine, re-arranging the inlet funnel to a smooth spot, and re-starting the machine. The resulting downtime, wire loss from abrasions, and replacement of the inlet funnels became costly and difficult to manage.
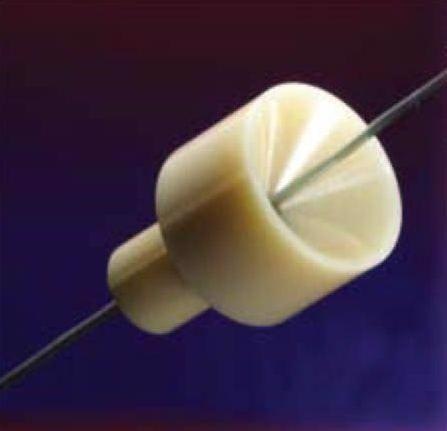
Insaco engineers, working with the OEM wire cutting machine manufacturer, Crescent Design, proposed changing the funnel to a hot isostatic pressed zirconia material significantly improving wear quality when compared to metals and even most other technical ceramics.
Following on from this, Insaco precision fabricated the new zirconia funnels, and after two years of use, there is NO noticeable wear in the inlet funnel, NO wasted material run, and virtually NO downtime. The end-user is extremely pleased with the results and has ordered several more machines equipped with this new material machined by Insaco.
Can you tell us about how Insaco solved a ceramics thermal conductivity problem?
What happened was a customer pioneering in the life sciences industry contacted Insaco for a quote on Aluminum Nitride machining for their developmental part requiring excellent hardness and good thermal conductivity. However, they weren’t sure the Aluminum Nitride was the most efficient choice.
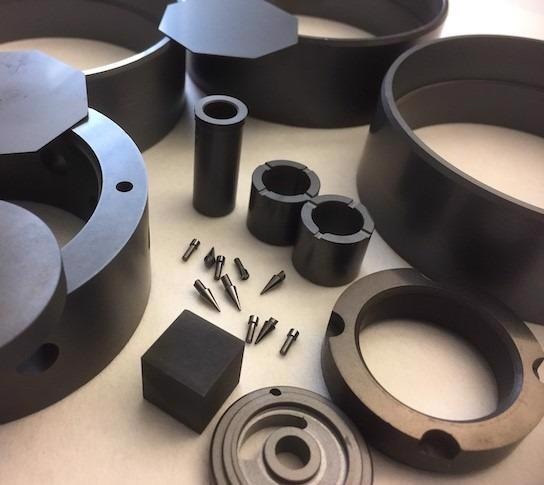
Therefore, research by Insaco sales engineers led to a better recommendation to use a CVD graded silicon carbide due to its outstanding thermal conductivity of over 250 W/mK, which is more equivalent to iron or steel, yet offers extreme hardness and wear resistance, even at high temperatures. This material machines well-using diamond grinding technology and there is no real cost penalty. Since Insaco does not produce any materials directly, they can offer unbiased guidance on ceramic material alternatives and their practical limits to size or tolerance.
As a result, the customer was extremely pleased with the early prototype results of their part fabricated from the recommended silicon carbide. Production has now launched, and the higher thermal conductivity performance has provided a competitive edge to expand sales.
How can fine-grained 99.5& Alumina be used for scientific instrumentation problems?
An example of this is that a cutting-edge developer of scientific instrumentation was sourcing a small diameter ceramic bobbin requiring concentricity to three microns on a tiny axial bore. Although high electrical and wear resistance was required, there was indecision over-specifying YTZP zirconia or 99+ alumina.
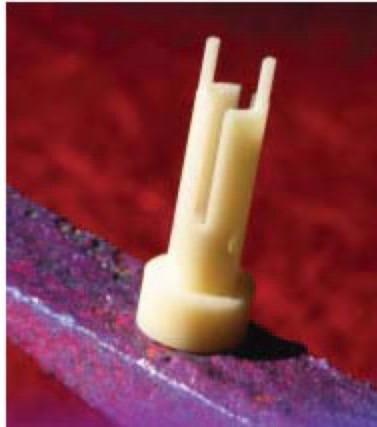
For a solution, with Insaco’s many years of machining experience with hardened materials, Zirconia was the recommended first choice for this application due to excellent impact resistance which might be vital with such a delicate design. However, being such a resilient material also makes diamond grinding tiny holes problematic and expensive. Alumina met all the stated requirements and was the lower-cost alternative once machining costs were included. To help the user decide, the first prototype order was split over both materials, without cost penalty, to allow real application evaluation.
Alumina more than exceeded performance requirements and was lower in cost for both material and machining. Production requirements have now been formalized for fine-grained, 99.5% Alumina, and reliability is proving excellent.
Tell us about the unique manufacturing process that solved metalized sapphire windows problem
So, a manufacturer of medical endoscopes needed metalized sapphire windows with extremely smooth optically polished faces to allow for hermetic sealing into a Nickel 200 tube that was brazed to the sapphire.
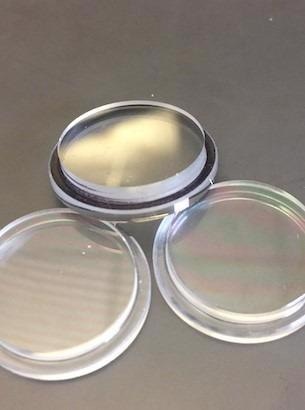
Therefore, Insaco recommended a unique manufacturing process at Insaco which would improve the overall quality of the sapphire window while allowing for improved hermetic sealing in order to autoclave the endoscope.
As a result, the manufacturing changes in the orientation of the sapphire window allowed for creating a strong hermetic seal which further enhanced the ability to autoclave the endoscope resulting in a 35% increase in overall yield on the final brazed sub-assembly.
How can precision ceramic gearing, in particular with precision zirconia (YTZP) be used to solve contamination problems?
What happened was that a semiconductor processor was having contamination problems from metal and plastic gears due to intense chemical, thermal, and high vacuum conditions. They were considering technical ceramics for chemical resistance, however precision pinion gear teeth must be not only uniform but strong enough to survive load.
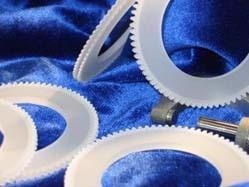
Then, based on fine features and point stresses in the application of precision ceramic gear, Insaco recommended Yttria blended tetragonal zirconia polycrystal (YTZP) ceramic material for toughness and resistance to chipping. The fine grain and unique crystal orientation actually absorb energy to fight fissure or crack propagation.
Continually, because of many years of experience machining sapphire as well as YTZP, Insaco was able to provide both materials. The precision machining required to generate useful gear profiles in sapphire was challenging, but the result allowed our customer to proceed confidently with technical trials. YTZP zirconia, being more robust, may still be the ultimate choice for production, but having the choice to fabricate with either material was the key to successful early trials.
About Insaco
Since 1947 Insaco has been a precision machining and polishing fabricator of parts from all technical ceramics, sapphire, glass, and quartz. They machine these materials to very precise tolerances (many times measured in millionths of an inch) for dimension, flatness, wedge, and roundness or cylindricity. Their customers typically have a critical application that requires extremely tight tolerances in ultra-hard materials. They also have the capability to grind and polish spherical radius parts in a variety of hard materials, both inside and outside diameters, to optical requirements.
About Scott D. Mittl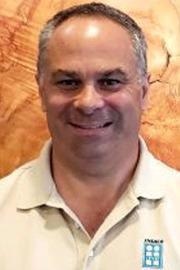
Scott D. Mittl, Sales Engineer, has been an employee of Insaco since 1990 and is responsible for sales engineering activity including quotations and account management.
He takes an aggressive proactive approach to develop new customers and new product applications. This approach includes developing subcontractors to offer new capabilities/services to our customers.
With his technical expertise and experience, he can provide guidance in designing products using the materials we machine. He has a B.A. in Applied Sciences and a B.S. in Metallurgy and Materials Engineering from Lehigh University and is a member of the American Ceramic Society.
Disclaimer: The views expressed here are those of the interviewee and do not necessarily represent the views of AZoM.com Limited (T/A) AZoNetwork, the owner and operator of this website. This disclaimer forms part of the Terms and Conditions of use of this website.