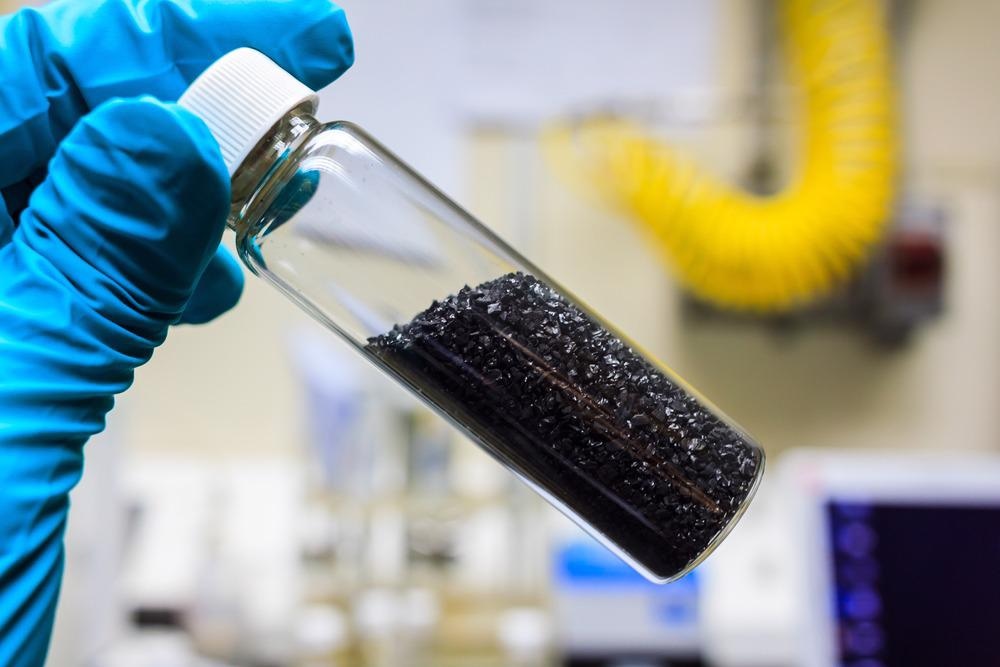
Image Credit: Eaum M/Shutterstock.com
Despite the misuse of carbon black (CB) and black carbon (BC) as synonyms, these materials differ considerably in their production processes and use in commercial products. Several different analytical tools have recently demonstrated the physical and chemical differences between CB and BC.
What is Carbon Black?
Carbon black (CB) is commercially produced under tightly controlled thermal conditions that can either occur in an inert atmosphere, otherwise known as partial combustion, or in oxygen-depleted environments through a process known as vapor-phase pyrolysis. Through these processes, aggregates of carbon nanoparticles are produced to form the final CB product, a fine black powder that is almost purely elemental carbon (EC).
CB is produced at the largest industrial scale as compared to all other nanocarbons. It has been commercially produced for more than 100 years and has an estimated worldwide production rate of over 9.8 million metric tons.
With an average price of $1 per kilogram (kg), CB is also considered to be far cheaper as compared to other types of nanocarbons, particularly carbon nanotubes and graphene nanoplatelets, which are currently sold at around $600/kg and $10,000/kg, respectively.
Applications of CB
Approximately 90% of all CB produced within the United States, Western Europe, and Japan is devoted to a wide range of rubber applications. Automotive rubber products, such as tires, tubes, tread, belts, hoses, and other miscellaneous items, as well as non-automotive industrial products such as industrial molded and extruded products, are some of the most common uses of CB.
When CB is produced for these products, the partial combustion process injects a combination of both an atomized spray of aromatic oils and an air-deficient fuel source, such as natural gas or oil.
The remaining 10% of commercial CB can be used for various products ranging from links and paints to plastics and coatings.
CB vs. BC
Both CB and black carbon (BC) are the end products of the incomplete combustion of carbon sources such as fossil fuels, biofuels, and biomass. Despite this apparent similarity in their production processes, the precise methods by which CB and BC are produced are fundamentally different on several levels. For example, CB is produced in an industrial setting for a wide range of commercial applications, whereas BC is an undesired byproduct.
Furthermore, the production of CB rarely causes CB particles to be released into the product, as these particles are often tightly bound in the matrices within tires and other rubber products. Comparatively, BC particles are usually released into the environment through ambient pollution and diesel exhaust. CB and BC's dominant exposure pathways vary greatly, as CB is predominantly associated with occupational exposure, whereas individuals are most often exposed to BC through the environment.
In addition to differing in how they are produced, CB's structure, which is graphitic and almost purely comprised of EC, is highly different from that of BC, which is often described as having a morphology that resembles aciniform or grape-like CB aggregates of highly fused spherical particles.
The concentration of organic compounds within CB is also particularly low, with an average of less than 2%. In contrast, BC tends to have a much higher concentration of organic carbon compounds, typically around 30% of the total mass. Some combustion soot products include organic carbon fractions that are up to 50% of their total mass and have higher ash contents than CB.
Methods to Differentiate CB from BC
X-ray photoelectron spectroscopy has been reported as a useful technique for differentiating CB from BC, as CB has S 2p core-line spectra, whereas BC, in the form of diesel soot, is not associated with these spectra. Despite its utility, the presence of elemental sulfur on the surface of either CB or BC will cause the S 2p spectra to be present, limiting its application for this purpose.
Transmission electron microscopy (TEM), dynamic light scattering spectroscopy (DLS), electrophoretic light scattering spectroscopy (ELS), and field-emission scanning electron microscopy (SEM) have also successfully been used to differentiate the physicochemical properties that exist between CB and BC.
CB particles, which are generally spherical, are typically formed in the size range of 15 to 300 nanometers (nm). Upon analysis by TEM and DLS, CB and BC can share similarities in terms of an aggregate appearance in some cases.
Ultimately, studies have found that it is not ideal to differentiate BC from CB samples in terms of their primary particle diameter, aggregated size, hydrodynamic diameter, particle size, zeta potential, sedimentation rate, or surface area, as significant differences between CB and BC in terms of these properties have yet to be confirmed.
Despite this finding, BC and CB samples' thermal treatment caused distinct differences in terms of how these samples responded. Whereas 96% of the CB mass remained after being heated to 1000 °C, the mass of BC samples reduced by 58%.
Another method that successfully allowed researchers to differentiate CB from BC involved comparing the atomic ratio of carbon (C), hydrogen (H), and hydrocarbons (H/C).
Moreover, the H/C ratio of BC samples is ten times greater when compared to those present in CB samples. Therefore, this finding suggests that a simple 100H/C-log(C/10)-1/H ternary plot can be used to distinguish CB from BC samples quickly.
References and Further Reading
Khodabakhshi, S., Fulvio, P. F., & Andreoli, E. (2020). Carbon black reborn: Structure and chemistry for renewable energy harnessing. Carbon 162; 604-649. doi:10.1016/j.carbon.2020.02.058.
Hong, J., Moon, H., Kim, J., et al. (2021). Differentiation of carbon black from black carbon using a ternary plot based on elemental analysis. Chemosphere 264(Part 1). doi:10.1016/j.chemosphere.2020.128511.
Long, C. M., Nascarella, M. A., & Valberg, P. A. (2013). Carbon black vs. black carbon and other airborne materials containing elemental carbon: Physical and chemical distinctions. Environmental Pollution 181; 271-286. doi:10.1016/j.envpol.2013.06.009.
Disclaimer: The views expressed here are those of the author expressed in their private capacity and do not necessarily represent the views of AZoM.com Limited T/A AZoNetwork the owner and operator of this website. This disclaimer forms part of the Terms and conditions of use of this website.