In this interview, Matthew Andrew Ph.D., Scientist from ZEISS Microscopy talks to AZoM about ZEISS Solution Lab and how it is revolutionizing customized automation in microscopy.
Please introduce yourself and tell us about your role at ZEISS?
My name is Matt Andrew and I sit within a group called Business Sectors, essentially customer representatives within ZEISS. My current area of responsibility includes the Solutions Lab program, which involves customized software development to help our customers achieve their goals.
How is the ZEISS Solutions Lab revolutionizing customized automation in microscopy?
Solutions Lab is an umbrella term for a new service at ZEISS which customizes our instruments and technology to specific application needs. As customers bring a myriad of sample types and imaging requirements, agile and flexible solution development is critical to meeting their goals.
One of the most critical technologies that we use is machine learning or AI. These technologies are incredibly powerful, but often need to be tailored to a particular customer problem. Training data needs to be generated, algorithms customized and tweaked, and workflows optimized. However, once we have built the workflows, they are so powerful they can solve problems that have been previously impossible!
For example, a steel producer might find the ZEISS is close to what they need, but perhaps the analysis needs to be set up differently and the report format changed slightly so it is compliant with some specific analysis standard. Or perhaps they like the data, but want some more advanced algorithms that can improve data quality. In the past, we had no way of addressing that in a dynamic, time-sensitive way- but we do now.
Another example, a car manufacturer needs an automated way to inspect every single car in a particular way to classify individual grains, zoom in on them and make measurements. This may have been extremely challenging to solve using traditional algorithms; however, with machine learning we use training data and models specific to this use case and string together all these components into a complete workflow.
Solutions Lab is the platform which allows us to do all these applications and can be applied across our portfolio of light, electron and X-ray microscopes. It is a personalized solution for each customer.
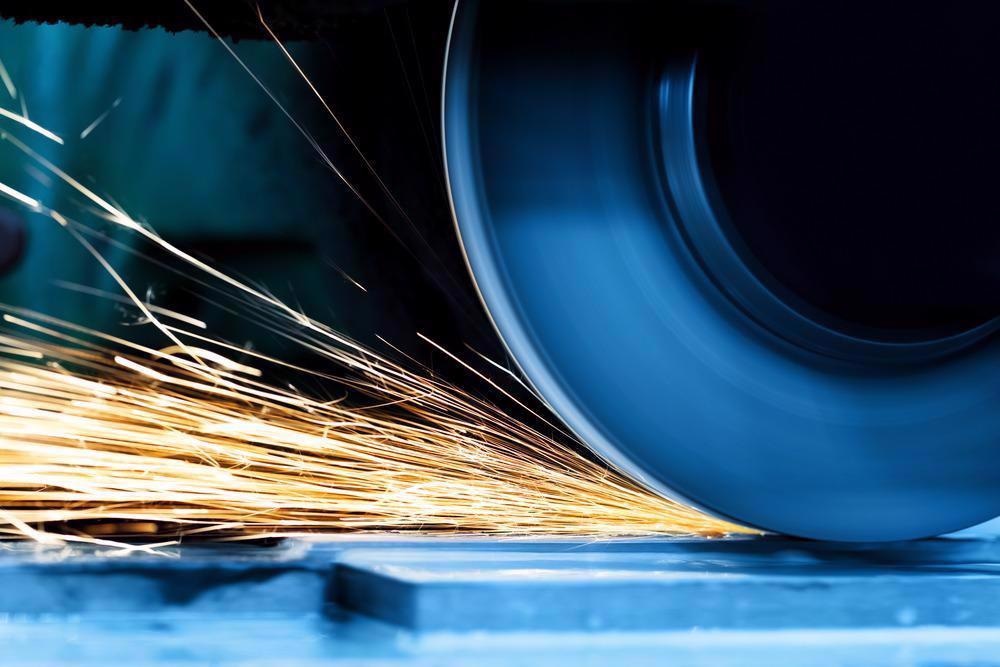
Image Credit:Shutterstock/Photocreo Michal Bednarek
In terms of advancement, what problem areas can the Solutions Lab solve?
We have a catalog on our website and you can see a whole range of different solutions that we have tested. We have applications for the mining industry, the pharmaceutical industry, for the oil and gas industry as well as a broad set of solutions for metallography. We have also worked on solutions for the aerospace industry and for automation across a wide range of manufacturing. As volume manufacturing is inherently about making the same thing repeatedly, a certain level of automation is highly desirable!
Across our industrial segments, we have partnered with universities with technology-driven research interests and utilized this capability to prototype new technologies or give a particular customer access to technology that would not otherwise be available. For example, for a university buying a high end scanning electron microscope (SEM), we have built solutions that allow for STEM tomography. STEM is scanning transmission electron microscopy and has an extremely high spatial resolution.
The advantage of STEM is that it is a lot cheaper than a normal transmission electron microscopeand we can build up a three-dimensional image of the sample by doing electron tomography.
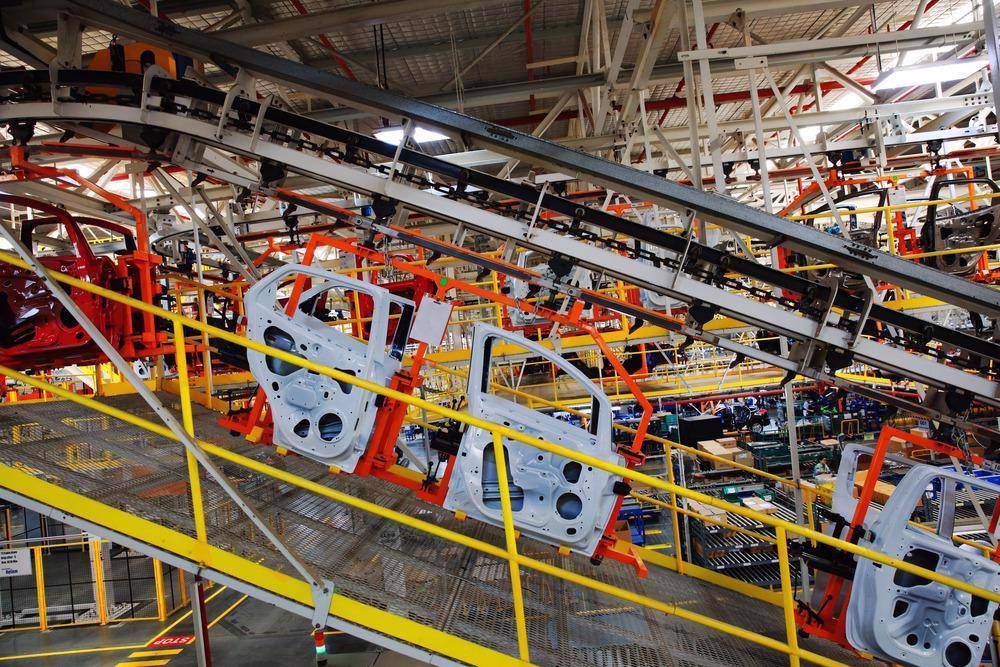
Image Credit:Shutterstock/naraichal
How does the Solutions Lab create unique, tailored solutions across different applications, such as academia or large industries?
Solutions Lab is very application-agnostic.
ZEISS will partner with any application set and has done a lot of work already in the manufacturing industries, pharmaceuticals, raw materials and extractive industries, as well as both oil and gas and mining and with the academic material science. There are no limits to the applications that can be addressed with this capability!
To do this, we make use of modern development practices and tools when building workflows. This does not just mean using agile development (which of course we do use) but leaning on specific technology building blocks and platforms that ZEISS has invested in over many years.
There is, for example, a strong lean towards modularity in the codes and tools that we build and use. This has been formalized using a set of tools that we have had for a couple of years now. And maybe some of the readers have seen something called "APEER".
This is an online platform, but fundamentally that online platform is based on the modularization of solutions. This allows you to put a little bit of code and image processing (e.g. a machine learning workflow) into a box. Then, the computer can abstract that box from every other part of the workflow, just defining what goes into and out of the box.
This is really important in terms of the long-term sustainability of development efforts like this because it allows you to modify discrete portions of a workflow without affecting other portions. You can then run really fast and solve individual bite-sized chunks of problems without having to bite off the whole problem itself.
The virtualization technology behind it also allows you to be more confident about its long-term supportability, shortening your development time and speeding up development cycles. This makes the customization of specific workflows more practical. We lean strongly on this containerized, virtualized, modularized approach as it also lets module snippets be re-used in future developments relatively easily.
The workflows themselves are built around our main software platform ZEN. ZEN has an engine inside it that allows us to insert arbitrary workflow portions, accepting modules from the APEER framework. It also has workflow-building tools, which allow for multiple modules to be strung together into a solution.
When our global team create one of these solutions, they are both building new blocks and using pre-existing blocks into an integrated solution.
How is the Solutions Lab revolutionizing particle analysis in materials research in particular?
Particle analysis in 2D is a well-established set of techniques and technologies. At ZEISS, we have been doing it forever using both light and electron microscopy. Three-dimensional particle analysis is very new and utilizes noninvasive 3D imaging techniques, particularly X-ray microscopy, to look at particles in three dimensions. There are many different applications for this technology, three of which are of particular interest.
The first is for the mining industry. When a mineral ore is processed, called comminution, it is crushed into fine powder to expose the minerals of interest in the ore. It then goes into either a flotation or leaching process, which needs minerals of interest to be on the surface of a particle. Three-dimensional imaging determines the relative distribution of all the minerals in a sample to the particle surface. This uses the following workflow:
- A 3D X-ray tomography is fed into a machine learning-based pixel classification routine which separates out all the individual mineral phases. Connected particles are then separated using an advanced multiscale morphological object separation.
- Then, on a particle-by-particle basis, we can perform exposure analysis on the different minerals in the rock, generating a three-dimensional report of what minerals are in contact with other minerals and what are in contact with the outside of the particle (exposed or liberated).
Now, if we abstract ourselves from that application to examine the generic workflow, we have taken an X-ray image segmentation, performed particle separation and then performed analysis. This can be used for a range of other applications as well.
When looking at additive manufacturing (3D printing), there is a particular problem in the powders that are used as an input to the powder printing process, particularly for metal additive manufacturing. Traditional powder characterization techniques really struggle with the characterization of included particle porosity (little holes inside of the particle at the powder stage), and this is strongly correlated to defects in a final printed part. Access to that cannot be gained from the outside; you need to noninvasively image it in 3D - this is where the X-ray techniques come in. The exact same technology we used in mining (X-ray imaging and the workflow around it), can be used to get porosity analysis for additive manufacturing.
Finally, I want to talk a little bit about the application of this technology where we are looking at respiratory drug delivery. This is a particle analysis problem but for lactose and sucrose particles inside of an inhaler. The size, orientation and the relative coherence of different phases within the particle makeup are the areas of interest, particularly in which particles are in contact and where. Using X-ray imaging, phase techniques can be added to the particle analysis workflow, as we are imaging low-density things at very high resolutions with very low energies. After adding this phase imaging component, the particle analysis looks very similar to the sorts of problems present in mining or in additive manufacturing. Generically, we address these applications quickly in multiple different application areas by reusing technology and customizing the new workflow to a particular customer’s needs.
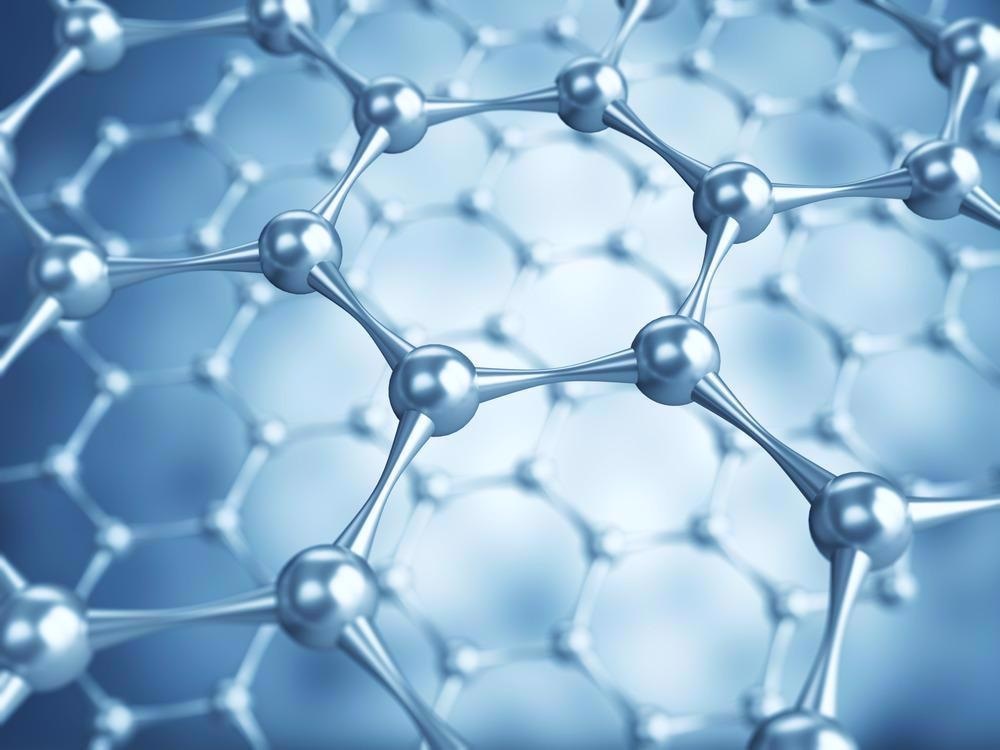
Image Credit:Shutterstock/AnnaKireieva
What is the benefit of showing these solutions publicly?
I would say that the benefit is in terms of building awareness in a network of things that have been done and things that we sold. People often simply do not know that technology is available to solve their problems. We share solutions publicly to try and tell them!
We want to get the awareness up of the sort of things that you can use microscopes to solve.
By making the solutions available online, we can offer a single one-stop repository of solutions for a whole array of different customers where they can find the things that have been solved already by other people around the globe.
It is about creating that kind of network to increase the visibility and awareness of this technology.
How does requesting a solution work?
If you know your local ZEISS representative, you can always start with him/her. If you don’t, there is an online form that will get you directly in contact with us.
After we are in communication, we will work to understand your problem a bit better and then propose a solution. We then respond with an offer and work collaboratively over an iterative process over a few months to deploy the solution to ensure your success.
What ZEISS systems and components can the Solutions Lab be used with?
ZEISS is a very big company that makes everything that has a lens in it. It might be dimensional metrology or semiconductor manufacturing or microscopy.
In Solutions Lab we are focused on building solutions for our microscopes, broadly grouped into three major product classes: light, electron and X-ray microscopes.
Solutions Lab offers the option of keeping solutions local without cloud interruption. How can this benefit customers?
There are two major reasons people do not want to go to the cloud.
The first thing people are worried about is security. Modern cloud platforms underpin some of the most secure implementations on the planet, but there is still a lot of perceived risk. People want to keep their data on their own servers and be responsible for it themselves. We provide solutions on-premise, without the requirement of cloud interaction, if that is a requirement. That is why we built these modular components to be able to be downloaded and workable offline.
The other major issue with cloud implementations is bandwidth. Information-dense microscopes, like an X-ray microscope or high throughput scanning light microscopes, or one of our three dimensional light microscopes, produce terabytes of data. Getting them up and down to the cloud is no mean feat, so dealing with the data on-site can be useful just because of upload / download speeds!
How does the ZEISS Solutions Lab compare to other software on the market today?
My answer here is confined to microscopy and high-resolution imaging. Within this, there are small companies that offer a level of software customization but do not have the solid platform, reach or advanced technology that ZEISS offers.
In the major players in the microscopy market, ZEISS is the only company engaged in this level of integration and partnership with customers. It offers a unique edge over our competitors.
What is the future of ZEISS Solutions Lab and how is it going to benefit the scientific community?
One of the things that I am excited to see in some of the solutions we have generated with Solutions Lab being integrated into more standard product offerings. If you build a solution for one customer, it is likely that there are others who want to do a very similar. It is really gratifying when you can see technology that you prototype for someone scale to the entire fleet of systems going out the door.
In terms of tech trends, I think that the AI and machine learning technologies have a lot of distance still to be run in their integration in our kind of imaging technologies. I expect to see a lot more from that space, including the development of more broadly usable technology coming out in the months and years ahead.
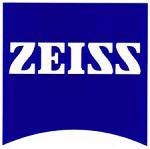
This information has been sourced, reviewed and adapted from materials provided by Carl Zeiss Microscopy GmbH.
For more information on this source, please visit Carl Zeiss Microscopy GmbH.
Disclaimer: The views expressed here are those of the interviewee and do not necessarily represent the views of AZoM.com Limited (T/A) AZoNetwork, the owner and operator of this website. This disclaimer forms part of the Terms and Conditions of use of this website.