New technologies shift paradigms and bring change in their wake, and that certainly the case with what is termed the Internet of Things (IoT). It is regarded as one of Industry 4.0’s enabling technologies, and in the manufacturing sector, it has been labeled the Industrial Internet of Things (IIoT).
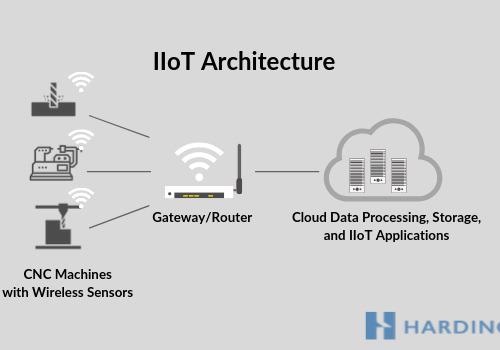
Image Credit: Hardinge Inc.
Though still in their infancy, IIoT technologies are already showing benefits for early adopters through applications such as smart factories.
Research carried out by Bain & Company indicates that the value of the industrial portion of IIoT - which covers hardware, software and system solutions in the manufacturing, building, infrastructure and utilities sectors - could be worth up to $200 billion in 2021.
IIoT will almost certainly affect the metalworking industry. This article provides an overview of the best approach to negotiating the changes it will bring to the sector.
What is Industry 4.0, and How is it Connected to IIoT?
Industry 4.0 is a range of technologies bringing seismic shifts to the manufacturing sector.
BCG, a management consulting firm, says that Industry 4.0 will facilitate the gathering and analyzing of data across machines. This will enable processes to operate with increased speed, efficiency and flexibility, ultimately producing greater quality goods at reduced cost.
Over the coming decade, companies will be able to utilize digital manufacturing technologies to link physical assets together, generating a stream of data across the value chain.
This will allow manufacturers to connect the product life cycle at every point, from the design stage to sourcing, production and distribution, point of sale, and the end-user. IIoT utilizes and connects software, sensors, networks, cloud computing and analytics - a grouping of technologies able to make every machine ‘smart.’
How Does IIoT Work?
IIoT solutions can vary in composition, but each will encompass the following five fundamental functions:
Data Collection
Sensors are a primary form of data collection, constantly monitoring and collecting data; for example, energy usage or environmental and operational conditions such as vibration, temperature, downtime and time-to-complete.
Though sensors will eventually become a standard part of CNC machinery, replacing all current plant and machinery with sensor-enabled equipment may not currently be possible for companies wishing to take advantage of IIoT.
In such cases, retrofitting machines by adding external, sensor-bearing devices can allow these to be IIoT-compatible. These cost-efficient alternatives bolt onto existing equipment and contain connectivity, sensors and control functionality.
Connectivity
Sensors and retrofit appliances are connected to a network via wireless or hard-wired connections. A wireless option will reduce costs and complexities related to the need for dedicated wiring. It also allows for machines to be located in areas where wiring is restricted or too expensive to utilize.
IIoT uses a variety of common wireless protocols: WiFi, Zigbee, cellular, Near Field Communication (NFC) and Bluetooth (Low Energy). To determine which protocol is the most appropriate, a range of variables such as environment, location, distance and IIoT platform should be considered.
Edge Computing
Large volumes of data are gathered from machines, placing networks under considerable pressure. An efficient solution for this potential problem is to pre-process data on a device, with only the data that has value being sent to the cloud for storage and analysis.
A network manager, also called a router or gateway, is a hardware and software device located at the periphery of the IIoT network. Located between the factory and internet/cloud, it provides a linking point between the plant and cloud platform.
Software managing the network or gateway carries out a number of functions, aggregating and pre-processing the data collected from sensors and IIoT devices and then transmitting this to the cloud for storage and utilization in IIoT applications.
Another function involves receiving data and commands from IIoT applications, which are passed back to IIoT devices, triggering some type of activity in machines; for example, causing these to shut down.
Cloud Data Processing and Storage
Any data collected will need to be stored for utilization in IIoT applications, allowing manufacturers to analyze, revealing patterns in machine operations, for example, vibrations in machinery at a recurring time or unexplained lulls in production.
This enables the manufacturer to uncover any root cause for these issues and carry out corrective procedures as appropriate.
Cloud computing is unique in that it offers the potential to scale up rapidly, efficiently storing and processing the large quantities of data that IIoT produces. This is not generally cost-effective when carried out on-site.
IIoT Applications
Remote monitoring and predictive maintenance applications can analyze collected data, allowing results to be presented in what is known as a dashboard format. As a primary user interface, a dashboard offers a straightforward way to understand complex data.
The dashboard can show key performance indicators (KPIs) - such as efficiencies or inefficiencies - in a format that is graphical or user-friendly, offering users accessible insight into machine operations that can help them better formulate future decisions.
Taking Advantage of IIoT
Many companies are currently taking the time to explore the potential of IIoT, evaluating the investment required to best take advantage of the benefits of employing smart technologies.
IIoT will lead to increased efficiencies in CNC machines, resulting in lower wastage, lower costs and decreased downtime by allowing for predictive maintenance.
Harnessing the improved efficiencies offered by IIoT and taking advantage of its ability to reduce downtime ultimately affords businesses the opportunity to increase profitability.
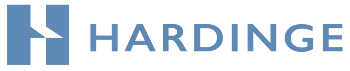
This information has been sourced, reviewed and adapted from materials provided by Hardinge Inc.
For more information on this source, please visit Hardinge Inc.