Manufacturers are placed under immense pressure to balance keeping up with developing trends with keeping costs under control and maintaining productivity at an optimal level.
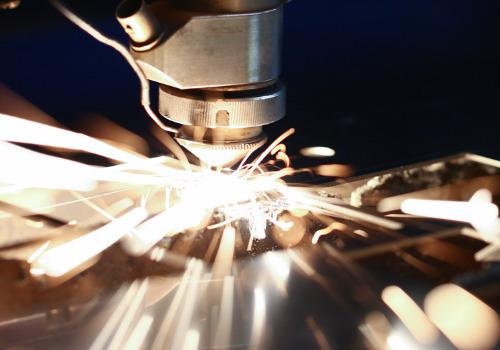
Image Credit: Hardinge Inc.
Customer expectation, the desire for increased customization, growing costs, the need to increase efficiency, and shorter lead times all play a role in making component production ever more complex.
A recent addition to this list of considerations is the requirement to produce workpieces and parts to a level of detail and accuracy not typically achievable with conventional lathes or turning equipment in a cost-effective manner.
The bearings sector, along with vertical industries, including transportation and aerospace, are seeing the emergence of new, more efficient product designs that require complex components with extremely tight tolerances.
Workpiece accuracy is an essential factor in meeting crucial equipment design standards, along with ensuring peak performance of the final product. The need for extremely accurate workpieces can challenge the machine tool capabilities of some providers.
Process automation involving modern CNC machining capabilities has enabled manufacturers to deliver a range of products, from prototypes to finished fabricated parts, with greater precision and in a shorter period of time.
New workpiece requirements involving exceptionally tight tolerances could be beyond the present capacities of CNC machine tooling equipment.
As a result, manufacturers must explore approaches to repeatedly and consistently produce parts that meet customers’ exacting tolerances. While grinding machines may attain the accuracy and precision expected by customers, it is a time-consuming, costly process that results in challenging grinding by-products.
Changes in technology allow turning to achieve a comparable level of accuracy to grinding, but more quickly and cost-effectively. This has allowed manufacturers to reconsider their method of production, re-evaluating what have been historically regarded as ‘normal’ abilities for turning centers and lathes.
The Importance of Precision
Customers expect parts to meet their engineering specifications consistently and repeatedly. Manufacturers need to utilize what are known as super-precise turning centers to create complex workpieces that attain meticulously precise detail and form tolerances in an efficient and uniform manner.
These super-precise turning centers combine best practice design with hardware and software that is integrated into a production machine tool capable of delivering precise results with minimum person hours on a consistent basis.
Ideal for intricate items with a high level of detail, super precise turning centers not only allow for delicate part handling but also for components to be finished in a single setup.
Their ability to work with a range of materials, combined with the option to pre-configure them to manufacture complex parts, means they can offer high repeatability, accuracy and extraordinary finish quality in an effective manner. They can also ensure there is no variation between production runs regardless of time scales involved.
Defining Super Precision
Numerous machine tools currently offer standard resolutions of 0.0001 ″; however, new industry specifications can require machinery that incorporates 0.000010 ″ programmable resolution abilities, a standard many manufacturers may not be able to achieve.
Contemporary super precise turning centers allow for accuracy in the lower range of diamond-turning machines, offering cylindricity of less than 1-2 μm and turning out pieces that are within the 2 μm range.
With super precise turning centers, manufacturers are able to achieve exceptional performance, meeting demanding standards of up to 0.5 μm - half the size of a typical bacteria cell.
The Importance of Form Tolerances
Workpieces need to accommodate not just precise details but also form tolerance standards and the required geometric form, including cylindricity and roundness. Super precise turning centers can produce workpieces with exact surface form and finish tolerances from 2D to 3D accuracy.
Ensuring Stability
Super precise turning centers require an extremely stable base to deliver exceptional levels of accuracy. This need for unrivaled stability and extraordinary stiffness is essential if they are to offset high-pressure forces in the machining process while inhibiting thermal deformation and twisting.
Overall, this level of stability is essential in ensuring super precise cutting performance and exacting part accuracies.
The New Normal
Super precise turning centers allow for the consistent production of parts that are perfect, uniform and meet the exact needs and specifications required, typically facilitating the customization of parts to meet specific application design standards or unique customer needs.
Hardinge’s industry-leading SUPER-PRECISION® turning equipment is suitable for a wide range of applications.
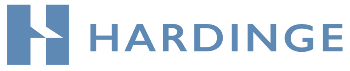
This information has been sourced, reviewed and adapted from materials provided by Hardinge Inc.
For more information on this source, please visit Hardinge Inc.