It has been over fifty years since humanity first landed on the moon as part of the 1969 Apollo 11 mission. The aerospace industry has changed a great deal since those days; for example, privatization has occurred in the space exploration and travel sectors.
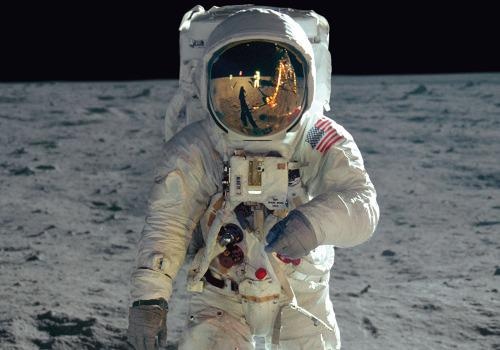
Image Credit: Hardinge Inc.
In recent years, companies such as Blue Origin, SpaceX and Virgin Galactic have been developing commercial space vehicles and reusable space rockets. The aerospace manufacturing sector has expanded to include guided missiles, aircraft, aircraft engines, space vehicles, propulsion units and related components.
Space exploration and air flight have been revolutionized by advances in aerospace technology that have led to improvements in power sources, engine/wing design and materials that are now lighter and stronger.
These important advances have led to growing demands in aerospace manufacturing, especially in relation to adherence to requirements. When the smallest imperfection can generate the most catastrophic of results, there can be no room for error.
Aerospace Industry’s Demand for Precision
The aerospace and defense (A&D) industry is one of the most highly regulated industries. Manufacturing environments and procedures are diverse and complex, involving a mix of heavy-duty and sophisticated functions.
As a result, product specifications may require suppliers to accommodate not just sizeable and unwieldy parts but also complicated machining requirements.
A&D manufacturing is an industry where custom work is standard, as parts may need to be manufactured or engineered to order. This trend towards customized solutions requires specialized workholding and tooling solutions.
Manufacturers also need to demonstrate flexibility. Engineering change notices can require multiple alterations to components or products, impacting the sourcing of components and subsequent manufacturing methods.
The aerospace industry has made great strides in the design of gas-powered turbine engines. Jet engine manufacturers expect very close tolerances; consequently, they are highly dependent on their suppliers’ ability to provide precision castings, forgings and machinery.
Unsurprisingly, suppliers will encounter rigorous standards when it comes to ensuring the quality, oversight and reliability of these important components.
Workholding Requirements
Suppliers to the A&D sector need to have satisfactory workholding capabilities in order to meet the industry’s precise expectations. Employing an appropriate workholding solution means a supplier can offer the optimum level of precision in machining operations. It can also enhance flexibility in facilitating multiple part configurations.
Being able to securely clamp large parts is vital, even in instances where the majority of the material is likely to be removed. The ability to smoothly manage changeovers within part families or between part types may also be required.
Forkardt’s engineers have a wide range of experience in the workholding industry, particularly in providing innovative solutions and reducing set-up time while retaining precise workpiece placement.
A simple 3-jaw chuck offers a ‘one size fits all’ option to suppliers; however, it is imperative that a potential workholding solution offers a good fit with the product requirements.
The correct workholding solution means A&D manufacturers can reduce labor costs, time involved in necessary tool changes and idle spindle time. The right solution will also lead to less manufacturing time lost, fewer rejected parts and fewer work delays.
Forkardt’s experience allowed the company to successfully support a New England A&D supplier to accurately finish jet engine compressor blisks that came from another facility in a semi-finished form.
The company accomplished this by supplying a system that allowed for the adjustment of the fixtures’ lateral runout by means of just a pair of adjusting screws. This bespoke solution also enabled an entire family of collet chucks to be used for flexible production changeover in under 5 minutes.
Handling Special Materials with Speed and Accuracy
Working with specialist materials can be challenging. Maintaining optimal accuracy and production speed can be difficult when cutting and drilling materials such as ceramics, beta alloys and titanium, materials that are favored by aerospace engineers as they strive to reduce material costs and weight.
These materials are hard to machine and can generate a high degree of cutting force, affecting machining speed and accuracy. With the correct workholding solution supporting the workpiece, deflection caused by such cutting forces can be reduced or even eliminated. This can result in a higher first run yield for the machining procedure.
Forkardt – The Ideal Partner for Aerospace Manufacturing
Forkardt (a Hardinge brand) understands the unique workholding requirements of the aerospace industry, specializing in the design and manufacture of high quality, high precision, custom designed and specialty rotating workholding devices for machine tools.
Working with industry engineers and designers, Forkardt offers customized solutions to the aerospace industry globally. Using a manufacturer’s prototype and details of production needs, the company offers tooling solutions that enable the optimal machining of gas turbine engine parts, as well as other A&D components.
Forkardt-engineered solutions have held parts such as blisks, turbine blades, spools, nozzles, cones, AFT shafts and rotors for a wide variety of component manufacturers.
Tooling solutions offer optimal results when it comes to the machining of components of gas turbine engines, for example, compressor rotors, spools, cones, nozzles and blades.
Other Forkardt solutions include chucks for general machining, application-specific chucks, chucks for hard part turning, cylinders and indexing chucks, collet chucks, steady rests, expanding mandrels and grip force meters.
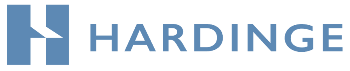
This information has been sourced, reviewed and adapted from materials provided by Hardinge Inc.
For more information on this source, please visit Hardinge Inc.