Quality and productivity are the keys to successful manufacturing. Testing machines are employed to assess the quality of raw materials like composites, steel alloys, plastics and rubber, and components including packaging materials, medical devices and fasteners.
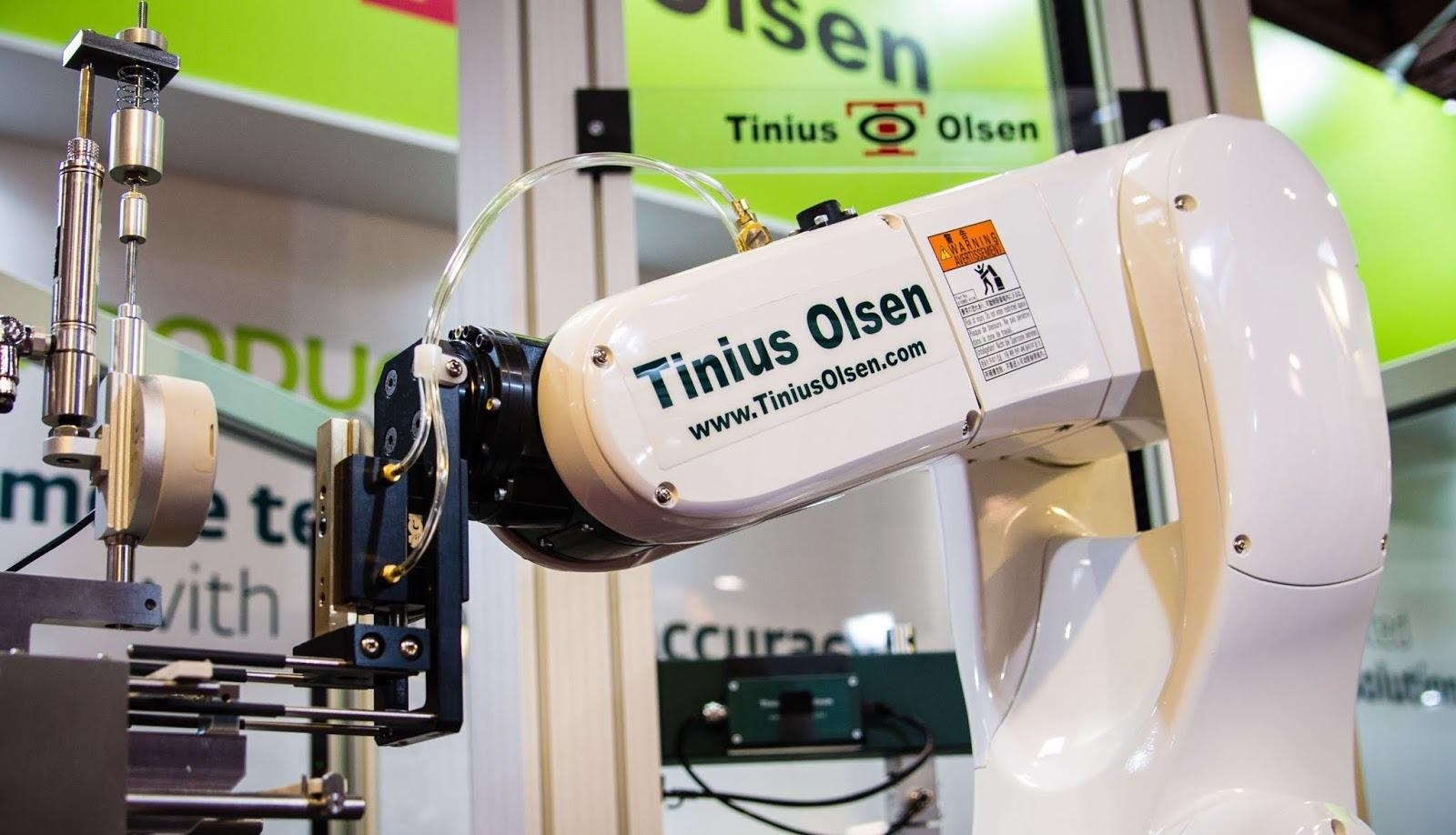
Image Credit: Tinius Olsen
Today, manufacturing processes are usually automated to some extent, although the quality process is usually manual.
Generally, this is time-consuming and involves entering reference data, carrying out test procedures, reporting on the results, preparing the testing machine, beginning the test, qualifying and accepting the results and appending comments before taking away the materials.
Materials testing has historically consisted of an operator utilizing single or multiple stations. In terms of operator time, where speed is vital, this historic way can be uneconomical; for instance, testing is required 24 hours a day in testing threaded fasteners for the aerospace industry.
One sector which could benefit from automation is drug delivery in the biomedical industry. Drug delivery tests are carried out on three individual stations with multiples of those stations, and lab operators working 24 hours a day loading, testing and removing the parts.
Yet, there is a discrepancy in manufacturing where businesses will pay for the automated manufacturing of products. No matter the size of the business or its industry, the testing of the materials utilized in the product is still based in the domain of manual workers.
The expense of introducing automated testing into the manufacturing process, and if a business believes it has enough samples to justify them, has been a barrier to smaller companies due to the amount of money that would be needed to supplant human operators with robots.
This has led to the development of scalable, automated testing systems, which can provide manufacturing businesses with an alternative to manual testing, with long-term advantages.
Tinius Olsen, UK, claims there are gains to be made, with their figures noting that an operator might spend 8.4 hours per 24-hour day watching and waiting for tests to run.
A robotic system can run all day and night, resulting in weekly gains of 59 hours against an operator, a total of 127 days over the course of one year. This means that with increased productivity, more tests can be performed.
The technology is versatile to accommodate any material or components and can be designed, developed and scaled to fit a business’ requirements. The idea is it can run single or multiple tasks at any combination or size.
Creating a scalable building block approach enables systems from low force applications of just a few newtons to very high force applications of a thousand kilonewtons or more.
Built in 1891, the Little Giant, Olsen’s first machine, was the first to combine and accurately carry out transverse, tensile and compression tests in one instrument, housed in a single frame.
This same design method is now seeing developments in fully automated testing, whereby numerous machines can be placed into a cell with single robot control. This can feed multiple materials, performing tests including tensile strength, hardness and flexibility.
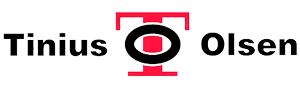
This information has been sourced, reviewed and adapted from materials provided by Tinius Olsen.
For more information on this source, please visit Tinius Olsen.