Robotic exoskeleton technology has been around for almost sixty years, but the most recent advances in its composites base render it an integral part of missions to Mars in the 2030s.
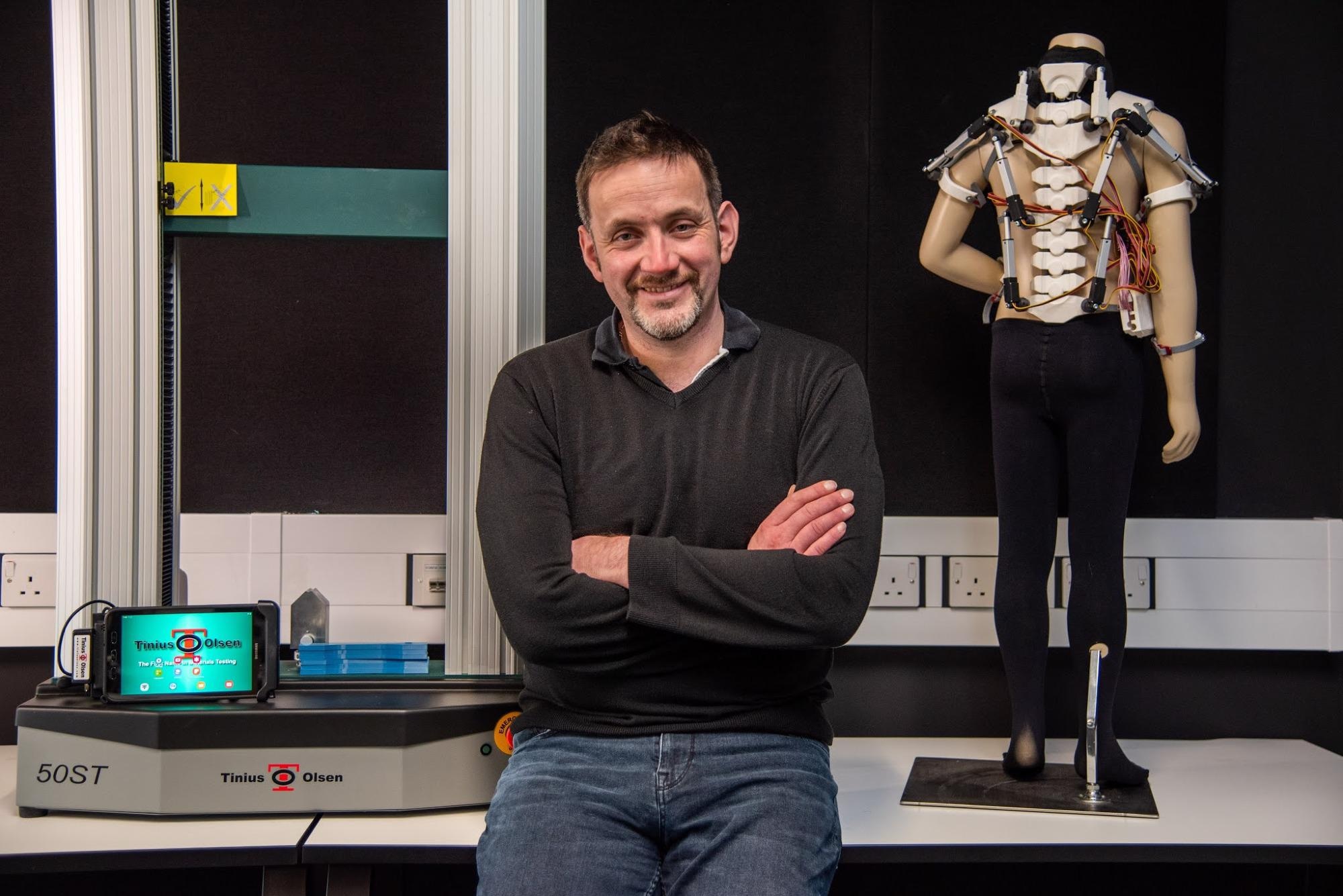
Image Credit: Tinius Olsen
To many of us, the term exoskeleton conjures up images of body armor clad superheroes, such as Iron Man or even Batman, or is reserved for the realms of science fiction.
While most of these have come from the fertile imaginations of writers and artists, the equally fertile lobes within the scientific community are turning this science fiction into science fact.
A rigid structure that wraps around the body and is often utilized to assist joint movement is known as an exoskeleton. This ‘exosuit’ aids the wearers’ muscles to contract and extend and acts like an artificial muscle.
It was in 1965 that the development of the first robotic exoskeletons began. This was when General Electric developed the Hardiman, a large full-body exoskeleton designed to augment the user’s strength to permit the lifting of heavy objects.
At the end of the 1960s at the Mihajlo Pupin Institute, Serbia, and in the early 1970s at the University of Wisconsin-Madison in the US, the first exoskeletons for gait assistance were developed.
Dr. Matt Dickinson, Senior Lecturer in Mechanical Engineering at the University of Central Lancashire in Preston, teaches in areas around concept design, with a special focus on the application of composite materials via 3D printing technology. He works from the University’s new multi-million pound Engineering Innovation Centre.
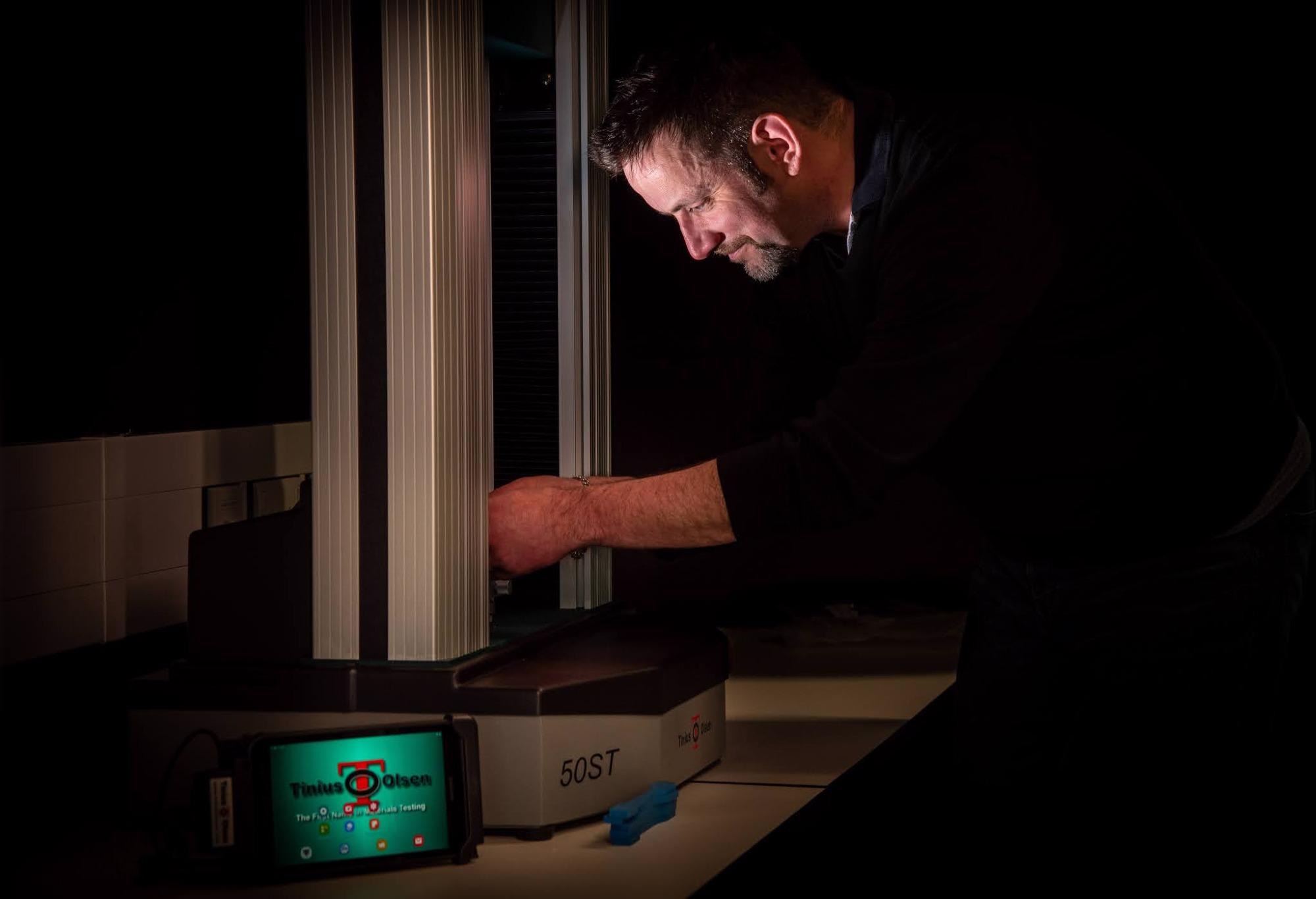
Image Credit: Tinius Olsen
“I’ll be honest, if you told me three years ago we’d be on the verge of developing world leading exoskeleton technology, I’d have questioned your sanity, but here we are,” said Matt.
It all started thanks to a local teenager who won the regional Primary Engineer competition back in 2019.
Luckily, it was my responsibility to assess each entry and this one instantly struck a chord with me, as it simply asked why there is no special suit, or exoskeleton, that a child with muscular disease can wear to aid with mobility. To me, it was such an obvious idea that there must be one out there already but how wrong I was!”
Dr. Matt Dickinson, Senior Lecturer in Mechanical Engineering, University of Central Lancashire
Design was the main reason for this lack of development. For example, how do you produce a suit that is lightweight enough to be practical, ‘grows’ with its host, and is also low cost and accessible to all?
As a mechanical engineer, my first thought was to produce the suit out of aluminium, which looking back, would have been totally impracticable as well as being horrendously expensive to produce.”
Dr. Matt Dickinson, Senior Lecturer in Mechanical Engineering, University of Central Lancashire
The required material had to be lightweight and accessible, but it also needed to be affordable. In short, the technology would be impracticable if no one could maintain it or if lower income families couldn't afford it.
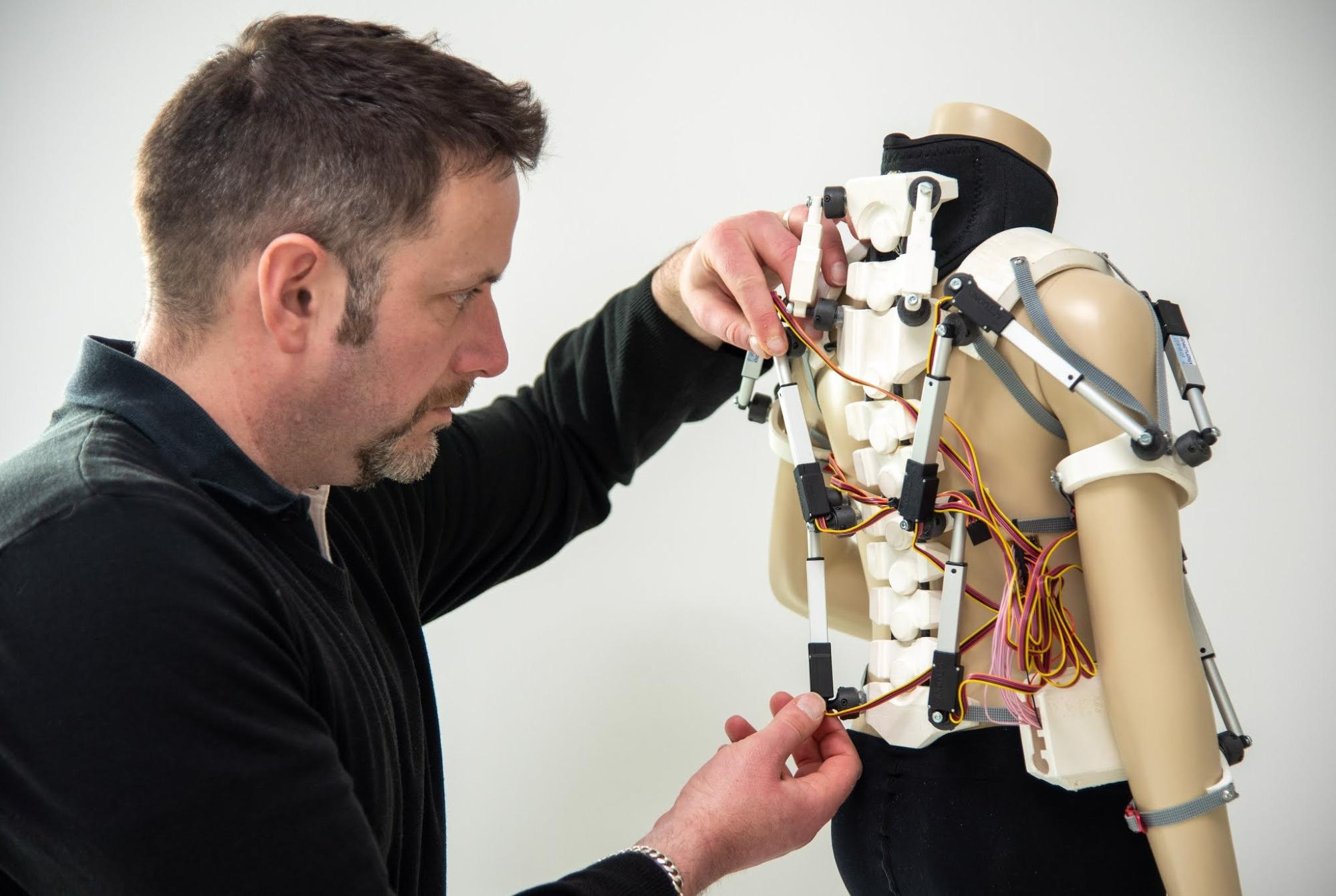
Image Credit: Tinius Olsen
“The structure of the suit is what's called a passive design system, meaning it’s part exosuit, which acts as a point of contraction, like a muscle but is also a passive exoskeleton, which distributes the force and load.”
“By taking these two approaches we are attempting to combine both of these technologies to build a hybrid system that will support the human frame and also aid in the muscle contraction and extension, which has led to the development of a new bespoke actuation method that we have designed.”
“The material I initially looked for with the potential to support this criteria was polylactic PLA. At this point, nobody had tested the material to see if it was capable of supporting the human body but the results soon indicated we had hit on something extremely special.”
The suitability of the composite was proven by the first iteration of the design, although the potential for the lactic acid in human skin to impregnate the material and issues with the material's reaction towards UV light had to be addressed.
“Skin can sometimes activate the lactic acid within the material, which would see bacteria forming and ultimately compromise its structural integrity. This led us to incorporate a material embedded with copper nanoparticles, that creates a barrier between body sweat and the composite - a perfect anti microbial if you like,” said Matt.
Chopped carbon PET is also being explored. This is because of the extra strength offered by the composite, which would be used as the core of the supportive structures of the suit, encased in carbon fiber and poly lactic acid.
“Basically, as with all projects such as this, things are continually under development. These are the materials we’re moving forward with at the moment but we’re continually looking to develop new composites that may supersede them,” continued Matt.
At this stage we couldn’t move any further forward until we had a better understanding of the mechanical properties of these materials, which is where Tinius Olsen comes in.
Dr. Matt Dickinson, Senior Lecturer in Mechanical Engineering, University of Central Lancashire
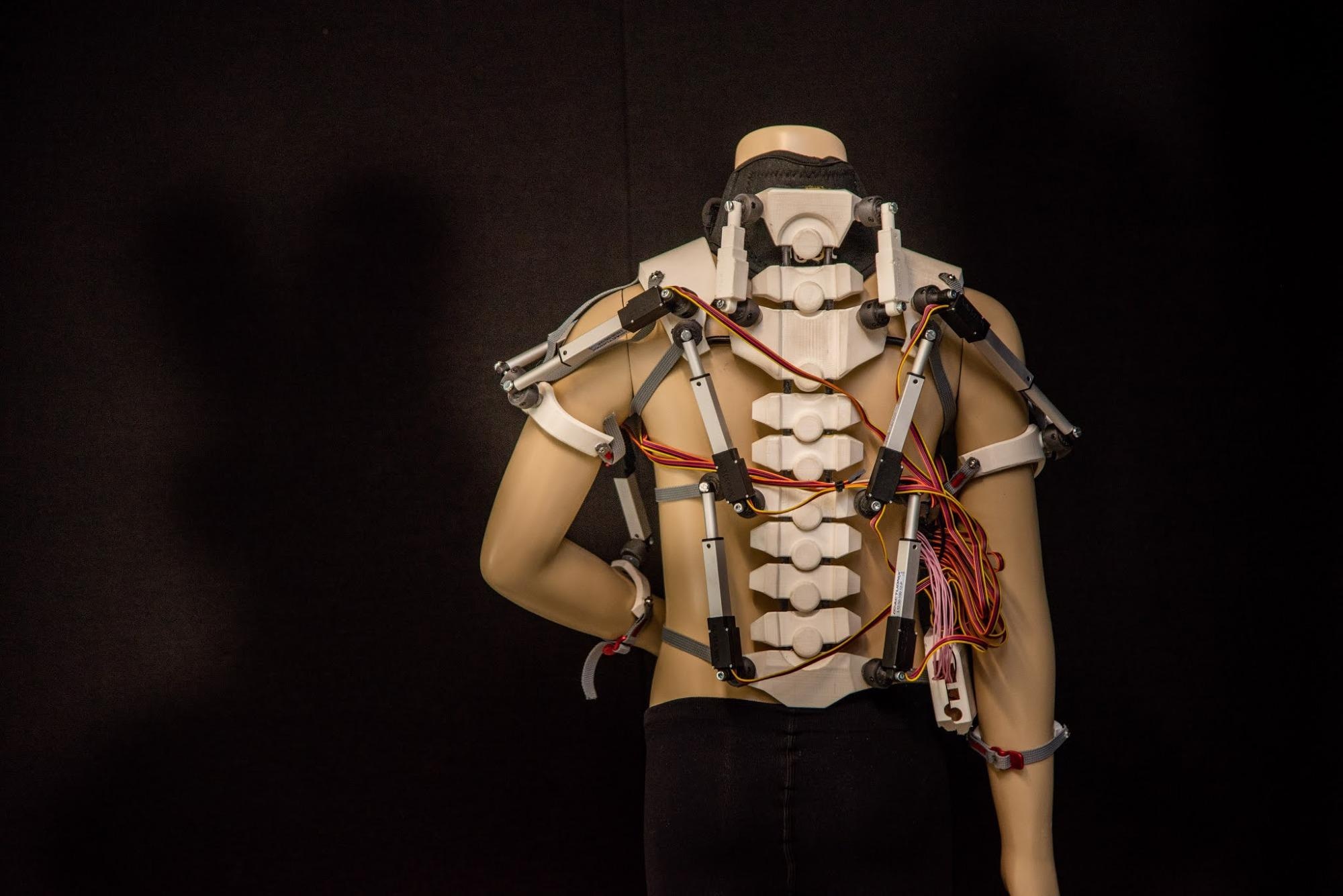
Image Credit: Tinius Olsen
The scene for the working partnership was set at a chance meeting at one of the UK’s major engineering shows. This meeting has seen the company loan, initially, a platform for optical extensometry, a 50ST testing frame, load cells and the company's powerful Horizon testing software. Where required, technicians are also on hand to give direction and advice.
However, the partnership goes much further than just machinery and advice. Matt was introduced to ASTM International through Tinius Olsen, becoming Subcommittee Chair of the F48.04 Committee for standards in exoskeleton development.
“Primarily, what the ASTM F48 Committee are looking at, as with any R&D project that is going to be utilised with human use, is failure fatigue of the components that are being utilised.”
“There’s also the life expectancy of the components and or material being utilised, through the usual compression, tension, and bending movements of everyday use. The Tinius Olsen machine and instruments we now have at our disposal will enable us to undertake this required testing at a much greater rate, literally taking years off the R&D time.”
“The doors this association has opened for the project are substantial, we have literally been catapulted from a lab in Preston onto the international stage, which has seen this development move forward exponentially. We literally wouldn’t have been able to get where we are currently without Tinius Olsen.”
“Our ultimate goal is develop a suit that can offer assisted living. It's not really designed to give extra strength, more to give children with muscle disease more mobility, more independence and, most importantly, a greater quality of life.”
The suit will be going into human trials later this year.
Other Applications
This development can be successfully applied in more places than the medical field. For instance, for the forthcoming missions to Mars, planned for the mid-2030s, space agencies such as NASA can adapt the technology into their spacesuit design.
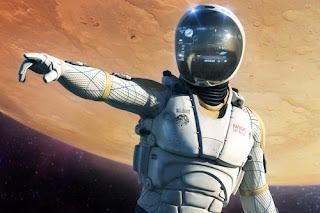
Image Credit: Tinius Olsen
This can extend to military applications, not just supporting the body structure of pilots and soldiers but also technicians and ground crew responsible for the building and maintenance of tanks, heavy ordinance and aircraft.
This technology is also beneficial to sports. Protective body equipment for sports like rugby and American football are obvious applications, but the opportunities for the supportive treatment of sports injuries are also huge.
The heavy lifting associated with construction and other manufacturing industries could see a decrease in work hours lost because of strain and back injuries to workers.
University of Central Lancashire, Engineering Innovation Centre
Located on the Preston Campus, The Engineering Innovation Centre (EIC) of the University of Central Lancashire, UK, is bringing together leading business minds, world-leading research and inspiring teaching in a spirit of discovery and collaboration.
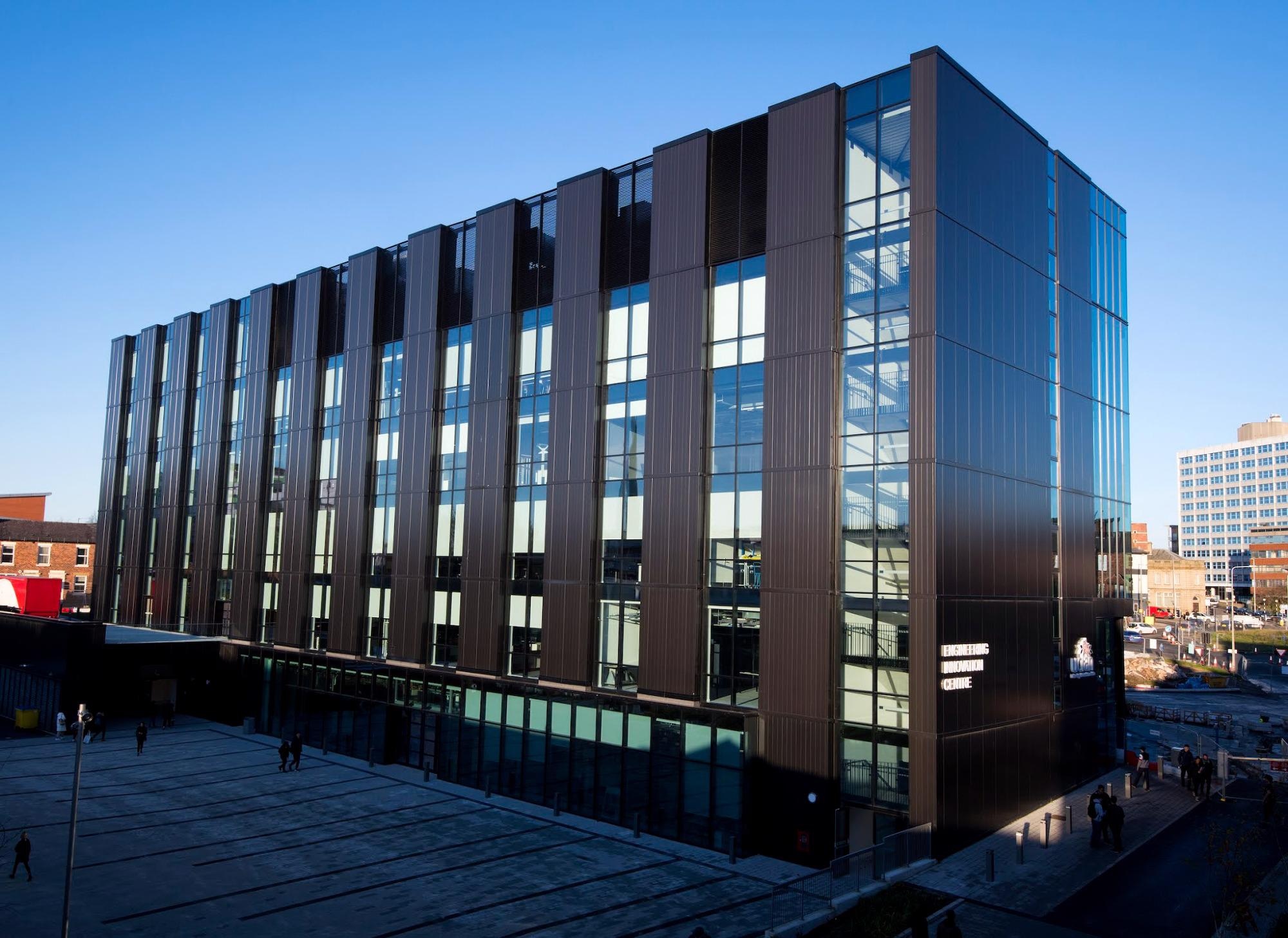
Image Credit: Tinius Olsen
Lancashire’s position as a national center of excellence for advanced engineering, aerospace and manufacturing is strengthened by the new £35 m EIC. This contributes towards maintaining the UK’s reputation as a global leader in these areas.
It supplies engineering students with the chance to work alongside industry partners and research experts, with the opportunity to get to grips with flight simulators and drone technology, work on vehicles inside the aerospace and motorsports laboratory, experiment with 3D printing, and much more.
The state-of-the-art teaching and research facility engages directly with industry and gives students real-world experience on live projects.
By doing this, the EIC acts as one of the pioneers of the industrial strategy, both on a regional and national scale, producing the next generation of world-class engineers and addressing the need for innovation.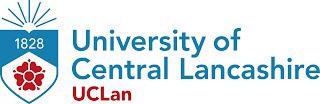
The Centre examines possible solutions to huge priorities in contemporary society and to elements of the UK Industrial Strategy. Its aim is to support, manage and stimulate strategic development and growth of knowledge transfer and engineering research, which will allow industry to address challenges at home and around the globe.
Activities are focused within a variety of research areas that contain a diverse series of specialist laboratories, covering a wide range of sectors, including composites, intelligent machines, oil and gas, aerospace, 3D printing and motorsport.
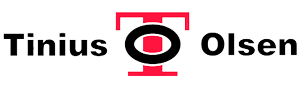
This information has been sourced, reviewed and adapted from materials provided by Tinius Olsen.
For more information on this source, please visit Tinius Olsen.