For many years, technical experts at Tinius Olsen have contributed their technical prowess to industry publications and their readers. Plastics Technology, one of the leading titles within the plastics industry, published an excellent interview with Tinius Olsen’s Applications Specialist, Harry Yohn.
The feature takes an in-depth look at utilizing a melt indexer, like the MP1200, to test the melt flow rate as defined by current test standard procedures.
Since 1996, Harry has been a product applications specialist for Tinius Olsen and has almost 32 years of experience in mechanical and testing of plastics.
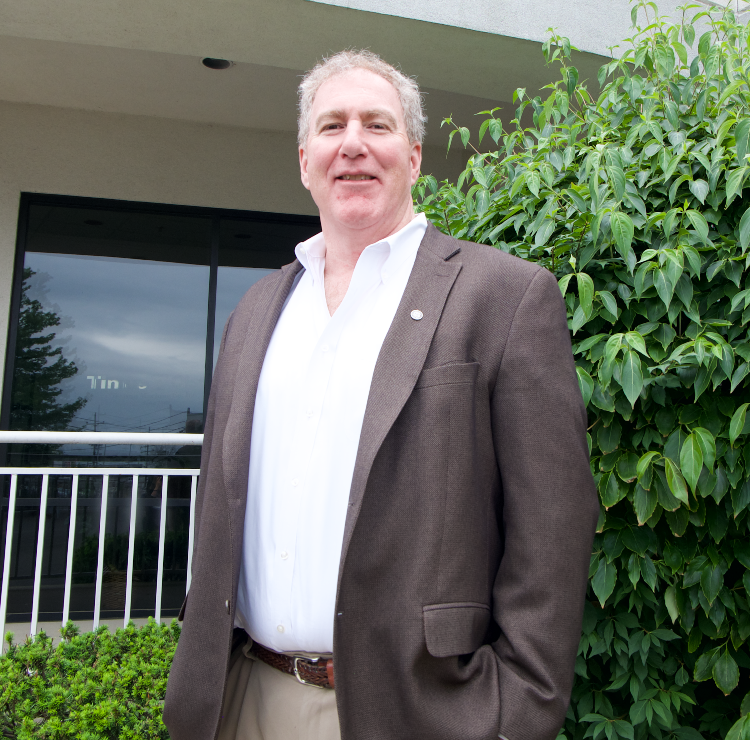
Image Credit: Tinius Olsen
Harry is Vice-Chair of the ASTM International Committee D20 on Plastics and is also the Subcommittee Chairman for the Thermal Properties group, D20.30. He has also been honored with several ASTM Service Awards.
Harry suggests in the Plastics Technology interview that although all operators may say that they follow the published test standards, like ISO 1133 or ASTM D1238, not everybody is following them exactly as they are written.
You can make your life a whole lot easier by paying close attention to the procedural steps detailed in the test standards, thus ensuring accuracy, efficiency and smooth operation.
Harry Yohn, Applications Specialist, Tinius Olsen
Harry looks at ASTM D1238 (Standard Test Method for Melt Flow Rates of Thermoplastics by Extrusion Plastometer), Procedures A and B and the correct procedures to follow in each to help establish his point.
“The melt-flow test is a measure of the mass of material that is extruded through a standardized orifice in a die under standardized temperature and load conditions. It is a common test used in the plastics industry. Values obtained from the test are useful to processors for material selection and processing machine setup,” says Harry.
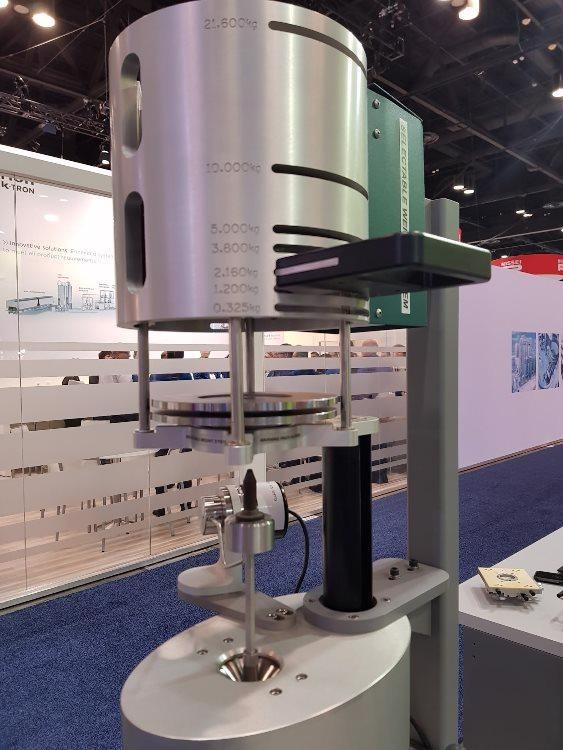
Image Credit: Tinius Olsen
The feature follows the test procedures, starting with Test Setup through to the Preheat Period, Test Measurement and the crucial Clean Up, a part of the procedure Harry is extremely eager to emphasize.
“After a test is completed, the remaining material must be purged from the bore and the equipment needs to be cleaned. The importance of cleaning the machine properly cannot be over emphasized. Some materials are easily cleaned from the machine while others present challenges.”
“After the remaining material is purged from the bore, the piston rod and the die are removed from the bore and wiped down with a cotton cleaning rag. Both items should be cleaned down to bare metal.”
Following the procedures to the letter is one thing, but a user should also ensure that they are up to date with any modifications to existing Standards.
It is important to remember that standards can change over time, based on real-world input from the many members of various industry associations like ASTM. In fact, the ASTM standard for melt flow was recently revised. That is why it is important to stay involved in the industry and to always be sure you are working with the latest version of any standard.
Harry Yohn, Applications Specialist, Tinius Olsen
“It is also good practice to review the latest version of the standard before testing, regardless of whether you are a new user or an experienced testing veteran. Updated test standards can be downloaded from www.astm.org for a small fee,” said Harry.
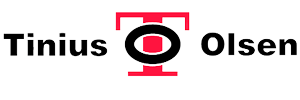
This information has been sourced, reviewed and adapted from materials provided by Tinius Olsen.
For more information on this source, please visit Tinius Olsen.