Technology development plays a significant role in rail transportation safety. Although the highest priority is placed on the protection of life, the preservation of property is critical.
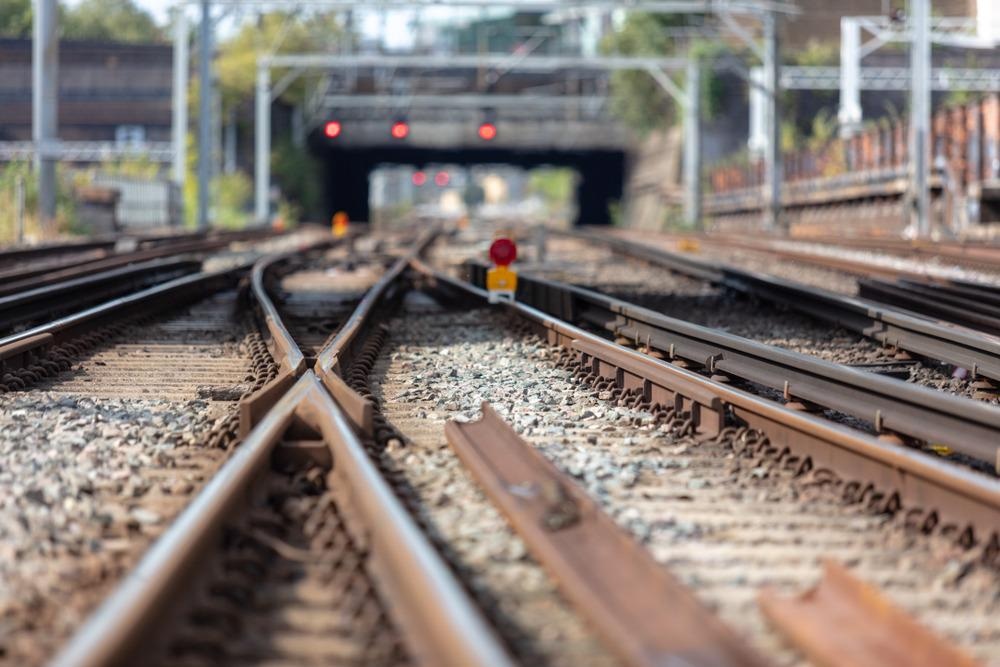
Image Credit: Matthew Nichol/Shutterstock.com
The importance of non-destructive testing (NDT) and the underpinning technology partially lies in maintaining railway rails free of defects and inspection, which is a vital aspect of everyday rail maintenance. Constant structural monitoring alongside taking preventative action as and when necessary aids these efforts, preventing future complications and minimizing the likelihood of catastrophic incidents. It is also very cost-effective as inevitably there is less disruption and downtime.
Here the more frequently seen rail defects are described. The NDT techniques typically used to identify them and their developments are also explored.
Stress Leading to Material Fatigue
Railway vehicle wheel treads incorporate flanges that are sloped like cones. They are designed to enable smooth passage between straight, linear tracks, curves in the line, curves that accommodate bends, and so on.
Modern railroad operation involves significant loading on “coning wheels”, placing the material under enormous, unrelenting stress. This stress, in turn, causes work hardening that leads to material fatigue, referred to as rolling contact fatigue (RCF).
Head Checks and Squats
Two specific types of damage in railway rails are synonymous with RCF, commonly known as head checks and squats.
The high contact stresses experienced between a wheel and the gauge corner of a railroad are responsible for causing head checks, characterized as fine surface cracks manifesting at discrete intervals and visible externally. Gauge corners on outer rails with a curve radius typically ranging between 500 meters and 3000 meters are the most prone areas to suffer from this type of fatigue phenomenon. If not detected in time, they can cause catastrophic events.
Sections of a straight or mildly curving track (within the running band) where the rail is heavily sheared are where rail squats tend to be located; they are “near-surface” damage. It is understood that these defects are initiated by trapped material between wheel and rail, such as pieces of track ballast, for example. Squats are characterized by having a round shape generated from the growth of an isolated crack, preferentially formed in the direction of the heavily sheared surface layer.
Ultrasonic Techniques
NDT is the evaluation and collection of data from materials and components without permanent alteration or damage. In the context of rail defects, the preferred measurement method has mainly centered on ultrasonic techniques. These have typically provided head checks and squats detection in their early formation, and where appropriate, measure depths and inclinations associated with the defects.
Electromagnetic acoustic transducers (EMAT) are typically deployed. Usually, they require a coupling fluid at the interface between the railhead with a probe for direct contact to ensure wave propagation.
An ultrasonic surface wave is propagated down an area under investigation in most systems, capturing its interaction with surface-breaking defects. Here, a Rayleigh surface wave is induced. These waves travel near the rail sample's surface, having longitudinal and transverse motions that cause surface particles to move in an elliptical fashion.
Data is then harvested and processed into reconstructed images. Based on the findings, such as the inclination angles and defect depth, assessments are made into suitable remedial action. This response often results in rail grinding to prevent escalating danger.
Electromagnetic Pulses
Electromagnetic pulses are another rail NDT approach involving exciting eddy currents in a specimen.
Eddy currents are electrical current loops induced by changing high-frequency magnetic fields in the sample's surface; 100–200 kHz is typically the applied excitation frequency range. Resistive losses in the eddy currents release heat. Distorted surfaces disturb heat diffusion via eddy current distribution with local electrical current density changes.
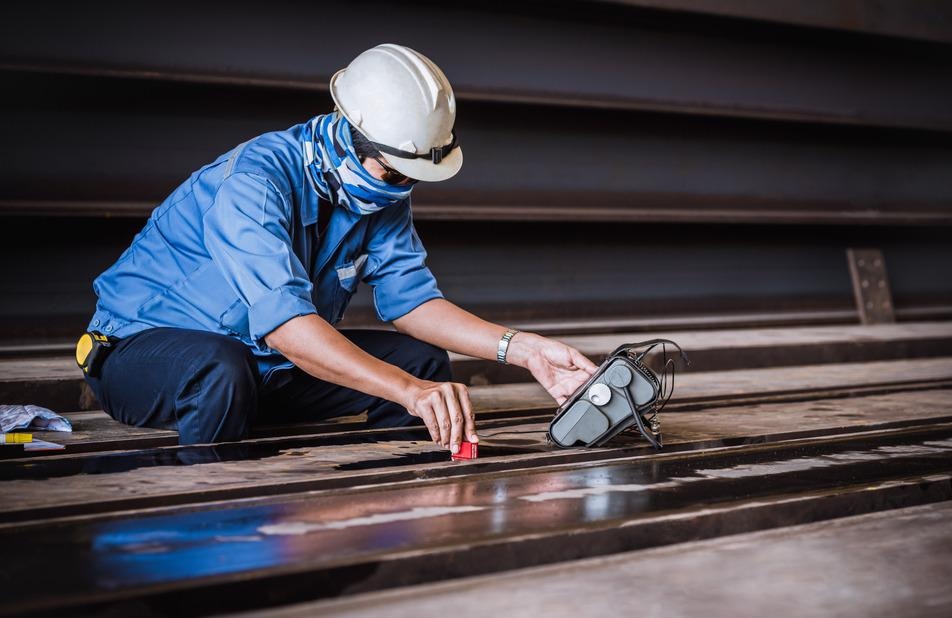
Image Credit: N_Sakarin/Shutterstock.com
Inductive Thermography
As a quick and contact-free approach, inductive thermography has excellent potential as a rail inspection NDT method. However, it is still in the development stage and requires advanced sophistication to be implemented.
Compared to traditional methods such as ultrasonic testing, this technique can produce information from and below a rail surface, garnering data pertinent to head checks and squats. In addition to delivering rail images sub-surface of 1–2 millimeters in thickness, the technique also has the scope to automate rail inspection fully.
In essence, sampling is done by probing with short, inductive heating pulses, typically between 0.1–0.3 seconds, which is enough to achieve a 1–2 oC temperature increase at the surface. Surface cracks or hidden cracks interfere with the heat, and any changes can be recorded using infrared imaging. As a result, irregularities are made visible through thermographic images.
Finite Element Simulations
Recent years have seen several research groups, including Wilson et al. (2011) and Oswald-Tranta et al. (2021), prove the validity of using inductive thermography to localize surface cracks in metal samples. Much experimentation has been undertaken using head checks from rail pieces and comparing differences between these and artificial cuts made by machining to improve the technique's accuracy.
Crack detectability optimization has received attention as influenced by various parameters, including heating pulse duration and excitation frequency. Finite element simulations allow understanding between different processing conditions to be illuminated.
Numerical calculation is exploited in these simulations to understand better how cracks disturb heat diffusion and distribution of eddy currents or the impact of crack properties on the results.
Consecutive Snapshots vs. Continuous Movement
The emphasis is on image presentation in other research areas, where trade-offs are needed between contrast and practicality. For example, Tuschl et al. (2021) describe one approach involving a continuous scanning movement being adopted during the testing while in another, a less practical approach builds a panorama image from a series of consecutive snapshots. The latter method produces higher quality results, and therefore future research into improving image quality from continuous movements is desirable to enable progress in rail NDT techniques.
References and Further Reading
Tuschl, C., et al. (2021) Inductive Thermography as Non-Destructive Testing for Railway, Appl. Sci., 11: 1003. Available at: https://doi.org/10.3390/app11031003
Wilson, J., et al. (2011) PEC thermography for imaging multiple cracks from rolling contact fatigue, NDT & E International, 44:505. Available at: https://doi.org/10.1016/j.ndteint.2011.05.004
Oswald-Tranta, B., et al. (2021) Detection and characterization of short fatigue cracks by inductive thermography, Quantitative Infrared Thermography Journal, 1. Available at: https://doi.org/10.1080/17686733.2021.1953226
Lua C., et al. (2010) An experimental study of EMAT ultrasonic surface waves modes in railhead, International Journal of Applied Electromagnetics and Mechanics, 33: 1127. Available at: https://doi.org/10.3233/JAE-2010-1229
Disclaimer: The views expressed here are those of the author expressed in their private capacity and do not necessarily represent the views of AZoM.com Limited T/A AZoNetwork the owner and operator of this website. This disclaimer forms part of the Terms and conditions of use of this website.