Researchers from the University of Braunschweig in Germany have recently developed silicon microprobes that can be easily integrated with a wide range of manufacturing processes to perform in-process high-speed surface measurements at a low cost.
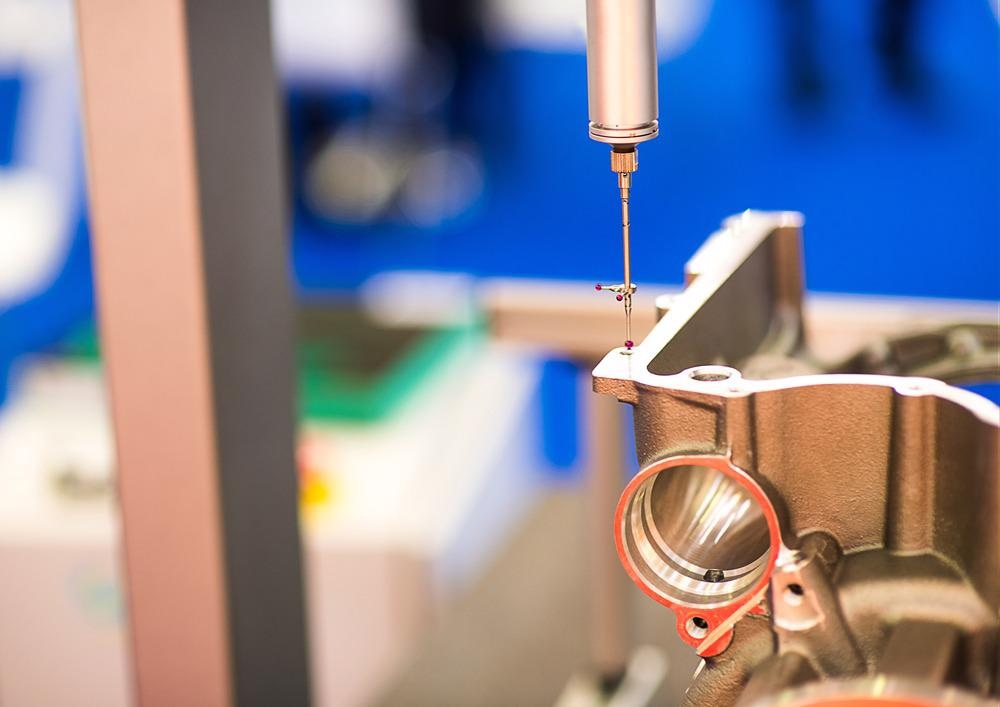
Image Credit: Denis Starostin/Shutterstock.com
Surface properties on the micrometer and sub-micrometer scale play a fundamental role in the life cycle of many modern industrial products, such as medical equipment, automotive components, and semiconductor devices.
Surface metrology measurements require high accuracy and high throughput methods that provide a sufficiently large measurement range and low probing force.
Precision is one of the essential characteristics of manufacturing. High precision ensures high quality, high performance, and reliability of industrial products.
The development of high-precision manufacturing technologies, together with advanced measurement methods, enabled surface metrology to play a crucial role in many manufacturing processes related to semiconductor and biomedical industries, additive and automotive manufacturing, and many others.
Surface Metrology is Vital to Quality Control in Manufacturing
The surface topography of an object determines some of its mechanical and physical properties, such as friction, adhesion, thermal and electrical conductivity, and others.
Since most mechanical or chemical manufacturing processes induce surface defects and irregularities, high-speed in-process surface contour, surface roughness, and deformation measurements can provide the necessary feedback to optimize the manufacturing process and ensure stringent quality control.
The surface metrology measurements can be either contactless, performed by optical instruments, or contact measurements performed by a stylus probe.
Although the optical methods allow high throughput zero-force measurements, their utilization is restricted by the optical properties and the topography of the measured surface, and a relatively high cost of operation. Thus, contact probe surface metrology instruments are still favored by many industrial users.
Traditionally, contact surface measurements are performed by stylus profilometers, micro-coordinate measuring machines, or, if ultra-high lateral and vertical resolution is needed, by scanning probe microscopy.
Surface Topography Measurements Require Balance Between Speed and Force
All contact measurement techniques operate by scanning a sharp probe (that can be made of silicon, steel, or diamond) over the specimen surface. Depending on the application, the radius of curvature of the probe's tip ranges from a few micrometers down to few nanometers.
The probe is usually mounted on a flexible cantilever that enables vertical movement of the probe as it scans the sample surface. The deflection of the probe's cantilever is detected either by optical or electrical sensors (usually inductance sensors) and represents the surface topography.
The main drawbacks of the contact surface instruments are the relatively low throughput and the contact force applied between the probe and the specimen surface.
The maximum probe traverse speeds used in state-of-the-art instruments are in the range of 1–3 mm/s, which can result in time-consuming measurements when characterizing large surface areas.
The force applied between the probe and the surface needs to be high enough to ensure adequate tracking of the surface profile and a sufficient signal-to-noise ratio from the cantilever deflection sensor. The force is usually in the millinewton range. Despite that, the contact pressure might be in the order of gigapascals (depending on the probe sharpness) and cause damage to the measured surface.
A Novel Silicon Microprobe for High-Speed Surface Measurements
Recently, researchers from the University of Braunschweig in Germany, in collaboration with CiS Forschungsinstitut für Mikrosensorik GmbH (an industry-oriented research institution focused on microsensors), have developed piezoresistive silicon microprobes for fast surface roughness measurements.
The microprobes are fabricated from monocrystalline silicon by using lithographic methods and consist of a base and a cantilever.
A monolithic silicon probing tip is located near the free end of the cantilever, while four piezo-resistors (acting as strain sensors) connected to a Wheatstone bridge are fabricated at the junction between the cantilever and the base of the probe.
The base contains the contact pads used to detect the signal from the piezoresistive strain sensors.
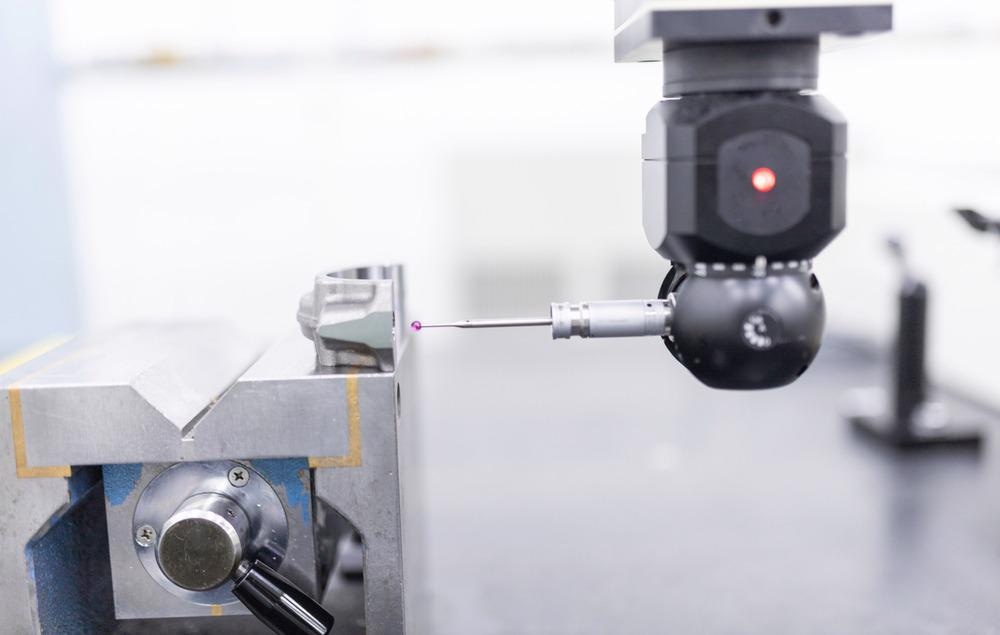
Image Credit: JETSADA POSRI/Shutterstock.com
Depending on the intended application, several different cantilevers were designed for the microprobes, with lengths between 1.5 mm and 5 mm, and widths between 25 μm and 50 μm. The height of the conical probing tip attached to the cantilever can be in the range of 10-200 μm.
The Piezoresistive Microprobes Promise Speed, Accuracy and Reliability
The small dimensions of the microprobes arise from the fact that they were originally designed for roughness measurements inside diesel engine injection nozzles and other narrow openings with bore-hole diameters of less than 100 µm.
Until now, surface roughness and shape measurements inside such high-aspect-ratio microstructures were extremely challenging, since no suitable sensors are available on the market. As a result, approximately 50 million fuel injector nozzles are manufactured every year, without adequate control of their surface roughness and geometry.
Both parameters directly affect the fuel efficiency and exhaust emissions of diesel engines.
The German scientists successfully demonstrated the use of the novel piezoresistive microprobes both in laboratory prototypes and adapted commercial instruments for surface metrology.
Importantly, the small mass and dimensions of the probe ensured high-fidelity tracking of the surfaces features at traverse speeds up to 10 mm/s and a probing force around 100 micronewton.
Both parameters show a significant improvement over the traditional surface metrology techniques, leading to increased throughput and reliability of the measurements.
Besides their enhanced performance, the piezoresistive microprobes also provide a cost-efficient performance compared to the traditional contact surface measurement methods.
As a proof-of-concept application, the researchers integrated a piezoresistive microprobe instrument into a paper mill press for in-process monitoring of the diameter, shape, and texture of the press rolls, as these parameters are critical for the quality of the final product.
In the industrial setting, the microprobe-based instrument showed less than 3% measurement deviation compared to an industry-standard inductance surface tester, while operating at a higher traverse speed.
Enhancing Probe Wear-Resistance for Faster Measurements
Further attempts to increase the measurement throughput revealed that at traverse speeds above 15 mm/s, noticeable wear of the probe's tip may occur.
To overcome this drawback, the researchers are investigating the use of wear-resistant coatings, such as diamond-like carbon or synthetic sapphire, to protect the piezoresistive microprobes.
These results so far confirm that the relatively cheap and compact piezoresistive silicon microprobes can successfully solve various emerging tasks of industrial high-speed surface measurements.
References and Further Reading
K. Miyoshi (2013) Surface Characterization Techniques: An Overview. NASA Technical Report NASA/TM-2002-211497. https://ntrs.nasa.gov/archive/nasa/casi.ntrs.nasa.gov/20020070606.pdf
Xu, M., et al. (2021) Investigating the Trackability of Silicon Microprobes in High-Speed Surface Measurements. Sensors 21, 5, 1557. https://doi.org/10.3390/s21051557
Teir, L., et al. (2021) In-Line Measurement of the Surface Texture of Rolls Using Long Slender Piezoresistive Microprobes. Sensors 21, 17, 5955. https://doi.org/10.3390/s21175955
Fahrnbach, M., et al. (2021) Customized piezoresistive microprobes for combined imaging of topography and mechanical properties. Measurement: Sensors 15, 100042. https://doi.org/10.1016/j.measen.2021.100042
Brand, U., et al. (2019) Long Slender Piezo-Resistive Silicon Microprobes for Fast Measurements of Roughness and Mechanical Properties inside Micro-Holes with Diameters below 100 µm. Sensors 19, 6, 1410. https://doi.org/10.3390/s19061410
Disclaimer: The views expressed here are those of the author expressed in their private capacity and do not necessarily represent the views of AZoM.com Limited T/A AZoNetwork the owner and operator of this website. This disclaimer forms part of the Terms and conditions of use of this website.