Carbon black may be a fairly basic product in terms of its chemical structure, consisting of just carbon, but by clever processing, this important plastics additive can be manipulated to impart a variety of important properties in a range of different applications. During the past few years, US-based Cabot Corporation has been undertaking a major programme aimed at developing differentiated products with specific performance characteristics for the plastics and rubber industries using carbon black. Applications for New Grades of Carbon Black The product development programme has resulted in several new grades of carbon black with specific combinations of properties designed to meet particular requirements. These include pressure pipes, ESD (electrostatic discharge), film, fibre and other applications. All these new materials have clearly differentiated characteristics and are quite different in concept from the general purpose grades, which previously were the only types available. Allotropes of Carbon In nature, carbon is present in two forms - diamond and graphite. Diamond has a three-dimensional structure, while graphite is composed of a series of parallel planes. The structure of carbon black is intermediate between these two forms and is termed ‘quasi-graphitic’, as a series of layers are formed during the nucleation process. Formation of Carbon Black Carbon black is formed by the incomplete combustion or thermal cracking of a hydrocarbon raw material (CxHy + 02 C + CH4 + CO + H2 + C02 + H20). In almost all instances, carbon black is prepared by the ‘oil furnace’ process, in which an aromatic feedstock is atomised and fed into a hot flame (> 1500°C) to produce powder ‘fluffy’ carbon black. The black is often pelletised into beads in order to aid storage and handling while maintaining adequate dispersability in various media, including plastic resins. Pressure Pipes While furnace blacks are essentially elemental carbon, they often contain a number of contaminants, some or all of which may be undesirable for a specific industry or application. in the case of pressure pipe applications, Cabot has developed three new grades with particularly low contaminant levels. Designated by the company as P-types, ELFTEX 254, ELFTEX P100 and ELFTEX TP meet five key performance criteria for this specialised application: • Long term weatherability - The end product is required by utility companies to provide long service life without failure, despite being exposed to ultraviolet light. The three new grades incorporate very fine prime particles, which present more surfaces to incident light, and hence have greater UV light absorbing efficiency than a coarser grade. • Very low levels of moisture absorption - Compounds containing carbon black usually absorb moisture when exposed to air. This can create processing problems, surface defects or internal cavities in the finished part. The high purity of the carbon black grades developed for this application has resulted in very low moisture absorption during the compounding process. • Microscopic dispersion - Undispersed carbon black agglomerates in the pipe wall can lead to premature failure and also reduce fluid flow properties. These problems are recognised in the industry, and most standards for pressure pipes specify a microscopic dispersion rating of no greater than 3 under ISO 11420, NFT51 - 142. Conventional blacks typically rate between 5 and 6. • Chemical cleanliness - Chemical impurities, particularly sulphur, ash and toluene extract, when present in the compounds used to make pipes for drinking water can impart unpleasant tastes or odours. All carbon blacks include some residues of these materials, but in the P-type grades the amounts have been greatly reduced. For example, sulphur content - typically around 10,000 ppm in a conventional black - is some 600 ppm in the new grades. • Dispersability - This performance measure depends primarily on the fundamental characteristics of the carbon black and relates to the attractive force needed to separate the agglomerates into discrete carbon black aggregates. It is also an indicator of the relative yields that can be achieved on compounding equipment with different carbon black grades. The P-types show much better dispersability than a conventional grade, resulting in better wetting with the polymer and subsequent de-agglomeration. Electrostatic Discharge For ESD applications, Cabot had to design new materials for a very different set of requirements. Conductivity, stiffness and impact strength are primary performance requirements in this sector, with surface smoothness and dispersability also important considerations. With most other grades of conductive black, conductivity performance has tended to reduce smoothness, flexural modulus and impact strength. With this in mind, the aim of Cabot’s product development programme was to achieve all five primary performance criteria without the trade-offs usually encountered. As in the case of the P-types developed for pressure pipes, a high degree of dispersability has been achieved with the VULCAN grades, leading to good polymer wetting and full de-agglomeration which is essential if the network of fine particles necessary for the creation of continuous paths is to be formed throughout a matrix. This superior conductivity can allow compound formulators to use a comparatively lower loading to achieve the minimum required surface resistivity for an application. It also needs chemical cleanliness in order to avoid the migration of ions that could cause the failure of electronic equipment. The star diagram, figure 1, compares the relative performance of VULCAN XC305, XC605 and XC72 with an extra-conductive black with respect to the five primary performance measures. The extra-conductive black has superior conductivity but is substandard in all other respects, while the VULCAN grades provide a balanced performance. 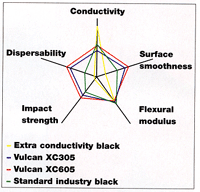 | Figure 1. Star diagram showing the performance of various grades of carbon black. | Polyolefin Film For polyolefin film production, opacity, weatherability, film smoothness and dispersability are the four most important criteria for film masterbatch producers. Film opacity depends mainly on film thickness and pigment loading. When the thinnest films are produced, the choice of carbon black grade significantly affects the final pigment loading needed to achieve a certain opacity level. BLACK PEARLS 4040 has been designed as a productivity grade with a good cost and performance balance, while BLACK PEARLS 4060 provides superior opacifying power, making it suitable for agricultural film requiring extreme weatherability performance and also long service life. The type of black pigment also has a primary impact on the final film smoothness that can be achieved. For applications such as surface protection and photographic film, high standards of surface smoothness and dispersability are required. Film smoothness is measured by counting the number of undispersed pigment agglomerates (known as pips) in a sample of blown or cast film, BLACK PEARLS 3030 typically has about 20% of the number found in a sample incorporating an industry-standard carbon black. 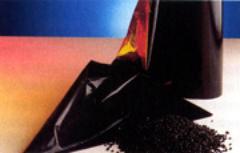 | Figure 2. Polyolefin film containing carbon black (Black Pearls 3030). | Summary Carbon black plays an important role in changing the physical characteristics of the end product, such as its colour, the weathering properties or the electrical conductivity. Cabot’s product development programme highlights the new processing and technology going into developing new grades of carbon black, demonstrating that the material is not as low-tech as it may seem. |