Images of satellites, space probes or space stations sometimes look as though they are blanketed in what looks like gold foil. This blanket owes its golden color to the highly engineered polyimides with which they are constructed, not to the precious metal it resembles.
The blanket material is more commonly known as multilayer insulation (MLI) and is wrapped over sections of spacecraft and satellites in orbit, which need protection from the electromagnetic and solar radiation in space. It also stops the loss of heat from the inhabited sections of spacecraft.
Due to limited air convection in the microgravity of spacecraft, radiation is the key mode of heat transfer, both in and out, within the space environment. The utilization of MLI is crucial to the uninterrupted operation of the sensitive electronics, in addition to the safety of the astronauts aboard.
The polyimide film substrate component central to MLI is able to withstand temperatures between −260 °C and 400 °C, with short-term exposures of over 480 °C. It is resistant to degradation from ultraviolet radiation and has low outgassing (making it suitable for employment in the vacuum of space).
So, the lightweight MLI becomes a perfect insulation material for utilization in space applications. MLI, when properly designed, is also employed as the first line of defense against dust impacts in space for the spacecraft.

Figure 1. Multilayer insulation (MLI) based on aluminized polyimide films. Image Credit: Jayhawk Fine Chemicals Corporation
MLI is typically created by metalizing a thin layer of a durable polyimide film, usually by vapor deposition of a thin layer of aluminum onto it. Even though the final MLI is still fairly thin, it is made up of a collection of even thinner individual layers, which is where the term multilayer comes from.
As seen in Figure 2, the polyimide film central to the construction of the MLI is produced from the reaction of a dianhydride with a diamine in a two-step process, with the resulting polymer having exceptional chemical and heat resistance.
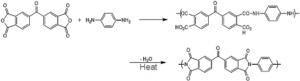
Figure 2. The two-step process for making thin polyimide films using a dianhydride and a diamine. Image Credit: Jayhawk Fine Chemicals Corporation
Polyimides possess glass transition temperatures in the range of 300 °C to 400 °C or even higher. In addition, they possess very high thresholds for thermal or thermo-oxidative degradation. Polyimides with different performance characteristics can be generated via an appropriate selection of dianhydride and diamine.
Frequently utilized dianhydrides for high temperature performance are based on the aromatic structures, e.g., Pyromellitic dianhydride (PMDA), Benzophenone tetracarboxylic dianhydride (BTDA), Biphenyl tetracarboxylic dianhydride (BPDA), etc.
Thus, every time you see a spacecraft with gold-colored coverings, you can be appreciative of the humble dianhydrides which go into producing this exceptional and efficient thermal management material.
References
- https://www.nesdis.noaa.gov/content/good-gold-are-satellites-covered-gold-foil

This information has been sourced, reviewed and adapted from materials provided by Jayhawk Fine Chemicals Corporation.
For more information on this source, please visit Jayhawk Fine Chemicals Corporation.