Copper metal is usually at the core of any electrical wire, and this carries the current for the entire device. Wire insulation is another crucial but understated component.
Common wire is insulated with a thick plastic material that is colored to identify neutral, hot and ground wires. The wire diameter can be twice or many times that of the core conductive wire, which works well for the majority of applications. Yet, such thick insulation is impractical when wire is coiled for electric motors.
That is where a highly efficient but extremely thin insulating enamel is ideal. Although numerous polymers can be utilized for this purpose, polyimide is undoubtedly the best choice. Its high electrical resistance enables its utilization in extremely thin layers as the primary insulation on bare wire.
In turn, this allows winding the wire into tight coils over itself, as seen in Figure 1. The wire coated using this method is known as magnet wire, where coils are employed to produce artificial electro-magnets.
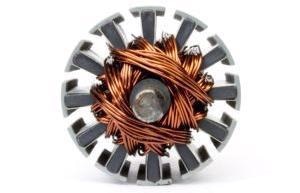
Figure 1. A motor’s rotor coiled with magnet wire coated with polyimide enamel, formed using a dianhydride. Image Credit: Jayhawk Fine Chemicals Corporation
As seen in Figure 2, polyimides are usually created from the reaction of a dianhydride with a diamine in a two-step process. Step 1 produces poly(amic acid) (PAA) in an organic solvent. Usually, this solution is known as polyimide varnish, although poly(amic acid) varnish would be more correct.
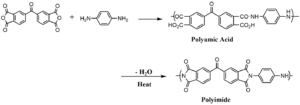
Figure 2. Two-step process for producing polyimide varnish and enamel from a dianhydride and a diamine. Image Credit: Jayhawk Fine Chemicals Corporation
The bare wire is thinly coated with the varnish and heat is applied in Step 2, known as imidization. The heat leads to dehydration along the PAA backbone, releasing water and generating the polyimide. This step also flashes off the solvent and leaves behind a cured polyimide enamel on the wire.
Polyimide varnishes and enamels provide superior dielectric performance over a large temperature range from cryogenic to hot environments. Furthermore, their near-universal resistance to chemicals and moisture and their excellent thermo-oxidative stability results in uninterrupted performance throughout the entire lifecycle of motors used in all types of service.

This information has been sourced, reviewed and adapted from materials provided by Jayhawk Fine Chemicals Corporation.
For more information on this source, please visit Jayhawk Fine Chemicals Corporation.