An extensometer is an instrument that measures test specimen elongation for characterizing strain. There is a diverse range of applications where extensometers can be used, and these devices have multifaceted technical requirements. Generally speaking, there is not a single device that can typically meet every requirement for every testing application.
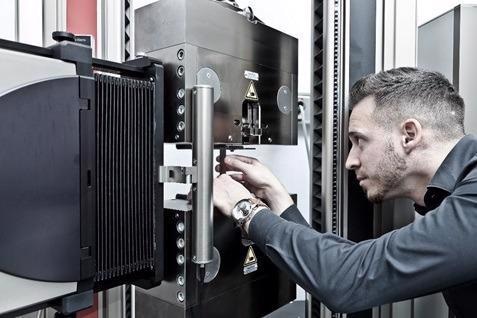
Image Credit: ZwickRoell GmbH Co. KG
The characteristics of the material to be tested determine the requirements for an extensometer; these requirements include the test standards that must be satisfied, test requirements, specimen dimensions and geometry.
Deciding whether an extensometer can be connected directly to the specimen is also necessary. Small diameter wire specimens lack sufficient visible area for reliable non-contact measurements, while very thin specimens, such as foils, can be sensitive to clamping forces, for example.
More than one extensometer may be required if there is high stiffness in the initial extension range, followed by high plasticity. The first extensometer is used to very accurately measure small strains (typically up to 5 mm) in the elastic range, and the second is used to measure very high extensions (typically up to 500 mm).
Materials with very smooth surfaces or made of transparent materials are not suitable for non-contact measurements unless measuring marks are first fixed onto the surface of the test specimen.
Standards use quantitative terms, such as uncertainty, deviation and resolution, to qualify the integrity of a measured signal. In most cases, the accuracy of extension measurement requirements is provided in internationally recognized standards and application-specific test requirements.
Sequences that can be automated and easy-to-set-up devices reduce both effort and personnel time. The integrity of the test results can be improved by minimizing subjective influences by simplifying set up routines.
As is implied by the name, clip-on extensometers are mounted directly onto the test specimen. The mechanical parts that transfer extension from the specimen to the internal transducer via knife edges are short and stiff. There is a high level of measurement accuracy due to the incredibly low amounts of relative movement between the extensometer and the specimen.
Clip-on extensometers apply a load directly onto the specimen, and their range is usually limited to a few millimetres. To compensate for superimposed bending stresses, extensometers with double-sided measuring systems and counter-balance weights can be used. Some clip-on extensometers are equipped with motorized application and removal systems to minimize setting errors.
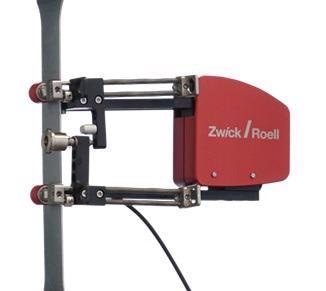
ZwickRoell Clip-on extensometer - measuring strain on a metal specimen. Image Credit: ZwickRoell GmbH Co. KG
Sensor arm extensometers have the advantage of a large measurement range with high measurement accuracy and automatic operation. Precision designs with a very balanced and smooth mechanical operation apply minimum loading to the specimen.
Superimposed bending strains are largely compensated due to the fact that the sensor arms are in contact with both sides of the specimen.
Sensor arm extensometers can be prone to damage or even destroyed at the failure point of high extension, high elasticity specimens due to the direct contact with the specimen. The testing of safety belts is an example of this from the automotive industry. The material will exhibit backlash characteristics that could damage the extensometer at the point of failure.
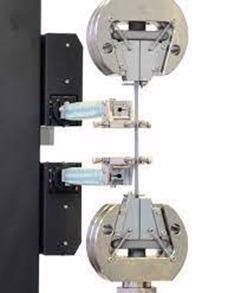
ZwickRoell multiXtens extensometer with fully automatic sensor arms. Image Credit: ZwickRoell GmbH Co. KG
Non-contact video extensometers can safely be used up to the material breaking point without damage, even when testing specimens that exhibit backlash, which is a significant advantage. Another benefit is the capability to use strain as a control loop mechanism for test samples undergoing large deformations.
Characterization of biomaterials and medical-grade polymers is a typical example. In the featured example, a video extensometer supports large strain measurement. There are additional applications where the attachment of a traditional extensometer would not be practical, including the testing of medical components in liquid environments.
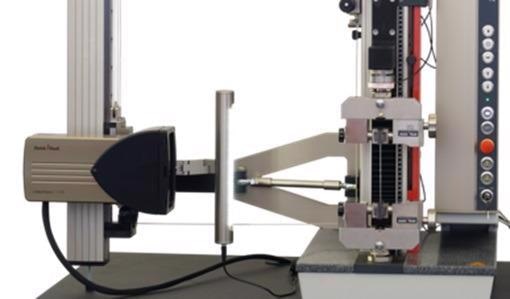
ZwickRoell videoXtens non-contact extensometer. Image Credit: ZwickRoell GmbH Co. KG
In most instances, when non-contact extensometers are used, there is a requirement for measurement marks or targets to be attached to the specimen, which are optically distinct from the surrounding area of the specimen.
The specimen is marked with a colored pen, or the measurement marks are glued, tacked or clipped onto the specimen. Taking time to apply the measurement marks creates an additional step in the test cycle, which can potentially introduce inaccuracies through potential human error, increase the cost of testing and reduce throughput.
Software algorithms evaluate the position of the measurement marks on the specimen to determine a certain area around an optical center point. This measurement becomes the gauge length. As a load is applied to the specimen, the movement of the marks is then converted to extension values.
To optimize the contrast to the measurement mark, special lighting for background or surface illumination of the specimen is used. The ambient lighting changes on the measurement marks during deformation, as well as on the specimen. The reflections and other surrounding influences can influence the optical center point – this is often the cause of scatter in the test results.
The latest extensometer technology does not require measurement marks to be applied to the test specimen and uses a non-contacting device. The unique structure of a specimen’s surface is used by the laser extensometer as a ‘fingerprint’ to generate a virtual measurement mark.
Then, a specific pattern of speckles is created by directing laser light on these measurement positions, which is reflected in various directions corresponding to the surface structure. To determine extension values, selected measurement points are constantly followed and converted.
There is a constant evaluation of the change in the surface structure during specimen deformation, which is the basis of the speckle pattern.
Test laboratories can characterize components, materials and even sub-assemblies using this laser interferometer-based method of non-contact extensometer, making it well suited for quality control and R&D applications.
In addition, this extensometry approach supports tests on micro specimens with small gauge lengths that necessitate exceptional strain measurement accuracy.
Using traditional extensometers would not make such tests possible. Speeding up throughput and delivering the utmost accuracy in strain measurement, laser interferometer, non-contact extensometers provide significant value for high volume testing.

ZwickRoell laserXtens non-contact extensometer operating without specimen marks. Image Credit: ZwickRoell GmbH Co. KG
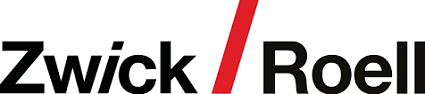
This information has been sourced, reviewed and adapted from materials provided by ZwickRoell GmbH Co. KG
For more information on this source, please visit ZwickRoell GmbH Co. KG