Arc welding using the Metal filler wire as consumable electrode and an Inert Gas to protect the molten pool against oxidation. 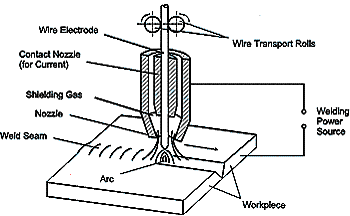 | Figure 1. Schematic of the MIG welding process. |
In the metal inert gas (MIG) welding process, an electric arc is struck between the filler wire and the work piece, while a shroud of inert gas shields the electrode and protects the molten pool against oxidation. Generally, a smoothed direct current power source is used. To ensure the removal of the oxide film (alumina) and the fusion of the consumable wire electrode the negative pole is connected to the work piece. If the oxide film is thick (oxidised aluminium work pieces), the film has to be removed mechanically with stainless steel brush. MIG welding is suitable for thickness above 2.5 mm. There is also a MIG version where a pulsed current is superimposed over the main current. This allows a better arc stability and can be used for thickness between 1 to 5 mm. Manual MIG Welding As the filler wire, that is the consumable electrode, is always automatically fed from a reel, the process is also known as “semi-automatic welding”. This process can be used for all welds of a complex nature where the dimension and thickness are compatible with MIG welding. The system is good and easy to use in manufacturing and for localised repairs of vehicles. Automatic MIG Welding Here, the welding gun is automatically guided or a robot is used. This process is attractive for vehicle manufacturers, especially for very long straight welds like chassis, etc. |