This article discusses the basics and types of alloy design, the role of additive manufacturing (3-D printing) in this process, and the challenges associated.
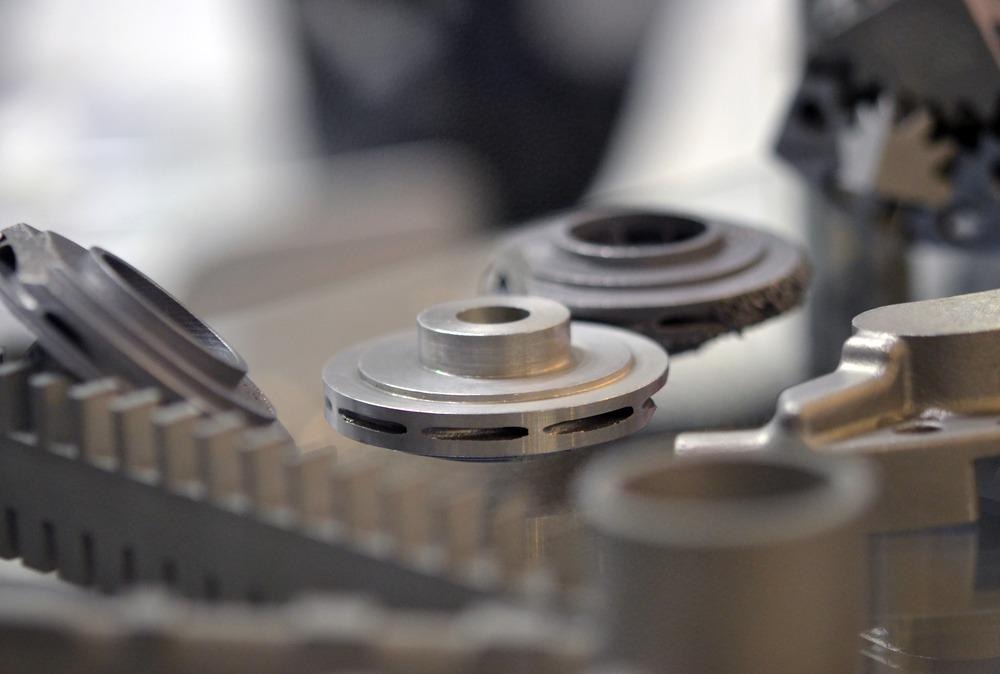
Image Credit: MarinaGrigorivna/Shutterstock.com
What is Alloy Design?
The phrase alloy design refers to a knowledge-based method of developing and designing innovative metallurgical materials that are texturally responsive. On a daily basis, experts in the field of materials engineering use up to 1000 different types of metallic alloys.
The quantity of component primary elements for metallic alloys has risen from one to three or more thanks to the rapid growth of technological advances and concepts for manufacturing sophisticated materials. In comparison to ordinary metal alloys based on one or two essential parts, high-entropy alloys (HEAs) often have 5 or even more primary metals, with each having an atomic proportion ranging from 5% to 35%.
Current Demands for Alloy Design
Pure metals are rarely employed in any industry since their qualities are not adequate or adapted to the unique demands of a product. A minor inclusion of a second or third element to pure metal, on the other hand, can create a substantial difference in the alloy's characteristics.
Developing novel alloys is done depending on the application requirements, and it necessitates comprehensive empirical abilities, ranging from a high-temperature furnace to melting different components to post-processing facilities for reshaping.
Because surface alterations are straightforward to execute where bulk characteristics are not impaired, major efforts have been spent on exterior alterations of an alloy instead of creating new alloy chemicals for several years. The issue is not only in developing a novel alloy, but also in locating a vendor capable of producing certain combinations on a large scale. However, alloy design via additive manufacturing can make a big impact, since it allows for the development of novel chemistries and the production of functional components in a variety of forms.
Pros and Cons of Additive Manufacturing
One of the most transformational technologies of our time is additive manufacturing (AM), sometimes known as 3D printing. 3D printing may be used to build a very accurate simulation image, which is especially useful in the aerospace and automotive industries. It has a wide spectrum of applications, creating technological devices with a range of biochemical capabilities and other biomedical applications, such as custom-made implantable devices.
Although 3d printing is one of the most well-known processes, it has several restrictions in its use. The low production capacity and related costs are significant factors limiting the use of AM. Furthermore, owing to changes in manufacturing techniques, 3D printed goods may differ in size from CAD models.
Alloy Designing Methods Utilizing Additive Manufacturing
AM methods for metallic alloys are classified into two types: metal powder-based and metal wire-based technologies, using various energy sources such as laser beam, electron beam, and arc. The two primary metal–AM processes, DED and PBF, may be utilized for alloy design, however there are some key differences in the method and the accessible raw input materials.
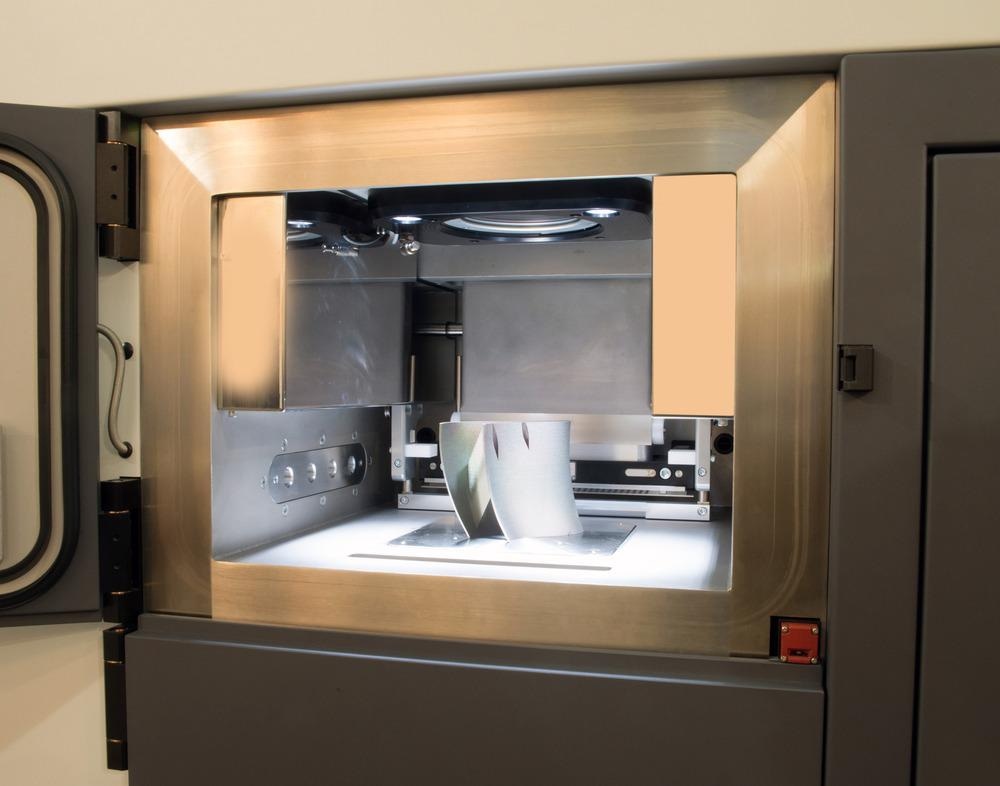
Image Credit: Moreno Soppelsa/Shutterstock.com
The location of the input concerning the printing of the entire design is the most important distinction between the two main groups. DED is a wire or powder-fed process that employs an inert gas supply to drive powder material or wire into a melt-pool at the central focus of a laser.
PBF, on the other hand, uses a laser or electron laser to merge a powder layer that has been dispersed all across the face of the build-plate, generally between 30 and 100 mm thick. This method requires that the input material is of single alloy composition, either atomized as a single alloy or blended or alloyed in situ.
The earliest predecessors of laser-based AM methods may be found in publications dating back to the 1970s. The primary processing factors that influence alloy material behavior are the beam kind, laser power, scan rate, track separation, film thickness, and pulse duration.
These parameters impact the growth of the melt pool and, as a result, the pace of solidification. Another frequent source of energy for powder-based AM is the electron beam.
The electron beam preferentially merges the powder bed surfaces in a style analogous to laser-based approaches; however, due to the restricted mean free path of electrons in gasses, the electron beam melting process must be carried out in a sealed chamber. In 1997, electron beam melting was patented. If a multi-material element is desired for powder-bed-based AM, the component powder can be pre-alloyed or pre-mixed to the needed quantities.
Latest Advances in the Industry
As mentioned, publications on high entropy alloys or multi-principal constituents’ compositions resulted in a paradigm shift in how we see metal combinations. The emergence of high entropy alloys (HEA) proved that the inclusion of five or more elements in identical quantities can result in a basic solid solution combination.
This contradicted traditional physical metallurgy knowledge and posed a barrier to the development of metallic alloys. The introduction of HEAs has ushered in a new way of thinking about new alloy creation, which coincides with the timetable of advancement of laser powder bed 3d printers.
A substantial body of literature on laser particle ped fusing additive fabrication of high entropy alloys has begun to emerge. An increasing trend is to create alloys that may combine the transition-induced plasticity (TRIP) mechanism in addition to the twinning induced plasticity mechanism (TWIP). TWIP and TRIP steels are broadly accepted, but HEAs present new meta stability development potential.
Challenges and Future Perspective
While great expense is incurred in producing novel alloys with metal–AM utilizing DED and PBF, certain challenges remain that prevent the methodology's wider application. As businesses begin to utilize AM technology, facilities will need to handle additional machines and powder/wire inventories, comparable to that used for manufacturing, for alloy development, as well as experimentation with how they fit into the product's overall workflow and network.
Critical distinctions between lab-scale AM biomaterials and full-scale production must be resolved, and examining current technologies may frequently offer insight into issues encountered in alloy design employing AM.
In short, 3-D printing has revolutionized the field of alloy design, but still more research needs to be focused on contributing towards cost-effectiveness and fast processing.
Further Reading
Bandyopadhyay, A. et al., 2022. Alloy design via additive manufacturing: Advantages, challenges, applications and perspectives. Materials Today. Available at: https://www.sciencedirect.com/science/article/pii/S1369702121004314?via%3Dihub
Clare, A. T., et al. 2022. Alloy design and adaptation for additive manufacture. Journal of Materials Processing Technology. 299. 117358. Available at: https://www.sciencedirect.com/science/article/pii/S0924013621003186?via%3Dihub
Su, Ching-Hua, et al. Design, processing, and assessment of additive manufacturing by laser powder bed fusion: a case study on INCONEL 718 Alloy. 2022. Journal of Alloys and Compounds. 163735. Available at: https://www.sciencedirect.com/science/article/pii/S0925838822001268?via%3Dihub
Disclaimer: The views expressed here are those of the author expressed in their private capacity and do not necessarily represent the views of AZoM.com Limited T/A AZoNetwork the owner and operator of this website. This disclaimer forms part of the Terms and conditions of use of this website.