This article focuses on the effect of particle size on the additive manufacturing process.

Image Credit: sspopov/Shutterstock.com
What is 3D Printing?
3D printing, often known as additive manufacturing, is a type of popular manufacturing technique. This technique is based on CAD model files and employs adhesive substances such as powdered plastic or metal to produce items in three dimensions layer-by-layer.
Additive manufacturing materials include thermoplastics like acrylonitrile butadiene styrene (ABS), metallic substances (especially powders), varnishes, and porcelain. ISO/ASTM 52900 additive manufacturing has classified 3D printing operations into seven distinct classes. These include binder jetting, material extrusion, powder bed fusion, sheet lamination, VAT polymerization, direct energy deposition, and material jetting.
Technologies
Sintering, melting, and stereolithography are the three primary forms of 3D printing techniques. To make high-resolution products, sintering is a method in which the heat is applied to the substance but not to the extent of melting.
Powder bed fusion, electron beam melting, and direct energy deposition are 3D printing melting processes that employ laser beams, electrical sparks, or electron beams to print things by melting the components together at extreme temperatures. Photopolymerization is used in stereolithography to produce components. This method uses the proper light source to selectively contact the material to heal and crystallize a cross-sectional area of the product in thin sheets.
Importance and Industrial Utilization
3D printing is one of the most transformational novel methods of our day, utilized to generate a very exact virtual model that is especially useful in the aviation and car industries. It has a broad spectrum of applications, incorporating portable technology with several biological capabilities and other biomedical applications, such as custom-made implantable devices.
It is commonly utilized in mold making, product engineering, and other disciplines. Printing components with this technique is typical nowadays, and it is fast overtaking other techniques that were previously employed. Jewelry, apparel, structural engineering, architecture, building and design, dentistry and medical sectors, spatial analysis, and geotechnical works are just a few of the industries and applications.
More from AZoM: Laser Diffraction Particle Size Analysis of Cement
Limitations of the Process
While additive manufacturing is among the most well-known processes, it has several restrictions in its uses. The low production throughput and related costs are significant factors limiting the use of AM. While 3D printing can make products from a variety of polymers and metals, the accessible raw materials are not exhaustive.
This is because not all metals or polymers can be thermally regulated sufficiently to allow 3D printing. Furthermore, owing to changes in manufacturing techniques, 3D printed goods may differ in size from CAD models. Furthermore, unlike more traditional processes like compression molding, where high volumes may be more expense efficient in producing, 3D printing has a fixed cost.
Factors Affecting Additive Manufacturing
Numerous variables influence the effectiveness of 3D printing. Some are completely hardware-related, although general quality can also be impacted by the performance of the material, cutting possibilities, and a variety of other factors. The grain size, sphericity, chemical characteristics, oxygen concentration, and mobility of the powdered substance all have an impact on 3D printed part performance indicators.
Additionally, layer thickness and temperature also majorly affect the quality of 3-D printed materials. The focus for the rest of this article will be on the grain size and roundness of the particles implemented for the process.
Traditional Particle size and Roundness Data in 3D Printing
Currently, the sizes of the particle categories of powdered materials widely utilized in metal 3D printing include 15-53 μm, 53-105 μm, and in certain circumstances, 105-150 μm.
The grain size range to be employed is determined by the energy sources used by the metallic printer. Printers that employ lasers as a source of energy are acceptable for usage due to their fine focusing point and simplicity with which it can dissolve finer particles, and the average size of 15-53 μm powder is appropriate to be used. When dissolving coarse material and using 53-105 μm powder, a plasma beam can be employed as a power source for the printer.
Roundness is a description of the closeness of powder material particles to a circle, with a value ranging from 0 to 1, with ideal spherical grains having a value of 1. The ability of a substance to flow readily is defined as fluidity, and its value is assessed by the time required for a specific amount of powder particles to flow through a measurement instrument with a given aperture (s/50g).
In general, the greater the sphericity value, the greater the flowability of the metal powder. As a result, it is simpler to regulate the particle layering and flow during metal 3D printing, resulting in improved printing quality components.
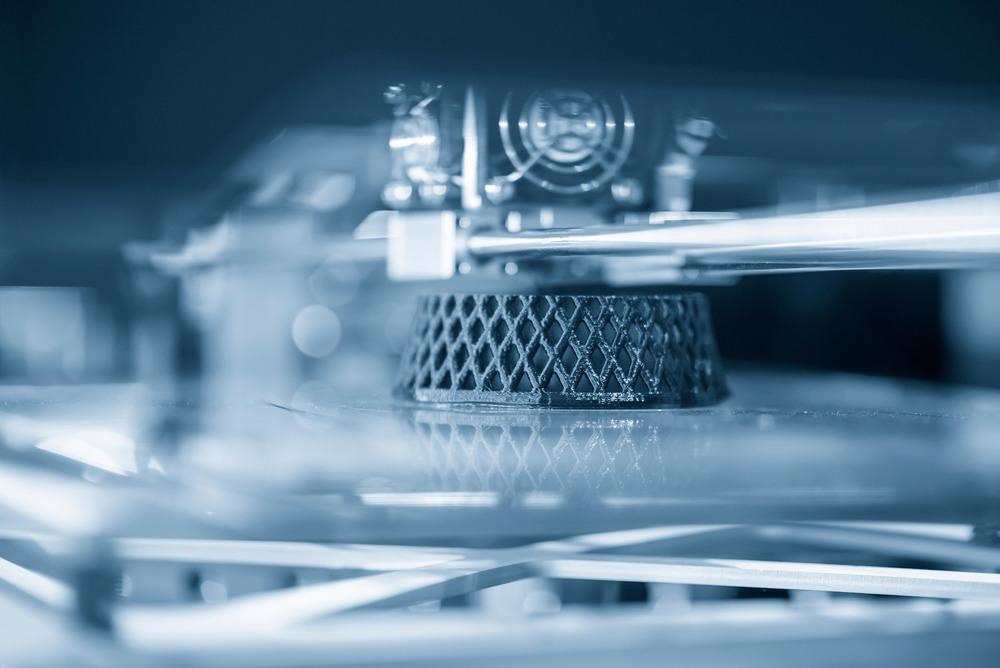
Image Credit: Pixel B/Shutterstock.com
Particle Size Analysis of Nickel Alloy Feedstocks
Research by Mr. Du and his team in the Journal of Manufacturing Science and Engineering showed that mixtures consisting of different particles may attain better compressibility than their constituent particles, and there was an ideal mixing percentage to produce the highest packing density of the mixture. A higher maximum mixture packing density was obtained by having a lower component particle size ratio (fine to coarse) and a higher component packing density ratio (fine to coarse). There was a component stacking density ratio threshold beyond which the mixing approach was ineffective for density enhancement. As the mass fraction of tiny particles increased, the powder flowability deteriorated, causing problems in powder feeding and, as a result, impacting the stability of 3-D printing.
The roundness of particles is another essential aspect. As the spherical or sub-spherical powder is more fluid, it is less prone to clogging the powder delivery mechanism during the printing. Furthermore, the spherical powder is simpler to distribute into a thin layer, improving the dimension precision and surface integrity of 3D printed products. Furthermore, the density and homogeneity of the components increase, making spherical powders the preferable raw material for 3D printing.
To summarise, to preserve AM's competitive edge, careful control and analysis of particle dispersion and roundness are required to deliver higher quality output.
References and Further Reading
Bettersize, 2022. The Importance of Particle Size and Roundness Analysis for 3D Printing. [Online]
Available at: https://www.bettersizeinstruments.com/the-importance-of-particle-size-and-roundness-analysis-for-3d-printing.html
Du, Wenchao, et al. Binder jetting additive manufacturing: effect of particle size distribution on density. 2021. Journal of Manufacturing Science and Engineering 143(9). Available at: https://asmedigitalcollection.asme.org/manufacturingscience/article-abstract/143/9/091002/1100582/Binder-Jetting-Additive-Manufacturing-Effect-of?redirectedFrom=fulltext
Thakkar, Rishi, et al. 2021. Impact of Laser Speed and Drug Particle Size on Selective Laser Sintering 3D Printing of Amorphous Solid Dispersions. Pharmaceutics 13(8). 1149. Available at: https://www.mdpi.com/1999-4923/13/8/1149
Gao, M. Z., Ludwig, B., & Palmer, T. A. 2021. Impact of atomization gas on characteristics of austenitic stainless steel powder feedstocks for additive manufacturing. Powder Technology. 383. 30-42. Available at: https://www.sciencedirect.com/science/article/pii/S0032591020311669?via%3Dihub
Wang, D. W., et al. 2022. Inheritance of microstructure and mechanical properties in laser powder bed fusion additive manufacturing: A feedstock perspective. Materials Science and Engineering: A. 832. 142311. Available at: https://doi.org/10.1016/j.msea.2021.14231
Disclaimer: The views expressed here are those of the author expressed in their private capacity and do not necessarily represent the views of AZoM.com Limited T/A AZoNetwork the owner and operator of this website. This disclaimer forms part of the Terms and conditions of use of this website.