Components of today’s turbines can be categorized into the tower, blades, and nacelle (including the turbine drivetrain), each of which has exacting and diverse material requirements.
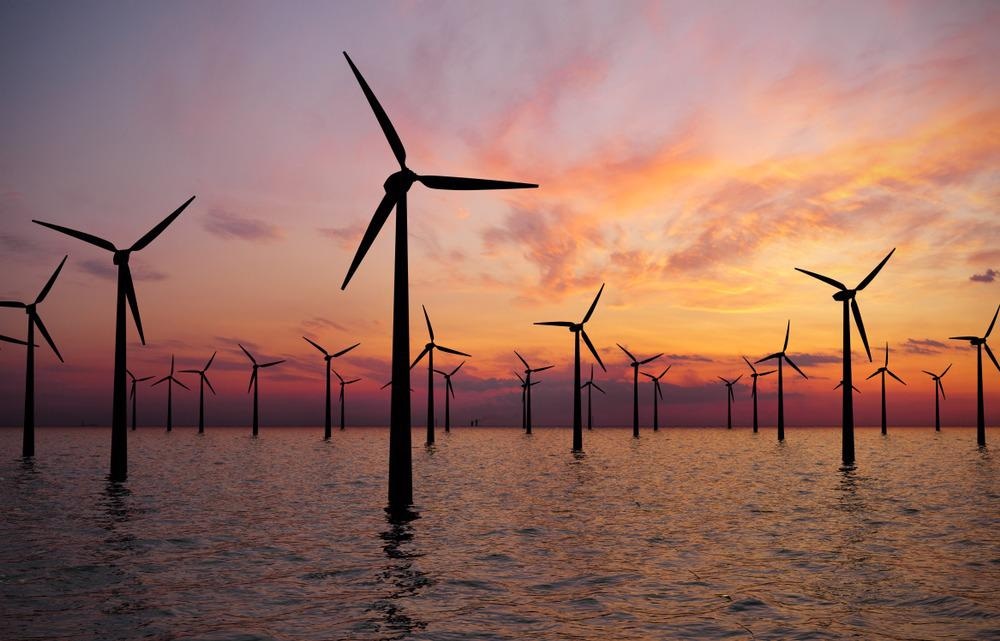
Image Credit: TebNad/Shutterstock.com
The ongoing transition to a decarbonized energy sector has placed wind power as one of the fastest-growing energy sources today, with hundreds of thousands of wind turbines giving over 740GW of capacity worldwide. To meet the Paris Agreement climate goals, this capacity must increase nearly ten-fold by 2050 according to the International Renewables Agency (IRENA) (Future of wind, 2019).
This places the utmost importance on continuing to optimize wind turbine efficiency, durability, recyclability, and cost-effectiveness through intelligent engineering design and material selection.
Historic Materials and Designs
The first wind turbine that produced electricity was created by James Blyth in 1887 and powered the Scottish inventor’s holiday cottage. The turbine was 10m tall with a wooden tripod tower, semicylindrical canvas sails, and a vertical main rotor shaft.
The following decades saw the development of this design and material selection with varying degrees of success. For example, in 1945 the world’s largest turbine at the time suffered a catastrophic failure in one of its two steel blades after only a few years of intermittent use, whilst a slightly later three-bladed design of composite construction was operational for 11 maintenance-free years before its decommissioning and installation in the Danish Energy Museum (Mishnaevsky et al., 2017).
It wasn’t until the 1970s, amid rocketing fuel prices, that rapid development was made and turbine designs and materials began to converge on those commonly seen today. This includes steel tubular towers, three composite blades, and a horizontal main rotor shaft.
Tower
To make use of the higher wind speeds and reduced turbulence at greater altitudes, turbine towers can reach heights of nearly 180m. This results in enormous static, dynamic, and cyclical loading from factors such as the self-weight of the turbine, wind shear, and the rotation of the blades.
To withstand buckling from such loads, towers are commonly made of tubular steel manufactured in sections and tapered towards the top. Although standard structural grade steel (S235 and S355) is normally used, various subgrades are common for offshore applications where high levels of corrosion and wave loading must also be considered (Igwemezie et al., 2018).
To combat the transportation restrictions and costs of increasingly large steel bottom sections of taller towers, concrete-steel hybrid construction is proving more and more popular. This uses concrete for the lower part of the tower whilst keeping the smaller diameter tubular steel sections higher up, which can result in total turbine cost savings over 12% and improved structural stiffness (Huang et al., 2022; Chen et al., 2020).
Blades
Turbine blades can reach speeds of up to 180mph at their tip and are subject to immense aerodynamic, inertial, and gyroscopic loads. They must therefore be made from stiff and lightweight materials resistant to high-cycle fatigue.
By exhibiting such properties, glass fiber-reinforced polymer (GFRP) has become the most common material for blade construction. Depending on the location in the blade, it is either used monolithically or in combination with a core material such as balsa wood in sandwich construction.
More from AZoM: A Closer Look at Plant-Based Composites
GFRP blades typically use a thermoset as the polymer matrix and contain approximately 75 wt.% glass fibre for longitudinal reinforcement. Alternatives to replace or to compliment the glass fibres include carbon, aramid, and basalt, which give stiffer, lighter, but more expensive composites.
The pursuit of higher capacity turbines has continued to lengthen the blades (now reaching up to 118m) and drive the development of these composites. One possible future development lies in the inclusion of nano-reinforcements, such as carbon nanotubes or graphene, within the composite matrix. This is predicted to drastically increase blade lifespan and facilitate longer blades through enhanced material strength, toughness, and fatigue resistance (Zhou et al., 2016; Ma and Zhang, 2014).
Nacelle and Generator
The nacelle refers to the protective cover on top of the tower which houses the turbine drivetrain (including the generator, gearbox, and low- and high-speed shafts). Although under considerably less severe loading than the turbine blades, the nacelle also commonly uses GFRP in sandwich construction. The core material is typically a polymer foam, which also forms the stiffeners often present throughout the nacelle to support maintenance workers and equipment.
Much of the turbine drivetrain is produced from various alloy steels and cast irons, the generator, however, can contain a more diverse range of materials depending on the type. The most common of which is the doubly-fed induction generator (DFIG), containing predominantly magnetic steel and copper.
However, the most popular generator type with new turbines and particularly those offshore is the permanent magnet generator (PMG). PMGs are smaller, lighter, more efficient, and more reliable than equivalent DFIGs, but come with a higher capital cost. Part of this cost is due to the presence of rare earth elements alongside the magnetic steel and copper, including neodymium (Nd), praseodymium (Pr), dysprosium (Dy), and terbium (Tb) (Lacal-Arántegui, 2015).
Generators of even smaller dimensions, lighter weight, and more efficient operation than PMGs appear close to commercialization. Such generators use superconducting rotor windings, either at high (-180°C) or low (-260°C) temperatures, to give a much stronger magnetic field and potentially satisfy the demand for larger capacity turbines.
Last year, a turbine with a high-temperature superconductor (HTS) generator was successfully trialed for 6 months in Denmark. Despite a higher capital cost than PMGs due to the superconducting wire (containing gadolinium and barium) and the cryogenics (liquid helium), HTS generators showed tremendous promise as a cost-effective and high-performance solution, especially for larger turbines of over 10MW capacity (SKF, 2021).
References and Further Reading
Irena.org. 2019. Future of wind. [online] Available at: <https://www.irena.org/publications/2019/Oct/Future-of-wind> [Accessed 23 February 2022].
Mishnaevsky, L., Branner, K., Petersen, H., Beauson, J., McGugan, M. and Sørensen, B., 2017. Materials for Wind Turbine Blades: An Overview. Materials, 10(11). https://www.mdpi.com/1996-1944/10/11/1285
Igwemezie, V., Mehmanparast, A. and Kolios, A., 2018. Materials selection for XL wind turbine support structures: A corrosion-fatigue perspective. Marine Structures, 61, pp.381-397. https://www.sciencedirect.com/science/article/pii/S0951833917304859
Huang, X., Li, B., Zhou, X., Wang, Y. and Zhu, R., 2022. Geometric optimisation analysis of Steel–Concrete hybrid wind turbine towers. Structures, 35, pp.1125-1137. https://www.sciencedirect.com/science/article/pii/S2352012421007487
Chen, J., Li, J. and He, X., 2020. Design optimization of steel–concrete hybrid wind turbine tower based on improved genetic algorithm. The Structural Design of Tall and Special Buildings, 29(10). https://www.researchgate.net/publication/340255062_Design_optimization_of_steel-concrete_hybrid_wind_turbine_tower_based_on_improved_genetic_algorithm
Zhou, H., Mishnaevsky, L., Yi, H., Liu, Y., Hu, X., Warrier, A. and Dai, G., 2016. Carbon fiber/carbon nanotube reinforced hierarchical composites: Effect of CNT distribution on shearing strength. Composites Part B: Engineering, 88, pp.201-211. https://www.sciencedirect.com/science/article/pii/S1359836815006654
Ma, P. and Zhang, Y., 2014. Perspectives of carbon nanotubes/polymer nanocomposites for wind blade materials. Renewable and Sustainable Energy Reviews, 30, pp.651-660. https://www.sciencedirect.com/science/article/pii/S1364032113007570
Lacal-Arántegui, R., 2015. Materials use in electricity generators in wind turbines – state-of-the-art and future specifications. Journal of Cleaner Production, 87, pp.275-283. https://www.sciencedirect.com/science/article/pii/S0959652614009779
SKF, 2021. High output. Low weight. Wind energy’s superconducting future. [online] Wind Farm Management Blog. Available at: <https://windfarmmanagement.skf.com/high-output-low-weight/> [Accessed 24 February 2022].
Disclaimer: The views expressed here are those of the author expressed in their private capacity and do not necessarily represent the views of AZoM.com Limited T/A AZoNetwork the owner and operator of this website. This disclaimer forms part of the Terms and conditions of use of this website.