AT&T researcher Johannes F. Gottwald published the first 3D-printing patent in 1971. Gottwald’s machine was designed to create 3D objects out of heated metal alloy, but now the new material options available for 3D printing are bringing the technology ever closer to an imagined sci-fi future.
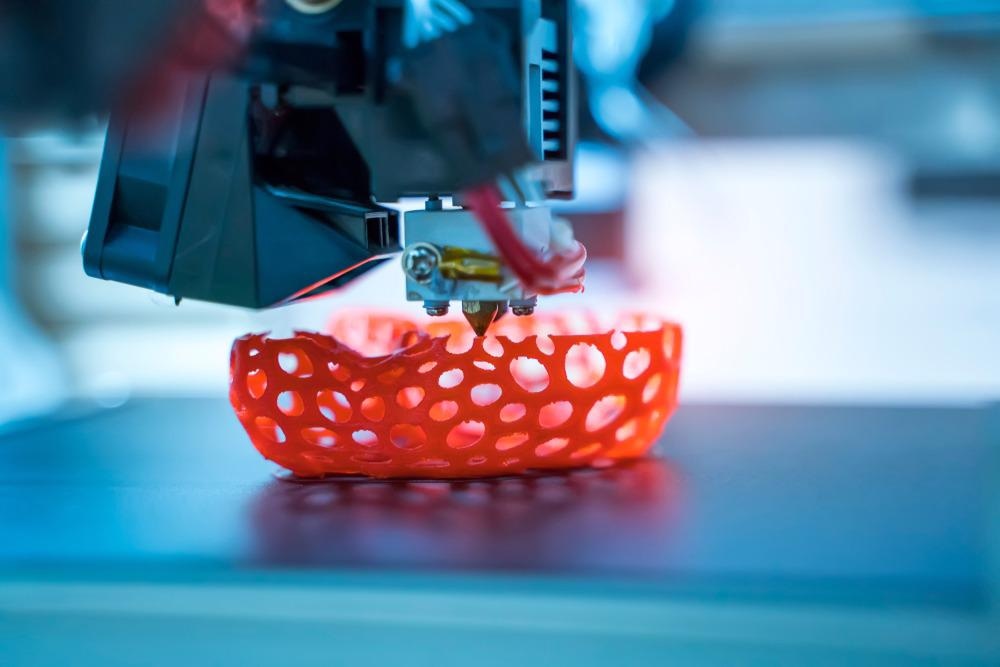
Image Credit: asharkyu/Shutterstock.com
Types of Additive Manufacturing
“3D-printing” is something of a misnomer: there are in fact seven types of additive manufacturing employed today, and not all of them are layer-by-layer deposition methods as the “printing” part of the name implies.
Within all of the following categories, there are different methods that offer different print speeds, accuracy and tolerances, and sizes. These include nanoscale additive manufacturing and large format additive manufacturing for parts over a meter in one dimension.
Vat Photopolymerization
In vat photopolymerization, a vat of liquid photopolymer resin is selectively solidified with a light source layer-by-layer to create a 3D model.
Material Jetting
Material jetting works in a similar way to typical 2D inkjet printers. The material is jetted onto a build platform – like ink-jetted onto a piece of paper – and built up layer-by-layer to make a 3D object. Material jetting works with either continuous or drop-on-demand (DOD) jetting.
Binder Jetting
In binder jetting, alternating layers of typically liquid binder material and powdered build material are deposited by a printer head moving horizontally along x and y axes.
Material Extrusion
In material extrusion – one of the most popular additive manufacturing techniques, especially fuse deposition modeling (FDM) which is trademarked by the U.S. company Stratasys – print material is drawn through a nozzle where it is heated and extruded layer-by-layer to make a 3D piece. The extrusion unit typically moves horizontally in x and y axes while the print bed moves up and down on the z axis, although robotic arms are also used with fixed print beds for material extrusion.
Powder Bed Fusion
In powder bed fusion, energy is applied to a powder material that melts or sinters the material into a 3D shape. Lasers, electron beams, and selective heat are all used as energy sources.
Sheet Lamination
Lamination is an additive manufacturing technique that includes advanced ultrasonic additive manufacturing (UAM) – which processes sheets or ribbons of metal and binds them with ultrasonic welding – and the more traditional wood- or composite-based laminated object manufacturing (LOM) methods.
Directed Energy Deposition
Directed energy deposition (DED) is a catch-all name for a number of additive manufacturing techniques for adding material and shapes to existing materials and equipment. DED methods include 3D laser cladding and direct metal deposition.
Materials for Additive Manufacturing
There are three main categories of materials for additive manufacturing: polymers, ceramics, and metals. Polymers are the most commonly used and available materials, but the use of more materials is being developed constantly as the technology matures. Materials are typically produced in powders or wire feedstock, although this is also diversifying over time.
Further Reading: A Current Look at 3D Printed Food
Polymers
Common plastics including nylon, polycarbonate, ABS (acrylonitrile butadiene styrene), and PLA (polylactide) including soft PLA – as well as their recycled alternatives – can all be used in 3D printing. Polymers like these are typically distributed in wire feedstock and used in material extrusion printers.
Waxes and epoxy-based resins are also frequently used, and many techniques involve mixing powdered polymers in different quantities for varying aesthetic and structural effects.
Metals
Metals are used for 3D printing complex electronic components and circuitry as well as structural and mechanical parts and integral working components. They can be deposited in liquid form with high-temperature techniques, or sintered or melted from powder.
Commonly used metals for 3D printing include steel, gold, silver, aluminum, cobalt chrome alloy, titanium, and stainless steel.
Ceramics
Ceramics are typically used in powder-based additive manufacturing techniques. Silica and glass, porcelain, and silicon-carbide are typically used, and ceramic fibers can be combined with polymer or metal substrate materials for increased strength.
Novel Materials for Additive Manufacturing
In theory, any material can be printed in a layer-by-layer method. There are methods for 3D printing adhesive and regular paper, chocolate, and combined polymer and adhesive sheets for laminate object manufacturing.
While any material can be 3D printed in theory, it should be noted that the high temperatures and pressures required by many additive manufacturing techniques can fundamentally alter the microstructure of the material, resulting in changes to properties such as mechanical strength and durability after manufacturing.
Medicine
Some of the most promising novel applications of 3D printing are in medicine. So-called “bioprinting” is capable of printing human tissues from stem cells, building up material molecule by molecule. Customized implants, drug delivery devices, scaffolds for tissue engineering and regeneration, and prostheses have all been created in 3D printers.
Medical additive manufacturing uses polymer, metal, and ceramic materials – as well as compounds with various doping agents - to provide biocompatibility or nanostructured programmable biodegradability.
Construction
Additive construction is currently on the rise around the world. Traditional building materials like wood, glass, metal, and concrete can be 3D printed with on-site machines, enabling remote and round-the-clock construction.
Biomaterials
Many researchers are developing biomaterials that can be sustainably produced for additive manufacturing. Bacteria and natural fibers are being explored in this area.
Materials in Space
NASA is developing additive manufacturing that can use materials found in space to make parts and components needed for long-term extra-terrestrial missions. Dust from Mars’s surface, for example, could be used to create replacement parts for a permanent base on Mars in the future.
References and Further Reading
Additive Manufacturing Research Group. Loughborough University. [Online] Available at: https://www.lboro.ac.uk/research/amrg/.
Additive Manufacturing. NASA. [Online] Available at: https://www.nasa.gov/sites/default/files/atoms/files/additive_mfg.pdf.
Bourell, D., J.-P. Kruth, M. C. Leu, and G. Levy (2017). Materials for additive manufacturing. CIRP Annals - Manufacturing Technology. Available at: http://dx.doi.org/10.1016/j.cirp.2017.05.009.
Haleem, A., M. Javaid, R. Suman, and R. P. Singh (2021). 3D Printing Applications for Radiology: An Overview. Indian Journal of Radiology and Imaging.
Schaffner, M. et al. (2017). 3D printing of bacteria into functional complex materials. Science Advances. Available at: https://doi.org/10.1126/sciadv.aao6804.
Tappa, K. and U. Jammalamadaka (2018). Novel Biomaterials Used in Medical 3D Printing Techniques. Journal of Functional Biomaterials. Available at: https://dx.doi.org/10.3390%2Fjfb9010017.
Disclaimer: The views expressed here are those of the author expressed in their private capacity and do not necessarily represent the views of AZoM.com Limited T/A AZoNetwork the owner and operator of this website. This disclaimer forms part of the Terms and conditions of use of this website.