Hardness Testing is applied to a great number of materials, and for over 250 years, it has been an invaluable and frequently used mechanical test.
A variety of hardness tests can be used to establish the different hardness values for the same test specimen. The type of hardness test is typically guided by customer requirements, as hardness measurements are often reported as values on the specification sheets of manufactured goods.
The most frequently used tests that determine material hardness are the Rockwell, Brinell, Vickers and Knoop hardness tests.
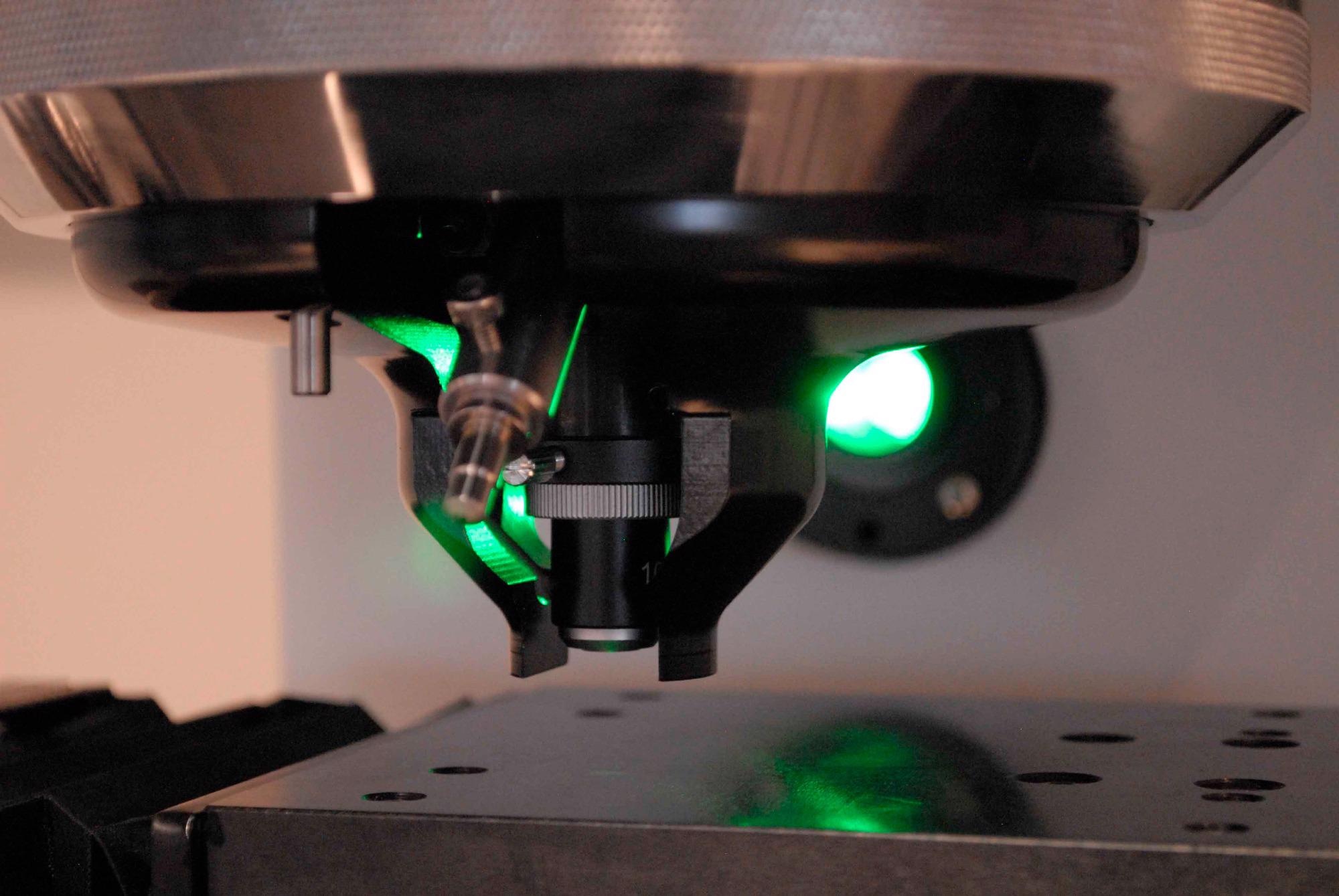
Image Credit: Tinius Olsen
Each of these tests measures hardness by evaluating and establishing resistance to the penetration of a non-deformable ball, cone or four-sided pyramidal Diamond indenter. Each test establishes the depth to which the indenter will sink into the material, at a pre-defined load, within a specific time period.
While the Rockwell and Brinell tests mostly apply to metals and ceramics, an ISO standard for Rockwell hardness testing of plastics (ISO 2039-2) can be used. The Vickers test can be applied to determine the hardness of metals, some ceramics, polymers and even a number of biomaterials.
Knoop testing was developed to measure the hardness of the thinnest materials and softer materials like paint and plated jewelry.
The Rockwell hardness test is the most frequently applied hardness test method. It is a measurement predicated on the application of a load and the net increase in depth of the resulting impression. To put it another way, when applying a fixed force (load) and a known indenter, the harder the material, the smaller the indentation.
This method is utilized for testing all metals, excluding conditions where the test metal structure or surface conditions would present an excess of variations, where the large indentations would be too much for the application, or where the sample size or sample shape prevents its use.

Image Credit: Tinius Olsen
Rockwell determines the permanent depth of indentation created by a force/load on an indenter. For instance, an indenter may be either a tungsten carbide ball of a specific diameter or a spherical diamond-tipped cone of 120° angle and 0.2 mm tip radius, typically referred to as a “Brale Indenter.”
The indenter and the test load combination determine the hardness scale which is expressed as letters such as A, B and C, etc.
When choosing the appropriate Rockwell scale, a general rule of thumb is to pick the scale that determines the greatest load and indenter combination possible. This means taking into consideration conditions that may influence the test result and not exceeding pre-defined operation conditions.
These conditions include but are not limited to adhering to the hardness range of the Rockwell scale used, test specimens that are within the minimum thickness for the depth of indentation, or a test impression that is near to the edge of the specimen or another impression. Cylindrical specimens should also be considered in these testing parameters.
On the other hand, Brinell hardness is determined by the application of a tungsten carbide sphere of a specific diameter at a particular load into the surface of a material and optically measuring the diameter of the residual indentation post-test.
The Brinell Hardness Test is most typically used for testing materials that have an extremely coarse structure or when the surface is too rough for testing using another test method, such as castings and forgings.
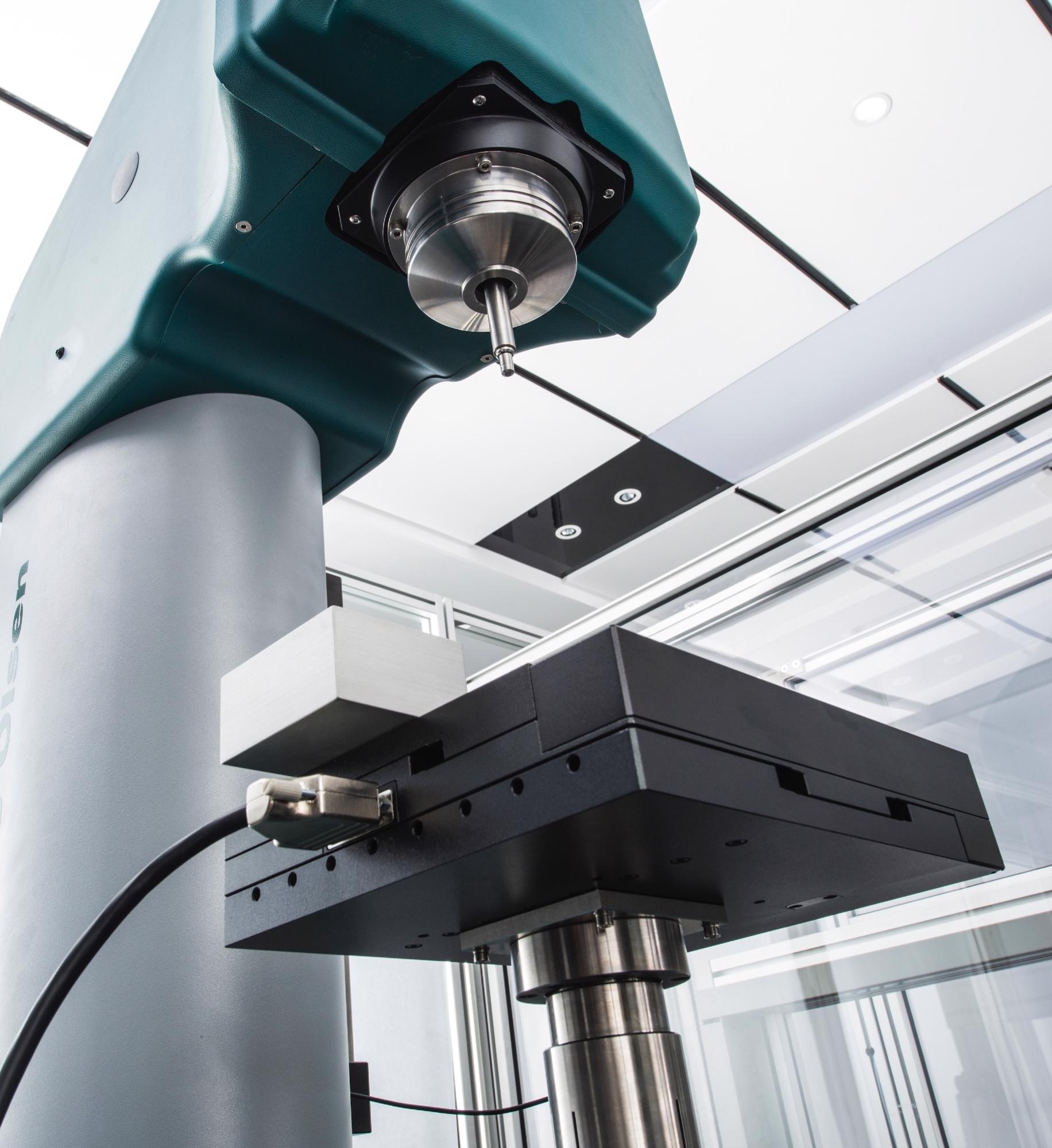
Image Credit: Tinius Olsen
Brinell testing generally applies a very high test load (3000 kgf) with a 10 mm diameter indenter so that the indentation averages out the majority of surface and sub-surface inconsistencies. Lighter load/Ball diameter combinations can be utilized when sample thickness does not support the heavier loads of Brinell.
The Brinell hardness number is calculated by dividing the load used, in kilograms, by the actual surface area of the indentation in square millimeters.
The Vickers and Knoop hardness test methods, also commonly known as micro-hardness test methods, due to the light loads being applied, are generally used for small parts, microstructures, thin sections, fracture testing, weld heat-affected areas, or case depth work.
Although Vickers and Knoop tests differ entirely based on the indenter design and the way they measure the resulting indentation, they both incorporate the same methodology for applying the test and are frequently performed using the same hardness tester.
It is extremely useful for testing across an extensive range of materials, but test samples must be polished as much as possible to facilitate measuring the size of the impressions in microns. Generally, loads for Knoop or Vickers testing are extremely light, ranging from 1 gm to 1 kgf, although "Macro" Vickers loads can range up to 120 kg or more.
The sample surfaces in the Vickers test method are subjected to a pre-defined load, exerted by a four-sided pyramidal diamond indenter. This offers a standardized length of time known as the dwell time. The diagonal of the resulting indentation is measured under a microscope and the Vickers Hardness value is then determined.
Knoop is different from Vickers testing in the way it elongates two of the four-sided diamond indenters and only applies the dimensions of the elongated impression to establish the Knoop hardness value. The development of this design is to test the hardness of the softer materials with a minimal amount of penetration by all types of hardness testing.
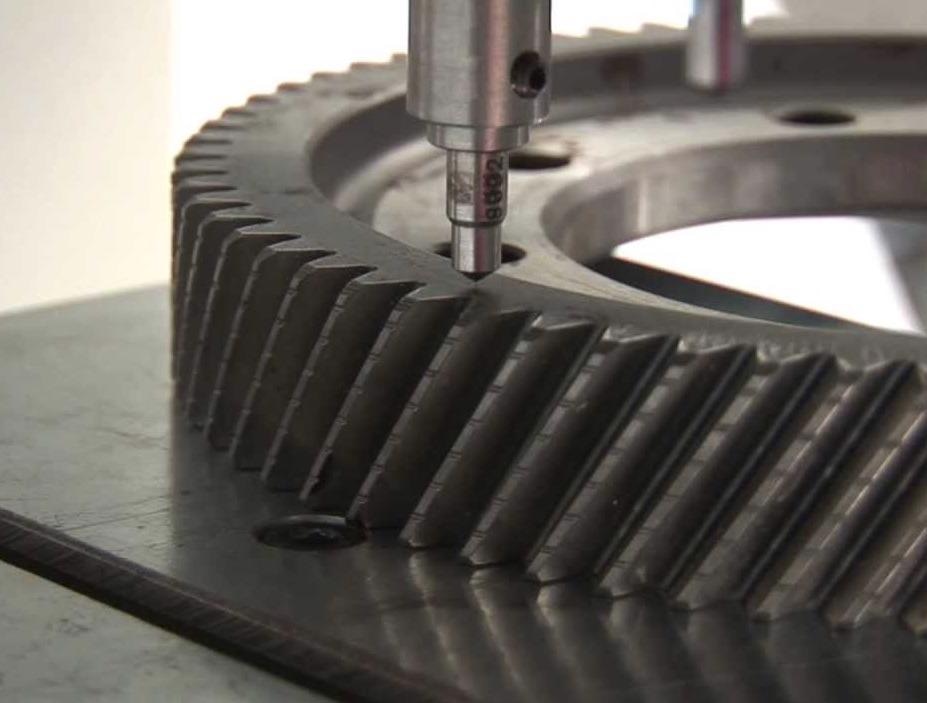
Image Credit: Tinius Olsen
This test is used in the most exacting of quality control applications. This includes inspecting welds that experience extreme pressures and heavy-duty machinery utilized in manufacturing operations.
Fundamentally, the test method used is determined by the type of material and expected hardness. Materials such as hardened bearing steels possess small grain size and can be measured with the Rockwell scale as diamond indenters and high PSI loading are used.
Materials such as cast irons and powder metals will necessitate the use of a much larger indenter such as those found in Brinell scales. Small sections or extremely small parts may require the application of the micro-hardness tester using the Vickers or Knoop Scale.
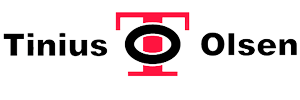
This information has been sourced, reviewed and adapted from materials provided by Tinius Olsen.
For more information on this source, please visit Tinius Olsen.