Corrosion is the degradation of an alloy, or the progressive disintegration of a component, caused by its exposure to the environment. Corrosion deterioration of metallic alloys exposed to the atmosphere, seawater, chemicals, or other adverse conditions can be prevented through the use of a variety of techniques.
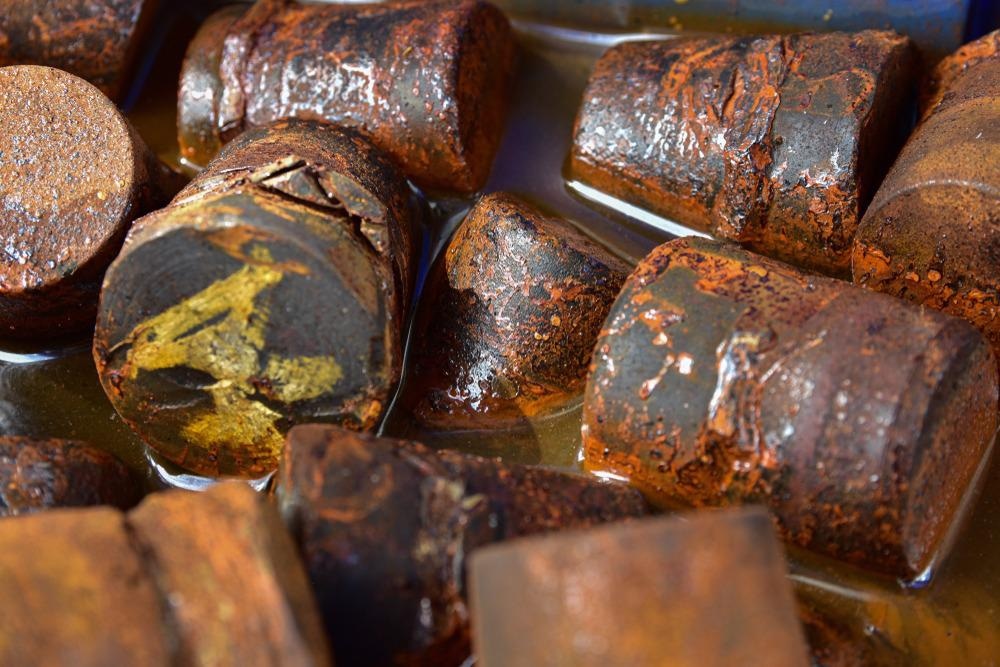
Image Credit: Tum ZzzzZ/Shutterstock.com
Some exposed metallic alloys, such as those used in electromagnets, are prone to corrosion and may disintegrate into a powder even in clean, temperature-stable interior conditions if not adequately treated to prevent corrosion.
Do All Alloys Corrode?
Almost all alloys corrode or rust to an extent. Corrosion is a type of oxidation, and rusting is a component of corrosion. Rusting occurs when the alloy is in contact with air and humidity, resulting in the formation of an iron oxide coating. Corrosion happens when alloys are exposed to oxygen and chemicals, resulting in the development of metal oxides or salts.
Corrosion Occurrence in Steel
As standard steel is made up of a variety of metals, including iron, it can corrode. Stainless steel, which is 18 percent or more chromium, creates a protective coating (chromium oxide) on the surface of the alloy, while a vanadium concentration also plays a substantial role in preventing corrosion.
Corrosion in Aluminum and Magnesium
Aluminum alloys do corrode, but when water comes into contact with the metallic surface, it develops a protective coating called 'aluminum alloy oxide' which makes it more corrosion resistant. Magnesium is prone to corrosion (especially galvanic corrosion), which appears as a grey layer on the surface. Out of all metallic alloys, magnesium alloys have the worst corrosion resistance properties.
Do Zinc and Nickel Corrode?
When zinc is exposed to air, it interacts with carbon dioxide to generate a zinc hydroxide film. This shields the metal from external air reactions, which is why zinc is used to galvanize other alloys and prevent corrosion. Pure nickel is extremely corrosion-resistant, particularly when exposed to a range of reducing agents. It is resistant to oxidation when it is alloyed with chromium, resulting in a wide range of alloys with excellent corrosion resistance in both reduction and oxidation conditions.
Types of Corrosion in Alloys
Corrosion is the result of a series of often complex chemical reactions that may be induced by a variety of factors, that depend on the setting. Uniform corrosion is the most typical form of corrosion, described as an even attack over a material's surface. It is the most innocuous since the attack is mild in intensity, making the impact on material performance simpler to measure and analyze due to the ability to consistently repeat and test the phenomenon.
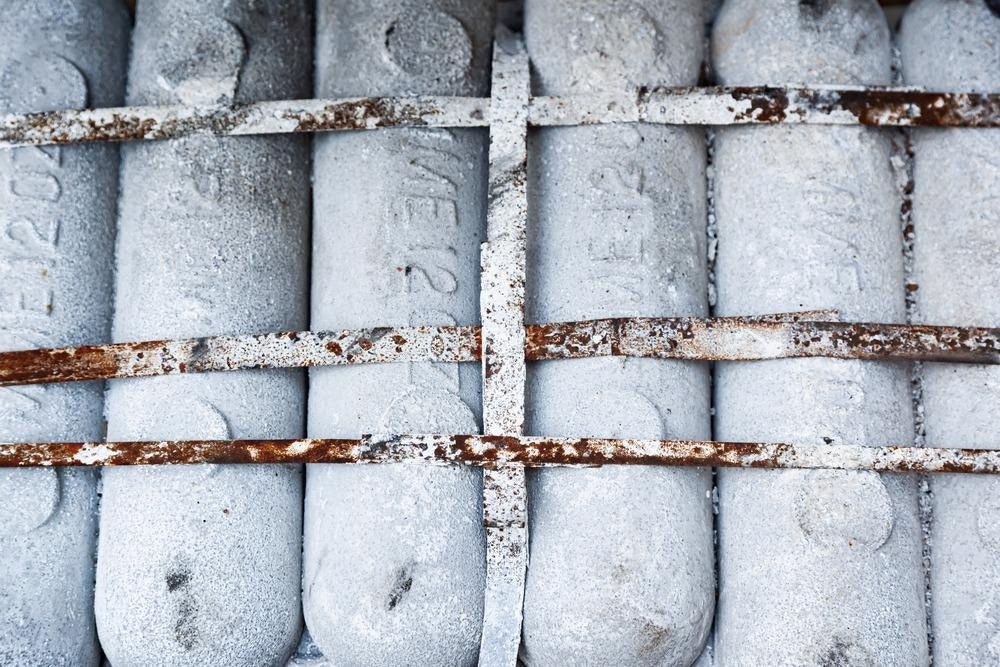
A pack of zinc anodes for installation on a ship to protect the hull from corrosion. Image Credit: ZHMURCHAK/Shutterstock.com
When fast corrosion of an alloy occurs at its grain boundaries while the remainder of the alloy surface remains intact, this is known as intergranular corrosion. Impurities can segregate at grain boundaries in some alloys because of improper heat treatment, affecting the mechanical characteristics of the alloy but leaving the remainder of the alloy unharmed.
Crevice corrosion is a type of extremely penetrative localized corrosion that often occurs from a stationary microenvironment with an ion concentration difference between two parts of a metal. Crevice corrosion occurs in protected areas and is produced by a connection between two surfaces or the accumulation of deposits such as dirt. Another factor that might cause this is the presence of stagnant water within a fissure.
Stress corrosion cracking is driven by a complex of shear strain and a corrosive environment, which happens often at high temperatures. It requires the simultaneous existence of three factors: first, a sensitive alloy, second, a wet or moist atmosphere, and third, maximum tensile, which initiates the fracture and permits crack propagation.
Stress corrosion cracking is driven by a complex of shear strain and a corrosive environment, which happens often at high temperatures. It requires the simultaneous existence of three factors: first, a sensitive alloy, second, a wet or moist atmosphere, and third, maximum tensile, which initiates the fracture and permits crack propagation.
Techniques to Prevent Corrosion in Alloys
There are several strategies for preventing corrosion in alloys, the most basic of which is the use of the correct alloy, such as corrosion-resistant nickel mixed with oxidation-resistant chromium, creating an alloy that can be used in both oxidized and reduced chemical conditions.
Another efficient way to prevent corrosion in alloys is to control the alloy's reactivity to particular chemicals that induce corrosion. For example, reducing exposure to specific chemicals by moving applications or decreasing chemical levels in the air or water.
Latest Research
According to a recent study published in the journal Proceedings on Engineering Sciences, coating another metallic alloy on the surface of the initial material increases the probability of that metal disintegrating faster than the one beneath it. This surface coating can be conducted in two ways:
- Cathodic protection transforms steel into the cathode of an electrochemical cell. Galvanizing, or the application of zinc to iron alloy steel, is the most frequent type of cathodic protection. Zinc is a more active metal than steel or alloys, therefore when it corrodes it prevents the metal or alloy from corroding. Steel pipes supplying liquid or gasoline, heater units, marine structures, and oil rigs all benefit from cathodic protection.
- Anodic protection transforms steel into the anode of an electrochemical system in the reverse of cathodic protection. Coating the iron-carbon steel alloys with a less active metal, like tin, is a popular method for doing this. The alloy is perfectly safe when the tin layer is there, since tin does not rust. Anodic protection is often employed on sulfuric acid and 50% caustic soda storage tanks made of carbon steel.
Paint coats also shield the alloy by blocking the electrochemical charge from passing to the corrosive medium and the metal underneath.
Furthermore, regulating the environment, which may assist in reducing these responses, is one of the most successful methods. This may be as easy as limiting exposure to rain or water, or it could include reducing the quantity of sulfur, oxygen, or carbon in the environment. In radiators, for example, altering the roughness, acidity, or oxygenation concentration of the water can prevent corrosion.
Role of Inhibitors in Corrosion Prevention
One more method used to prevent corrosion in alloys is the utilization of inhibitors. Corrosion inhibitors are compounds that are selected to interact with the alloy's surface or surrounding gases, inhibiting corrosion-causing electrochemical reactions. They create a protective covering when deposited on the alloy's surface.
Dispersion methods may be used to apply inhibitors as a mixture or as a protective layer. When it comes to applying corrosion inhibitors, passivation is a popular method. Aside from that, methods like galvanization and electroplating are used, in which the substrate is submerged in a molten bath of the protective alloy, or a small coating of metal such as chromium or nickel is applied to the substrate through an aqueous electrolyte.
More from AZoM: Electro-Spark Deposition Applied to Metal Alloys
References and Further Reading
Nyby, C., Guo, X., Saal, J. E., Chien, S. C., Gerard, A. Y., Ke, H., & Frankel, G. S. (2021). Electrochemical metrics for corrosion-resistant alloys. Scientific data, 8(1), 1-11. https://springernature.figshare.com/articles/dataset/Metadata_record_for_Electrochemical_metrics_for_corrosion_resistant_alloys/13611623
Harsimran, S., Santosh, K., & Rakesh, K. (2021). Overview of corrosion and its control: A critical review. Proceedings on Engineering Sciences, 3(1), 13-24. http://pesjournal.net/journal/v3-n1/2.pdf
Sander, G., Tan, J., Balan, P., Gharbi, O., Feenstra, D. R., Singer, L., & Birbilis, N. (2018). Corrosion of additively manufactured alloys: a review. Corrosion, 74(12), 1318-1350. https://meridian.allenpress.com/corrosion/article/74/12/1318/199171/Corrosion-of-Additively-Manufactured-Alloys-A
Disclaimer: The views expressed here are those of the author expressed in their private capacity and do not necessarily represent the views of AZoM.com Limited T/A AZoNetwork the owner and operator of this website. This disclaimer forms part of the Terms and conditions of use of this website.