Solid epoxy resins are widely utilized in additive manufacturing to produce functionalized components for a variety of fields. This article will look at the use of these resins in additive manufacturing, and recent research into improving their isotropic properties to manufacture materials with enhanced temperature and strain detecting abilities.
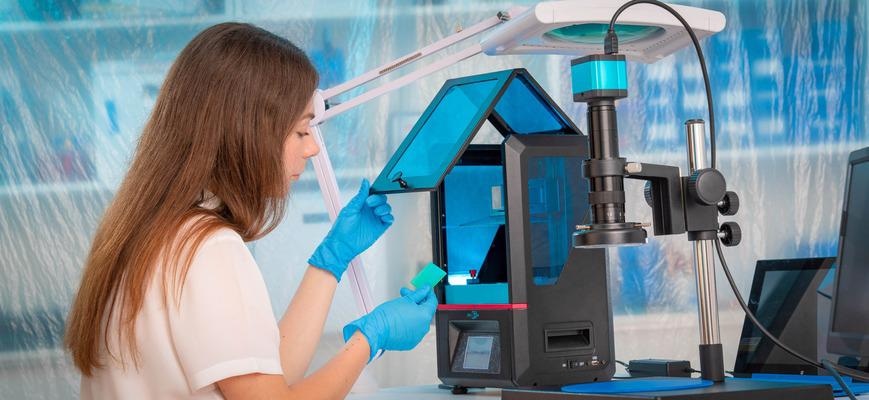
Image Credit: luchschenF/Shutterstock.com
Epoxy Resins and Additive Manufacturing
Additive manufacturing is an innovative technology that is disrupting several industries and research fields. 3D printing techniques possess several advantages over conventional manufacturing methods, such as waste reduction, freer design, low cost, rapid production, low volume production, and integrated assembly.
Epoxy resins have been widely used to produce numerous devices and components. Automobile parts, printed electronic materials, coatings, adhesives, and fiber-reinforced composites have all been manufactured out of 3D printed epoxy resin-based materials.
3D printing epoxy resin has advantages over conventional materials due to the low cost of resins and the ability to produce complex geometries rapidly. Technical aspects such as curing, the types of suitable resins, the role of photoinitiators and curing agents, and the performance of printed parts are crucial elements of research into these advanced materials. Optimizing printing processes and material properties is essential for improving the commercial viability of 3D printed epoxy resin-based materials and components.
Isotropic Materials
In isotropic materials, the material properties remain the same when tested in multiple directions. These materials differ from anisotropic materials, which possess varying properties when tested in multiple directions. Examples of isotropic materials include metals, plastics, and glass. Inducing isotropy in materials such as epoxy resins which display anisotropic behavior is a key area of research in materials science to produce printed components with enhanced mechanical and functional properties.
Material Extrusion 3D Printing
A widely used additive manufacturing method is material extrusion (MEX), which is otherwise known as fused deposition modeling or fused filament fabrication.
In material extrusion, the epoxy filament can be easily handled because of its availability in solid form. In contrast, the powders used in selective laser sintering and the often harmful resins used in stereolithography require specialist and careful handling, with specific safety and storage requirements. Moreover, material extrusion processes can handle a wider range of materials including thermoplastics compared to other methods.
Material extrusion processes are also more cost-effective than other methods, and multi-material printing can be easily achieved using multiple extrusion nozzles. Extruded materials can be functionalized with other materials without the limitations that other techniques such as selective laser printing place on additives.
However, MEX printing is hindered by the rapid solidification of printed materials after deposition. Weak interfacial bonding is caused by limits in diffusion and entanglement between layers and infill lines. Several studies have highlighted the limitations of this technique, with different techniques employed to overcome them.
MEX Optimization Methods
Several methods have been explored in current research to address the mechanical anisotropy of materials printed using MEX techniques. Parameters such as printing speed, layer height and width, and temperature can be optimized to achieve the strongest possible layer bonding. The optimal orientation of the component can be used. The drawback to these methods is that they have to be performed individually, and furthermore the design freedom is restricted.
Other methods involve optimizing the properties of the material and the fabrication process. Materials such as carbon nanotubes can be incorporated, with subsequent microwave irradiation used to heat them and facilitate polymer chain diffusion and provide improved adhesion between layers.
Some studies have reported the use of gamma radiation to induce cross-linking in the filaments, whilst others have used lasers to induce thermal energy to each layer and improve inter-layer bonding. Drawbacks to many of these methods is cost, the need for complex equipment, and increased processing steps. Many techniques fail to improve the isotropy of the materials.
Achieving Isotropy in MEX-Printed Epoxy Resin Materials
Introducing thermosets into the materials is another method for achieving isotropy in MEX printed materials. A new study in Additive Manufacturing has reported the first use of a thermosetting polymer filament which can be printed on a low-cost MEX printer. A feature of the technique developed in the research is a post-curing step that induces cross-linking, overcoming the mechanical anisotropy that hinders MEX printed materials.
A solid epoxy resin, which has a high molecular weight, has been used by the researchers for the material formulation. Liquid epoxy resins with additives can be incorporated into the material formulation, facilitating multi-material extrusion printing. This helps to incorporate localized functional properties into the printed components.
The authors have incorporated single-walled carbon nanotubes into the materials, which provides electrical conductivity, and they have stated that other properties such as flame resistance can be incorporated into the printed materials, providing opportunities for utilization in multiple applications.
By modifying the materials with electrically conductive nanoparticles, components can be printed with sensing capabilities, such as piezoelectric sensors. In addition, using carbon nanotubes can incorporate temperature sensing abilities into smart components printed using the proposed method in the research. A proof-of-concept study has been performed on the functionalized materials printed by MEX for temperature and strain sensing applications.
Further research opportunities have been identified in the study, including the need for further investigation of sensing capabilities and a focus on the effect of the material’s electrical anisotropy, repeatability, and different filler loadings in materials. The research has demonstrated the potential of this novel process for developing 3D printed components with superior properties and possibilities for application in a variety of advanced electrical devices.
More from AZoM: Laser Ablation for Elemental Analysis of Forensic Samples
References and Further Reading
Drücker, S et al. (2022) Solid epoxy for functional 3D printing with isotropic mechanical properties by material extrusion [online, pre-proof] Additive Manufacturing 102797 | sciencedirect.com. Available at:
https://www.sciencedirect.com/science/article/pii/S2214860422001981
Peerzada, M et al. (2020) Additive Manufacturing of Epoxy Resins: Materials, Methods, and Latest Trends [online] Industrial & Engineering Chemical Research 59(14) pp. 6375-6390 | pubs.acs.org. Available at:
https://pubs.acs.org/doi/10.1021/acs.iecr.9b06870
Disclaimer: The views expressed here are those of the author expressed in their private capacity and do not necessarily represent the views of AZoM.com Limited T/A AZoNetwork the owner and operator of this website. This disclaimer forms part of the Terms and conditions of use of this website.