Introduction Inorganic polymers formed from naturally occurring aluminosilicates have been termed geopolymers by Davidovits [1]. Various sources of Si and Al, generally in reactive glassy or fine grained phases, are added to concentrated alkaline solutions for dissolution and subsequent polymerisation to take place. Typical aluminosilicate precursors used are fly ash, ground blast furnace slags, and metakaolinite made by heating kaolinite at ~ 750oC for 6-24 h to render it X-ray amorphous and more reactive. The alkaline solutions are typically a mixture of hydroxide (e.g. NaOH, KOH) and silicate (Na2SiO3, K2SiO3). The solution dissolves Si and Al ions from the precursor to form Si(OH)4 and Al(OH)4 - monomers in solution [2]. The OH- ions of neighbouring molecules condense to form an oxygen bond between metal atoms and release a molecule of water and then polycondense at near ambient temperatures (20-90oC) to form a rigid polymer with interstitial unbound water [2]. The geopolymers thus consist of amorphous to semi-crystalline three dimensional aluminosilicate networks [1]. The physical behaviour of geopolymers is similar to that of Portland cement and they have been considered as a possible improvement on cement in respect of compressive strength, resistance to fire, heat and acidity, and as a medium for the encapsulation of radioactive and hazardous waste [3-10]. As for Portland cement usage, fine particles (e.g. sand) can be added to the paste to make a mortar, or aggregates can be added to make a concrete [11]. For industrial applications, the use of fly ash as a precursor gives a cost advantage over metakaolinite. However to understand the science of the polymerisation process, the use of the latter is preferred, because of the complexity of fly ash in terms of the various distinct crystalline and non-crystalline phases present . In the literature the use of different fly ashes has been published extensively; see for example, Van Jaarsveld et al. [12]. The use of several different aluminosilicate minerals has also been reported [13, 14]. Although the use of metakaolinite is limited apart from the early work by Davidovits [1] because most workers are interested in industrial applications, recently for more scientific study metakaolinite has been used on account of its near-constant composition and high reactivity with alkaline media; see for example Rahier et al. [15], Kriven et al. [16] and Barbosa et al. [17]. Several workers have studied the variation of physical and mechanical properties on composition of fly ash-based geopolymers [12, 18, 19] and similarly on metakaolinite-based geopolymers [20, 21]. The widespread use of geopolymers is currently restricted due to lack of long term durability studies, detailed scientific understanding and lack of reproducibility of raw materials [22]. One aspect of understanding the long term durability of geopolymers is the integrity of geopolymers under the influence of aqueous leaching. This is of particular interest for the use of geopolymers exposed to wet environments in applications as sewer pipes, railway sleepers, and outdoor paths for instance. Another application in which the dissolution behaviour has regulatory impact is when the geopolymer is a candidate for immobilisation of radioactive or hazardous waste. Here there are specific leach test methods which relate to disposal of solids containing toxic (e.g. TCLP [23]) or radioactive waste [24, 25], and from a practical point of view the regulatory test methodologies will give insight on how to look at dissolution behaviour in the other applications. Reduction of metal leaching in fly ash based geopolymers has been discussed previously [26, 27]. Also, the intrinsic scientific approach to mineral dissolution processes [28, 29] in aqueous media gives further clues so a valuable approach should be to study the kinetics of the transfer into solution of the principal cations as a function of solid surface area/solution volume, temperature, pH, solution composition etc. In the present work we have leached a range of metakaolinite- and fly ash-based geopolymers by immersion in deionised water (DIW) at ~ 20oC as a function of time. Since alkalis are the most leachable entities in geopolymers [30, 31] we followed the dissolution kinetics of the alkalis using ion-selective electrodes (ISE). The PCT-B test [24] at 90oC for immobilisation of high-level nuclear waste in borosilicate glass was also used for comparative purposes. Experimental Procedure Sample Preparation Metakaolinite was prepared by heating kaolinite for 15 h in air at 750oC (see Table 1). A series of metakaolinite geopolymers was made by varying the Si/Al molar ratio from 1.0-3.0 and the (Na or K)/Al ratio from 0.8-1.0. Samples in which the Si/Al ratio was 2 or less were made by mixing metakaolinite with sodium silicate solution D (see Table 1). For example a 20 g batch having Si/Al = 2 and Na/Al = 1 was made by adding 6.96 g metakaolinite to 13.04 g sodium silicate solution D. This was mixed by hand for 5 min to make a thick slurry. The H2O/Na molar ratio was ~ 7 but some compositions required more water to render them workable, up to a molar ratio of ~ 10. The slurry was poured into a 40 mm internal diameter polycarbonate container and sealed with a screw top lid. It was de-aired by holding it for 5 min on a vibrating table. Samples were cured for 2 h at ambient followed by 24 h at 65oC. After cooling to ambient the lid was opened after 5 days and the sample removed on the 7th day. In the first instance, to obtain the required composition in samples containing molar ratios of Si/Al ≥ 2, additional (fumed) silica was mixed with the powders and then added to the solution, together with any necessary water. Table 1. Precursors used to make fly ash and metakaolinite geopolymers. | NaOH | Ajax FineChem Ltd., Australia | Sodium silicate1 | Type D, PQ Corporation, Ltd., Australia | Kaolinite2 | Kingwhite80, Unimin Australia Ltd. | Fumed silica3 | X50, Degussa Ltd., Germany | Water | Deionised water | Potassium silicate4 | Kasil 1552, PQ Corporation, Australia | KOH | Aldrich Chemical Co., USA | 1. Na2O: 14.7; SiO2: 29.4; H2O: 55.9 (mass%) 2. Kaolinite heated to 750oC for 15 h in air to form metakaolinite (Al2O3.2SiO2). The XRD analysis showed an amorphous phase with trace amounts of anatase. The clay contained ~ 1 mass% quartz, TiO2 and Fe2O3 according to the supplier. 3. Fumed silica was X-ray amorphous. 4. K2O: 21.2; SiO2: 32.0; H2O: 46.8 (mass%). Material Preparation Geopolymers were also made using Class F fly ash supplied by Cement Australia Pty. Ltd, NSW, Australia and originally from the Gladstone power station in Queensland. The X-ray fluorescence (XRF) analysis as given by the supplier is listed in Table 2 and our X-ray diffraction (XRD) analysis (see below for details) showed mainly an amorphous phase plus mullite, quartz, hematite and iron silicate. From scanning electron microscopy (SEM, see below) it was possible to deduce the approximate compositions as (in vol%) quartz (20), mullite (20), hematite (5) iron silicate (2) and the balance as an amorphous aluminosilicate phase. By using the precursors listed in Table 1 a range of fly ash-based compositions was made with Si/Al molar ratios from 1.5-4.0 and Na/Al ratios from 0.6-1.4. For example the Si/Al = 3 and Na/Al = 1.4 geopolymer batch of ~ 25 g was made by dissolving 3 g NaOH in 8 g DIW and adding pre-mixed 10 g of flyash and 5 g fumed silica, followed by hand mixing as above. Some compositions required additional water to make a workable paste and the H2O/Na molar ratio was maintained between 7-10. Table 2. XRF analysis of Class F (Gladstone) fly ash as expressed as oxide mass%. | | | | | | | | | | | | 4.7 | 48.3 | 28.2 | 11.2 | 1.6 | 0.3 | 0.2 | 0.7 | 1.5 | 0.9 | 0.2 | 1.9 | The metakaolinite geopolymers had bulk densities of 1.4-1.7 g/cm3 and open porosities of 10-25% [29]. The fly ash geopolymers had bulk densities of 1.8-1.9 g/cm3 and open porosities of 1-7% [29]. The final cast samples were all approximately 40 mm in diameter by 10 mm high, except that the geopolymers with Si/Al > 2.5 displayed significant diametral contraction (~ 30%) on solidification. Subsequently six samples, both fly ash-based and metakaolinite-based geopolymers, Si/Al > 2.5 - 4 were fabricated by dissolving the silica in alkali solutions as far as possible by heating at 75oC overnight prior to mixing with metakaolinite or fly ash followed by curing. Phase Analysis All the finely ground dried samples were analysed by XRD (Model D500, Siemens, Karlsruhe, Germany, using CoKα radiation). Selected samples were mounted in epoxy resin, cross sectioned, and polished to a 0.25 μm diamond finish and examined by scanning electron microscopy (SEM: Model 6400, JEOL, Tokyo, Japan) operated at 15 kV and fitted with an X-ray microanalysis system (EDS: Model: Voyager IV, Tracor Northern, Middleton, WI, USA). Leach Testing ISE Dissolution Experiments Experiments on metakaolinite geopolymers only were conducted with Radiometer Analytical equipment: double-junction Ag/AgCl reference electrodes and either a sodium (ISE21Na) or potassium (ISE25K) electrode in conjunction with a PHM250 Ion Analyser. For both the Na and K electrodes, calibration was conducted at ambient temperature with three 20 mL standards to which 1 mL of 0.01 M BaCl2 as an ionic strength adjustment buffer (ISAB) was added. DIW was used in the preparation of the standards as well as the ISAB solutions. The standards used to calibrate the analyser for Na+ consisted of NaCl solutions of 0.01 M, 0.05 M and 0.1 M concentration and for K+ were KCl solutions of similar concentration. The inner reservoir of the Na reference electrode was filled with a saturated KCl solution, while the K reference electrode was filled by a saturated NaCl solution. The outer reservoir was filled with the ISAB. The Na and K leach tests were each conducted using 200 mL of deionised water in a glass beaker that was held at 22.5ºC in a water bath. A roughly cuboid-shaped sample of geopolymer produced by judicious fracture and weighing ~ 1 g was used in each dissolution test and its exact mass was recorded before it was placed in the beaker and the data logging by the Ion Analyser started. The geometrical surface area/water volume was ~ 0.02 cm-1. Parafilm® M barrier film was then placed over the top of the beaker in between the protruding electrodes, thermometer and stirrer to prevent water evaporation. The tests were generally left to run over 1-2 days. The amount of ISAB added to the DIW was chosen to give the same concentration of BaCl2 as present in the calibration standards. PCT-B Tests All the fly ash geopolymers and two metakaolinite geopolymers were also leached, closely following the PCT-B test [24] protocol in which the geometrical surface area/water volume was ~ 10 cm-1. One g aliquots of crushed samples of size fraction 75-150 μm were washed with non-polar cyclohexane (rather than water as in the protocol) to remove adhering fines as far as possible and leached in sealed Teflon containers with 10 mL of deionised water maintained at 90oC for 7 days. Tests were carried out in triplicate and averages are reported. The leachates were analysed by ICP-OES (Perkin-Elmer Optima 3000DV, USA). Unacidified leachates were analysed for Si,4+ while the acidified leachates were analysed for Al3+ and either Na+ or K+. The two metakaolinite geopolymers were also tested after heating to 300oC to almost completely dehydrate them (necessary in radioactive waste applications to prevent the buildup of radiolytic H2), but without producing any observable structural changes [32]. The fly ash geopolymers were tested without heating and after heating to 900oC for 2 h. The reason for heating was to form the silicate glass and crystalline nepheline as this assemblage was expected to be more leach resistant than the unheated samples, especially because of the disappearance of open porosity [32]. To study the effect of leaching for up to 90 days under the PCT-B protocol a Na-based metakaolinite geopolymer with 1 mass% Fe and Ca added as the hydroxides prepared in a previous work [30] was used in the present work. Results and Discussion Phase Analysis The XRD analyses for Na and K-based metakaolinite geopolymers showed an amorphous phase in all samples, as evidenced by a diffuse hump in the scattering pattern and peaking at a d-spacing at ~ 0.32 nm, together with weak Bragg peaks due to the quartz and anatase impurities (see above). However the two geopolymers Si/Al=1.0 (Na/Al= 0.95 and 1.0), showed only a slight hump in the X-ray scattering pattern because of the presence of peaks due to Zeolite 4A (Na92Al92Si100O384 – JCPDS no. 43-412). Zeolite 4A was also observed in the Si/Al = 1.5 (Na/Al = 0.85) sample but none of the other samples showed it. Fletcher et al. [20] observed a zeolite (JCPDS no. 31-1271) in Na metakaolinite geopolymers with Si/Al ≤ 1 and Rowles and O’Connor [21] observed slightly different zeolites (A and X) for Si/Al 1.08 -1.5. Clearly low Si/Al ratios in fly ash samples favour the formation of “zeolitic” phases, as noted by other workers (e.g. Bao et al, [31]). None of the K-based samples showed the presence of any zeolites. However the sample with Si/Al = 1, K/Al = 0.9 showed XRD evidence of the phase K2Si14O29.8H2O (JCPDS no. 46-155). The SEM images of the Na- and K-based geopolymers showed ~ 1% anatase and quartz and ~ 2 mass% of incompletely reacted metakaolinite particles. The SEM images observed here were similar to those already published [33]. The XRD analyses of the fly ash geopolymers showed a similar phase distribution for all samples; as noted by others [8, 34, 35] the major phase was an amorphous phase giving rise to the above mentioned diffuse X-ray peak. Crystalline phases were mullite, quartz and hematite, which were present in the original fly ash (see above) but the iron silicate was not detected because it only constituted ~ 2% or less. The backscattered SEM image of the fly ash sample with Si/Al= 1.5 and Na/Al = 1.0 is shown in Figure 1. 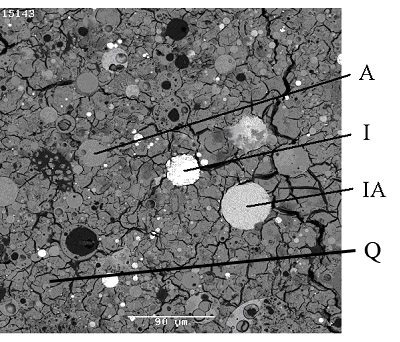 Figure 1. Backscattered SEM image of Si/Al= 1.5 and Na/Al = 1.0 geopolymer. (A = mullite, I = iron (probably iron oxide); IA = iron and Si (probably iron silicate); Q = quartz; cenospheres are unreacted fly ash). (Scale bar = 90 μm). ISE Leach Experiments The Na+ concentrations determined as a function of exposure time to DIW are plotted in Figure 2. Similar plots for K+ concentration derived from the K-based geopolymers are shown in Figure 3. 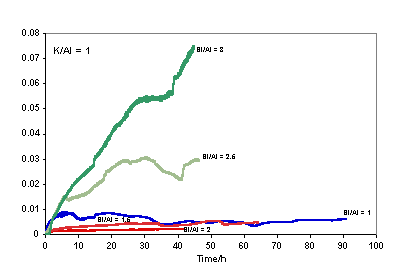 Figure 2. Leach data comparison (Mol/L) for Na-Geopolymers with Na/Al = 1. 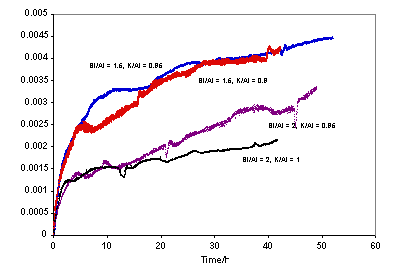 Figure 3. Leach data comparison (Mol/L) for K-Geopolymers with K/Al = 1. All the samples with Na/Al = 1 disintegrated to fine powders during leaching apart from those with Si/Al = 2 and Si/Al = 3. For the Si/Al = 1 sample, the increase in ion concentration of the leachate at the early stages of leaching appeared to follow the accelerated leaching model of Jantzen and Pareizs [36], with an initial fast rate followed by a period of steady-state leaching, after which the leach rate appears to revert to the initial rate (Figure 2). One possibility to explain the first stages of the curve is that the sample disintegrates quickly in water, giving rise to rapid transfer of the alkali-rich pore water to the solution; once this is completed, further leaching of alkali would come from breakdown of the framework, which would likely be slower than the transfer of pore water. The reason for the subsequent speeding up of the alkali leach rate is not known. Of the K/Al = 1 samples, the geopolymers with Si/Al = 1.5 and 2 were the only samples to have remained intact throughout the duration of the leaching experiment and these naturally exhibited the lowest leach rates (Figure 3). The K-based geopolymers appeared to be approximately as durable as their Na counterparts, on the basis of molar release rates. Since the curves obtained for the geopolymers of K/Al = 1, Si/Al = 1.5 and 2 appeared to exhibit fairly similar leaching behaviour (i.e. possessed concentration curves of similar shape and magnitude), it was decided to then test these two latter Si/Al ratios with somewhat lower K/Al ratios. Figure 4 showed that lowering the K/Al ratio from 1.0 to 0.9 produced higher leach rates. 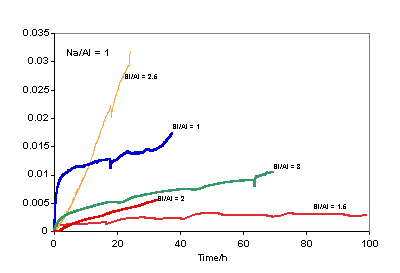 Figure 4. Leach data comparison (Mol/L) for K-geopolymers with Si/Al = 1.5 and Si/Al = 2. Similar to the leach curves of the geopolymer of Si/Al = 1.5, K/Al = 1, shown in Figure 3, the Si/Al =2, K/Al = 0.95 sample also exhibited significant fluctuations in leachate concentration with time (after about 37 h). When the raw concentration values recorded by the data logger were plotted along with the recorded temperature for each reading, the results revealed the strong influence of temperature (even a change of 0.5oC) had on the concentration read by the apparatus once the initial rapid “forward rate” of leaching began to give way to steady-state leaching. One possibility for the cause of the sensitivity of the measured concentration to temperature fluctuations is the interaction of ion species in the leachate solution with possible precipitated secondary phases. It was observed for both the Na- and K-based geopolymers that leaching resulted in the formation of a white powder on the surface of the geopolymer, but this occurred to a much lesser extent in the K-geopolymers. This precipitate was collected from one of the leached K-based geopolymers as well as from a leached Na-based geopolymer and XRD analysis showed it to be BaCO3. Also the EDS analysis of these precipitate regions of the geopolymer revealed the phase to be predominantly comprised of barium. BaCO3 possesses a very low room temperature solubility of 0.002 g in 100 g water [37], and the carbonate would have originated in the geopolymer from the absorption of carbon dioxide by the alkali hydroxide/silicate solutions used during geopolymer synthesis. ICP-OES Analysis Although efforts were made to allow the ISE measurements to yield absolute alkali concentrations, it was clear from the above that there were sources of potential error, so in new experiments nominally reproducing the methodology in the ISE experiments, absolute elemental alkali releases were also measured by ICP-OES analysis after 20 h exposure to DIW. The elemental ICP-OES analyses are listed in Table 3 for Na- and K-geopolymers of Na or K/Al = 1. Comparison of the ISE and ICP alkali leaching results showed better than 30% agreement for the 20 h results, which is very reasonable given uncertainties in comparative surface areas of the imperfectly cuboidal samples, not to mention their tendency to disintegrate. The agreement for the K-based samples was better than 50%, except for the Si/Al sample in which the disagreement was a factor of 3. Here there could have been sample inhomogeneity, given that the sample was prepared by a non-ideal method (see below). In converting the ICP-OES concentration data to a percentage of Na leached from the samples, the highest value was ~ 82%, which occurred (as expected from the ISE experiments) in the leachate sampled at 20 h from the testing of the sample having Si/Al = 2.5 and Na/Al = 1. As with the Na-geopolymers, converting the K+ ppm concentration values to % K values for the ICP-OES data showed a maximum value of 85% in the geopolymer of Si/Al = 2.5, K/Al = 1. In summary, the overall agreement between concentration results obtained with the ISE and the ICP-OES was fair. The geopolymers having Si/Al = 1.5 and 2.0 for Na at 20 h showed the best correlation between values obtained with each instrument. This might be because the concentrations were relatively small, so the errors in the ISE method were limited. Leach Rates From the data in Figures 2-4, leach rates for the first 2 days, normalised in terms of fractional extractions per unit geometrical surface area (of the unleached sample), were calculated as ranging from hundreds of g/(m2 day) for the alkali ions in the samples that disintegrated to tens of g/(m2 day) for those that did not. The latter values were in broad agreement with those derived from a sample which maintained its integrity upon being leached in water at room temperature [30]. In terms of leaching depth, 1 g/(m2 day) corresponds to ~ 0.7 μm/day for a sample density of ~ 1.5 g/cm3. In measurements of the compressive strength of geopolymers, it is important to pre-dissolve fumed silica [21] in the caustic alkali solution as far as possible (see above). It was not possible to quantitatively detect the free after curing silica by XRD because it was amorphous. If the silica was not part of the structure then there would be fewer structural units in the matrix and hence Na would be in excess to charge balance requirements to the geopolymer network, thus more Na would be in the pore water and would easily leach out, as seen here. The Si which was not incorporated into the 3-dimensional geopolymer network would also be expected to be somewhat soluble in the (alkaline) pore water, giving rise to the observed high Si concentrations in the leachates for the Si/Al = 2.5 and 3 samples in Table 3. Table 3. Concentration data (ppm) after 20 h for undiluted leachate by ICP-OES for Na and K-based metakaolinite geopolymers of Na or K = 1 (For Na and K, values in mMol/L are listed in brackets for comparison with ISE values). | 1 | Al | 1.5 | 19 | | K | - | 247 (6.3) | | Na | 184 (8.0) | - | | Si | 62 | 6.0 | | | | | 1.5 | Al | 5. | <0.5 | | K | - | 68 (1.7) | | Na | 53 (2.3) | - | | Si | 3.0 | <0.5 | | | | | 2 | Al | 0.5 | <0.5 | | K | <0.5 | 74 (1.9) | | Na | 94 (4.1) | - | | Si | 5.0 | <0.5 | | | | | 2.5 | Al | 28 | 29 | | K | - | 680 (17.4) | | Na | 364 (15.8) | - | | Si | 530 | 580 | | | | | 3 | Al | 10.0 | 7.0 | | K | - | 560 (14.4) | | Na | 307 (13.3) | - | | Si | 466 | 590 | To explore the effect of pre-dissolution of fumed silica in alkali solution, six samples with high Si/Al ratios that necessitated the use of fumed silica and NaOH (rather than solution D) were made and their ICP-OES releases in tests carried out in the same way as the ISE experiments are listed in Table 4. It is seen that Al, Si and principal alkali releases for the equivalent compositions made without the silica predigestion (Si/Al ratios of 2.5 and 3) as listed in Table 3 were substantially higher, confirming the view that pre-dissolution of the silica is necessary for lower leach rates. The SEM image (Figure 5) of the Si/Al = 3, Na/Al = 1 sample without pre-dissolution of the silica shows some undissolved silica particles, probably agglomerates of fumed silica particles. However what was surprising was that the overall alkali leach rates of the metakaolinite (and the fly ash samples) were around a factor of 5 lower than those of nominally equivalent samples made without fumed silica, and this is not understood but will be studied in further work. 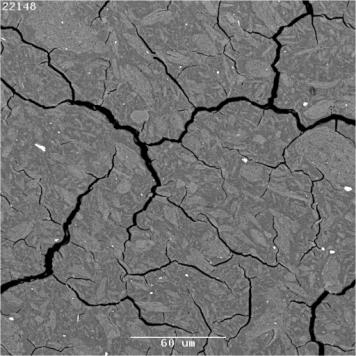 Figure 5. SEM image of Si/Al = 3, Na/Al = 1 geopolymer prepared without the pre-dissolution of fumed silica (the silica and unreacted MK have a similar contrast; anatase is from the original clay). (Scale bar = 60 μm). Table 4. Concentration data (ppm) after 20 h for undiluted leachate by ICP-OES for FAGPs and MKGPs (Na or K/Al =1) (For Na and K, values in mMol/L are listed in brackets for comparison with ISE values). | | FAGP | | | 4 | | Al | 0.5 | | | Na | 19 (0.8) | | | Si | 23 | | | | | 3 | | Al | <0.5 | | | Na | 4.5 (0.2) | | | Si | 2.5 | | MKGP | | | | Na | | | 3 | | Al | 1.0 | | | Na | 14 (0.6) | | | Si | 22 | | | | | 2.5 | | Al | 0.5 | | | Na | 12 (0.5) | | | Si | 14 | | K | | | 3 | | Al | 0.5 | | | K | 15 (0.4) | | | Si | 14 | | | | | 2.5 | | Al | 2.0 | | | K | 41 (1.1) | | | Si | 41 | PCT-B Leach Test PCT-B tests were also of interest both in the context of the effects of geometrical surface area/volume on aqueous dissolution of the geopolymers as well as for nuclear waste immobilisation [30, 31, 38]. The PCT-B leach results for the fly ash geopolymers are listed in Table 5, given as normalised elemental releases for Na, Al and Si. The normalised elemental extraction in g/L is calculated by dividing the measured elemental extraction (g/L) in the solution by the elemental concentration. For complete dissolution the value would correspond to 100 g/L. However the leach rates require separate calculation [38]. For unheated and heated samples the Al release in these tests is low compared to the releases of Na, K and Si. For the unheated geopolymers Na, K and Si releases are high by factors of 1-10 or more compared to candidate glasses for high level nuclear waste immobilisation [31] and also the geopolymers after conversion to glass-ceramics by heating at 900oC. Also at high Si/Al geopolymer ratios the elemental extractions are comparatively very high; in these mixtures fumed silica was added without predigestion with the alkali. Table 5. Normalised releases for Na, Al and Si in fly ash geopolymers in PCT tests. | | | Na | Al | Si | Na | Al | Si | 1.5 | 1.0 | 26 | 0.03 | 7.4 | 3.5 | 0.06 | 1.7 | 2 | 0.6 | 21 | 0.04 | 4.1 | 1.1 | 0.07 | 0.3 | 2 | 1.0 | 29 | 0.12 | 8.9 | 1.5 | 0.19 | 0.4 | 2 | 1.4 | 38 | 0.03 | 16 | 2.4 | 0.62 | 0.2 | 2.5 | 0.6 | 53 | 0.03 | 23 | 1.1 | 0.03 | 0.3 | 2.5 | 1.0 | 56 | 0.07 | 34 | 1.0 | 0.08 | 0.2 | 2.5 | 1.4 | 38 | 0.07 | 16 | 1.0 | 0.19 | 0.4 | 3.0 | 0.6 | 60 | 0.04 | 24.0 | 1.6 | 0.03 | 0.3 | 3.0 | 1.0 | 67 | 0.18 | 61 | 1.4 | 0.06 | 0.2 | 3.0 | 1.4 | 43 | 0.09 | 37 | 0.8 | 0.13 | 0.6 | 4.0 | 1.0 | 63 | 0.12 | 51 | 2.7 | 0.14 | 0.8 | In previously reported work [38], the normalised Na leach extraction from an unheated fly ash-based geopolymer was 15-16 g/L which was less than that was observed here (Table 5). In the previously-reported work [38] the molar ratios were Si/Al = 2.18 and Na/Al = 0.65, with the sample not containing any extra added silica. The normalised Si leach rate was only 0.2 g/L, much lower than any of the results given in Table 5 for the unheated samples. After the geopolymers were heated to 900oC, the leach rates were considerably reduced. The reason for this is that at 900oC the material is partly vitreous, much less porous and the Na is held more strongly in the glassy and crystalline (nepheline) phase. These results are similar to those on another fly ash geopolymer which was heated to 900oC for 2 h [32]. The PCT-B test was carried out on the metakaolinite-based geopolymer with Si/Al = 2, Na or K = 1 for comparison with sample on which the ISE measurements were made and the results are listed in Table 6. The results are fairly comparable, although a factor of 2-3 higher for alkali extractions, to those reported earlier for metakaolinite-based samples containing Cs and Sr [38], which have given the best results reported for geopolymers within the framework of the test protocol. Table 6. PCT-B test summary for Na- and K-based metakaolinite geopolymers (Si/Al = 2, Na or K/Al = 1). | Na | 21 | - | K | - | 14 | Si | 2.3 | 0.7 | Al | 0.2 | 0.2 | In these tests, the Si extractions were much lower for metakaolinite-based geopolymers than those for the corresponding fly ash-based geopolymers (see Table 3) and the K-based geopolymer has a somewhat lower Si leach rate than that for the Na-based geopolymer. Here again leach rates are high for Si/Al = 2.5 and 3, similar to those of the fly ash-based geopolymers (Table 6). Extended PCT tests for 28 and 90 days (in addition to 1- and 7- day tests) were carried out on a metakaolinite-based geopolymer [30] specifically to look at the possibility of forming crystalline secondary alteration phases, as well as to look at the long-term dissolution. The basic result for Na was that the releases at 28 and 90 days were not greatly different to those after 1 and 7 days (Table 7), and crystalline alteration phases could not be detected by either XRD or SEM examinations. It was concluded that the relatively low elemental releases, compared to those observed in dilute solutions at ambient temperatures, were due to the samples essentially equilibrating with the solutions at ~ 1 day and beyond. Conclusions It was confirmed that the most leachable species in water solutions derived from correctly made geopolymers exposed to deionised water are alkalis. Leach rates at room temperature in dilute solutions over 1-2 day periods derived from Na or K ion-specific electrode studies were in broad agreement with values obtained previously (tens of g/(m2 day) in dilute solutions, using geometric surface areas). The leaching of all elements generally increased with time but the detailed kinetics were complicated by the less durable samples’ tendency to disintegrate on exposure to water. It is not yet clear whether the predominant dissolution mechanism, apart from increased surface area from disintegration, is diffusion to the leaching solution of alkali-rich pore water or dissolution of alkalis forming part of the geopolymer network. However, disintegration of the samples in water would imply breakdown or incompleteness of the network rather than mere transference of pore water. Experiments are planned to prepare partly deuterated samples to bear further upon this question. Alkali leaching rates derived from PCT-tests in deionised water at 90oC in which the sample surface areas/water volume are relatively high are only ~ 1 g/(m2 day) or less and the disparity between these results and those obtained in dilute solutions at ambient temperatures appears to derive from essential equilibration between leachate and solid in long-term PCT studies. No significant crystalline alteration of the geopolymers was seen in PCT tests lasting up to 90 days. The most leach-resistant compositions of both metakaolinite- and fly ash-based materials are centred around alkali/Al ~ 1 molar ratios. Metakaolinite-based samples on the whole were less leachable in deionised water than those derived from fly ash. It was confirmed that high-Si samples need pre-digestion of the Si to minimise leachability. However the improved durability of samples made from fumed SiO2 as against conmmercial silicate solutions was surprising and needs further investigation of itself and also to define the Si/Al molar ratio of geopolymers with maximum leach resistance in dilute aqueous solutions. Heating the geopolymers to ~ 900oC considerably improves their leach resistance, because of crystallisation of nepheline and severe reduction of open porosity. Acknowledgements This work was conducted under the auspices of the Cooperative Research Centre for Sustainable Resource Processing. We thank J. Davis (SEM), P. Yee (ICP OES) and R. Wong (ISE) for technical assistance. References 1. J. Davidovits, “Geopolymers: Inorganic Polymeric New Materials”, J. Therm. Anal., Vol. 37, 1633-1656, 1991. 2. P. G. McCormick and J. T. Gourley, “Inorganic Polymers – A New Material for the New Millenium”, Materials Australia, Vol. 23, 16-18, 2000. 3. J. Davidovits, “Geopolymers: Man Made Rock Geosynthesis and the Resulting Development of Very Early High Strength Cement”, J. Mat. Edu., Vol. 16, 91-139, 1994. 4. J. Davidovits, ”Chemistry of Geopolymeric Systems, Terminology”, Geopolymere ’99, Geopolymer International Conference, Proceedings, 30 June – 2 July, 1999, pp. 9-39, Saint-Quentin, France. Edited by J. Davidovits, R. Davidovits and C. James, Institute Geopolymere, Saint Quentin, France (1999). 5. A. Allahverdi and F. Skvara, “Nitric Acid Attack on Hardened Paste of Geopolymeric Cements”, Ceramics-Silikatay, Vol. 45, [3] 81-88, 2001. 6. M. Y. Khalil and E. Merz, “Immobilization of Intermediate-level Wastes in Geopolymers”, J. Nucl. Mater., Vol. 211, 141-148, 1994. 7. A. P. Zosin, T. I. Priimak and Kh. B. Avsaragov, “Geopolymer Materials Based on Magnesia-Iron Slags for Normalization and Storage of Radioactive Wastes”, Atomic Energy, Vol. 85, 510-514, 1998. 8. D. S. Perera, E. R. Vance, Z. Aly, K. S. Finnie, J. V. Hanna, C. L. Nicholson, R. L. Trautman and M. W. A. Stewart, “Characterisation of Geopolymers for the Immobilisation of Intermediate Level Waste”, Proceedings of the 3rd International conference on environmental remediation and radioactive waste management, ICEM’03, September 21-25, 2003, Oxford, England, Laser Options Inc., Tucson, USA, 2004, CD, paper no. 4589. 9. M. Palacios and A. Palomo, “Alkali Activated Flyash Matrices for Lead Immobilisation: A comparison of different leaching tests”, Adv. Cement Res., Vol. 16, 137-144, 2004. 10. D S Perera, Z. Aly, E R Vance and M. Mizumo, “Immobilisation of Pb in a Geopolymer Matrix”, J. Am Ceram Soc., Vol. 88, 2586-2588, 2005. 11. D. Hardjito, S. E. Wallah and B. V. Rangan, “Study on Engineering Properties of Fly Ash Based Geopolymer Concrete”, J. Aust. Ceram. Soc., Vol. 38, 44-47, 2002. 12. J. G. S. van Jaarsveld, J. S. J. van Deventer and G. C. Lukey, “The Characterisation of Source Materials in Fly Ash-Based Geopolymers”, Mater. Lett., Vol. 57, 1272-1280, 2003. 13. H. Xu and J. S. J. Van Deventer, “The Geopolymerisation of Alumino-silicate Minerals”, Int. J. Miner. Proc., Vol. 59, 247-266, 2000. 14. J. G. S. van Jaarsveld, J. S. J. van Deventer and G. C. Lukey, “A Compartive Study of Kaolinite Versus Metakaolinite in Fly Ash Based Geopolymers Containing Immobilized Metals”, Chemical Engineering Communications, Vol. 191, 631-649, 2004. 15. H. Rahier, B. Van Mele and J. Wastiels, “Low Temperature Synthesized, Aluminosilicate Glasses. Part I. Low-Temperature Reaction Stoichiometry and Structure of a Model Compound”, J. Mater. Sci., Vol. 37, 80-85, 1996. 16. W. M. Kriven, J. L. Bell and M. Gordon, “Microstructure and Microchemistry of Fully-Reacted Geopolymer Matrix Composites”, Ceram. Trans., Vol. 153, 227-250, 2003. 17. V. F. F. Barbosa, K. J. D. MacKenzie and C. Thaumaturgo, “Synthesis and Characterisation of Materials Based on Inorganic Polymers of Alumina and Silica: Sodium Polysialate Polymers”, Int. J. Inorg. Mat., Vol. 2, 309-317, 2000. 18. A. Palomo, P. F. G. Banfill, A. Fernandez-Jimenez and D. S. Swift, “Properties of Alkali-Activated Fly Ashes Determined from Rheological Measurements”, Adv. Cem.Res., Vol. 17, 143-151, 2005. 19. M. Stevson and K. Sagoe-Crentsil, “Relationship Between Composition, Structure and Strength of Inorganic Polymers, Part 2: Fly Ash-Derived Inorganic Polymers”, J. Mater. Sci., Vol. 40, 4247-4259, 2005. 20. R. A. Fletcher, K. J. D. MacKenzie, C. L. Nicholson and S. Shimada, “The Composition Range of Aluminosilicate Geopolymers”, J. Euro. Ceram. Soc., Vol. 25, 1471-1477, 2005. 21. M. Rowles and B. O’Connor, “Chemical Optimisation of the Compressive Strength of Aluminosilicate Geopolymers Synthesised by Sodium Silicate Activation of Metakaolinite”, J. Mater. Chem., Vol. 13, 1161-1165, 2003. 22. G. C. Lukey and J. S. J. van Deventer, “Geopolymer Technology: the Formation of Cost-Competitive Construction Materials from Coal Ash and Blast Furnace Slag”, Proceedings of the GGC 2005 (International Workshop on Geopolymers and Geopolymer Concrete), September, 28-29, 2005, Perth, Australia. CD ROM, qGGC2005.pdf 23. “Toxicity Characterisation Leaching Procedure (TCLP)”, EPA Method 1311, United States Environmental Protection Agency Publication SW-846, Cincinnati, OH, 1999. 24. “Standard Test Methods for Determining Chemical Durability of Nuclear, Hazardous, and Mixed Waste Glasses and Multiphase Glass Ceramics:The Product Consistency Test”, ASTM Committee, C26 (2000). 25. “Measurement of Leachability of Solidified Low-Level Radioactive Wastes by a Short-Term Test Procedure”, ANSI/ANS-16.1-2003. American Nuclear Society, Illinois, USA. 26. P. Banowski, L. Zou and L. Hodges, “Reduction of Metal Leaching in Brown Coal Fly Ash Using Geopolymers”, J. Hazardous Mater., Vol. 114, 59-67, 2000. 27. P. Banowski, L. Zou and L. Hodges, “Using Inorganic Polymer to Reduce Leach Rates of Metals from Brown Coal Fly Ash”, Miner. Eng., Vol. 17, 159-166, 2004. 28. E. H. Oelkers and J. Schott, “Experimental Study of Anorthite Dissolution and the Relative Mechanism of Feldspar Hydrolysis”, Geochimica et Cosmochimica Acta, Vol. 59, 5039-5053, 1995. 29. S. R. Gislason and E. H. Oelkers, “Mechanism, Rates and Consequences of Basaltic Glass Dissolution:II. An Experimental Study of the Dissolution Rates of Basaltic Glass as a Function of pH and Temperature”, Geochimica et Cosmochimica Acta, Vol. 67, 3817-3832, 2003. 30. E. R. Vance, D. S. Perera, Z. Aly, M. Blackford, Y. Zhang, M. Rowles, J. V. Hanna, K. J. Pike, J. Davis and O. Uchida, “Solid State Chemistry Phenomena in Geopolymers with Si/Al ~ 2”, Proceedings of the GGC 2005 (International Workshop on Geopolymers and Geopolymer Concrete), September, 28-29, 2005, Perth, Australia. CD ROM, nGGC2005.pdf. 31. Y. Bao, M. W. Grutzeck and C. M. Jantzen, “Preparation and Properties of Hydroceramic Waste Forms Made with Simulated Hanford Low-Activity Waste”, J. Amer. Ceram. Soc., Vol. 88, 3287-3302, 2005. 32. D. S. Perera, E. R. Vance, D. J. Cassidy, M. G. Blackford, J. V. Hanna, R. L. Trautman and C. L. Nicholson,, "The Effect of Heat on Geopolymers Made Using Fly Ash and Metakaolinite", Ceram. Trans.,Vol. 165, 87-94, 2004. 33. M. Schmuker and K J D MacKenzie, “Microstructure of Sodium Polysialate Siloxo Geopolymer”, Ceram. Int., Vol. 31, 433-437, 2005. 34. A. Palomo, M. W. Grutzeck and M. T. Blanco, “Alkali-Activated Fly Ashes a Cement for the Future,” Cement Concrete Res., Vol. 29, 1323-1329, 1999. 35. A. Fernandez-Jimenez, A. Palomo and M. Criado, “Microstructure Development of Alkali-Activated Fly Ash Cement: a Descriptive Model”, Cement & Concrete, Vol. 35, 1204-1209, 2005. 36. C. M. Jantzen and J. M. Pareizs, “Glass Durability Modelling: Activated Complex Theory (ACT) and Quasi-Crystalline Structural Ratios (U),” WSRC-MS-2004-00663, Rev. 0. Westinghouse Savannah River Co., Aiken, South Carolina, USA, April, 2003. 37. G. Aylward and T. Findlay, “SI Chemical Data”, 4th Edition, John Wiley and Sons, Brisbane, 1998. 38. D. S. Perera, E. R. Vance, Z. Aly and J. Davis, “Immobilization of Cs and Sr in Geopolymers with Si/Al ~ 2”, Ceram. Trans., Vol. 176, 91-96, 2006. Contact Details |