Atomic force microscopy (AFM) is an effective technique for evaluating microscopic surface topography and material parameters of any specimen. AFM microscopes are available in different sizes and modes of operation, each with its advantages and limitations.
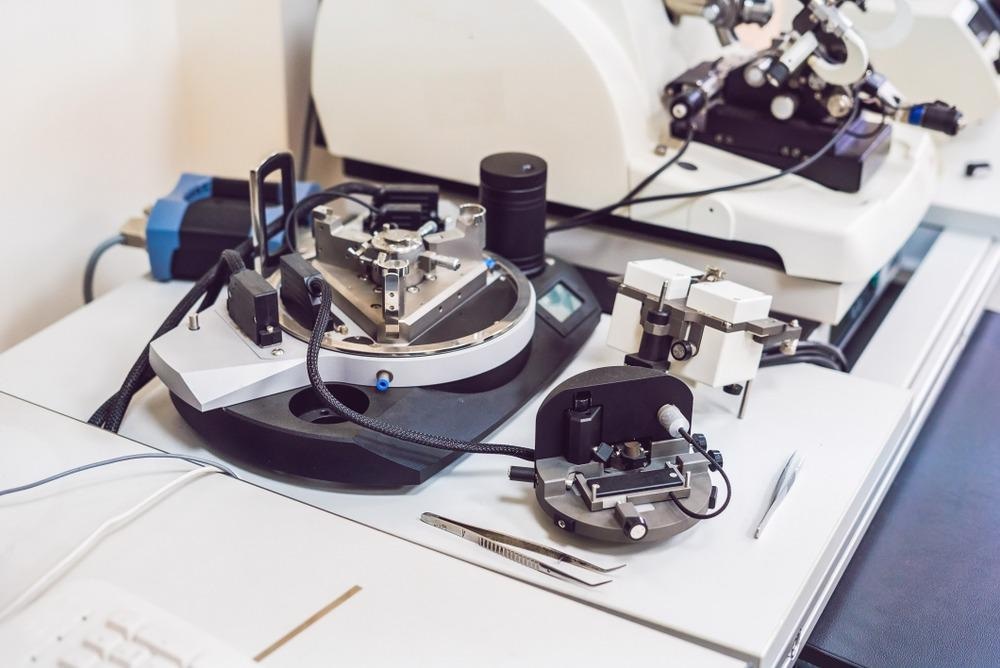
Image Credit: Elizaveta Galitckaia/Shutetrstock.com
A Brief Introduction to Atomic Force Microscopy
Atomic force microscopy is a powerful technique that has been widely used in materials research, nano-imaging, and bioimaging. It is a topographical metrology approach that is commonly utilized in imaging to acquire high-resolution images. Nanotechnology researchers are also employing it to characterize nanoparticles.
The technique images a region by influencing the interplay of pressures between a nanoscale probe and the adjacent surroundings. The ability to examine morphological regions with high signal-to-noise levels and sub-nanometer accuracy prompted the development of a number of AFM-related technologies that used a variety of devices to selectively detect contacts and regulate materials.
AFM uses a non-optical interface probing technology that is innovative specifically in the materials industry. This is based on the foundations of scanning probe microscopy, which uses a mechanical probe to examine material surface characteristics with extreme accuracy for horizontal and vertical assessments.
Working Principles of Atomic Force Microscopes
AFM microscopes work on the interface detection approach, employing an ultra-delicate tip on a microfabricated silicon sensor. This tip is utilized for imaging a sample by diagonal scanning across the exterior line by line, albeit the procedure varies greatly depending on the operating mode. Contact mode and dynamic or tapping modes are the two basic types of operating modes.
The essential idea of AFM involves the linking of the nanoscale to a tiny cantilever that functions as a spring. The contact between the tip and the exterior of the specimen results in the bending of the cantilever and the bending is sensed via a diode laser and a partitioned light detector. This bending is caused by the pressure of tip-sample contact.
Variation in Working of Contact and Tapping Mode
In contact mode, the tip is pushed on the substrate, and an electrical feedback system loop regulates the tip-sample contact intensity to maintain a consistent displacement throughout raster scanning.
Tapping mode reduces the amount of impact between the surface of the specimen and the tip in designed to safeguard both from degradation. The cantilever is made to oscillate near its resonant frequencies in this mode. The tip then glides vertically, known as a sinusoidal motion. As it approaches the sample, its mobility is diminished by strong attractive or repulsive contacts.
A feedback control system is employed in a manner similar to contact mode, except that it maintains the magnitude of this tapping movement steady rather than the nonlinear static displacement. The morphology of the material is sketched line by line as a result.
Which Materials are Used in its Construction?
To photograph the material, AFM magnifies the image and employs a cantilever composed of silicon or silicon nitride with a lower value of spring constant. Microelectromechanical systems technology is used to create AFM probes. The majority of AFM probes are constructed of silicon (Si), however, borosilicate glass and silicon nitride are also utilized.
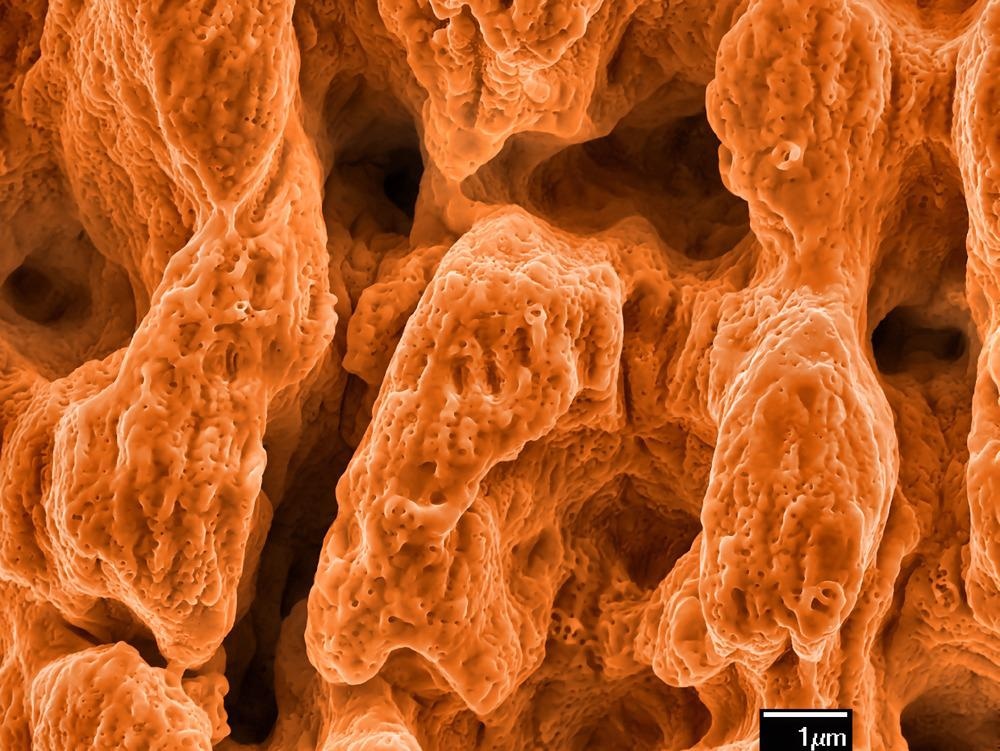
AFM image of gold surface ablated by laser pulses with scale bar. Image Credit: Georgy Shafeev/Shutterstock.com
To boost the intensity of the laser beam rebounding off the cantilever, the underside of the cantilever is frequently covered with a reflective metallic coating of a few tens of nanometers. Reflective films for silicon AFM probes are frequently made of aluminum and gold sheets. Mica and highly ordered pyrolytic graphite are most commonly utilized for AFM imaging.
Steps of Assembling an Atomic Force Microscope
There are various types of atomic force microscopes and the assembling methods for each may vary. It is advantageous here to specify a particular subtype that would present an example of the general concept of its assembly.
The keysight AFM 7500 is a famous and vastly utilized instrument. It consists of an optical column, the microscope assembly, the base plate, the AFM body, the gate, scanner, and additional components such as an LED light and Allen keys.
Initially, the base plate is set on a flat surface as irregular surfaces alter the readings. The sliding of the optical microscope assembly down the optical column is the next step in the assembly of AFM. It is then rotated to the specific position required for the operation and then an Allen key is used to tighten the screws to fix the position. It must be remembered that it shouldn’t be completely fixed so that later on a bit of rotation is possible in case of any changes.
Next, the AFM body is put on the base plate. It is adjusted vertically and laterally so that all four of its legs are inserted into the four holes of the base plate. To align and focus the microscope, the scanner is essential. It is inverted and the adjustment knob must be towards the user. It is then inserted into the body.
The levers of the scanner are rotated into their parallel position and pushed down to completely fix the scanner. Next, with the help of a lever, the optical microscope is tilted and rotated to fix it completely in position with respect to the scanner. The zoom ring on the microscope must be completely zoomed out for proper focus. This is done with the help of computer software. LED light is then inserted into the chamber of the AFM body to ensure the transmission of light.
Now, the final rotation is done and the microscope is completely fixed in position. There are two knobs for the adjustment of XY translation, and the translation process is repeated until the tip of the cantilever is visible. The focus adjustment knob is situated behind the microscope. It can be rotated to move the microscope up and down while looking at the optical view on the computer screen.
The laser alignment adjustment knob is integrated into the scanner. Next, the laser and detector are aligned, and then the AFM is ready for operation.
Future Perspective
The latest article published in the journal Metrology, Inspection, and Process Control for Semiconductor Manufacturing informs readers regarding the latest advancements in AFM technology. The new approach of miniaturizing and reconfiguring the head enables a 40x boost in performance over standard AFM systems.
Miniaturization enables many heads to operate in parallel across a wafer. When accompanied with the bandwidth enhancement, this might result in a two-order-of-magnitude improvement above typical inline AFM methods. The invention of the mini SMP-integrated head also enables embedded monitoring. When the detected tip-sample tension reaches a threshold range, quick and accurate specimen detection is achieved.
In short, AFM microscopy has emerged as a novel field for multipurpose sensing. Research all over the world is being conducted to improve its performance and efficiency, optimizing it for various industries.
More from AZoM: How is AFM Used in the Rubber Industry?
References and Further Reading
Keysight Hands-On`, 2015. Aligning the Laser on a Atomic Force Microscope. [Online]
Available at: https://www.youtube.com/watch?v=e6Ylh2jvP80&ab_channel=KeysightHands-On
van Reijzen, M. et. al. (2021, February). Recent advancements in atomic force microscopy. In Metrology, Inspection, and Process Control for Semiconductor Manufacturing XXXV. 11611. (p. 116112E). International Society for Optics and Photonics. Available at: https://doi.org/10.1117/12.2595426
KeySight, 2022. N9417S 7500 Atomic Force Microscope (AFM). [Online]
Available at: https://www.keysight.com/zz/en/support/N9417S/7500-atomic-force-microscope-afm.html
NanoWerk, 2022. Atomic Force Microscope (AFM) Manufacturers. [Online]
Available at: https://www.nanowerk.com/atomic_force_microscope_manufacturers.php
Science Direct, 2022. Atomic Force Microscope. [Online]
Available at: https://www.sciencedirect.com/topics/engineering/atomic-force-microscope
Disclaimer: The views expressed here are those of the author expressed in their private capacity and do not necessarily represent the views of AZoM.com Limited T/A AZoNetwork the owner and operator of this website. This disclaimer forms part of the Terms and conditions of use of this website.