A widely known producer of dressings, sauces, vegetable dips, herbs, and cheeses creates an estimated 75,000 gallons of wastewater each day in its manufacturing process at one of its North America sites.
Two dissolved air flotation (DAF) systems are used in the manufacturer's wastewater treatment plant. The water from the DAF units is then sent to a treatment plant for wastewater specifically, for treatment. Local discharge limits contain stringent laws that must be followed to avoid severe fines.
The organics loading and velocity of the wastewater created at this location are variable. For process management and discharge restrictions, the facility’s wastewater plant uses Biochemical Oxygen Demand (BOD) and Chemical Oxygen Demand (COD) data.
The wastewater treatment facility must adhere to the specified BOD limit of 800 lbs./day. The plant’s operators are supposed to undertake COD analysis at the start of each shift. To avoid exceeding the daily BOD discharge limit, the factory employs a COD: BOD correlation.
Furthermore, BOD analysis is carried out at a third-party local laboratory. This takes five days to complete, with additional charges.
COD analysis, on the other hand, takes much less time (2 hours), although it uses dangerous chemicals. Interferences induced by species other than organics in the sample reduce both BOD and COD accuracy. This is critical to examine to fulfill regulatory compliance.
Any delays in receiving real-time water quality data result in the facility being unable to reach its full throughput. As a result, untreated wastewater is hauled away by a third-party provider at a cost of more than $1.2 million a year.
Challenges
This food & beverage manufacturer worked with Sievers Instruments to better understand the company’s water monitoring requirements. The goals were as follows:
- More efficient capture of organics data from wastewater streams
- Enhance the wastewater treatment plant’s operational control
- Reduce the hauling cost of untreated wastewater
- Eliminate permit violations
- Process more wastewater
Exceeding the permitted limit might lead to the closure of the facility and the imposition of extra treatment requirements.
Solution
The factory required an organics monitoring solution that withstands high salt levels and FOG (fat, oils, and grease) samples. As a result, the Sievers InnovOx TOC Analyzer was chosen.
Faster analysis times for monitoring discharge limit parameters can result in a higher plant throughput since operators can make data-driven choices faster. Organics monitoring was the major metric utilized for process improvement in a three-month study conducted by the manufacturer.
TOC analysis is a reliable, precise and easy-to-use organics analysis technique that boosts confidence in process decision making. The facility can make fast modifications thanks to real-time information about upstream process changes.
The cost of garbage hauling is greatly reduced as a result of these changes. The monthly average of wastewater treated before and after utilizing the Sievers InnovOx TOC Analyzer is shown in Figure 2.
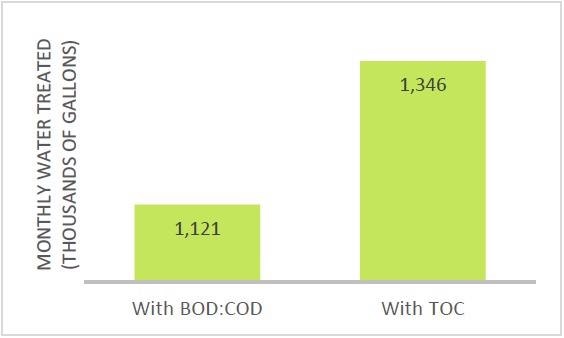
Figure 2. Increase in treated water volume using fast and accurate TOC measurements given by the Sievers InnovOx TOC Analyzer. Image Credit: Veolia Water Technologies & Solutions
Results
- The expense of hauling untreated water away was dramatically reduced, resulting in a $700,000+ yearly reduction
- TOC analysis takes about six minutes, compared to two hours for COD and five days for BOD
- The monthly wastewater treatment capacity has increased by 29%
Following the success of the Sievers InnovOx study, the manufacturer decided to utilize TOC as the principal metric for measuring organics loading from upstream food processing. Shifting from BOD: COD to TOC analysis cut down the time and expense of making efficient process modifications in half.
Conclusion
As soon as the assessment period ended, the manufacturer purchased a Sievers InnovOx ES Laboratory TOC Analyzer and installed it in its facility. The laboratory model was chosen as the best option for the plant since it allows for sampling from many locations rather than having to install several online analyzers.
The manufacturer increased the volume of wastewater treated while eliminating any regulatory problems due to TOC monitoring using the Sievers InnovOx TOC Analyzer. The wastewater facility was able to cut water shipping expenses by increasing the amount of water that could be processed on-site.
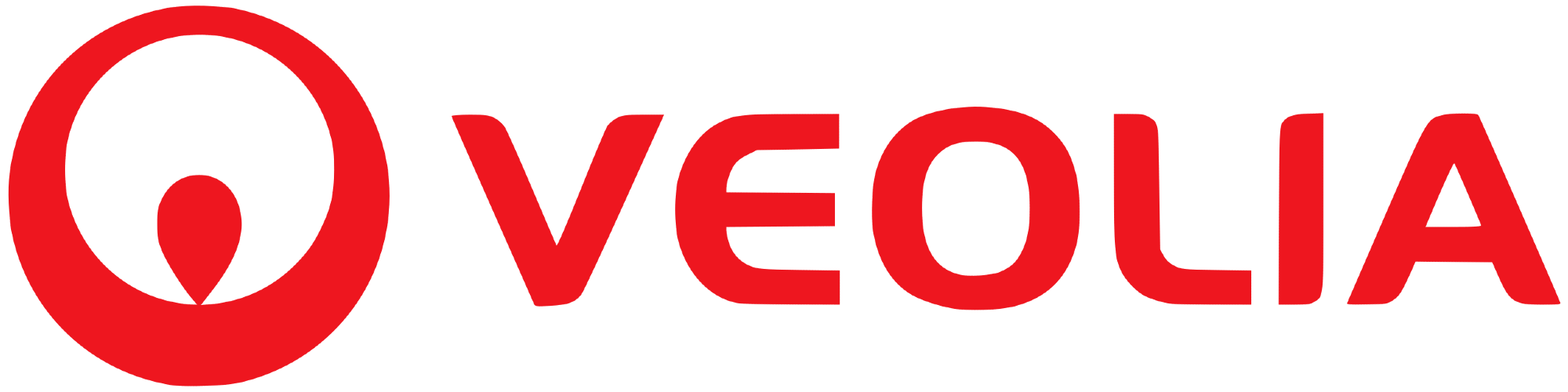
This information has been sourced, reviewed and adapted from materials provided by Veolia Water Technologies & Solutions.
For more information on this source, please visit Veolia Water Technologies & Solutions