Alloys are materials that are made by combining two or more materials to obtain a composite that possesses superior properties than any of its components on its own. The properties of alloys can be further improved through heat treatment to meet various needs. In this article, we will look at how heat-treating AerMet100, a steel alloy, impacts its properties.
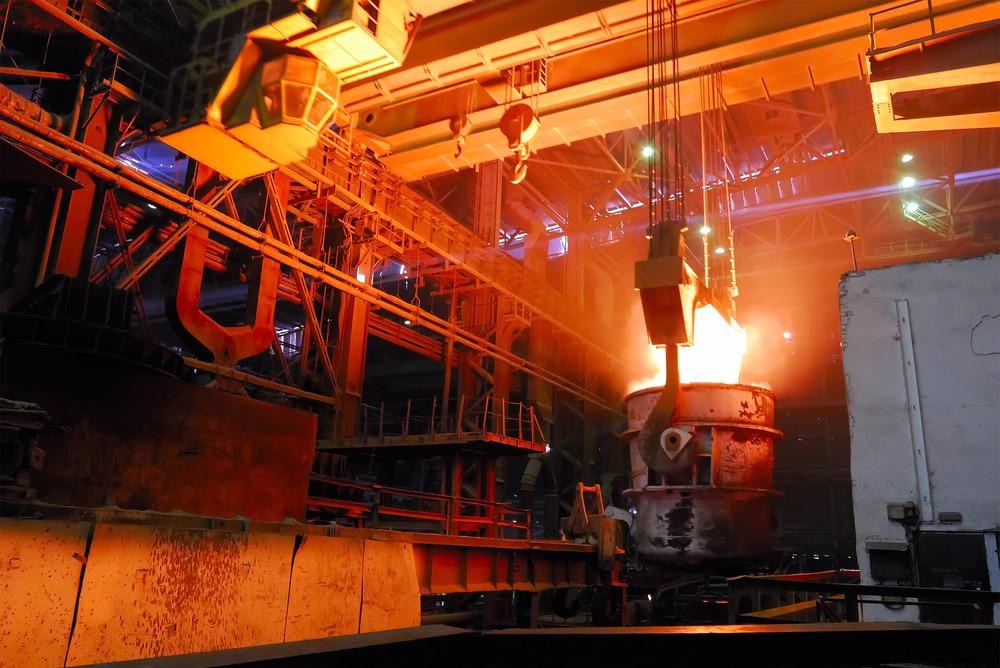
Image Credit: makspogonii/Shutterstock.com
Materials are typically mined from their ores and refined before being used in a variety of applications. The stages from mining to purification are often tedious and expensive, such that the finished products in their pure state become expensive as well.
Many technologies are emerging that require materials with very specific properties. Hence, the use of pure materials becomes inherently limited because of their intrinsic properties—they are generally softer, can be easily corroded, and above all are not cost-effective for a wide range of applications.
An alternative solution to these challenges is the development of alloys.
Why are Alloys Used?
During the process of synthesizing alloys, all components are initially melted and mixed. As mixing proceeds, contaminants are removed while the product is also protected from oxidation. Industrial manufacturing of alloys uses arc melting and induction to facilitate the melting and mixing process.
AerMet100 alloy is one of such alloys made from steel, cobalt, and nickel. Often added are also chromium and molybdenum. The combination of these materials confers fracture toughness and ductility, superior hardness, resistance to corrosion cracking, and high tensile strength.
AerMet100 Steel and Processing
This alloy is produced by the Carpenter technology corporation and is well known for its ultra-high-strength,
According to a Service Steel Aerospace Corp. fact sheet, tensile strength and ductility make this alloy a candidate for applications such as landing gear, armor, fasteners, actuators, ordnance, jet engine shafts, driveshafts, structural tubing, etc. It can function properly in temperatures as high as 800° F (427° C).
The need for materials is increasing and the shapes of parts are becoming very complex such that traditional forging methods are no longer suitable for their production. Many preforming operations are required before finishing forging (Forging involves heating, deforming, and finishing a piece of metal) when the desired final shape of the item is complicated. This ensures a better functional cross-section and final shape. Therefore, the process is longer as the complexity of the parts increases.
There are different types of before-finish forging operations. Generally, the choice of operation will need to consider changes in the microstructure, mechanical properties, and deposition efficiency of the process in a way that does not degrade the desirable properties of the material.
Advantages of Heat Treatment
Heat treatment has numerous advantages, including the ability to change a material's physical (mechanical) qualities and to aid in subsequent production procedures. It reduces tensions in the item, making it easier to manufacture or weld. It can also strengthen the material, making it ductile or more flexible, or can soften metal to improve formability.
To boost abrasion resistance, it can apply a hard surface to relatively soft components as well as create a corrosion-resistant skin to protect parts that would otherwise corrode.
The most common heat treatment methods include: annealing, normalizing, hardening, aging, stress-relieving, tempering, and carburization
Application of Heat Treatment on AerMet100
Generally, the microstructure and mechanical properties of as-deposited AerMet100 steel are greatly affected by post-heat treatments, and thus research on heat treatments is essential to the wider application of AerMet100 in the aerospace industry.
To understand these processes, one can discuss the heat treatment of AerMet100 steel alloy fabricated with a hybrid of wire and arc additive manufacturing and in situ microrolling methods, as reported in a study published in the Additive Manufacturing Journal.
AerMet100 was subjected to two heat treatment designs: standard and homogenization. Scanning electron microscopy, optical microscopy, and X-ray diffraction were used to study the microstructures of as-deposited and heat-treated specimens, and an electronic universal testing machine was used to examine the mechanical characteristics.
The results indicated that austenitization (to heat the iron, iron-based metal, or steel to a temperature at which it changes crystal structure from ferrite to austenite). was the primary grain refinement process of the as-deposited specimens, and a decreased layer height and an adequately large heat input aided in the refinement. The more open the structure of the austenite, the more it is able to absorb carbon from the iron carbides in carbon steel.
Cellular segregation formed during solidification had severe heredity and strong effects on the microstructures of the non-homogenized heat-treated group, causing lower mechanical properties and anisotropy. Anisotropy is most easily detected in single crystals of solid elements or compounds with regular lattices of atoms, ions, or molecules. A material's anisotropic qualities include its refractive index, absorbency, and tensile strength.
A special fracture mechanism related to segregation caused fracture morphology featuring parallel structures in both the non-homogenized X-direction tensile specimens and X-Y direction plane-strain fracture toughness specimens.
Solidus is the highest temperature at which an alloy is completely solid—homogenization heat treatment involves putting samples into a furnace at a high temperature below the solidus temperature. Compared with the non-homogenized heat-treated group, homogenization heat treatment of the alloys for an extended period eliminated cellular segregation and achieved a better combination of the tensile and plane-strain fracture toughness properties.
In Summary
Metal processing into alloys is a cost-effective approach to improve material structural and mechanical qualities. Heat treatments provide a way to improve the characteristics of alloys before forging. As shape requirements become more complex, the necessity to design solutions that do not compromise material qualities becomes increasingly crucial.
The variety of qualities that may be attained through different heat treatments gives this high-strength steel a level of versatility not found in other high-strength steel.
More from AZoM: Considering the Behavior of Doped SrTiO3 Ceramics
References and Further Reading
Steel Service Aerospace Corp (2018). AerMet100 alloy fact sheet. [Online] Steel service aerospace corp. Available at: https://www.ssa-corp.com/documents/Data%20Sheet%20AerMet100.pdf
Graves, J.H. (1994). Effect of Heat Treatment on the Microstructure and Properties of AerMet (trade name) 100 Steel. (No. ADA284387). Army Research Lab., Watertown, MA.
Hu, D., Meng, K., Jiang, H. (2015). Experimental Investigation of Dynamic Properties of AerMet 100 Steel. Procedia Engineering, 2014 Asia-Pacific International Symposium on Aerospace Technology, APISAT2014 September 24-26, 2014 Shanghai, China, 99, 1459–1464. https://doi.org/10.1016/j.proeng.2014.12.685
Lu, Y., Wang, G., Zhang, M., Li, R., Zhang, H. (2022). Microstructures, heat treatments and mechanical properties of AerMet100 steel fabricated by hybrid directed energy deposition. Additive Manufacturing, 56, pp.102885. https://doi.org/10.1016/j.addma.2022.102885
Disclaimer: The views expressed here are those of the author expressed in their private capacity and do not necessarily represent the views of AZoM.com Limited T/A AZoNetwork the owner and operator of this website. This disclaimer forms part of the Terms and conditions of use of this website.