Process Analytical Technology (PAT) is essential for quality control and for the purpose of reducing risks and threats. PAT techniques are utilized worldwide for quality manufacturing and real-time analysis.
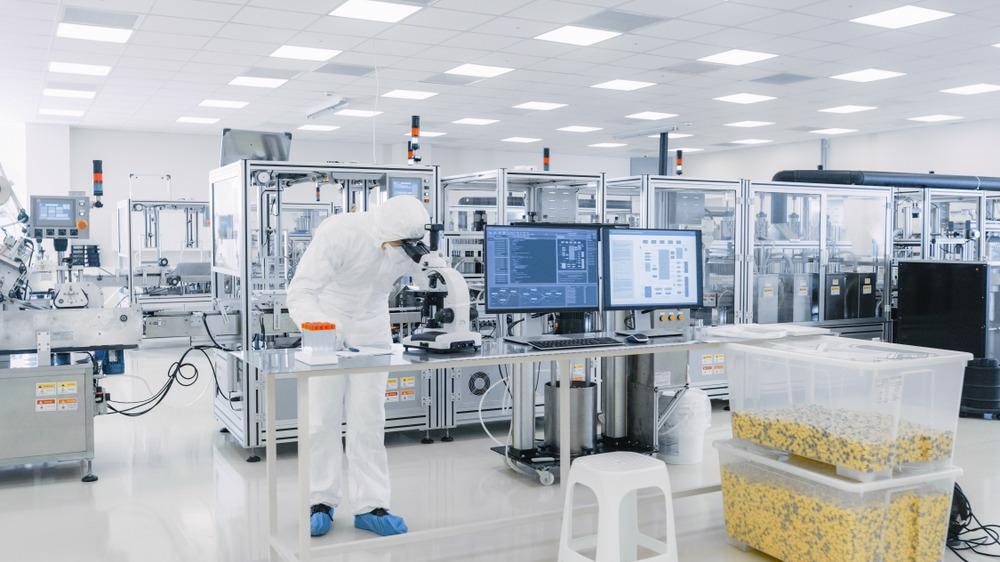
Image Credit: Gorodenkoff/Shutterstock.com
What is Process Analytical Technology?
Process Analytical Technology (PAT) is a high-value chemical and medicinal production approach. Critical parameters (CPPs) and key performance indicators (KPIs) of the operation are completely understood, well-defined, and continuously monitored to guarantee that the pre-defined critical quality attributes (CQA) of the final product are satisfied.
The United States Food and Drug Administration (FDA) defines PAT as a technique for designing, analyzing, and controlling pharmaceutical production processes via the measurement of CPP that impact essential quality features.
Methodology of PAT Techniques
PAT techniques continuously monitor important performance and reliability metrics in raw resources, in-process substances, and operations. A well-designed PAT-based procedure is robust, with crucial variables and indications remaining within predefined ranges to assure product quality and operational safety.
Why PAT Techniques are Implemented
PAT methods are particularly useful in the reduction of production cycling time and play an essential role in eliminating the rejection of batches. The enhanced automation and effective control of parameters and essential parameters are very advantageous. PAT techniques also allow for continuous fabrication and accurate real-time analysis leading to improved use of materials.
Which Tools are Utilized for PAT Analysis?
PAT employs several techniques, including spectroscopy methods and chromatography configurational monitoring systems, limited purpose sensors, computerized and quantitative data processing, and a collective knowledge management approach.
All of these technologies and approaches are intended to offer data in real-time or near real-time. As the goal of PAT is to increase the standards and security of produced goods, it must be integrated into activities leading to large-scale production, such as early and late-stage systems engineering and process scale-up.
PAT Based Machine Vision Systems for Particle Analysis
The latest research published in the International Journal of Pharmaceutics is focused on the analysis of particles of Meloxicam in tablets using digital UV/VIS imaging founded on machine vision systems. The particle size of pharmaceutical constituents has a substantial impact on the final product's effectiveness, durability, and safety. Operations that change the size of the particles of the employed ingredients are carried out during the manufacturing of drug formulations.
The particle size-based categorization was carried out using the image analysis programs and pattern classification computational model networks that were built. When five classes were adapted to various particle size specimens, UV pictures with or without the preprocessing procedure produced good results. However, when VIS photos were utilized as inputs, the created image analysis method produced better results.
The established approach was usable in the case of 2.5 w/w% percent MLX content, and it was not limited to particulate size fractions more or less than the ideal particle diameter of the employed API. The particle size analysis based on digital UV and VIS photographs of the tablets, on the other hand, was limited to particle size portions with D50 values greater than 5 μm.
What is the Relative Backscatter Index (RBI)?
RBI is a revolutionary process analytical technology method that shows how the size of the particles, morphology, and density vary in real-time under realistic operational parameters. Unlike turbidity measures, which are insensitive and confusing, RBI is an image-based assessment that uses real-time imaging to evaluate particulate system reflectance in the process.
RBI is a technique used to investigate alterations in particle diameter, structure, and abundance. RBI provides a simple, yet useful, continuous process measurement that may be utilized to analyze, optimize, and regulate complicated subatomic systems when it is dynamically integrated with high-resolution, real-time optical pictures.
Are There Any Innovative Nanoparticle Analysis Solutions?
The real-time evaluation of nanoparticles has enormous promise for a variety of PAT methods and implementations in a variety of industries. The NanoFlowSizer was created by InProcess-LSP as a one-of-a-kind PAT device for nanoparticle size analysis. Direct inline (underflow) assessment of size and dispersion is critical for non-solid materials to assure regular manufacturing quality. However, before the advent of NanoFlowSizer, no such systems were accessible.
To address the constraints of traditional Dynamic Light Scattering (DLS), a new novel method called Spatially Resolved Dynamic Light Scattering was used (SRDLS). SR-DLS can detect very opaque concentrations without dispersion and can characterize size distribution in a process flow. InProcess-LSP introduced the NanoFlowSizer as the only TRUE continuous particulate matter measuring technology in 2019.
It employs Fourier Domain Low-Coherence Interferometry (FD-LCI). FD-LCI Light scattering data is collected from nanoparticles at varying depths in the samples. The regionally or depth-resolved signal opens up new and interesting opportunities, with flow monitoring being one of the most important benefits. The distinctive depth-resolved light scattering data is relevant since it contains information on particle size as well as process flow properties.
Brief Introduction to Focused Beam Reflectance Measurements
Focused beam reflectance measurement (FBRMTM) is one approach for monitoring the quantity, structure, and morphology of particles using chord length distribution. ParticleTrack and EasyViewer probes with iC FBRMTM and iC VisionTM software, respectively, were proven to identify variations between a regular adjuvanted composition and one containing aggregation. They can also detect small variations in pore size distribution during the antigenic adjuvant sorption process.
To summarize, PAT techniques play a vital role in particle analysis. With the implementation of digitalized techniques, their effectiveness would increase manyfold leading to improved digital manufacturing and data analysis.
More from AZoM: What is Femtosecond Laser-Based 3D Printing?
References and Further Reading
Gerzon, G. et. al. (2022). Process Analytical Technologies–Advances in bioprocess integration and future perspectives. Journal of Pharmaceutical and Biomedical Analysis, 207, 114379. Available at: https://doi.org/10.1016/j.jpba.2021.114379
Chemical Engineering. A NEW PAT TECHNIQUE FOR REALTIME PARTICLE ANALYSIS. [Online]
Available at: https://www.chemengonline.com/new-pat-technique-realtime-particle-analysis/
Mettler Toledo, 2022. Process Analytical Technology (PAT). [Online]
Available at: https://www.mt.com/be/en/home/applications/L1_AutoChem_Applications/L2_PAT.html
InProcess-LSP. (2021, October 28). Innovative Solutions for Real-time Nanoparticle Analysis. AZoNano. Retrieved on May 13, 2022 from https://www.azonano.com/article.aspx?ArticleID=5832
Mészáros, L. A. et. al. (2022). UV/VIS imaging-based PAT tool for drug particle size inspection in intact tablets supported by pattern recognition neural networks. International Journal of Pharmaceutics, 121773. Available at: https://doi.org/10.1016/j.ijpharm.2022.12177
Disclaimer: The views expressed here are those of the author expressed in their private capacity and do not necessarily represent the views of AZoM.com Limited T/A AZoNetwork the owner and operator of this website. This disclaimer forms part of the Terms and conditions of use of this website.