Sponsored by Alemnis AGReviewed by Maria OsipovaJul 28 2022
Across academia and industry, glasses present the opportunity for a varied and rich field of study. Increasingly large window glass becomes ever more functional, while novel microfabrication techniques are pushing miniaturization to its limits. Many questions remain open, however, ranging from the basics of glass physics to ways of limiting brittleness for real-world applications.
To accomplish a more scientifically driven approach to designing and processing glass, the industry must lay its foundations on the physics of atomic rearrangements, defect initiation, and dynamic fracture as a reaction to mechanical loading.
In this article, we offer a perspective relating to the latest innovations in micro-mechanical testing of glasses and how they assist researchers and help better understand and improve the performance of glass components.
Miniaturizing Glass Components
Ensuring that the strength of glass is robust enough for a given task has been on the agenda since the beginning of glass production itself. One key issue is that the practical strength of glass is always lower than the theoretical strength as deduced from chemical bond strengths.
The main reason for this are microscopic flaws that act as stress concentrators. Such flaws are the result of fabrication and finishing processes and are extremely difficult to avoid.
To put it in simple terms, they expose weak links across the glass network. This was already established in the 1920s when Griffith observed that the strength of glass is contingent on the size of the test specimen.1
The probability of such flaws occurring lessens along with the volume of the specimen. Resultingly, glass components become comparatively more robust and stronger as they become smaller in size.
The opportunities this size-depended strength presents are numerous, with vast implications. Of course, significantly reducing the size of glass is not always a viable strategy – such as windows for buildings.
Instead, the application of composite glasses offers a much-improved solution to get around the inherent brittleness of glasses in civil engineering applications. Advancements in terms of size can be applied in the miniaturization of high-tech glass components down to the nanometre scale, where Griffiths’ theory is now gaining new significance.
Recently, progress in micro-additive manufacturing (µAM) and laser-assisted etching techniques has facilitated efficient and precise microfabrication of sophisticated glass components.2-4
The customizable properties of such glasses in combination with their exceptional chemical and thermal stability has revealed a host of new technological applications, including in microelectronics, medical technology, data storage, microelectromechanical systems, microfluidics, and microphotonics.
The capacity to understand and anticipate the exact micro-scale mechanical behavior of glass is now an important task.
Glass Mechanics at the Micro- and Nanoscale
As progress is being made in fabrication methods and the applications of miniaturized glass components, it is absolutely vital to reevaluate their mechanical performances.
As the mechanical properties at newly attainable small length scales typially exceed tabulated bulk properties, a considerable opportunity is now open.
Not only is there a potential increase in yield strengths, but approaching the intrinsic properties of glasses also reveals phenomena such as micro-ductility of glasses that would otherwise be brittle.
In the attempt to reduce the brittleness of bulk-sized glasses, investigations into micro-ductility can, for instance, serve as a stepping-stone towards the production of truly ductile glasses.
Micromechanical Testing in Practice
Pioneering advances in the field of in-SEM nanoindentation, Alemnis can offer a large range of time-tested micromechanical testing equipment. The Alemnis Standard Assembly (ASA) is the cornerstone of its modular system.
The three fundamental test types of micromechanical geometries that are made possible with the ASA are uniaxial compression or tension, nanoindentation, and lateral scratch testing (Figure 1).
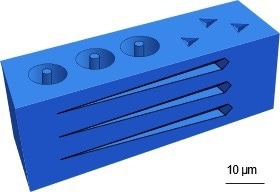
Figure 1. Sample geometry for micromechanical testing: Schematic representation of micropillars, nanoindents, and scratch test traces. Image Credit: Alemnis AG
Each of these geometries can be used as the base of a multitude of significant investigations. The conventional properties that can be evaluated using such tests are hardness and elastic moduli, fracture toughness, yield strengths, amongst others.
Add-ons for the ASA can also help evaluate the effects of extreme temperatures ranging from -150 °C up to 1000 °C, strain rates ranging from 0.001 s-1 up to 10’000 s-1, different atmospheres, humidity, and liquids.
This unparalleled versatility in terms of testing conditions pushes the limits of what is possible when it comes acquiring an understanding of materials under real-world operating conditions.
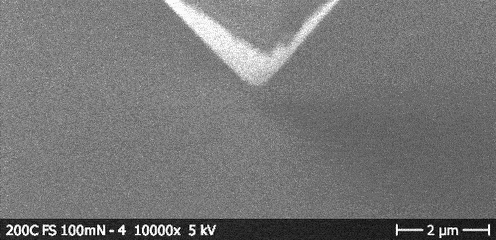
Figure 2. Fracture toughness of oxide glass measurement by nanoindentation. Image Credit: Alemnis AG
Practically speaking, investigating mechanical properties at the micrometer scale calls for the unrivaled and precise control over stability and positioning during in situ testing typically found in scanning electron microscopes (SEM).
Testing inside an SEM offers unmatched imaging capabilities. However, the vacuum environment of an SEM prevents any effects of environmental fatigue. Environmental humidity is known to provoke stress corrosion cracking by catalyzing bond breakage in propagating cracks. Therefore, there are also a number of good reasons to conduct micromechanical tests ex-situ – in air.
Extreme Conditions Testing
Downsizing glass facilitates testing of the intrinsic mechanical properties of the material. However, the concept of intrinsicality is not confined to room temperature and quasi-static strain rates. Both temperature and strain rate are just as important variables that must be defined and controlled. For glass science, there are many key application implications.
Firstly, the temperature–viscosity relationship tends to be non-linear and discontinuous around the glass transition temperature.5 As a result, operating limits at increased temperatures of glass micro-components are notoriously difficult to predict. Secondly, deformation processes of the amorphous atomic structures can be extremely sensitive to changes in strain rates.6
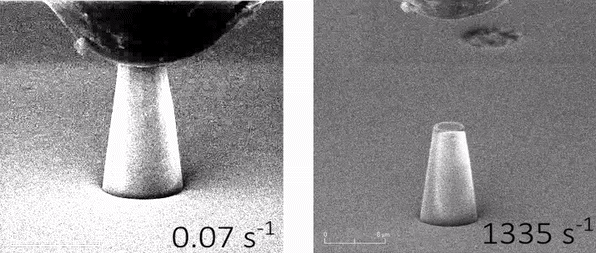
Figure 3: Strain rate dependent micro compression of fused silica6. Image Credit: Alemnis AG
It is important to tabulate micromechanical properties under such conditions, for component design, life-time prediction, and other engeneering tasks. Moreover, as these properties evolve as a function of temperature or strain rate (or both), they are also characteristic of atomic-scale deformation mechanisms that are not directly observable.
For instance, such data can be assessed in terms of activation energy, activation volumes, and strain rate sensitivities.
Extreme micro-mechanical testing offers more than just basic engineering quantities. It is a scientific approach that enables glass scientists to carefully evaluate the fundamental processes of deformation in amorphous materials, which are extremely difficult to investigate as a result of their lack of crystallinity.
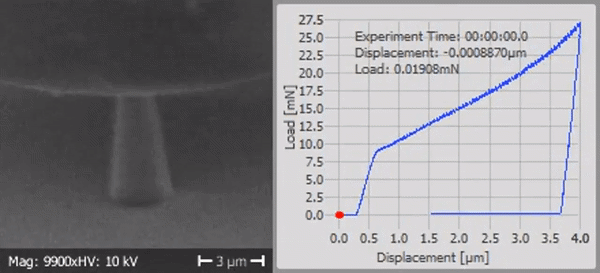
Figure 4. Extended micro-ductility of usually brittle fused silica at 600 °C (0.5 Tg).5 Image Credit: Alemnis AG
References:
- A. A. Griffith, ‘VI. The phenomena of rupture and flow in solids’, Philos. Trans. R. Soc. Lond. Ser. Contain. Pap. Math. Phys. Character, vol. 221, no. 582–593, pp. 163–198, Jan. 1921, doi: 10.1098/rsta.1921.0006.
- F. Kotz et al., ‘Three-dimensional printing of transparent fused silica glass’, Nature, vol. 544, no. 7650, pp. 337–339, Apr. 2017, doi: 10.1038/nature22061.
- X. Wen et al., ‘3D-printed silica with nanoscale resolution’, Nat. Mater., vol. 20, no. 11, pp. 1506–1511, Nov. 2021, doi: 10.1038/s41563-021-01111-2.
- J. T. Toombs et al., ‘Volumetric additive manufacturing of silica glass with microscale computed axial lithography’, Science, vol. 376, no. 6590, pp. 308–312, Apr. 2022, doi: 10.1126/science.abm6459.
- R. N. Widmer et al., ‘Temperature–dependent dynamic plasticity of micro-scale fused silica’, Mater. Des., vol. 215, p. 110503, Mar. 2022, doi: 10.1016/j.matdes.2022.110503.
- R. Ramachandramoorthy et al., ‘Dynamic Plasticity and Failure of Microscale Glass: Rate-Dependent Ductile–Brittle–Ductile Transition’, Nano Lett., vol. 19, no. 4, pp. 2350–2359, Apr. 2019, doi: 10.1021/acs.nanolett.8b05024.
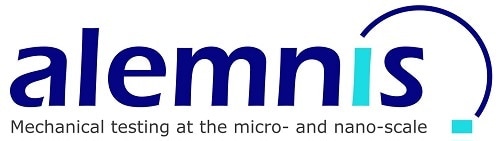
This information has been sourced, reviewed and adapted from materials provided by Alemnis AG.
For more information on this source, please visit Alemnis AG.