Updated by Reginald Davey 11/01/23
Nickel alloys are used extensively because of their corrosion resistance, high-temperature, strength, and their special magnetic and thermal expansion properties. This article will explore the different iron-nickel alloys used in industrial applications and naturally occurring types of iron-nickel alloys.
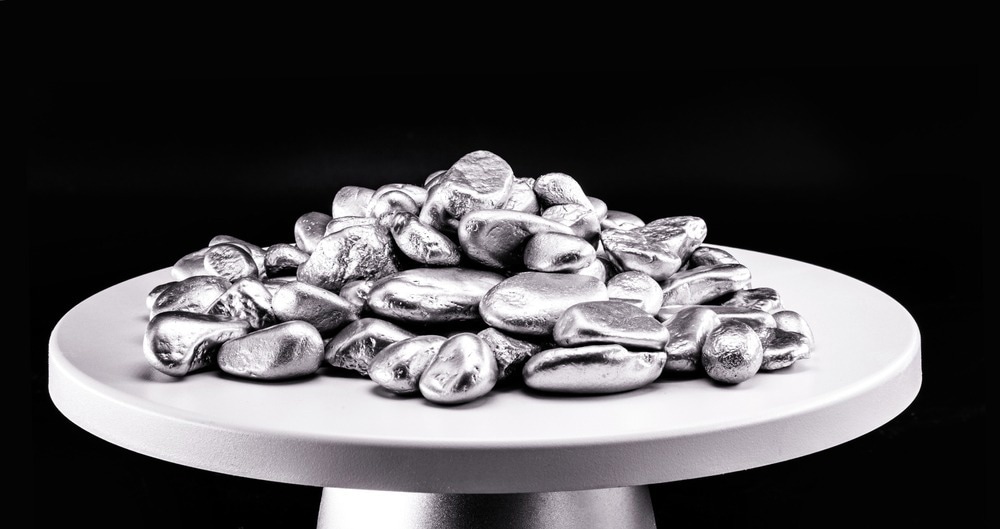
Image Credit: RHJPhtotos/Shutterstock.com
Overview
What is in nickel-iron alloys? These are a group of alloys that primarily consist of iron and nickel, with some additional fortifying elements such as chromium, cobalt, titanium, copper, and molybdenum. Iron and nickel are the main constituents of iron meteorites and planetary cores in telluric planets.
In massive stars, iron and nickel are produced during the final stages of stellar nucleosynthesis. This is the process whereby elements are produced during nuclear fusion. Iron comprises approximately 5% of the Earth’s crust, whereas nickel comprises around 0.0084%. Both elements are also found in small quantities in seawater and biological organisms.
Many naturally occurring iron nickel alloys exist due to the affinity between the two elements. Naturally abundant iron nickel alloy examples include meteoric iron or telluric iron. These are types of minerals and are called native metals. Some alloys, such as meteoric iron, have more than one crystalline structure.
The world has significant reserves of nickel and iron. The Nickel Institute estimates that there are around 300 million tons of nickel reserves on Earth. Major nickel producers include Canada, Australia, Russia, and South Africa. Over 80% of nickel extracted historically has been extracted in the last three decades.
The US Geological Survey estimates that global crude iron reserves are around 170 billion tonnes. Of this figure, 81 billion tonnes of extractable iron can be utilized in industrial applications. Iron is also recyclable, with 50 million metric tons recovered in the US in 2019. 4-4.6 million tonnes of nickel-bearing scrap is recycled per year.
Types of Major Commercial Iron-Nickel Alloys
The major alloy types that are used are:
• Iron-Nickel-Chromium alloys
• Stainless Steels
• Copper-Nickel alloys and Nickel-Copper alloys
• Nickel-Chromium and Nickel-Chromium-Iron alloys
• Low Expansion Alloys
• Magnetic Alloys
Other Naturally Occurring Alloys
Other iron-nickel alloys include taenite and tetratenite (both native metals contained in meteorites), kamacite, antinaenite, and awaruite (which is a native intermetallic compound commonly found in meteorites and serpentine.)
Stainless Steels
The majority of the stainless steels contain 8-10% nickel. In all cases, it is the combination of chromium with the nickel that does the job. Stainless steels are also useful as fire retardant materials since they retain their strength to higher temperatures than structural steel.
The most common stainless steel is the 304 grade with 8% nickel and 18% chromium as well as iron. This steel is used for such common items as spoons and forks, saucepans and kitchen sinks.
For applications which require enhanced corrosion resistance, such as for roofing in marine applications, type 316 is used. This has about the same amount of nickel and chromium as 304 but with 3% molybdenum added.
Nickel Copper Alloys
These alloys are sometimes referred to as MONEL or NICORROS and contain nickel with copper and small amounts of iron and manganese. A typical alloy is the 400 grade (UNS N04400). This contains 63% nickel minimum, 28-34% copper, and a maximum of 2% manganese and 2.5% iron. There are also a small number of impurities kept at limited values to ensure the metal’s properties are not harmed.
These alloys are used where a higher strength is required compared to pure nickel. They have a wider range of environments where they resist corrosion but in some specialised applications, such as strong alkali contaminant, nickel would be superior.
They find wide application in oil refining and marine applications where long corrosion-free life is required. Because of their good thermal conductivity they frequently are used for heat exchangers where sea water is one of the fluids concerned.
Nickel Chromium Base Alloys
These alloys are used extensively in applications where heat resistance and/or corrosion resistance is required. In some members of the group, where conditions are less demanding, some nickel is replaced by iron to decrease the overall cost
Metals fail at high temperatures by both oxidation (scaling) and through a loss in strength. Alloys in this class are designed to resist failure from both of these mechanisms. Nickel alloys are not suitable for high temperature sulphur rich environments.
Where corrosion resistance is significant, molybdenum is used as an alloying addition.
This group of alloys are frequently sold under trade name specifications but most are listed in the Unified Numbering System. Common trade names are HASTELLOY, INCOLOY, INCONEL, NICROFER, and NIMONIC,
The more recent alloys in these groups also have a wide range of ancillary elements added to give special properties - some of these can be quite complicated and require very close control over composition and heat treatment.
Table 1. Compositions of some common nickel alloys.
|
|
15.5
|
|
5.5
|
16
|
57
|
|
|
3.8
|
N06600
|
|
15.5
|
|
8
|
|
76
|
|
|
|
N06625
|
|
21.5
|
|
|
9
|
61
|
3.6
|
|
|
N08800
|
|
21
|
|
46
|
|
32.5
|
|
|
|
N07718
|
0.5
|
19
|
|
18.5
|
3
|
52.5
|
5.1
|
|
|
N07090
|
1.5
|
19.5
|
16.5
|
|
|
60
|
|
2.5
|
|
Table 2. Typical properties of some common nickel alloys.
|
N10276
|
Annealed
|
790
|
415
|
50
|
184
|
N/a
|
N06600
|
Annealed
|
550-690
|
210-430
|
55-35
|
120-170
|
38
|
N06625
|
Annealed
|
930
|
520
|
45
|
180
|
160
|
N08800
|
Annealed
|
520-690
|
210-410
|
60-30
|
120-184
|
70 (700°C)
|
N07718
|
Age Hardened
|
1350
|
1180
|
17
|
382
|
170
|
This list is far from exhaustive and enquiries should be made for specialised high temperature or corrosive situations.
All metals ‘creep’ under stress at high temperature and in their manufactured form, components may deform. This deformation could cause failure. Nickel alloys have higher strength and longer life at elevated temperature than most alloys. This makes them ideal for such parts as blades and disks in gas turbine engines. The designer however, must determine the expected life of each component and use the appropriate creep and rupture strength in the design.
Low Expansion Alloys
There are a group of nickel-iron ‘controlled expansion’ alloys where the expansion coefficient is low and constant over a range of temperatures.
These alloys are used extensively where changes in mechanical properties with temperature could be a problem, such as in precision springs. The alloys are also used where a metal/glass seal is required.
One example is the alloy containing 48% nickel and the balance iron (UNS K94800). This alloy has the following expansion coefficients:
20-100°C: 8.5 x 10-6m/m.°C
20-400°C: 8.3-9.3 x 10-6m/m.°C
This alloy has an expansion co-efficient designed to match that of soda-lime and soft lead glasses and thus provides a sound glass/metal seal that will not crack because of differential expansion between the two materials.
Magnetic Alloys
There is a requirement for materials with high magnetic permeability to minimise the power requirements to generate a strong magnetic field, such as that required in tape recorder heads and for magnetic shielding around precision cathode ray display devices.
These high permeability materials are complex alloys based on nickel with a range of composition possibilities. A typical composition could be: 70-80% nickel with small amounts of molybdenum and/or copper and the balance iron. This alloy would be expected to have a maximum relative permeability of between 50,000 and 100,000. Common trade names of this group are MU-METAL and PERMALLOY.
There is also a requirement for materials with a constant permeability over a range of magnetic flux densities. This is required in telephone equipment and electrical fitters where a variation in permeability would result in distortion. These alloys are generally known as the PERMINVAR alloys and have compositions ranging around 45% nickel, 30% iron and 25% cobalt.
Trade Names and Owners of Nickel Alloys
HASTELLOY is a registered trade name of Haynes Intl.
INCOLOY, INCONEL, MONEL and NIMONIC are registered trade names of the INCO family of companies.
INVAR is a registered trademark of Imphy S.A.
MU-METAL is a registered trademark of Telcon Metals Ltd
NICORROS and NICROFER are registered tradenames of Krupp UM GmbH
|