A hydrophilic and oleophobic surface repels oil. This innovative surface property has received increasing attention since it excels at anti-fogging, detergent-free cleaning, and oil and water separation.
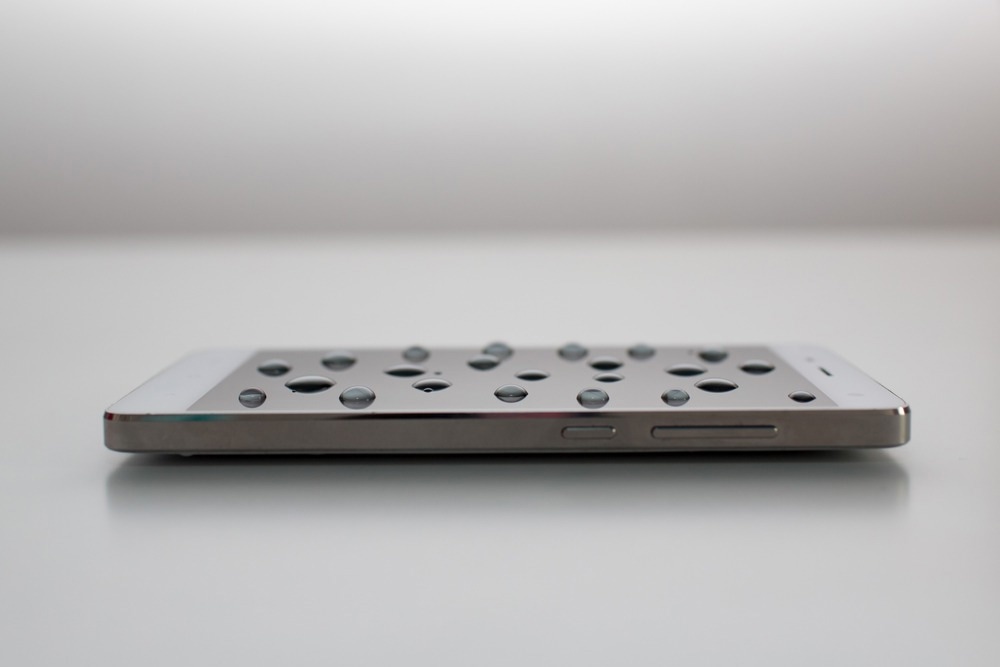
Image Credit: Max4e Photo/Shutterstock.com
The contact angle (CA) measures a surface's wettability by liquids; it's the angle created at the junction of the liquid droplet and solid tangent planes. When this angle is greater than 150⁰, the surface is superoleophobic.
The sliding angle (SA) determines the self-cleaning ability of a surface. A high CA and low SA value show that a surface has high liquid repellency and low adhesion properties (a solid won't attach to the surface but will slide away, keeping the surface clean).
Functional polymer chemical compositions affect surface free energy and wettability. For example, oil and organic liquids have lower surface tension than water. Therefore, the solid's surface energy must be lower than oil's for a superoleophobic surface.
Fluorinated polymers are used as coatings in industry, microelectronics, and biomedicine due to their chemical/thermal stability, low surface energy, and low friction coefficient. TiO2 is most commonly used for this purpose, along with several other organic and inorganic coatings.
Liquid-Repellent Surfaces in Nature
Liquid-repellent surfaces can be found in nature on various flowers, leaves, and animal skins. A few examples are lotus leaves, rose petals, watermelon skin, butterfly wings, fish and shark skins, beetle backs, bird feathers, mosquito compound eyes, gecko feet, and so on.
Their hierarchical micro/nanostructure affects their wetting capabilities and has been imitated in several artificially produced oleophobic and hydrophobic surfaces. Super-liquid-repellent surfaces require low surface energy and high surface roughness.
In a study published in The ACS Journal of Fundamental Interface Science (LANGMUIR), Yong Chae Jung and Bharat Bhushan looked at the skin of Squalus Acanthias, spiny dogfish to inspire an oleophobic surface for testing.
Different Liquid Repellent Approaches/Behaviors
Three major approaches are used:
Simultaneously Oleophobic/Hydrophilic: These repel both oil and water. Typically, oleophobic/hydrophilic surfaces are made by adding polymers to solid substrates using techniques such as layer-by-layer deposition, covalent graft, dip-coating, UV irradiation, and copolymerization.
Oleophobic/Hydrophobic to Hydrophilic Behavior: Water droplets can immediately wet oleophobic/hydrophilic surfaces and have a narrower contact angle than hexadecane. Several research studies have demonstrated oleophobic/hydrophilic surfaces that first exhibit oleophobic/hydrophobic behavior and then convert to hydrophilic behavior when wet for several minutes.
Hydrophilic/Underwater Superoleophibic: By modifying the environment of the surface, one can also achieve the oleophobic/hydrophilic property. Surfaces have been produced inspired by fish keeping their skin clean in water. These surfaces exhibit hydrophilicity in the air and superoleophobicity in water.
How to Fabricate Oleophobic Surfaces
Two common approaches are used for fabricating these coatings: bottom-up (coating techniques) or top-down (material removal techniques). The bottom-up approach results in random patterns, while the top-down approach produces regular patterns.
Top-Down Approach
Lithography: This technique uses a photoresist to transfer geometric shapes to a smooth surface. To make good patterns, it needs a leveled and clean surface. Different surface structures, such as circular pillars, squared pillars, star-shaped pots, and indented square pots, have been created using this approach.
Template Method: Hierarchical super-liquid-repellent surfaces can be made using the template method. This procedure involves preparing a master template, molding a replica, and removing the template. Templates can be made from natural or artificial surfaces.
Etching Technique: Suitable surface structures can also be produced by wet or dry etching (classified based on the use of the solution). Chemical, plasma, electrochemical, and liquid-based metal-assisted etching are examples of this approach. Wet etching is imprecise and can cause particle contamination, while dry etching requires expensive equipment. However, a uniform surface is possible through this technique.
Particle Coating: This is the most popular and straightforward way to create hierarchical surfaces. It creates multilayer films, and each layer's particle size affects wettability. TiO2 is the most prominent inorganic substance for this surface structure.
This technique is applied in three ways: (1) Blending fluoropolymer and nanoparticles in a solution and applying the solution to fabricate surfaces. (2) Modifying nanoparticles using fluoropolymer and then coating the surface. (3) Applying fluoropolymer after coating the nanoparticles.
Bottom-Up Approach
Electrodeposition: Electrochemical polymerization and deposition are cheap ways to make super-liquid-repellent surfaces. These approaches provide a controlled rough surface quickly. However, it's time-consuming, and the conducting solution gets polluted as the process continues.
Vapor Deposition: Any element or compound can be deposited using this technique. High-purity, dense films are made. Some processes require high vacuums, temperatures, and costs.
Spray Coating: Spray coating is a straightforward, low-cost, scalable way of making super-water-repellent surfaces. Mechanically damaged coatings are easily restored. These coatings can be applied to any size, shape, or material surface. The major drawback is that the spray coating wastes more material than other methods.
Immersion Method (Dip-coating): The easiest and most successful coating procedure requires a submerged substrate. This strategy eliminates waste. However, a huge amount of coating solution is needed to immerse the surface entirely.
Spin Coating: Spin coating's quick drying durations result in remarkable consistency on macroscopic and nanoscales. This process produces thin, homogeneous films. Spinning is a batch (single substrate) process.
What are the Properties and Applications of Oleophobic Coatings?
These surfaces have numerous applications due to their self-cleaning, transparency, oil-water separation, anti-corrosion, and anti-microbial properties, along with low cost and simplicity of processing.
Self-Cleaning: Self-cleaning was identified on a blue lotus in 1970. A lotus's smooth surface is rough on the nano or micro-scale and superhydrophobic. If dust accumulates on a superhydrophobic surface, water droplets roll off and remove the dust.
Detergent-Free Cleaning: An oleophobic/hydrophilic surface is more wettable by water than oil, so water may easily replace oil pollutants and flush them away. This self-cleaning surface reduces the need for detergents.
Anti-Corrosion: Corrosion is an irreversible interfacial interaction between materials and so the environment. Material loses structural integrity with time due to corrosion, while corrosion resistance increases product life. Studies recommend superoleophobic/superhydrophobic coatings for anti-corrosion protection.
Transparency: Transparency is critical when making superoleophobic/hydrophobic coatings for windshields, safety eyewear, photovoltaic cells, and windows/screens. Transparent superhydrophobic/oleophobic coatings also protect documents, clothes, buildings, and art.
Anti-Fogging: Super-hydrophobic/oleophobic surfaces reduce fogging and frosting by not allowing water droplets to stick to them. This characteristic is vital while making eyeglasses, solar cells, cars, and optical instruments with minimal surface contamination.
Solar Evaporation: Water scarcity is a global threat. Desalination employing porous superhydrophobic/oleophobic surfaces may be a partial solution. Superhydrophobicity helps evaporating structures float over water and minimizes absorber surface pollution.
Scratch-Resistant: A thin layer of microscopic substrates prevents scratching on surfaces. Minor cuts, compression marks, or rubbing can generate scratches on plastics like glasses. Anti-scratch coatings make optical lenses, discs, displays, injection-molded parts, gauges, mirrors, signs, and eye safety/protective goggles last longer.
Scratch-resistant coatings should be affordable, reduce scratch depth and width, and increase color and shine. For example, a recent study demonstrated a one-step procedure for making a superhydrophobic/superoleophobic fluorine-free coating on stainless steel mesh. In addition, the study demonstrated that the coating might keep its extreme hydrophobicity after being sanded and damaged 50 times, showing amazing resistance.
Thin Films: Flexibility is the main design parameter of flexible thin films. Chemical composition and surface polish determine whether thin coatings are oleophobic or not. Oleophobic coatings protect flexible thin films from fingerprints, dust, and other stains on smartphones and display screens. These can be factory-installed, integrated/embedded in flexible thin films, or purchased separately.
Limitations: In gadgets, these coatings give extra protection, but they wear off over time, limiting their ability to repel oil and water and attracting dust. Therefore, it is better to buy an oleophobic thin film coating separately and apply it to the device, even if it has an inbuilt oleophobic coating. When it wears off, replacing the coating is cheaper than replacing the entire gadget.
More from AZoM: What Materials are Used to Make Electric Vehicle Batteries?
References and Further Reading
Jung, Yong Chae, and B. Bhushan (2009). Wetting Behavior of Water and Oil Droplets in Three-Phase Interfaces for Hydrophobicity/philicity and Oleophobicity/philicity. The ACS Journal of Fundamental Interface Science (LANGMUIR) 25 (24), 14165-14173 http://doi.org/10.1021/la901906h
Paras, Aditya Kumar (2021). Smart bioinspired anti-wetted surfaces: Perspectives, fabrication, stability and applications. Journal of Current Research in Green and Sustainable Chemistry, Volume 4, 100139,ISSN 2666-0865. https://doi.org/10.1016/j.crgsc.2021.100139.
Son, T., Yang, E., Yu, E. et al. Effects of surface nanostructures on self-cleaning and anti-fogging characteristics of transparent glass. J Mech Sci Technol 31, 5407–5414 (2017). https://doi.org/10.1007/s12206-017-1035-y
Zhang, Zh., Wang, Hj., Liang, Yh. et al. One-step fabrication of robust superhydrophobic and superoleophobic surfaces with self-cleaning and oil/water separation function. Sci Rep 8, 3869 (2018). https://doi.org/10.1038/s41598-018-22241-9
Disclaimer: The views expressed here are those of the author expressed in their private capacity and do not necessarily represent the views of AZoM.com Limited T/A AZoNetwork the owner and operator of this website. This disclaimer forms part of the Terms and conditions of use of this website.