Lorena Saitta, PhD, was working on modeling micro-optofluidic devices suitable for the optical investigation of two-phase flow generated by immiscible fluids in the Polymers and Composites Lab at the University of Catania (responsible Professor Gianluca Cicala) in collaboration with the Microfluidic Lab (responsible Professor Maide Bucolo) and Inorganic Chemistry Lab (Professor Maria Elena Fragalà).
Saitta focused on a one-step manufacturing technique that provides optical transparency and customized surface chemistry without requiring additional assembly.
Finding the Right Materials to Achieve Necessary Functionality
The optical detection of immiscible fluids requires optical transparency. Under the incident laser, the two fluids with differing reactive index values display distinct light transmission properties. To eliminate flow instability within the microchannels, the device also requires adequate surface roughness and hydrophilic behavior. Fluid leaking at assembly sites could result from further assembly. The ability to build the device in a single piece eliminates fluid leaks.
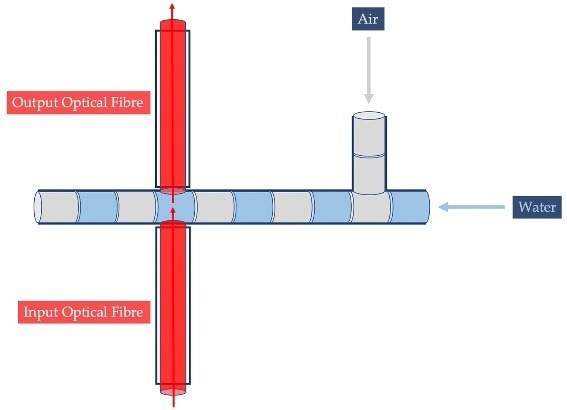
Schematic of the micro-optofluidic device. Image Credit: Boston Micro Fabrication
PDMS is a popular choice for micro optofluidic devices. However, PDMS has some significant drawbacks. When subjected to non-polar organic solvents, the microchannel walls deform slightly. It is difficult to permanently link molecules or polymers to PDMS, restricting the ability to form complex structures.
3D Printing the Micro-Optofluidic Devices
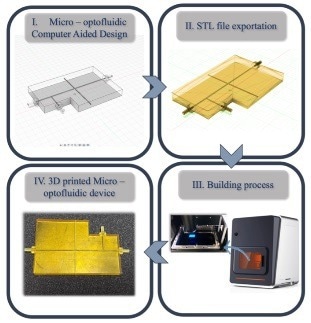
Steps for 3D printing the micro-optofluidic device. Image Credit: Boston Micro Fabrication
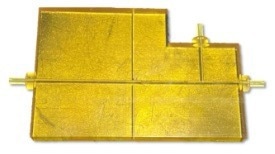
Micro 3D printed micro-optofluidic device. Image Credit: Boston Micro Fabrication
Saitta used 3D printing to create the micro-optofluidic device in a single piece. The group printed the device with embedded inlets, outlets, and insertions for micro-optical fibers using the microArch S140. BMF’s HTL resin provided the capabilities required by Saitta’s devices.
The resin’s transparency and hydrophilic nature enabled stable fluid flow and the detection of a wide range of reactive index values. The microArch S140 was also capable of producing the micro-optofluidic device in a single piece, alleviating concerns about fluid leakage.
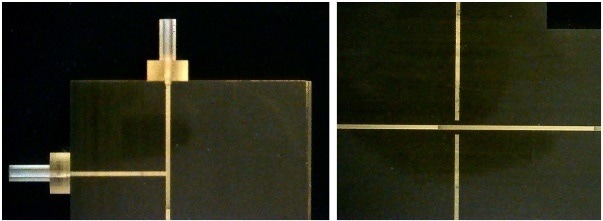
400 µm square channels in the micro 3D printing micro-optofluidic device. Image Credit: Boston Micro Fabrication
Projection Micro Stereolithography has opened new frontiers in the manufacturing of micro-optofluidic devices.
Lorena Saitta PhD, University of Catania
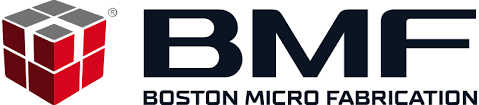
This information has been sourced, reviewed and adapted from materials provided by Boston Micro Fabrication (BMF).
For more information on this source, please visit Boston Micro Fabrication (BMF).