Compared to traditional steels, plastics, or other non-ferrous materials, modern technical ceramics provide extraordinary material qualities and features. Ceramics often have high hardness, wear resistance, compression strength, electrical resistance, and little sensitivity to acids or caustics.
Some ceramics, such as silicon carbide made by CVD, provide further benefits by enabling electrical and relatively strong heat conductivity. Aluminum nitride, in contrast, combines very poor electrical conductivity with a slightly high heat conductivity.
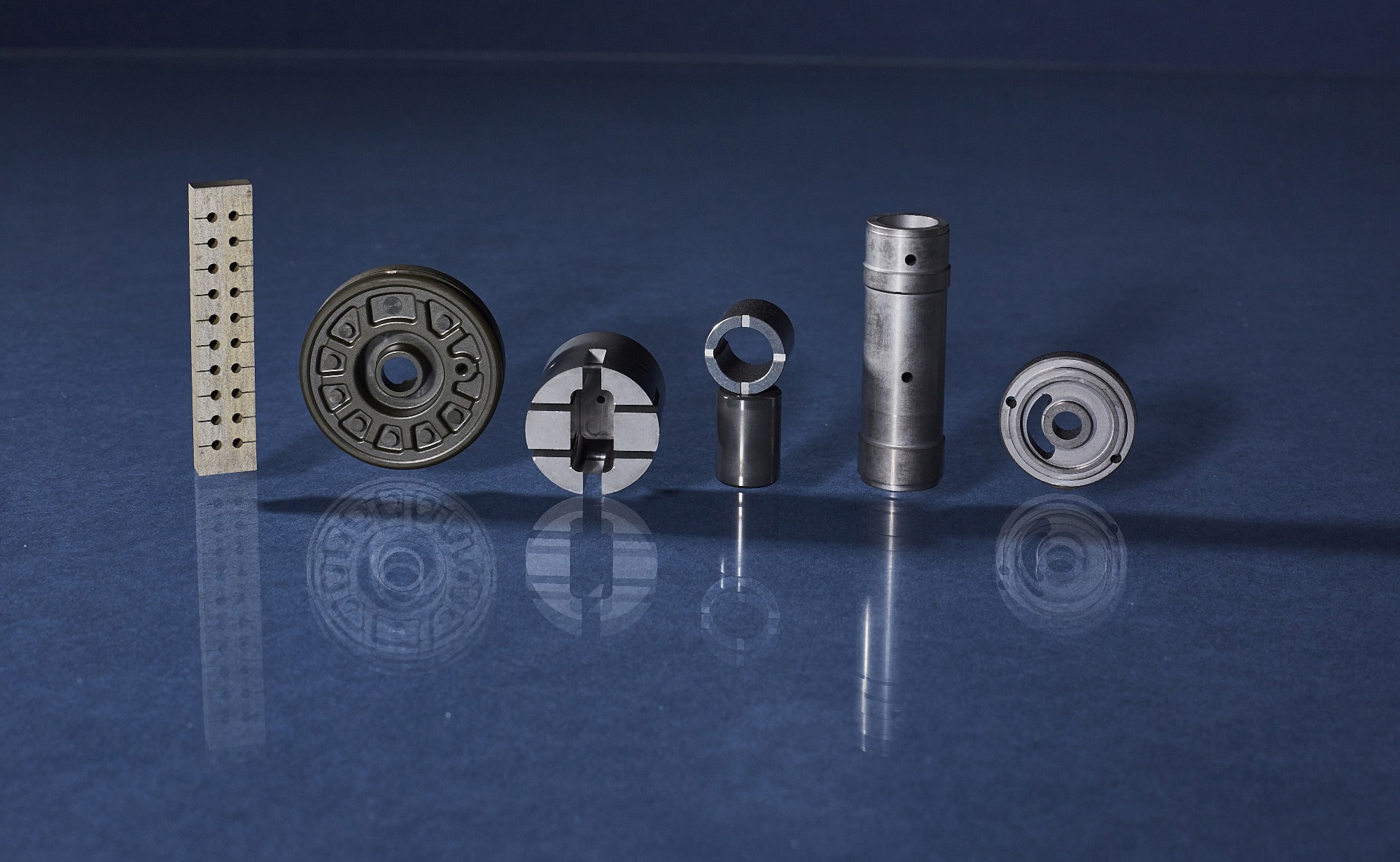
Image Credit: Insaco Inc.
When developing a new application for ceramics, it is advisable to consult with material experts early to determine which features can be easily attained and which would be constrictive. The Designer’s Guide can be used as a resource for designers to learn more about the qualities of common ceramics.
Challenges of Technical Ceramics
Technical ceramics provide a plethora of challenges. Many are made by pressing powders or pastes into rough forms and burning them at low temperatures to create delicate “green” ceramics, such as alumina or zirconia. Before the final high-temperature firing yields the solid product, a green ceramic can be machined to add holes, flats, or other characteristics.
However, high-temperature firing results in substantial shrinkage, which makes it impossible to ensure tolerances better than a few percent of the specified dimension, even with meticulous algorithms.
Precision characteristics such as holes, perpendicularity, or dimensions of +/–.001” can only be obtained after firing, which adds significantly to the cost. If users do not require such precise tolerances, they can save a considerable amount of money.
Diamond Grinding
Single-point cutting is used to manufacture the majority of metals. However, because heated ceramics are often tougher than the cutter, this technique does not work on them. There are always exceptions, and in this instance, a diamond chip can be used for single-point cutting, but this is only practical in extremely specific circumstances.
Fired technical ceramics are often “machined” via grinding, and the majority of this grinding typically uses diamond grinding wheels. These wheels are constructed using diamond grit implanted in composites or metals that remove the material by impact.
Due to the tremendous pressure being applied, grinding is a laborious operation that necessitates rapid cooling of the impact/cutting zone to prevent heat fracture of the diamond grits.
Although “tedious” and “diamond” suggest higher costs, it is feasible to create tight tolerances and small features that will remain stable for much longer than other material options because of the material stability.
Diamond grit has a very intense microscopic reaction with alumina or its single-crystal version, sapphire. Due to its alumina-like characteristics, sapphire is chosen for window or lens applications when glass is inadequate due to high pressure, extreme wear, or chemicals.
However, polishing sapphire necessitates reducing or completely removing any subsurface damage on a microscopic level. As a result, the object will be polished using diamond slurries with progressively finer grits after being ground with diamonds to obtain the shape.
As with any technique using diamond-on-ceramic, it is essential to exclude heat from the process to prevent piece damage and maintain the sharpness of the diamond edges.
Aerospace, Semiconductors, and Other Applications
Technical ceramics, particularly sapphire, can enhance the performance of components used in harsh environments. When steel or glass components frequently malfunction in unforeseen ways and halt the machine, this can be extremely helpful.
Sudden stops in a process flow will result in very high downtime costs, which might support the usage of a more expensive ceramic component. For demanding applications, such as high-temperature settings, or when conventional materials will not work, ceramic parts can also be used. Aerospace, semiconductor, oil field, and medical industries are among the applications.
With more than 70 years of experience, INSACO is acknowledged as the market leader in the machining of extremely hard materials, including quartz, sapphire, and ceramics. It is recommended that designers always start with common materials, such as steel, aluminum, or glass, since they are easily accessible and can be machined or shaped at a reasonable cost.
A designer should never overlook technical ceramics. Their capabilities can result in significant process advancements, if not outright breakthroughs, which readily justifies increased manufacturing costs.
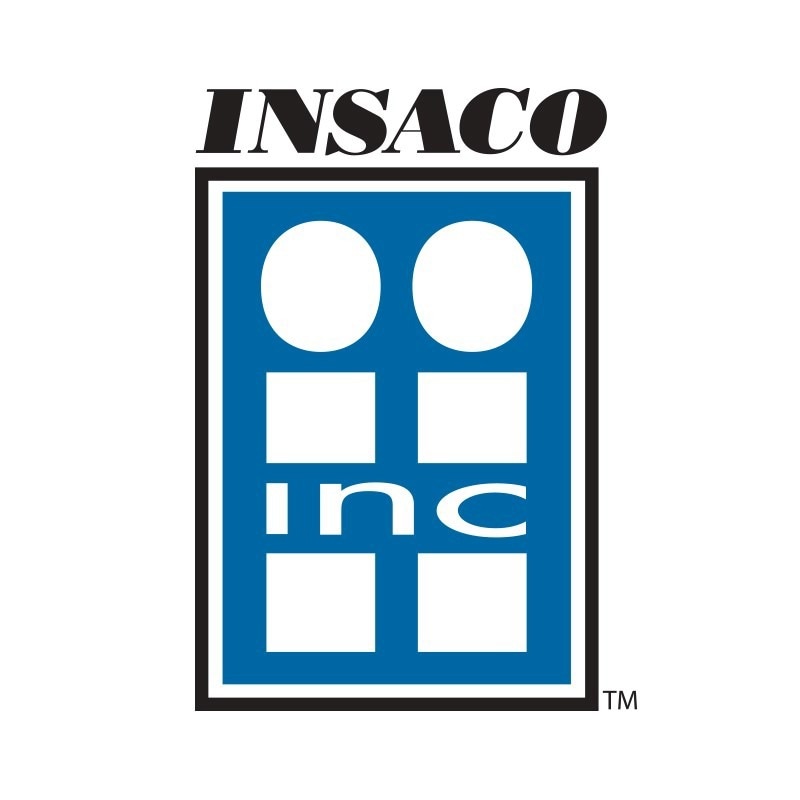
This information has been sourced, reviewed and adapted from materials provided by INSACO Inc. - Machining of Hard Materials.
For more information on this source, please visit INSACO Inc. - Machining of Hard Materials.