The main ingredients of borosilicate glass are 80.6% SiO2, 12.6% NaO2, 2.2% Al2O3, and traces of other important materials. Excellent thermal shock resistance and high-temperature resistance were the main priorities while manufacturing this glass. Low thermal expansion, excellent chemical resistance, and efficient transfer from UV to IR are further advantages.

Image Credit: Shutterstock/Keith Homan
This transparent material is designated for LCDs, telescope mirrors, electronic sensors, and other uses within optical, MEMS, nuclear energy, and other precision-engineered applications since it can create precise parts.
Many years ago, Corning gave their borosilicate glass the brand name Pyrex. It is widely recognized from cookware that stands up to oven temperatures and rapid cooling during kitchen handling. In addition to other uses, Pyrex was frequently used for laboratory equipment.
Corning eventually licensed both the Pyrex and Pyrex logos to various businesses. Although both Pyrex and Pyrex are advertised as cookware, Pyrex is a borosilicate glass, whereas Pyrex is a soda-lime glass product. However, the borosilicate variant is likely more resilient to heat stress.
The company’s borosilicate glass is currently made to Corning 7740 standards. This glass must first be sliced into smaller pieces since it is created in blocks rather than sheets. Due to this, designers requiring precision glass components in bigger sizes frequently specify that they want to use 7740.
The current borosilicate glass made by the Schott Company is Schott 8330. The float glass technique is used to create this glass, also known as Borofloat 33. Standard thickness could be useful without any further trimming, depending on the intended function.
If tolerances are not deemed crucial, a waterjet approach may be used to cut glass. To obtain the closest tolerances, however, a diamond grinding technique is necessary.
Precision pieces are often cut large and then ground back to the desired dimension to remove chips as simple cutting produces a “chippy” edge. Chamfers are required to reduce any issues with handling the sharp edges. It is possible to flame-polish ground surfaces, although doing so reduces the part’s dimensional accuracy and requires an additional anneal.
High degrees of polish can also be achieved on ground surfaces using chemo-mechanical processing. These operations are often carried out one surface at a time, making them a cost factor that needs to be carefully taken into account.
INSACO has a long history of obtaining borosilicate glass raw materials, producing, and polishing precise components in accordance with client requirements. The tubing of borosilicate glass comes in a variety of diameters and the usual 1 m length.
For further machining, this might serve as a practical and affordable starting point. If not, 7740 or Borofloat materials, as stated, are often specified for the production of precise components.
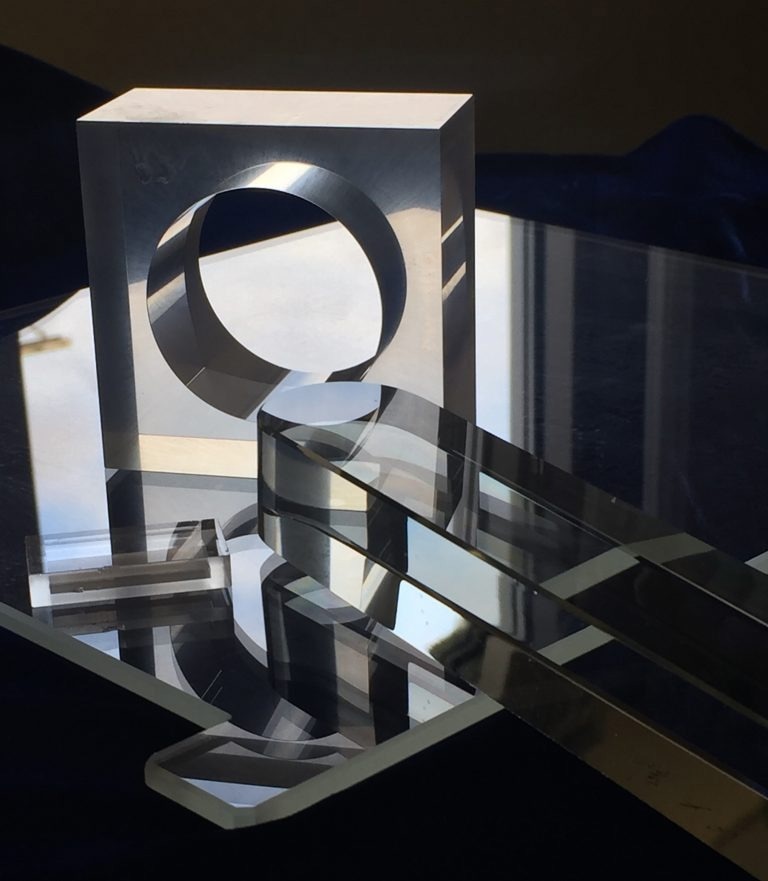
Image Credit: INSACO Inc.-Machining of Hard Materials
Source: INSACO Inc.-Machining of Hard Materials
Property |
Value |
Mechanical |
Density |
2.23 g/cc |
Hardness |
418 Knoop |
Modulus Of Elasticity |
9.1 x 106 psi |
Poissons Ratio |
0.20 |
Electrical |
Dielectric Constant |
4.6 (@ 1 MHz) |
Volume Resistivity |
8 x 1010 ohm-cm |
Thermal |
Coefficient Of Thermal Expansion |
3.3 x 10-6/°C |
Thermal Conductivity |
1.35 W/mk |
Specific Heat |
0.185 cal/g °C |
Maximum Working Temperature |
500 °C |
Optical |
Index Of Refraction |
1.474 |
All properties are at room temperature unless otherwise noted.
Engineering data are representative, and are not intended as absolute nor warrantable. Manufacturer’s Data shown is blended from multiple sources and therefore illustrates the marketplace.
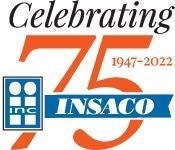
This information has been sourced, reviewed and adapted from materials provided by INSACO Inc. - Machining of Hard Materials.
For more information on this source, please visit INSACO Inc. - Machining of Hard Materials.