RNDR Medical, located in Louisville, Kentucky, US, is a team of accomplished medical device engineers, designers, technicians, and executives dedicated to advancing medical technologies.
The company boasts over 100 years of combined experience and provides comprehensive engineering services, utilizing a state-of-the-art FDA-registered clean room for manufacturing.
The team at RNDR Medical is known for its numerous professional achievements, including the creation of multi-million unit product lines, more than 100 patented designs with multiple pending, the successful launch of numerous products, and their innovative contributions to clinical fields such as endoscopy, cardiology, urology, peripheral vascular, and laparoscopy.
The Challenge
RNDR Medical has developed a cutting-edge single-use endourologic scope designed for the direct visualization and navigation of disorders within the urinary tract, such as urothelial carcinoma and kidney stones, as well as for performing pyeloscopy procedures.
The scope is equipped with advanced features, including a digital high-definition camera and illumination for clear visualization of anatomy, fluid irrigation for maintaining a clear image, and a working channel for the passage of therapeutic tools, such as lithotripsy fibers and retrieval baskets, for the treatment of kidney stones.
This innovative product will soon be launched and is poised to revolutionize the diagnosis and treatment of urinary tract disorders.
The device features a critical component known as the distal tip, which serves several functions. It contains the camera chip and illumination source, directs fluid pathways for irrigation, and provides the connection between the working channel and the exterior anatomy.
To ensure proper function, the distal tip must be manufactured precisely, housing all components within a .130-in diameter profile and sealed to prevent fluid from entering the device.
The exterior geometry of the distal tip must be atraumatic to anatomy, as it is part of the device that faces forward and advances.
Creating such a component, with its complex 3D geometry, tight tolerances, and thin wall thickness, typically requires niche micro molding. However, this method has a longer return on investment due to the large number of components required annually, which can reach tens of thousands.
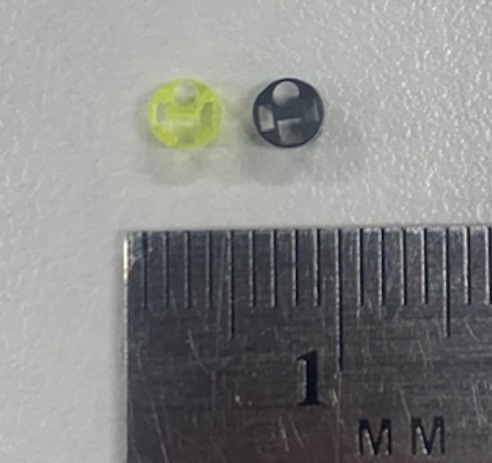
Micro 3D printed distal tip, Micromolded distal tip. Image Credit: Boston Micro Fabrication (BMF)
An Alternative to Micro Molding
Anthony Appling, Principal and Co-owner, and Keith Wells, Design Engineering Lead, sought a more efficient and cost-effective solution to the challenges of micro molding.
They discovered Boston Micro Fabrication's Projection Micro Stereolithography (PµSL) micro 3D printing technology, which offered a resolution in the range of 2 µm to 25 µm and tolerance of +/- 10 µm to 25 µm through its microArch series of micro-precision 3D printers.
During the early design phase of the device, the BMF printers enabled rapid iteration and development of the distal tip component at scale.
This significantly shortened the development timeline compared to traditional methods, which would have required costly micromachining for iterative development, followed by the long lead time and investment in micro molding, and possibly the need for multiple tools to test various optimal tip geometries in the appropriate material.
The speed and versatility of the BMF system greatly benefited the engineering team, enabling them to arrive at an optimal design with minimal time and cost.
Appling and Wells found that the BMF material performed well during their component testing, leading them to the realization that additive manufacturing was a viable option for design development and potential initial production volumes.
BMF 3D printing technology is critical to the fast, iterative development of precision components, enabling the advantages of additive manufacturing at scale from prototype to production.
Anthony Appling, Principal and Co-owner
The volume flexibility and scalability of the BMF system make it ideal for product development and manufacturing. In RNDR's case, a single build cycle can produce up to 500 distal tip components.
The impact of using BMF technology on RNDR Medical has been substantial, cutting development time by up to 50%. The microscale 3D printers from BMF allowed the company's medical device engineers to quickly evaluate and refine designs, taking only days and weeks instead of months.
The geometric accuracy and material strength of the 3D-printed parts instilled confidence in the team, and the 3D-printed distal tips passed pre-clinical evaluation in a simulated use environment.
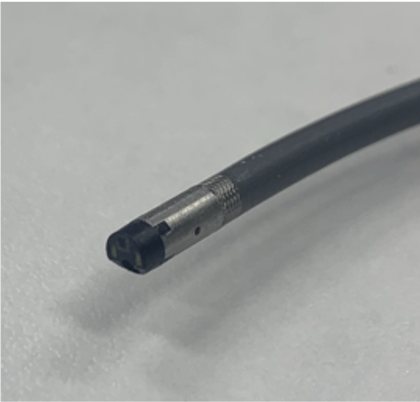
Disposable scope tip. Image Credit: Boston Micro Fabrication (BMF)
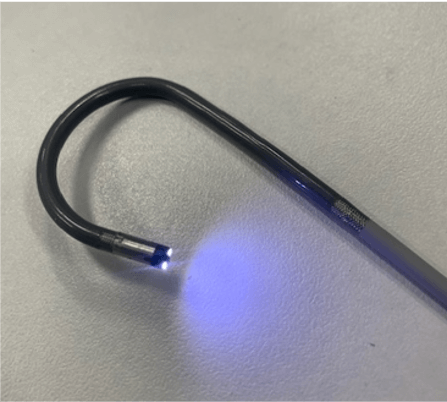
Disposable scope tip. Image Credit: Boston Micro Fabrication (BMF)
The Future
The company envisions using micro 3D printing as a bridge technology for early commercialization and large-scale production. To assess its suitability, an evaluation of available 3D materials will be critical.
The demand for minimally invasive medicine is increasing, and there is a need for disposable catheters and scopes with a wealth of features at the end of smaller-diameter catheters.
As demonstrated in this case study, multiple design elements must be accommodated within compact profiles.
For medical device engineers, the challenge of incorporating more features into a smaller space can quickly surpass the limitations of multi-axis machining and molding, where draft and uniform wall thickness must be maintained.
With microscale 3D printing, engineers can take full advantage of the entire volume of a component for functional purposes without the usual concerns about design for manufacturing (DFM).
As demonstrated by RNDR Medical, BMF 3D printers are ideal for visualization systems, therapy and diagnostic catheters, and delivery systems in the medical device industry.
To gain further insight into microscale 3D printing, contact BMF. Medical device manufacturers seeking an experienced and innovative team that provides a complete range of engineering services should contact RNDR Medical.
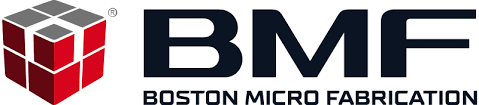
This information has been sourced, reviewed and adapted from materials provided by Boston Micro Fabrication (BMF).
For more information on this source, please visit Boston Micro Fabrication (BMF).