From MicrotracReviewed by Emily MageeJun 22 2023
In this interview, AZoM speaks to Paul Cloake, Director of Sales at Microtrac MRB, and Gert Beckmann, Product Specialist for Dynamic Image Analysis at Microtrac MRB. They discuss particle analysis and the role of Microtrac within this field. They also discuss the CAMSIZER 3D, a unique particle analyzer that is creating new standards in the characterization of bulk solids.
What is Microtrac, and what is the company’s background in particle analysis?
Microtrac is dedicated to materials characterization and specializes in the measurement of particle size, particle shape, particle charge, dispersion stability, surface area, porosity, and density.
In 2024 Microtrac will celebrate its 50th anniversary. Over the last 50 years, Microtrac has constantly been at the forefront of innovation in this field.
Back in 1973, Microtrac developed the first Laser Diffraction Particle Size Analyser. In 1998 the CAMSIZER was developed in Germany, setting the standard for Dynamic Image Analysis.
Throughout our long history, Microtrac has been a leader rather than a follower, continually delivering advanced solutions to our customers.
In 2019, Verder Scientific acquired Microtrac Inc. USA and Microtrac BEL Japan. Combining these with Retsch Technology GmbH based in Germany, the Microtrac MRB Segment of Verder Scientific was created.
What is particle size and shape analysis, and why is it so important?
Particle Size and Particle Shape Analysis measures the overall size (length, width, thickness, etc.) and morphology of either individual particles or a representative sample of a bulk material.
In almost any natural or manufactured material, particle size and shape are critical parameters that must be considered in order to determine the suitability of a material for a specific application.
Some examples are outlined below:
- In pharmaceutical materials, particle size is important in designing drug delivery systems, ensuring the active ingredient reaches the correct part of the body.
- For glass bead manufacturers, particle sphericity is critical to guarantee the retro-reflectivity of the beads used in road markings.
- For chocolate makers, the size of the chocolate particles determines the taste and texture of the final product for the consumer.
- For paint manufacturers, particle size and shape are important in the coverability and color consistency of the coating.
- In battery technology, particle size and the shape of the materials used in electrodes, electrolytes, and separators directly affect the efficiency of charging and discharging.
The list goes on.
How has particle size and shape analysis changed over the past decade?
The continual advances in the sensitivity of detector and camera technologies have driven improvements in the accuracy and precision of size and shape measurements.
The movement away from gas HeNe lasers to more modern semiconductor diode lasers has allowed for the fabrication of more stable and coherent light sources. Modern high-resolution cameras also have the enhanced capabilities of Digital Image Analysis to measure smaller sizes with higher accuracy.
Most methods for measuring particle size – Laser Diffraction, Dynamic Light Scattering, Time of Flight Measurements, Sedimentation methods, and Centrifuges – all measure ensemble samples delivering data as averages, such as mean volume and 10/50/90 percentiles.
In comparison to laser diffraction, where we need to look at ensemble samples, the progressive acceptance of Image Analysis allows us to look at individual particles of large samples, yielding significantly more qualitative data on additional size and morphological parameters.
The combination of Laser Diffraction and Image Analysis on the Microtrac SYNC provides QC users with the “go/no-go” data they need to deliver finished products while providing researchers and process engineers with significant information to help develop new products and processes.
Why does CAMSIZER 3D represent a step forward in particle analysis and the characterization of bulk solids?
Our world is three-dimensional. Thus, 2D images are unable to fully represent or even describe 3D objects and only exist in theory, such as on a piece of paper or a computer screen.
For context, about 25 years ago, all manufacturers of Digital Imaging systems and their customers used just one size parameter per particle. This one-size value came from an equivalent diameter of a circle with the equivalent area of the shadow image of the particle. This was easy and clear; every particle just had one result value, independent if it was a sphere, a cylinder, a cube, or any other irregular shape.
The first improvement from one-dimensional to two-dimensional size results came in the year 2000 when PCs got faster, and it was possible to connect every pixel on the particle perimeter to any other pixel and measure and calculate all of these connections.
From there on, it was possible to differentiate between the width and length of that particle image. But this is the crucial point; it was just the length and width of the 2D image and not the particle itself.
When the particle was not seen from its largest projection, the length could be measured too short, and the width of the image could have been the width or the thickness of the particle, depending on the orientation and angle at which the photo was taken.
Microtrac MRB developed the CAMSIZER 3D because measuring the real 3D dimensions is an important step to enhance accuracy and precision. This device is the first to allow the individual particle result to become a true representation of the actual particle in all dimensions.
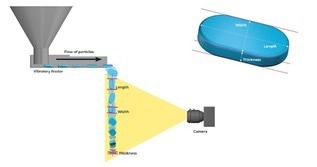
Measurement Principle of the CAMSIZER 3D. Image Credit: Microtrac MRB
What is particle tracking, and what are its benefits?
Imagine a supersonic jet or a survey satellite flying around the globe and taking representative images from many angles. From this, it would then be possible to describe or reproduce a 3D model of Mother Earth. This is the principle of 3D tracking as used in the CAMSIZER 3D; many 2D images can describe a 3D object, two or three orthogonal images cannot.
Particle analyzer Camsizer 3D Function principle - Microtrac MRB
Video Credit: Microtrac MRB
Why is 3D analysis considered a more powerful tool than 2D analysis?
3D analysis is considered a more powerful tool compared to 2D analysis as we now have one more parameter than in conventional 2D analysis, where we are only able to see the length and width of the image. In addition, 3D analysis helps facilitate a deeper understanding of the true dimensions of the particle (true length, true width, and true thickness).
Can you describe the CAMSIZER 3D dual-camera setup?
These two features cover two different subjects.
The CAMSIZER 3D tracking technology measures the particle’s 3 dimensions with a fast camera and over a long travel distance, while the Dual Camera Setup covers a wide measuring range, from 20 µm to 30 mm.
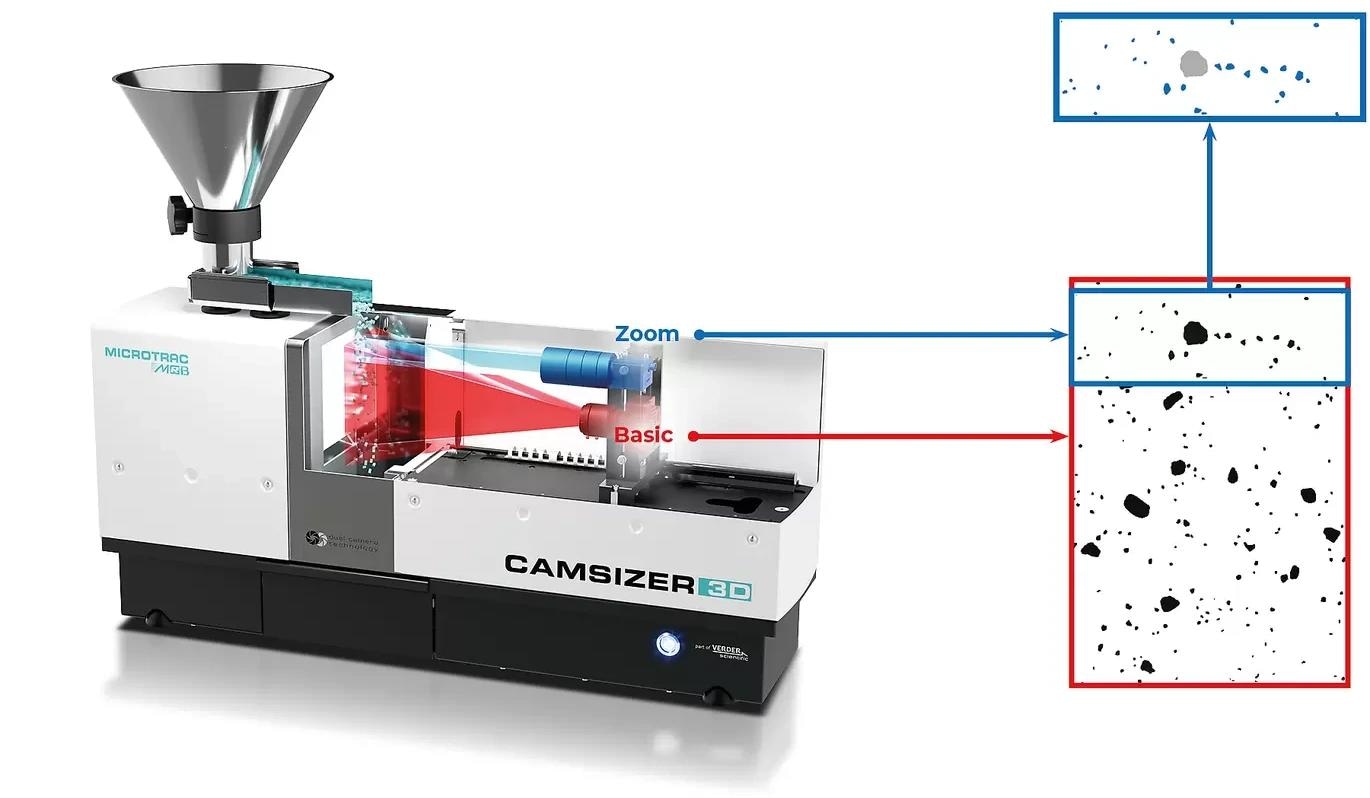
CAMSIZER 3D Features a Zoom and a Basic Camera. Image Credit: Microtrac MRB
What advantages do dual cameras confer in terms of measuring range?
Due to the different magnifications of the camera/lens systems, the Dual Camera Setup offers additional advantages in terms of measuring rage, meaning that it can cover a much wider measuring range, from very small dust particles to larger objects like stones and pebbles than a one-camera system.
What challenges lie ahead in particle analysis, and how can Microtrac help its clients face these?
As more and more sophisticated materials are developed, the demands of regulation to ensure environmental sustainability and general consumer protection will drive manufacturers to provide accurate and transparent data.
Advances in automation and artificial intelligence will also materially alter the workplace, requiring manufacturers of equipment like Microtrac to adapt and deliver “smarter” automated solutions. Data processing, pattern recognition, predictive algorithms will all become more prevalent.
IoT solutions will be deployed to deliver more seamless communication channels and contribute to better equipment reliability and “up-time.” However, Microtrac MRB’s research and development team is well-positioned to meet these challenges.
About Paul Cloake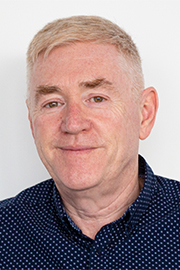
Paul Cloake is currently the Director of Sales at Microtrac MRB. Born in Ireland and educated at University College Dublin, Paul has been involved in the Particle Characterization field for almost 40 years.
About Gert Beckmann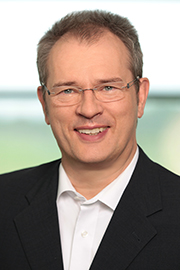
Gert Beckmann is Product Specialist for Dynamic Image Analysis at Microtrac MRB.

This information has been sourced, reviewed and adapted from materials provided by Microtrac MRB.
For more information on this source, please visit Microtrac MRB.
Disclaimer: The views expressed here are those of the interviewee and do not necessarily represent the views of AZoM.com Limited (T/A) AZoNetwork, the owner and operator of this website. This disclaimer forms part of the Terms and Conditions of use of this website.