Interview conducted by Emily MageeJun 19 2023
In this interview, AZoM speaks with Brandon Van Leer, Sr. Product Marketing Manager, and Eric Goergen, Sr. Product Marketing Manager, from Thermo Fisher Scientific, about the new CleanMill Broad Ion Beam System. They discuss the applications and the inspiration behind the creation of the product.
Please can you explain what the CleanMill Broad Ion Beam System is?
Brandon: The CleanMill is a broad ion beam system. This allows people to prepare sample surfaces and cross-sections for a variety of analytical techniques, generally in scanning electron microscopy (SEM).
It also has the ability to do cryogenic polishing, cross-sectioning, or cross-polishing. If you have samples that are really soft or heat up easily, then you can make them cold with the cryo sample holder and then make cross-sections under cryogenic conditions.
Eric: A system like this is a critical piece of electron microscopy in terms of basic sample prep, particularly when looking at advanced materials or any time you need a pristine, clean surface for analysis. This is the type of system that you need to achieve the highest level of success and repeatability possible for that type of analysis.
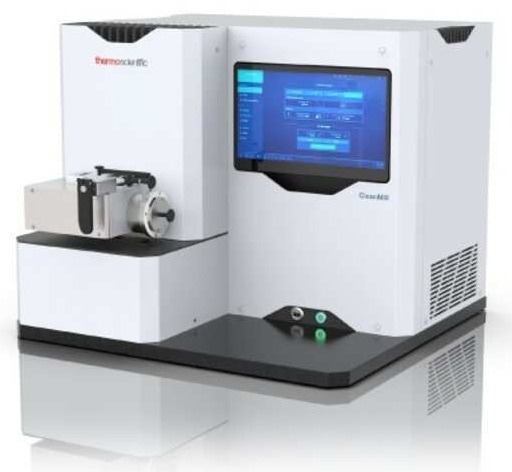
CleanMill Broad Ion Beam System.
Image Credit: Thermo Fisher Scientific
How is the system used, and what can it do?
Eric: The system utilizes a broad ion beam, specifically argon ions that are collimated in a broad beam. The ions interact with a sample to sputter the surface, smoothing out any roughness to create a flat, clean surface.
You can use this to cross-section a sample. If you are looking at a piece of metal or a multi-layered sample and you want to look at the microstructure on the inside, you can cross-section it to look at the different layers.
If you are looking at different types of structures that are multi-phased, for example, you can also do surface polishing. If you are looking at a wide area, you can surface polish the sample and look at a large area with a nice clean, consistent surface.
That is really important if you are doing advanced energy dispersive X-Ray spectroscopy (EDS), and especially if you are doing electron backscatter diffraction. This is another technique that looks at the crystallography of the sample, and it requires a very pristine surface for it to be successful.
When traditionally preparing a sample for SEM, you might mechanically polish it on a very fine sandpaper, but it induces many defects onto the surface. The ion mill helps remove all those defects so that the features you are looking at are the result of a process or a specific material characteristic rather than an artifact from what you did to prepare the sample.
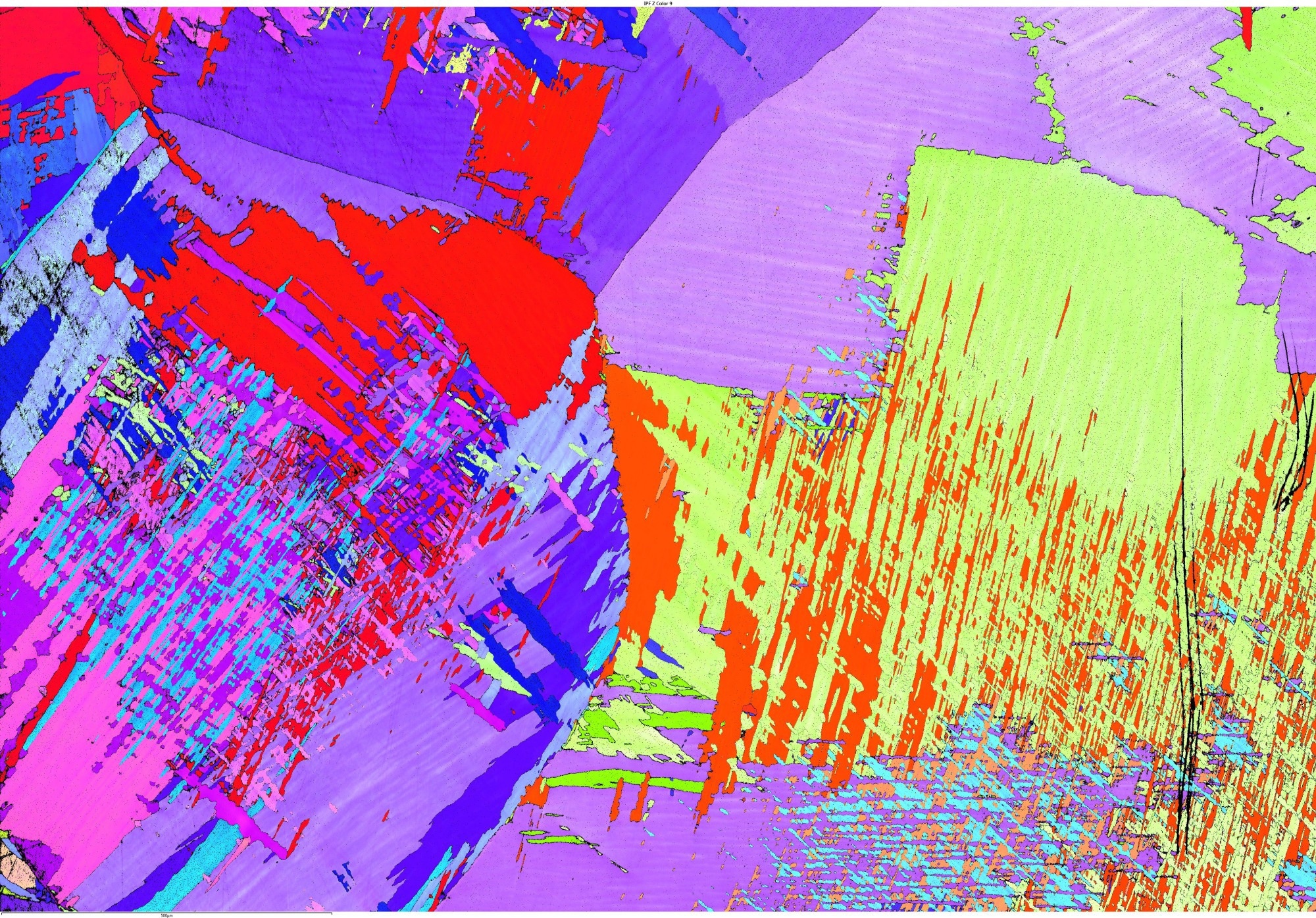
Sample of Ti6Al4V inverse pole figure (IPF) captured with an EBSD detector after CleanMill polishing at 10 kV.
Image Credit: Thermo Fisher Scientific
What inspired the development of the system?
From experience and working closely with our customers in the field, we learned that our customers need something seamless and easy that fits in with all of their needs for sample preparation and sample investigation. That’s why we decided to invest in designing the CleanMill, which can be integrated with our sample transfer devices.
Broad ion beam polishers have been around for almost as long as electron microscopes. So far, we have been relied on third parties, but as newer materials are being developed, this has become such an important part of the microstructural characterization workflow, that we wanted to provide a solution that is more seamless with the rest of our equipment. This was especially important when looking at fast growing industries like lithium-ion batteries. One of the trademarks of these materials being lithium-based is that they are extremely sensitive to air and moisture.
Working with air-sensitive materials is not as simple as prepping a sample and moving them to the SEM because if you expose it to the air, you can start oxidizing the surface before you even get a chance to look at it.
That’s why with CleanMill we now provide a system that is integrated with our Inert Gas Sample Transfer system. This keeps the sample enclosed in argon or a vacuum so that it is not exposed to air.
Please can you explain the workflow?
Brandon: We have an overarching workflow that we call the Thermo Scientific IGST (Inert Gas Sample Transfer) Workflow, which is made possible by CleanConnect.
Let me explain:
In electron microscopy, you have materials that are reactive. They can be reactive with the beam, air, or water, and that hinders you from understanding the fundamental properties or microstructure of the material that you are working in. CleanConnect allows us to move samples from a glove box where there is an inert gas protecting the sample.
That is important for clean energy materials in particular because any exposure to water or air is a problem. If you are in the battery industry and you are doing any sort of research, you will know that argon-filled glove boxes are everywhere to aid with sample preparation.
That is why we developed CleanConnect sample transfer device. This tool integrates with and connects directly to the CleanMill, but it can also connect directly to our SEMs or a glove box, depending on what the customer is doing. The CleanMill is part of an ecosystem that allows us to characterize these materials that would otherwise be contaminated. This workflow keeps air-sensitive samples and materials isolated so that your chances of success are higher.
There are a lot of product names that sound similar. That was intentional because we wanted to let people know that we were working on something that is going to allow them to observe their materials in their native (read: CLEAN) state.
If I want to cut a pen in half, I can use a pair of scissors, then a ceramic slurry, and then polish this so that it is relatively smooth and I can look at it optically. But if I want to look at it in the electron microscope, the surface will still be way too rough for me to get any interesting information about the polymer or about any metal that is inside.
An ion beam takes what optically looks like a very smooth surface and makes it flat.
For example, lithium metal is currently used in the solid-state batteries that are being developed right now and the lithium-ion batteries that are mass-manufactured for our phones and vehicles. You cannot analyze these materials in the air.
You will need a protected environment instead, that allows you to characterize the microstructure. In the case of the IGST workflow, this protected environment is created by argon. Argon is an inert gas, that will not cause a reaction (oxidation) with your sample. You do the initial sample preparation in a glove box, which is a protected environment. Then, you can use CleanConnect to transport the sample to the CleanMill for further preparation if you need an even smoother surface. Note, that not all sample types will require that. In case, you want to look at the sample in its native state, you can also use CleanConnect by transporting the sample straight from the glove box to the SEM. However, most often, people want to prepare cross-sections so that they can see buried features underneath the sample surface, for example, layer thickness.
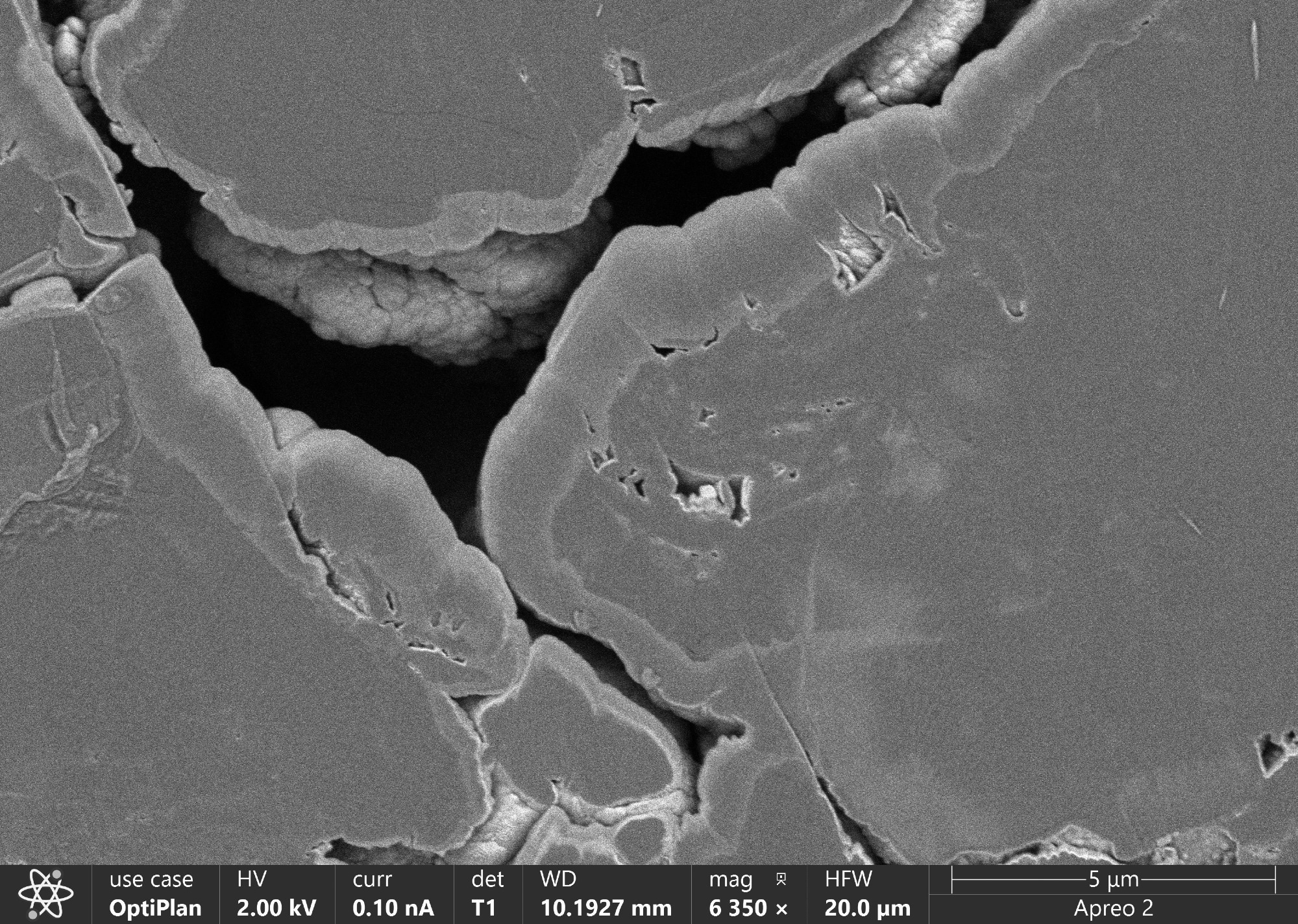
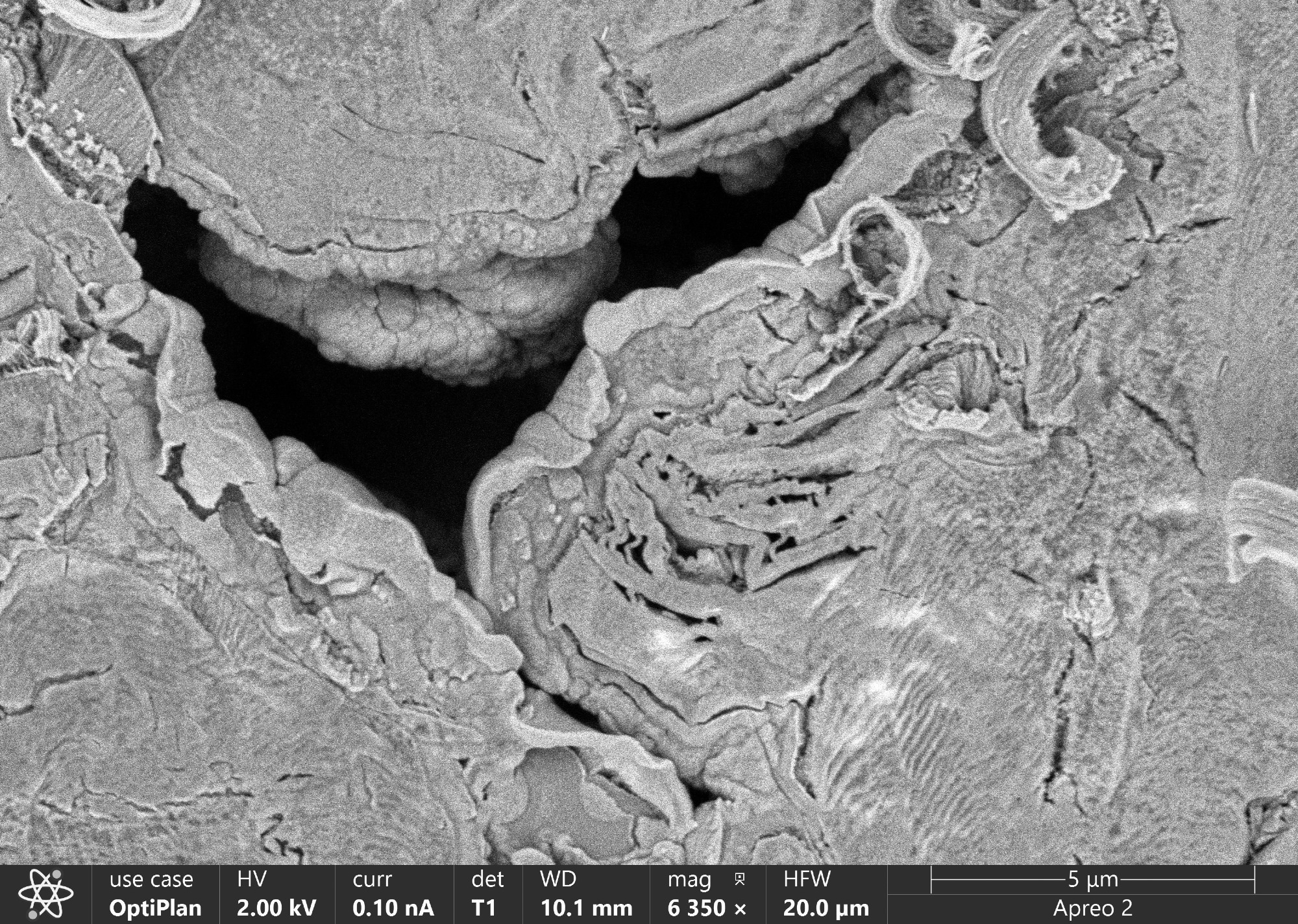
Graphite anode in Li-battery after polishing at 16 kV in CleanMill. First figure was transferred to SEM in CleanConnect. Second figure was transferred in air.
Image Credit: Thermo Fisher Scientific
What industries benefit from the ion polisher?
Eric: A lot of the advanced metals, even aluminum, and some specific super alloys, have very high reactivity to air and water. That is why metal industries would benefit from the ion system.
The CleanMill can be used in a broad range of research/industrial segments as a general-purpose tool. Traditionally, the geoscience sector is a big user of this technique for sample preparation.
Another industrial use is multi-phase ceramics, where you have different hardnesses of materials. This means that when you mechanically polish them, you get height differences because of their different physical properties. The ion mill actually removes those types of artifacts so that you are always looking at a flat surface.
What are some of the maintenance considerations with the system?
Eric: The system is designed to be plugged in, put on a benchtop, and ready to be used with minimal facilities. Regarding maintenance, there is not much to consider for the user. The user can maintain the system themselves. The only part that needs maintaining is the ion-source that needs to be replaced every so often; the interval depends on how much the system is used. Spare parts that go into the ion source are readily available from Thermo Fisher Scientific.
How easy is it to replace those components?
Brandon: It’s quite easy. When customers buy the system they get access to a series of online user videos, both for training and maintenance. You’ll need a few specific tools, like a source holder, but generally, following the videos is straightforward.
We like to consider that most folks who are using scanning electron microscopes are already relatively familiar with replacing a tungsten filament electron source on their own SEM. You’ll need the same skill-set for operating and maintaining a broad ion beam system, since the process is very similar.
If you are a brand-new user, not experienced with any of processes, then having the online videos, instructions, and operating procedures will be of great help.
Where can the users find maintenance tutorials?
Brandon: The goal is to have all the videos available to customers within the system. Additionally, we will offer the videos through a learning management portal that will be ready later in 2023. A physical copy of the videos and the training materials will also come with the CleanMill.
During the development of the system, was there anything that surprised the design team? For instance, did it function beyond expectations?
Brandon: We designed it intentionally for two things. One was for high throughput processing, which is why the design team worked to create a source that goes up to 16 kV. At this moment in the market, CleanMill is the only system that has that high an accelerating voltage for its energy source.
Secondly, to be apart of the Thermo Scientific IGST workflow, to enable preparation and observation of air-sensitive materials. With CleanConnect samples can easily go from the CleanMill straight into a SEM or a dual beam without compromising sample integrity due to air or moisture.
Those were the two key focus areas for us to ensure the product operated well.
Within Thermo Fisher, we already have a huge knowledge base in focused ion beams and electron beams. For us, this was a natural extension in providing a fast, sample preparation solution compatible with our SEM and DualBeam product line.
Eric: The one takeaway that I have seen in the quality of the results that we have been getting is how nice the samples look at the high accelerating voltage of 16 kV.
Typically, with all these types of technologies, like ion-based technologies, the higher the power of the beam, the more artifacts come up because you are milling much faster. There are a lot more chances for some artifacts to form. However, we are seeing solid, consistent results, even when pushing the system to its limits.
From that perspective, that might be one surprise, as people do not normally think of high current processing or high kV processing as providing good results. We observe really nice results, even at the system’s highest ranges.
Are there any future improvements on the horizon?
Brandon: We always have a list of capabilities and new attributes that we would like to bring to our products, but first, we want to see the customer response to this particular solution and let the feedback drive the priority of future improvements to CleanMill.
Have you got any customer feedback so far?
Brandon: Anecdotally, during the webinar, we had someone join who was already pretty far down the evaluation process in looking at broad ion beams. After seeing the technology surrounding Inert Gas Sample Transfer and connectivity to our microscopes, they are now considering the CleanMill.
Even on paper, some of the differentiators we have put forth for CleanMill have been enough to cause interest in the SEM community. This has told us we have been focusing on the right attributes.
Watch the CleanMill Webinar Here
About Brandon Van Leer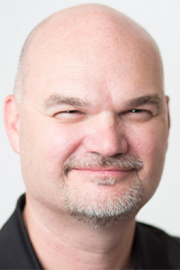
Brandon Van Leer joined Thermo Fisher Scientific in 2004 and has held various positions including Senior Applications Engineer, Applications Manager, and Product Marketing Manager. Currently, he is a Senior Product Marketing Manager for Thermo Fisher Scientific’s emerging analytical instrumentation solutions focused on batteries and clean energy. Brandon’s professional background has focused largely on materials characterization and development of electronic materials and polymers. He has over 27 years’ experience in various analytical techniques and over 20 years exploring SEM and FIB. Brandon’s current research interests are applications development for inert gas sample transfer, cryo-plasma FIB and multi-ion source plasma FIB for air and beam sensitive materials. Brandon received his BS in Physics (1998) and his MS in Electrical Engineering (2002) from Oregon State University. He is a member of MSA, MRS and IEEE.
About Eric Goergen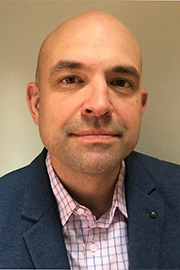
Dr. Goergen first joined Thermo Fisher Scientific eleven years ago as a research scientist and is currently a senior product marketing manager for SEM solutions. He has a Ph.D. in geology and geophysics from the University of Minnesota and over 20 years of experience using electron microscopy for microstructural analysis, EDS, and EBSD applications. He holds multiple patents in EDS acquisition and visualization techniques and deep experience using broad ion beam systems for advanced surface preparation.
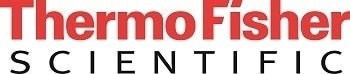
This information has been sourced, reviewed and adapted from materials provided by Thermo Fisher Scientific – Materials & Structural Analysis.
For more information on this source, please visit Thermo Fisher Scientific – Materials & Structural Analysis.
Disclaimer: The views expressed here are those of the interviewee and do not necessarily represent the views of AZoM.com Limited (T/A) AZoNetwork, the owner and operator of this website. This disclaimer forms part of the Terms and Conditions of use of this website.