In 2008, during his recovery from a broken ankle, Alex Berry, the Founder and Engineering Director of Sutrue, conceived the notion of an automated suturing device tailored for minimally invasive surgery.
This surgical approach reduces patient recovery periods, improves outcomes, and decreases complications. Nevertheless, the dearth of suitable instruments for these intricate and precise tasks hampers surgeons in providing minimally invasive options to their patients.
Sutrue, with its dedicated focus on keyhole surgery encompassing both laparoscopic and robotic procedures, has developed a minimally invasive suturing device. Surgeons are entrusted with the vital responsibility of suturing, yet the absence of an instrument capable of achieving the requisite scale for minimally invasive surgeries (8 mm diameter) persists.
Sutrue's innovative design tackles this void by emphasizing extreme accuracy in the compact size of its prototype devices.
Suturing for Minimally Invasive Surgery
After years of research and experimenting, Berry’s team designed a device that passes a suturing needle and thread through tissue and returns to the device securely.
The needle rotates out and back into the device on a fixed path while staying level on the third axis. The team had prototypes of the device machined from steel, which required significant time and help accommodating design iterations.
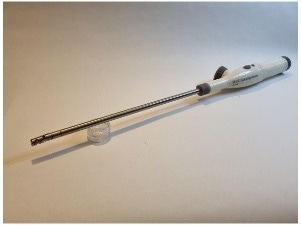
Sutrue's device machined from steel. Image Credit: Boston Micro Fabrication (BMF)
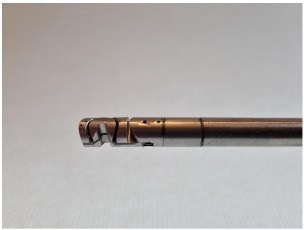
Sutrue's device machined from steel. Image Credit: Boston Micro Fabrication (BMF)
Prototyping the Device
During the development of the suturing device, Berry's team encountered an obstacle related to the stability of the needle's path, which necessitated an update to one of the most crucial device components. Reproducing the part via machining would have caused a considerable delay in product testing by several months and incurred significant expenses.
The machining process presented another limitation as the team would receive only one replacement design, leaving no room for experimentation.
By utilizing 3D printing technology to manufacture the replacement parts, the team could swiftly test various versions of the part with slight differences and determine various tolerances within a shorter timeframe.
The 3D printing approach allowed the team to consider the parts' aesthetics, resulting in the printing of the parts in two distinct colors.
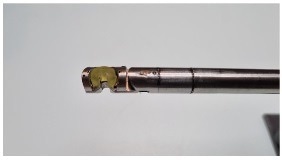
Sutrue's device with the 3D-printed component. Image Credit: Boston Micro Fabrication (BMF)

3D-printed component to stabilize the needle path. Image Credit: Boston Micro Fabrication (BMF)
The accuracy of BMF printers at small scale means that we could try three different parts to find the ideal fit. This allowed for our device to finally function as designed without the cost and time delay of machining the part. This has led to us being able to do initial testing and advance the development of a unique medical device with the assurance that the BMF printed parts are true to the design and consistently accurate.
Alex Berry, Founder and Engineering Director, Sutrue
Continuing Advancements for Minimally Invasive Surgery
Ongoing progress in medical devices is set to further enhance the accessibility of minimally invasive surgery.
The capacity to fabricate prototypes through 3D printing, with resolutions, sizes, and tolerances comparable to precision injection molded components, offers extensive prospects for advancements in the instruments essential for minimally invasive procedures.
3D Printing an Innovative Suturing Device for Minimally Invasive Surgery
Watch the suturing device in action. Video Credit: Boston Micro Fabrication (BMF)
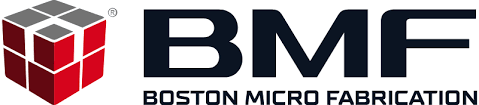
This information has been sourced, reviewed and adapted from materials provided by Boston Micro Fabrication (BMF).
For more information on this source, please visit Boston Micro Fabrication (BMF).