Superior cost-to-performance ratio, resilience, and versatility are the core reasons behind the success of polymers in every major field. However, their inherent properties need to be modified as per requirements, which is done via the integration of additives and fillers.
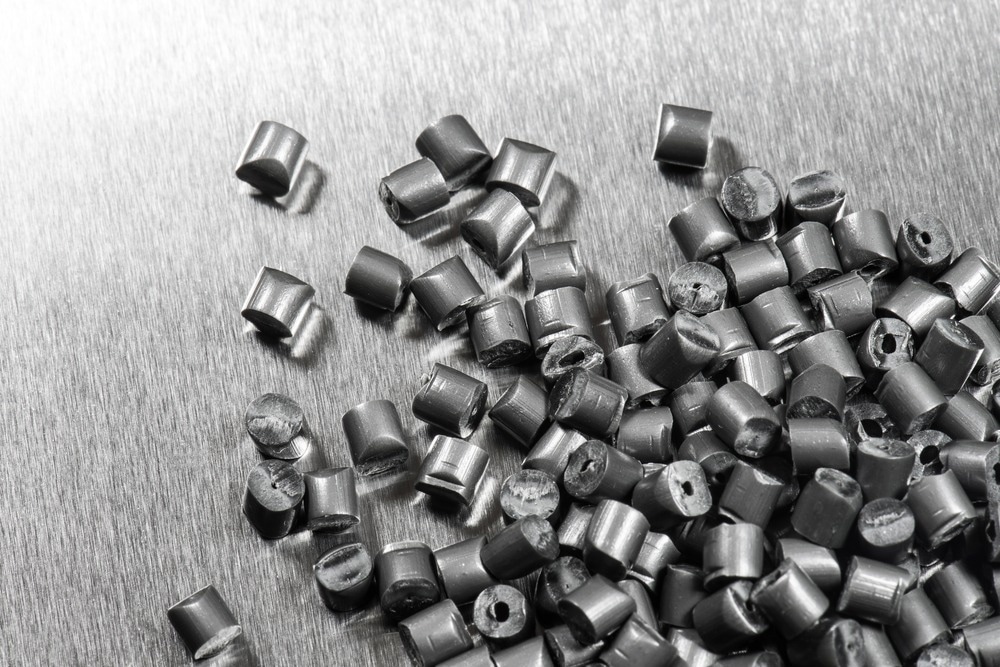
Image Credit: XXLPhoto/Shutterstock.com
Additives constitute a substantial category of chemical compounds integrated into the polymer matrix before or during processing. Plastics can be manufactured with additives that improve particular attributes such as biodegradability resistance or accelerant, physical characteristics, and mechanical durability. Fillers are stable compounds that can be incorporated into polymers to improve their properties or reduce their cost. Various varieties and configurations of these materials have been added to the polymer based on the specifications. This article focuses on how different types of fillers and additives affect the properties of polymers.
How do Antioxidant Additives Affect Polymers?
Polymers can be manufactured with additives that boost properties such as decomposition resilience or accelerant, physical characteristics, and mechanical durability. Antioxidant compounds, emulsifiers, antistatic substances, antifogging agents, lubricating agents, plasticizers, and solvents are famous examples of additives.
As per an article published in the journal Polymers, antioxidants (AO) are compounds that prevent oxidation or impede oxygen-driven reactions. Efficient AOs, such as phenols and amines that have been chemically retarded, are radical eliminators that inhibit reactive chain reactions. The primary benefit of AOs is to safeguard polymers and composites from heating and photo-oxidative reactions that occur throughout their natural aging.
AOs include a variety of substances that may hinder or prolong the oxidative breakdown of polymers by interfering with oxidation reactions. To avoid or mitigate the oxidative decomposition of polymers, many additive classes have been devised.
How do Antistatic Agents as Additives Effect Polymers?
Antistatic additives are incorporated into polymers to sacrifice some conductive properties to prevent or reduce the buildup of electrostatic charges in the ultimate polymer material. This electric charge buildup can make polymers susceptible to static hold, electrical discharges, and particle adhesion.
In addition to their biodegradability, sustainability, and durability, bio-based additives have piqued the research community's curiosity. Silk fibroin/chitosan microspheres (SFCM) and low-temperature nitrogen plasma (LTNP) have been utilized to improve the antibacterial and antistatic properties of polyethylene terephthalate (PET) fabrics.
An article published in the journal Polymer Testing focuses on ionic liquids (ILs) as antistatic additives. Their investigation of antistatic substances has been one of the fastest-growing disciplines in polymer chemistry and industry, primarily due to their distinctive characteristics. In general, ILs are defined as ions with melting points below 100oC.
Some polymers' antistatic abilities have been substantially enhanced by melting ionic liquids. Specialists employed ionic liquids as antistatic agents for a variety of polymers. The alteration of polymers, such as poly-methacrylate, using a variety of ionic solvents. The authors also succeeded in fixing hydroxyl-containing ILs in the Polyurethane (PU) matrix by polymerizing PU in the presence of hydroxyl-containing ILs. Not only did it aid in reducing electrostatic charge, but it also guaranteed transparency.
How do Plasticizer Additives Effect Polymers?
Plasticizers are among the most common additives used in the manufacturing of polymeric materials. Typically, they are liquid and inert organic substances. They can enhance the adaptability, flexibility, and processing ability of plastics and elastomers when added to them.
These improvements are the result of the plasticizer's solubility in the polymer, which may also reduce the modulus of elasticity or glass transition temperature of the final product.
Increasing the plasticity of material is frequently needed for the manufacturing of plastic goods and/or packaging, as well as epoxy compounds.
Graphene as Flame-Retarding Additive
The aforementioned article published in the journal Polymers focuses on expandable graphite (EG) and graphite (G) as multifunctional additives for boosting flame retardancy and thermal conductivity. Expandable graphite, like graphite, is composed of layered graphene platelets. When subjected to heat, the layers are pushed apart, producing structures resembling worms.
Expandable graphite exhibited superior flame retardant properties for thermally conducting polymeric materials. In cone calorimeter experiments, the thermal conductivity had no impact on the combustion features observed. A mixture of graphite and expandable graphite could be a viable option for accelerating the creation of thermally conductive polymers requiring high flame retardancy classifications.
How do Natural Fillers Effect Polymers?
In the Journal of Natural Fibers, a new article focuses on the utilization of natural fillers. Rice husk (RH) is an intriguing cellulose-based biodegradable filler that is derived from agrarian products' byproducts. The inclusion of additives in high concentrations increases the proportion of hydroxyl (OH) groups in RH-based composites, thereby enhancing the hydrogen bonding with water molecules.
Coconut shell additives are byproducts of agriculture comprising approximately 36–43% cellulose and 0.15–0.25% lignin. These additives can be used to generate active carbon, and their inclusion of lignocellulose in polymer composites has a strengthening effect.
Eggshells are organic byproducts of the culinary industry that are considered refuse and have no commercial worth on the market. Due to their high calcium content, they are also known as calcium filling. The attributes of 5% and 10% eggshell powder (ESP) filled polymer matrix composites were investigated. The bending stress was elevated for composites containing 5% ESP.
Peanuts are one of the most essential culinary goods, and their shells, which are comprised of cellulose, are obtained after their extraction. Studies on the inclusion of Peanut shell powder (PSP) into natural rubber revealed an increase in minimum and maximum torque but a decline in physical characteristics. The properties of the vulcanized composite with 10% infill were superior.
Nano additives such as graphite, graphene oxide, and Nano clay could be combined with various polymer matrices to produce automobile and aerospace components. Nanofillers improve the thermal processing, mechanical, and electrical attributes of polymer matrix composites.
How do Fillers Modify the Mechanical Attributes of Inverse Vulcanized Polymers?
Polymer Chemistry hosts an article focusing on the improvement of tensile characteristics of vulcanized polymers by incorporation of fillers. The alteration of inversely vulcanized polymers with additives, especially liquid metals such as gallium and gallium–zinc eutectic alloy, is renowned. These substances enhanced the breaking strength and electrical conductivity of the polymers. The incorporation of 20.95 wt. % liquid metals increased the yield strength from 0.25 MPa to 0.59 MPa.
Carbon Black (CB), cellulose microfibers (CMF), and Nano clay (NC) were utilized by the researchers. At 10 wt. % loading, all supplements produced the greatest increase in tensile stress, which also led to an increase in durability. These additives are advantageous for vulcanized polymers.
Effect of Synthetic Fillers on Polymer Composites
The Journal of the Textile Institute has an article stating that synthetic fiber-reinforced composites have more desirable material properties than natural fiber composites. Silicon carbide (SiC) is an industrially applicable synthetic additive with excellent tensile, electrical, and thermal attributes. Its abrasive nature is crucial in the production of abrasive wheels and the creation of high-wear objects. Examining SiC particles with jute-reinforced epoxy composites typically reveals an 8% and 15% increase in tensile and flexural strength, respectively.
As a result of its remarkable durability, Al2O3 particulates are frequently utilized in polymer matrix and metal matrix composites. Al2O3 particulates in epoxy at concentrations ranging from 0.5 to 2.0 wt%, with increments of 0.25%, increase the Ultimate Tensile Strength, Young's modulus, and toughness values by 27.6%, 18.9%, and 187.9%, respectively.
Boron carbide is among the lightest materials available. This ceramic substance with increased wear resistance and abrasion resistance is used in composite applications requiring a lightweight. The increased toughness and low-density result in a variety of applications. The incorporation of these particles into a polyester matrix enhances the composite's rigidity while having a lesser influence on its longitudinal properties. Boron carbide particle incorporation in the matrix results in thermal stability.
Graphite is an anti-friction, resilient to-wear substance and is, therefore, appropriate for polymeric applications. By incorporating these tiny particles into a matrix substance, both the tensile and exterior characteristics are enhanced.
In short, additives and fillers are both essential for the modification of polymeric materials. Extensive research is being done all over the world for the development of novel additives, with market demands to increase shortly.
More from AZoM: The Role of Composites in Aerospace Engineering
References and Further Reading
Almeida S. et. al. (2023). A Brief Evaluation of Antioxidants, Antistatics, and Plasticizers Additives from Natural Sources for Polymers Formulation. Polymers. 15(1):6. Available at: https://doi.org/10.3390/polym15010006
Tomiak F. et. al. (2022). Expandable Graphite as a Multifunctional Flame-Retarding Additive for Highly Filled Thermal Conductive Polymer Formulations. Polymers. 14(8):1613. Available at: https://doi.org/10.3390/polym14081613
Kosinski et. al. (2022). Ionic liquids as antistatic additives for polymer composites – A review. Polymer Testing.112. 107649. Available at: https://doi.org/10.1016/j.polymertesting.2022.107649
Siengchin et. al. (2022). Effect of natural filler materials on fiber reinforced hybrid polymer composites: An Overview. Journal of Natural Fibers. Available at: https://doi.org/10.1080/15440478.2020.1854145
Praveenkumara. J. et. al. (2022). A comprehensive review on the effect of synthetic filler materials on fiber-reinforced hybrid polymer composites, The Journal of The Textile Institute. Available at: https://doi.org/10.1080/00405000.2021.1920151
Hanna, V. et. al. (2022). Incorporation of fillers to modify the mechanical performance of inverse vulcanised polymers. Polymer Chemistry, 13(26), 3930-3937. Available at: https://doi.org/10.1039/D2PY00321J.
Disclaimer: The views expressed here are those of the author expressed in their private capacity and do not necessarily represent the views of AZoM.com Limited T/A AZoNetwork the owner and operator of this website. This disclaimer forms part of the Terms and conditions of use of this website.