Natural fibers have a rich history of reinforcing materials for over 3,000 years. The renewed interest in natural fiber composites in the last five years is driven by a focus on improving and stimulating rural economies, reducing dependence on petroleum-based materials, and adopting responsible practices for managing materials at the end of their service life.
Natural fiber composites not only offer advantageous properties at a lower manufacturing cost; they also aid in reducing the production of greenhouse gases and preserving the environment.
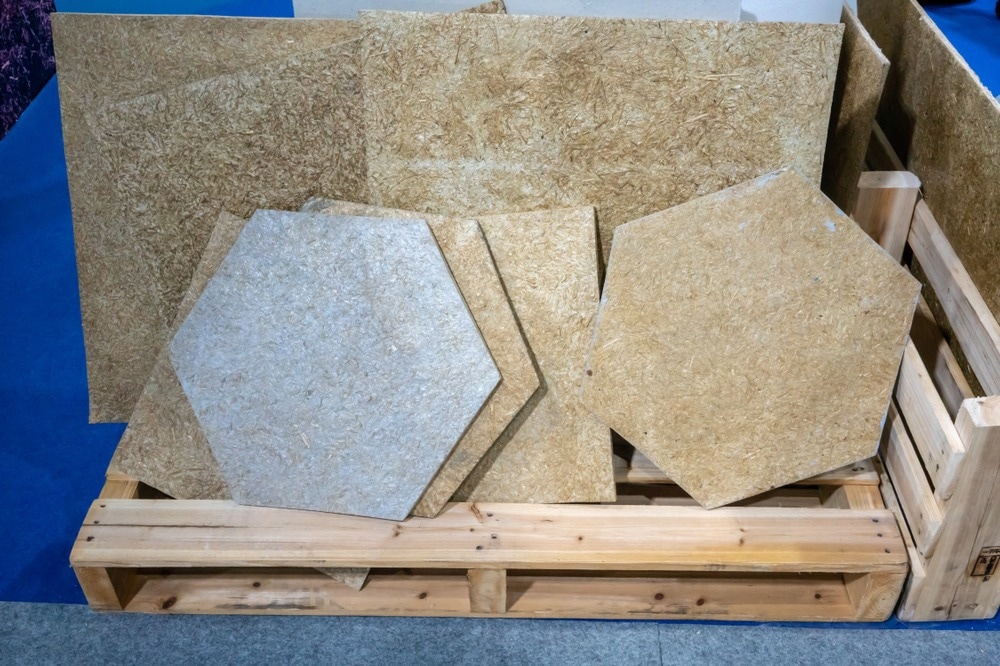
Image Credit: v74/Shutterstock.com
What are Natural Fiber Composites?
Scientists all over the world are devising efficient methods of reducing energy consumption and using materials that offer better properties than conventional industrial elements. Composites have been the center of attention for quite some time as they can be modified as per the application requirements.
A research article in Materials Today: Proceedings states that the modification of composite properties for high-strength applications is usually done using the common practice of reinforcement, typically accomplished by adding fillers or fibers. Natural fibers are obtained from natural resources such as bark and branches of trees and other organic sources. The addition of such natural fibers leads to the composite being environmentally friendly and significantly reduces manufacturing costs, as natural fibers are usually abundantly present in the environment.
Natural Fiber Composites: A Preferred Choice for Automotive Applications in Recent Years
In the current era of Manufacturing 4.0, the focus is on sustainability, automation, and efficient manufacturing. Almost all industries are researching the utilization of sustainable materials as a substitute for traditional components.
The automotive industry has seen a trend of focusing on natural sources of materials. In this context, natural fiber composites are gaining prominence. Utilizing composites based on natural fibers in different components of an automobile has the potential to achieve a weight reduction of up to 34%; as mentioned by an article published in Engineered Sciences.
Natural flax fiber is being used to make the hood of modern vehicles, and research studies involving structural analysis have rendered it safe and durable. Mechanical tests on the hybrid natural composite, comprising coir and carbon fiber reinforced with epoxy resin, suggest the feasibility of using multiple fibers for constructing bike helmet covers, car floors, and roofs.
The design and analysis of a vehicle bonnet utilizing flax fiber reinforced with a vinyl ester matrix composite material reveal a 30% reduction in weight compared to a steel bonnet. The luxury car brand Audi is incorporating flax and sisal fibers in the production of door trim.
Natural Fiber Composites are Being Used in Bullet Proof Vests
National Armed Forces personnel require essential personal protective equipment, including bulletproof vests, in battlefield scenarios. The material within these vests is crucial for minimizing the kinetic energy resulting from projectile penetration. As an alternative to composite materials, natural fibers can be employed as a substitute for Kevlar fibers in these vests. This significantly reduces the manufacturing cost while maintaining the same level of security.
Researchers from Indonesia published an article in Defense and Security Studies highlighting the importance and effectiveness of five natural fibers in composite material to be used for bulletproof vest applications. Pineapple leaf fiber, water hyacinth fiber, salak frond fiber, hemp fiber, and bamboo fiber were analyzed by researchers based on the National Institute of Justice (NIJ) standard.
The research team performed experimental testing by firing bullets at a specific velocity from a specified distance to determine the effectiveness of natural fibers in bulletproof vest application. The pineapple leaf fiber was used with varying thicknesses of 10mm, 15mm, and 20mm. The test was performed for each type of vest, and the results indicated that the bullet penetrated the vest.
The depth of penetration was 58 mm, 10 mm, and 4 mm, respectively. These values were within the dangerous limit, exceeding the thickness of the vest and causing harm to the personnel.
The defense standard specifically states that the bullet should not be able to penetrate the thickness of the vest. In case of penetration, the vest has failed and can’t be used by military personnel—alternative material for bulletproof vests. So, the pineapple lead fiber can’t be used to make bulletproof vests.
The same test was performed for the remaining four natural fiber composites. The bullet was not able to penetrate the bulletproof vest. This demonstrated that the bamboo, hemp, water hyacinth, and salak fibers had exceptional tensile properties and impact strength. Hence, these materials are safe to be used in bulletproof vests.
Natural Fiber Composites: Revamping the Construction Industry
Traditionally, cement and concrete were used all over the world for construction. However, recent scientific progress has led to the development of materials with enhanced thermal and mechanical properties. These materials, called bio-composites, are made from natural fibers, and they reduce the carbon footprint of the buildings significantly. Bio-composites fall into two categories: structural and non-structural natural composites.
The structural composite type is suitable for robust applications like bridges, while the latter finds use in sliding doors, panels, exteriors, and windows.
As per the article published in Results in Engineering, these materials offer excellent thermal and sound insulation, serving as eco-friendly alternatives to traditional construction materials like plastic or metal. They are particularly advantageous for reinforcing thin-walled structures, contributing to the principles of eco-design. Bamboo, sisal, and coir fibers are examples of natural elements used in these composites for various construction purposes, particularly for roofing purposes.
Additionally, Natural Fiber fiber-reinforced composites (NFRC) find diverse applications in the building and furniture industries, as highlighted by the research published in Polymers. These composites are employed in the production of door frames, windows, floor matting, partitions, and ceilings.
Furthermore, they contribute to the manufacturing of furniture items like tables, chairs, and kitchen tools. In addition to the exceptional durability, products made from NFRC are also aesthetically pleasing and very elegant.
A New Discovery
Researchers are working to discover and develop new natural fibers to make novel high-quality composites for industrial applications. A research team has published a study in Heliyon focusing on the development of a new cellulose-rich natural fiber. The natural fiber was extracted from the bark of the jack tree.
The team performed standard tests and soxhlet extraction techniques to determine the chemical composition of the fiber. The new fiber was rich in cellulose as the test revealed the concentration consisted of α-cellulose to be approximately 79.32%, along with 8.01% of hemicellulose present in the fiber. The concentration of lignin was found to be 6.77%, while ash was present in trace amounts.
The team used standardized X-ray diffraction analysis to determine the crystalline properties of the fiber. The crystalline level of the fiber was 89%.
FTIR analysis confirmed the presence of expected functional groups. Thermogravimetric analysis was performed to determine the thermal attributes, especially the thermal stability of the fiber. The maximum amount of degradation for the fiber occurred at a very high temperature of 358°C. These properties make the new fiber suitable for various applications, including reinforcement in composites, textiles, cellulose nanomaterials, activated or conductive carbon, and biomaterials.
In short, the scientific community is focused on using natural fibers to achieve the sustainable development goals. The use of natural fiber composites will lead to a significant reduction in global warming and decrease the supply chain issues for various industries, such as the automobile industry.
More from AZoM: How are Bioplastics Made?
References and Further Reading
Dasore, A. et. al. (2022). An overview of refinements, processing methods and properties of natural fiber composites. Materials Today: Proceedings, 49, 296-300. Available at: https://doi.org/10.1016/j.matpr.2021.02.103
Naik, V., & Kumar, M. (2021). A review on natural fiber composite material in automotive applications. Engineered Science, 18, 1-10. Available at: http://dx.doi.org/10.30919/es8d589
Aminudin I, et. al. (2023). “Potential of natural fiber composite materials for bulletproof vest applications”, Defense and Security Studies, vol. 4, pp. 8–14, Available at: https://doi.org/10.37868/dss.v4.id222
Elfaleh, I. et. al. (2023). A comprehensive review of natural fibers and their composites: an eco-friendly alternative to conventional materials. Results in Engineering, 101271. Available at: https://doi.org/10.1016/j.rineng.2023.101271
Kamarudin H, et al. (2022). A Review on Natural Fiber Reinforced Polymer Composites (NFRPC) for Sustainable Industrial Applications. Polymers. 14(17):3698. Available at: https://doi.org/10.3390/polym14173698
Hossain, S. et al. (2022). A low-density cellulose rich new natural fiber extracted from the bark of jack tree branches and its characterizations. Heliyon, 8(11). Available at: https://doi.org/10.1016/j.heliyon.2022.e11667
Disclaimer: The views expressed here are those of the author expressed in their private capacity and do not necessarily represent the views of AZoM.com Limited T/A AZoNetwork the owner and operator of this website. This disclaimer forms part of the Terms and conditions of use of this website.