Flow Imaging Microscopy (FIM), also referred to as Dynamic Image Analysis (DIA), combines the advantages of traditional particle counters with high-resolution imaging to efficiently and expeditiously characterize particle size, concentration, and shape within a liquid sample.
FlowCam, when paired with the VisualSpreadsheet® software, provides more than 40 morphological parameters for each particle, facilitating the identification of various particle types within a heterogeneous mixture.
This comprehensive particle analysis platform, FlowCam, offers an efficient means of obtaining data or verifying information obtained through other particle analysis methods. The utilization of digital images allows for the straightforward identification of particles and emulsions.
How FlowCam Works
The FlowCam imaging analysis system comprises a light microscopy apparatus equipped with a sample flow cell placed in the optical path between the light source and the camera with an objective lens.
During analysis, a sample is introduced via a syringe pump, and the system automatically captures and records images of particles passing through the optics. Subsequently, these microscopic images are analyzed to determine the types of particles present as well as their size, concentration, and morphology.
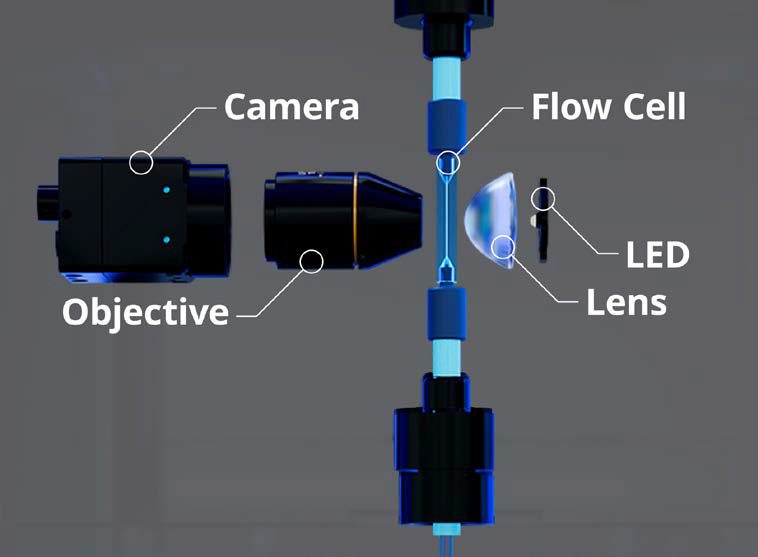
Schematic of the internal components of the FlowCam system. Image Credit: Yokogawa Fluid Imaging Technologies, Inc
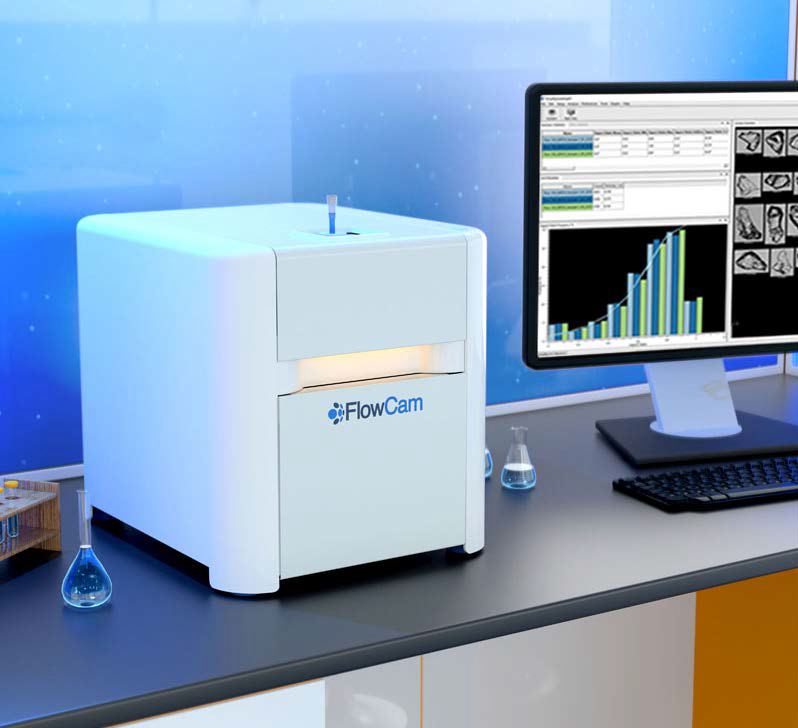
FlowCam 8000 instrument. Image Credit: Yokogawa Fluid Imaging Technologies, Inc
VisualSpreadsheet Particle Analysis Software
Turning Data into Insight
VisualSpreadsheet stands as a powerful and versatile software program for both data acquisition and analysis of images captured with FlowCam. The morphological properties identified by VisualSpreadsheet encompass diameter, area, aspect ratio, circularity, image intensity, average intensity, and transparency.
Furthermore, users can effectively filter and sort particles based on their properties, and the results can be presented in interactive scattergrams or histograms. The software's sophisticated pattern recognition capabilities permit immediate identification and display of particles sharing similar morphology.
Users can create, define, and save particle type libraries, thus enabling a swift comparison of FlowCam data against existing libraries, which facilitates the instantaneous determination of concentrations for specific particle types.
Applications
Food and Beverage Characterization
In the food and beverage industry, the importance of ingredients cannot be overstated. FlowCam offers a valuable capability, enabling users to separate various particle types within heterogeneous mixtures. This ensures the integrity of contents and facilitates the early detection of process flaws.
One key example lies in the analysis of hydrocolloids, such as xanthan gum, guar gum, and pectin. These products play a pivotal role in imparting thickening, stabilizing, texturizing, and other essential properties to foods, beverages, and personal care items.
To achieve optimal results, meticulous attention is given to formulation, production, and packaging processes. Meeting crucial performance characteristics, including dispersibility, hydration rate, and powder flow, heavily relies on understanding individual particle size and shape.
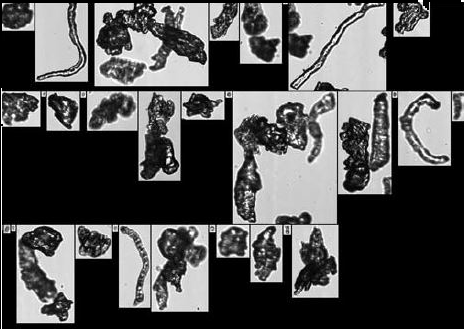
FlowCam images of cellulose particles used in food texturing applications. Image Credit: Yokogawa Fluid Imaging Technologies, Inc
Crop and Soil Sciences
FlowCam finds applications in Agronomy by monitoring the microencapsulation process of fertilizer particles, assessing the presence and monitoring health and growth of soil microbes, mites, forest litter invertebrates, and nematodes, determining seed viability, observing naturally occurring defects in plant development, and analyzing pollen particles and pollen shell capsules.
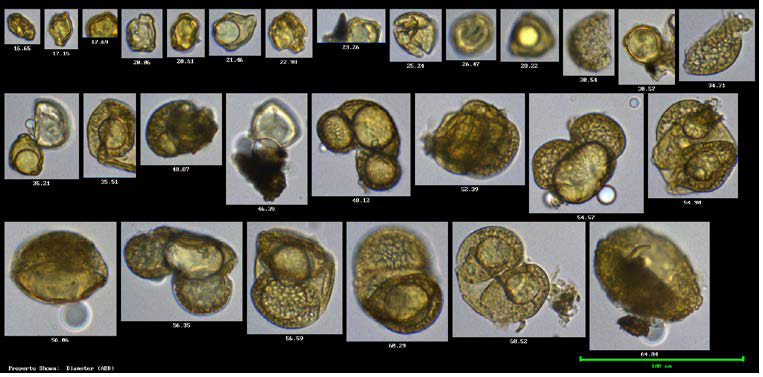
FlowCam images of pollen particles. Image Credit: Yokogawa Fluid Imaging Technologies, Inc
Printer Toner Quality Assurance
The size and shape of printer toner particles significantly impact image resolution and printer efficiency.
Moreover, particle consistency influences the charge distribution they hold, affecting overall image quality. Utilizing FIM for image characterization allows for printer toner particle size, shape, circularity, and material uniformity to be determined during and after production.
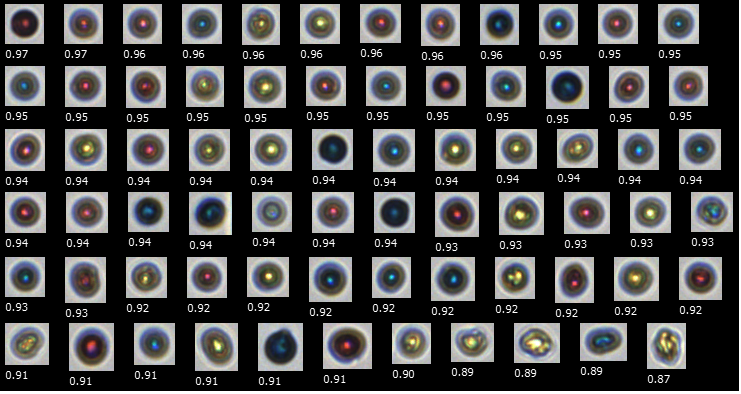
FlowCam images of color printer toner particles. Particles are shown in order of decreasing circularity, where 1 is a perfect circle. Image Credit: Yokogawa Fluid Imaging Technologies, Inc
Microencapsulation Process Analysis
Microencapsulation is a commonly used technique in various applications - from pharmaceuticals to foods to detergents – and the FlowCam imaging particle analyzer offers unique insight into the microencapsulation process.
When studying the effects of temperature, concentration, pH and other variables, FlowCam can dynamically monitor capsule formation over time. This helps to optimize the encapsulation process, allowing companies to yield the most clean coacervate formation.
Offering such insights into the process, FlowCam can be an indispensable tool for microencapsulation R&D and QC applications.
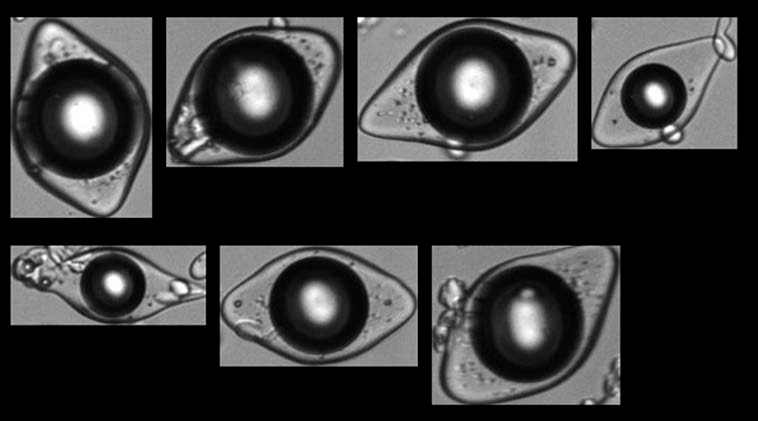
FlowCam images of encapsulated flavor particles. Image Credit: Yokogawa Fluid Imaging Technologies, Inc
Fiber Analysis
Geometry plays a crucial role in determining the performance of fibers across various applications. Factors such as length, width, and curl significantly influence their overall functionality. However, many conventional particle sizing methods struggle to accurately capture the morphology of these fibers.
FlowCam can be used to help streamline and expedite the analysis of fibers.
By incorporating integrated fiber morphology parameters like geodesic length, geodesic thickness, fiber straightness, and fiber curl, FlowCam provides highly accurate and reliable data compared to volumetric-based techniques. Moreover, it offers substantial time savings over manual microscopy.
An added advantage lies in the option to construct custom filters within VisualSpreadsheet. This capability enables instantaneous reporting of results upon completion of sample analysis, thereby saving users valuable time and effort while assessing fiber quality.
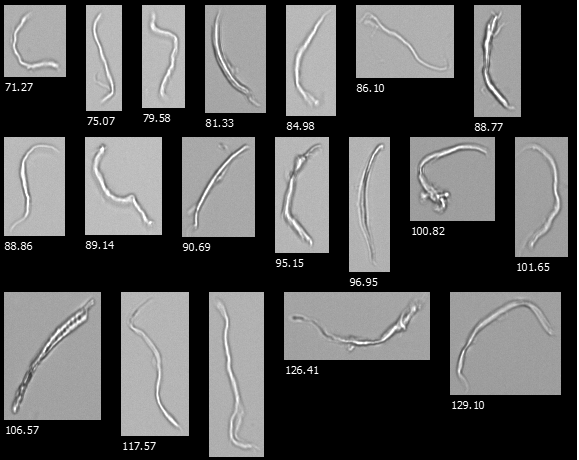
FlowCam images from a cellulose microfibril sample. Image Credit: Yokogawa Fluid Imaging Technologies, Inc
Characterization of Superabrasives
Superabrasives, such as micronized diamonds and cubic boron nitride (CBN), are crucial for cutting, grinding, and drilling hard materials. However, the effectiveness of a superabrasive material in a specific application is entirely dependent on particle size and shape.
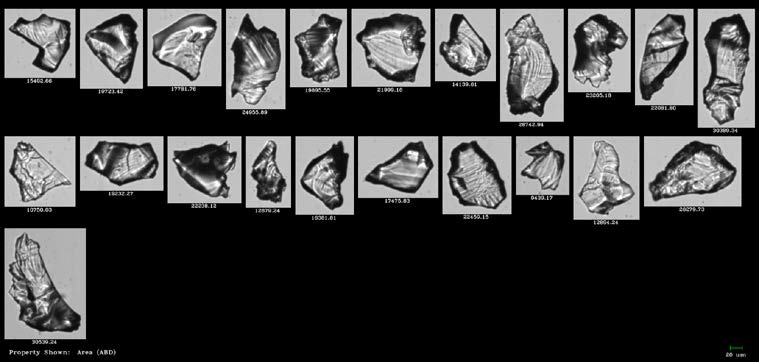
FlowCam images of zeolite particles. Image Credit: Yokogawa Fluid Imaging Technologies, Inc
FlowCam's ability to characterize thousands of particles per minute allows for quick and easy determination of whether a batch of superabrasives meets desired specifications. This process is significantly more time-consuming when performed manually through microscopy, with less statistical significance in results.
Wash Water: Heterogeneous Sample Analysis
In numerous applications, the analysis of heterogeneous samples is essential for characterizing the types and quantities of particles within them. For instance, in the context of washing electronic devices after manufacturing, the water used for this purpose undergoes analysis to identify the particles present.
Devices are washed to remove traces of fibers, metals, and plastics that could remain from the manufacturing process, and it is important that the wash water contains less than a certain number of each of these particle types. Too many leftover particles could cause failures.
FlowCam simplifies the sorting and filtering of particle data, streamlining the process of building libraries that automatically quantify and characterize each particle type.
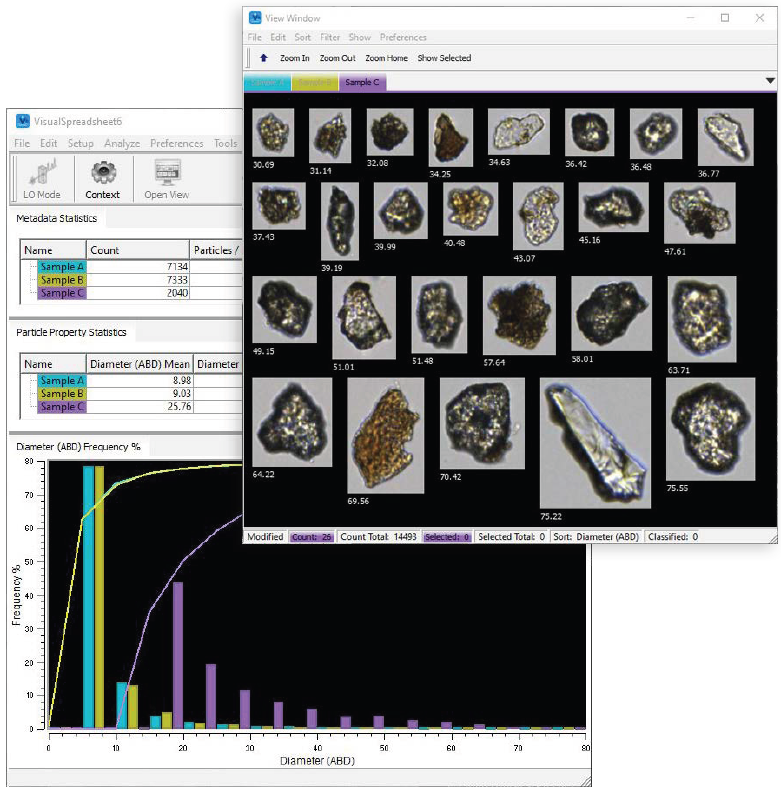
VisualSpreadsheet user interface showing particle data and images of various particle types in a heterogeneous sample. Image Credit: Yokogawa Fluid Imaging Technologies, Inc

This information has been sourced, reviewed and adapted from materials provided by Yokogawa Fluid Imaging Technologies, Inc..
For more information on this source, please visit Yokogawa Fluid Imaging Technologies, Inc.