Soft lithography facilitates the fabrication of intricate three-dimensional patterns and structures at both microscale and nanoscale dimensions. Diverging from photolithography, a technique commonly employed within the semiconductor industry, soft lithography specializes in the production of microfluidic devices, microarrays, and microelectromechanical systems (MEMS).
The “soft” in soft lithography refers to the mechanically soft materials such as polydimethylsiloxane (PDMS) used to produce a mold or stamp.
How Does Soft Lithography Work?
During soft lithography, a master mold with the desired microscale or nanoscale pattern is fabricated. This pattern is generated using computer-aided design (CAD) software, and conventional microfabrication methods are employed in the production of the master mold.
Among these fabrication techniques is photolithography, which employs light to etch features, and electron beam lithography, which crafts patterns using an accelerated stream of electrons. Nanoimprint lithography is the best option if you are looking to attain nanoscale features.
It is crucial to emphasize that the master mold for soft lithography is not constructed from PDMS. Instead, it is typically composed of a light-sensitive material like chrome-coated glass.
During the photolithography process, this photosensitive material loses its resistance to etching upon exposure to light. A photomask with transparent areas allows light to shine through to produce the desired pattern. In other words, the photomask determines where the light shines onto the chrome-coated glass and, in turn, where patterns are etched.
Subsequently, a liquid polymer like PDMS is carefully poured into the etched channels or areas of the master mold and is left to cure, usually at an elevated temperature of approximately 70 °C.
Once the PDMS has hardened, it is separated from the mold. This PDMS stamp, as it is known, carries the reverse pattern of the master mold and is pressed onto the target substrate. The pattern is applied through physical contact, capillary action, bonding, or other surface actions. A variety of different substrate materials, including glass slides, can be used for this.
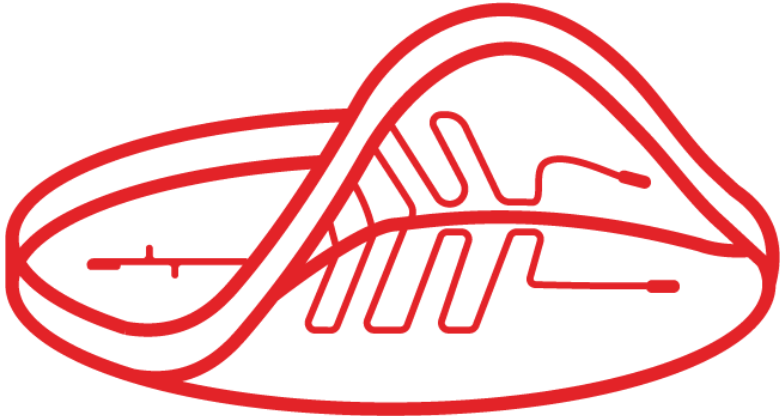
CAD Drawing of a PDMS Mold. Image Credit: Boston Micro Fabrication (BMF)
How Soft Lithography Compares to 3D Printing
Similar to soft lithography, 3D printing can fabricate structures at both microscale and nanoscale dimensions. However, a notable distinction arises in the fact that numerous 3D printers primarily cater to the macroscale.
3D printing also shares similarities with photolithography, which is commonly used with soft lithography. Both photolithography and resin 3D printing, a group of 3DP technologies, make use of a light source and a polymer. However, that is where the similarities end.
In soft lithography, material is removed to create features such as microchannels. In a subsequent step, a liquid polymer such as PDMS is poured into these channels and is left to cure, typically via the application of heat.
By contrast, resin 3D printing adds, rather than subtracts, material. The material that is added is a polymer, but this polymer cures or hardens with the application of light rather than heat. In addition, this photosensitive polymer is added one layer at a time rather than poured all at once.
There is not just one type of resin 3D printing, however. Members of this technology family include stereolithography (SLA), digital light processing (DLP), and projection micro stereolithography (PµSL).
SLA and DLP tend to be used for macroscale rather than microscale and nanoscale applications. Conversely, PµSL technology from Boston Microfabrication (BMF) is designed for microscale 3D printing. For applications such as microfluidics, BMF’s microArch® series of 3D printers can replace soft lithography.
Soft Lithography Vs. PµSL 3D Printing
In contrast to soft lithography, PµSL 3D Printing utilizes a machine rather than a master mold and a press for a PDMS stamp. Furthermore, this type of resin 3D printing excels in generating intricate 3D channels, often surpassing the capabilities of soft lithography.
As well as achieving high accuracy, precision, and resolution, PµSL 3D printing overcomes the challenge of using soft lithography to cut microscale features into layers and then bond these layers together to create one functioning device.
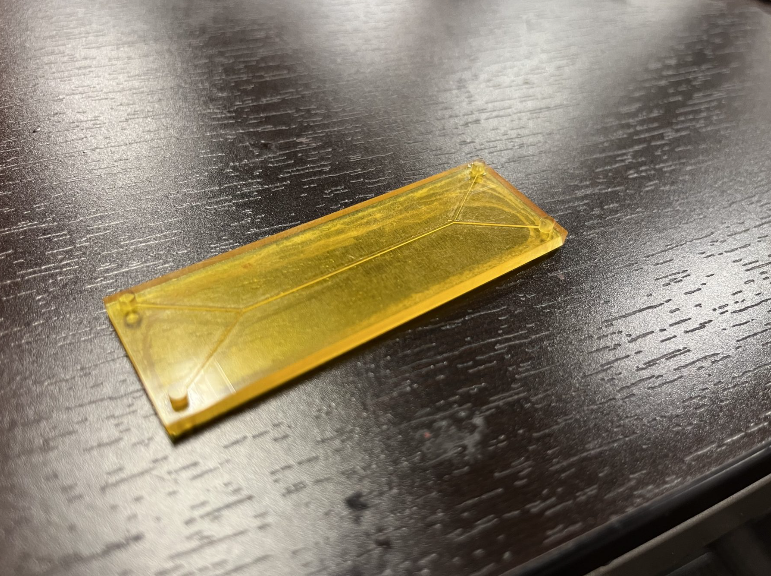
3D Printed PDMS Mold. Image Credit: Boston Micro Fabrication (BMF)
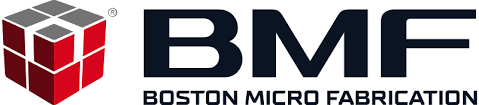
This information has been sourced, reviewed and adapted from materials provided by Boston Micro Fabrication (BMF).
For more information on this source, please visit Boston Micro Fabrication (BMF).