This article discusses the chemistry of additive manufacturing (AM) powders and the chemical analysis of raw ingredients, recycled materials, and feedstocks. To physically characterize these powders, it is crucial to consider the most suitable and relevant ways to do so.
When evaluating powders for any application, whether the properties of the constituent particles or those of the powder bulk define the performance should be considered. Powders are three-phase constructions, comprised of solid particles, liquid (usually water present at relatively low levels), and gas (typically air).
Frequently, there is good reason for measuring particle properties such as shape and size, but characteristics like spreadability and flowability are more closely associated with the bulk powder and are subsequently affected by interactions between all three phases.
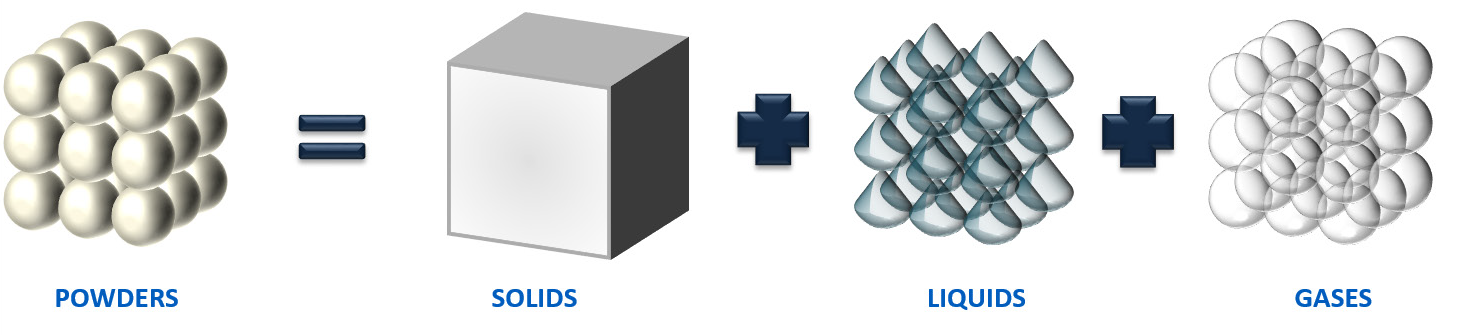
Figure 1. Powders consist of solid particles, liquid and air; bulk properties such as flowability are a function of the interactions between all three phases. Image Credit: Micromeritics Instrument Corporation
Focusing on Particle Properties
Particle size is frequently considered to be a defining characteristic of a powder. It is often included in AM powder specifications and directly affects many aspects of performance.
For example, Figure 2 displays the effect of particle size on sintering performance for a metal part produced via Binder Jetting (BJ). The finer powder sinters at a lower temperature and over a narrower temperature range, which reduces the probability of slumping and dimensional distortion.
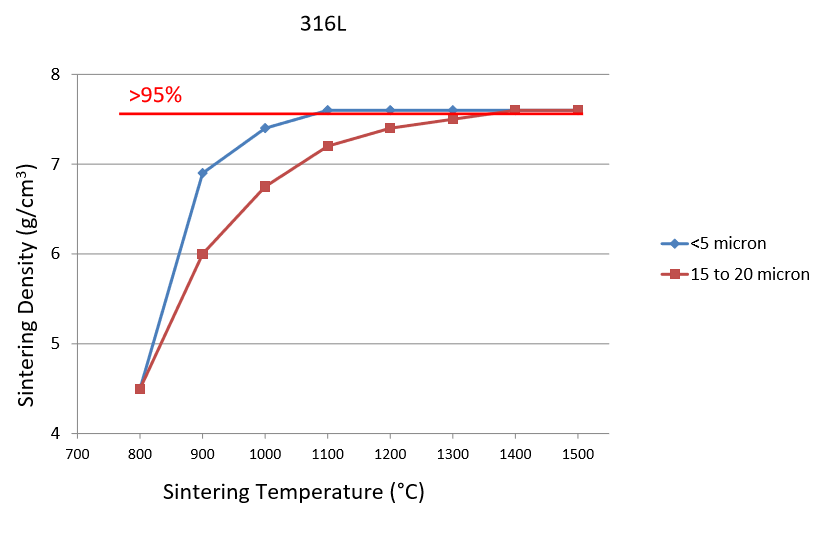
Figure 2. Finer metal particles sinter over a lower, narrower temperature range than coarser particles, which can be advantageous in BJ processes. Image Credit: Micromeritics Instrument Corporation
Finer grains are typically associated with lower energy inputs and less aggressive conditions for sintering and melting. This is a significant characteristic of all AM processes that utilize considerable heat input.
Particle size directly affects a powder’s packing density. The relationship between particle size, or particle size distribution, and packing performance is displayed in Figure 3.
Finer particles can pack together more closely than coarser analogs, and to attain maximum packing density, a broader particle size distribution is advantageous compared to a very narrow one because finer particles pack in the spaces formed by larger particles.
During the printing processes, relatively fine powders with an optimized particle size distribution yield the uniform layers of powder necessary for finished products of consistent quality with few flaws.
Shape is another important particle property. More regularly shaped particles can pack more easily than less regular analogs of an equivalent size. High sphericity is also desired in AM powder supplies, although smooth spherical particles may only sometimes be beneficial for optimal performance.
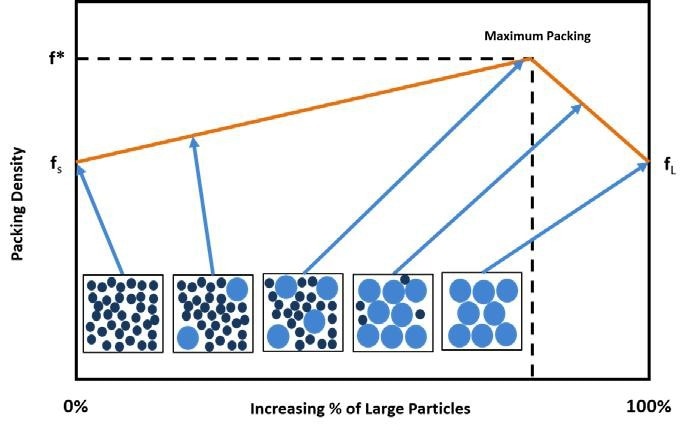
Figure 3. Finer particles pack more closely than coarser particles with a relatively broad particle size distribution required for maximum packing density. Image Credit: Micromeritics Instrument Corporation
The Importance of Bulk Powder Properties
Powder flowability is a critical variable to the performance of powders in all AM processes. It is regularly associated with particle shape and size. Fine particles are often linked to relatively poor flowability, and high sphericity is typically advantageous to powder flow.
However, powder flowability is not only impacted by particle size and shape, but also many other parameters via an array of mechanisms, as shown in Figure 4. Other relevant particle properties include porosity, stiffness, density, surface texture, and electrostatic charge.
Powder flowability is a function of ‘system variables’, such as the degree of aeration or the amount of moisture present. This complexity means that predicting powder flowability from only particle properties is difficult.
The quantification of bulk powder behavior is ideally conducted under conditions that closely replicate the process environment, avoiding the need to infer behavior from non-representative data.
In practice, quantifying the required flowability to print powders successfully relies on measuring bulk powder properties.
These measurements must be recorded under conditions that reflect a printer's stress and flow regimes. These are very clear requirements for a system for powder flow testing to add to the AM powder characterization toolkit.
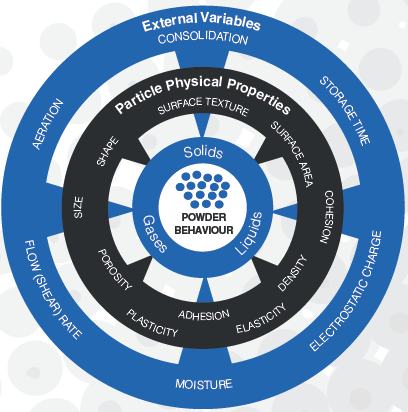
Figure 4. Bulk powder properties are defined by complex interactions between the three phases of a powder. Image Credit: Micromeritics Instrument Corporation

This information has been sourced, reviewed and adapted from materials provided by Freeman Technology.
For more information on this source, please visit Freeman Technology.