Contamination, comingling, mislabeling, and using improper lubricants can all result in equipment performance degradation or failure.
Viscosity is the most sensitive physical property of a lubricant. Using the product certificate of analysis (COA) and viscosity-grade specifications and a new class of field-capable viscometers enables contamination to be detected.
Problem Summary
Lubricants pass through many hands, conveyance systems, and containers while moving from manufacturer to end user. Tracking the complete trail of the lubricant may be complicated.
Numerous off-loadings and transfers result in many opportunities for comingling, contamination, and uncertainty through transfer lines, tanks, drums and totes, pumps and filters, and mislabeled containers.
Many manufacturers and distributors utilize dedicated tanks and lines for each lubricant product. If this is not the case, the tanks and lines must be cleaned each time a product is switched to another.
The cleaning process involves flush oil being passed through the lines to confirm that the previous product does not contaminate each product. “Line Flushing” is not an exact science and can result in commingled or cross-contaminated lubricants.
Lubricants consist of a complex blend of base oils and specialty additives. They must meet strict performance specifications, and some examples include ISO VG industrial lubricants, SAE gear oils, hydraulic fluids, and SAE motor oils.
There are different classes of lubricants, with each class intended for a specific purpose. These are typically not compatible with one another because of differences in additive chemistries.
Each class of lubricant has multiple grades, mainly varying in viscosity, such as ISO VG 32, 46, and 68, and 5W-30, 10W-40, and 15W-40.
Lubricants are required to meet strict specifications, including those of the American Society of Testing and Materials (ASTM), International Standards Organizations (ISO), and the Society of Automotive Engineers (SAE).
These standards define the exact physical property limits for each grade, as well as detail the correct laboratory test method and type of instrumentation that must be used. Outside of numbers in a test report or table, most lubricants are not visibly distinguishable from each other.
Formulated lubricants have complex blend chemistries. Lubricants have more than just a simple base oil in the blend, whether it is an ISO VG industrial lubricant, SAE gear, automotive, or heavy-duty engine oil.
Most contain many additives for anti-foam and corrosion inhibitors to improve low-temperature flow ability or to provide high-temperature stability of viscosity and oxidation. When together, they are usually incompatible with each other.
Most bulk and industrial oil deliveries are accompanied by a Certificate of Analysis (COA). For example, the American Petroleum Institute (API) Standard 1525A demands a COA and chain-of-custody documentation.
Manufacturers of lubricants test the oils in their labs and produce the COA to guarantee that the oil meets the required specifications before the product is transferred to the distributor.
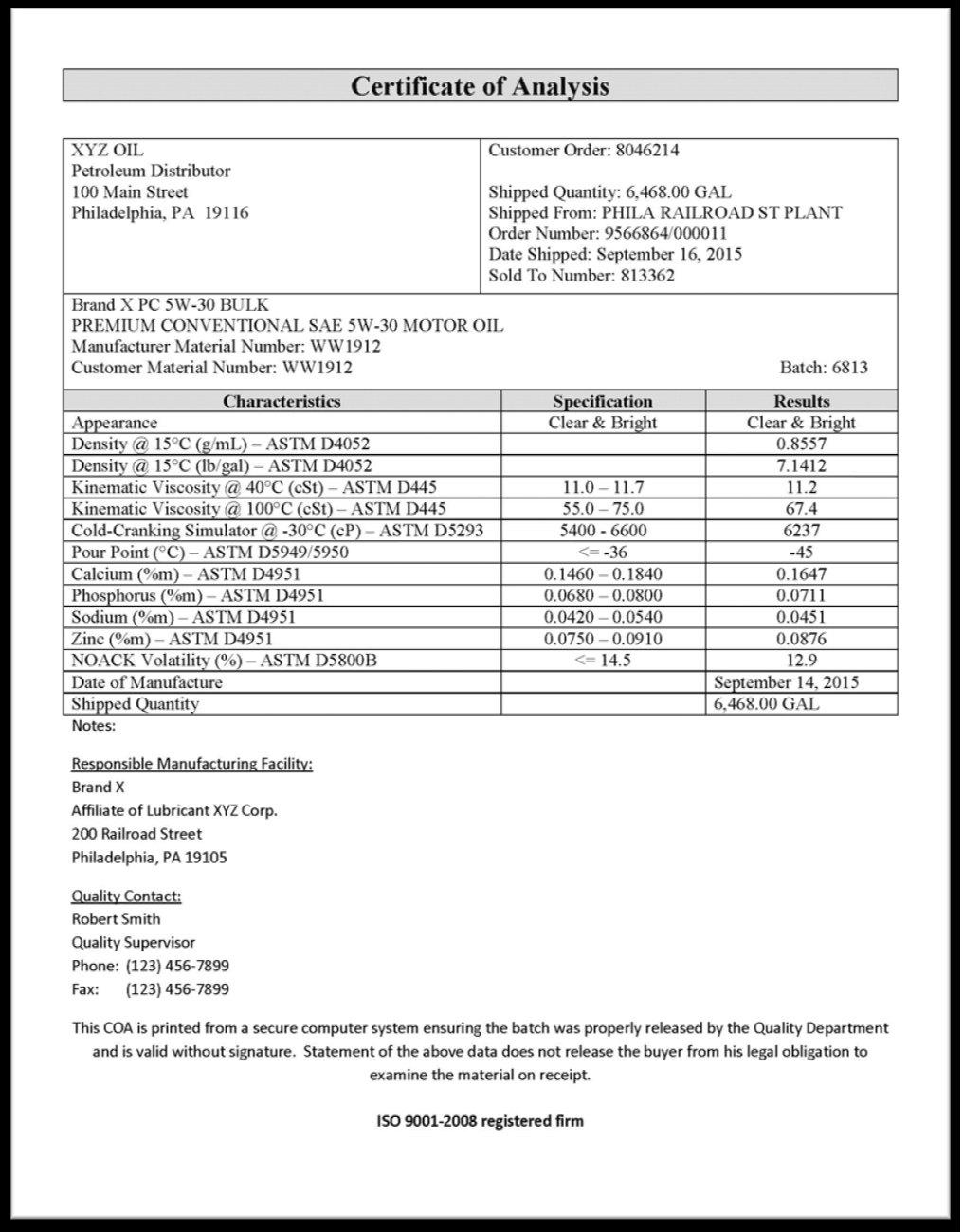
Image Credit: Cannon Instrument Company®
Finding the Solution
To the human eye, most oils appear alike, except for differences in the relative viscosity or thickness. Additionally, the same oil may vary in color if it is produced in different lots.
Comparing the lubricant viscosity against its original viscosity specification is the only reliable method to determine if a lubricant is correct.
Source: Cannon Instrument Company®
SAE J300 Multi-grade Engine Oil |
Minimum Kinematic Viscosity in mm2/s at 100 °C |
Maximum Kinematic Viscosity in mm2/s at 100 °C |
xW-16 |
6.1 |
<8.2 |
xW-20 |
6.9 |
<9.3 |
xW-30 |
9.3 |
<12.5 |
xW40 |
12.5 |
<16.3 |
xW-50 |
16.3 |
<21.9 |
xW-60 |
21.9 |
<26.1 |
Note: “x” denotes either 0, 5, 10, 15, 20, or 25 as in 0W-5, 5W-30, 15W-40.
Formulated lubricants are required to satisfy multiple physical property specifications when manufactured. These properties differ by the lubricant use, grade, and purpose.
The most common properties include density, kinematic viscosity, flash point, and pour point. Of these, kinematic viscosity is the most sensitive to small amounts of contamination, making it the ideal parameter for determining whether a product is truly what it is labeled as.
What is Viscosity?
Viscosity is a physical property of a fluid that defines its resistance to flow under certain conditions, such as the temperature of the fluid, and the type and amount of force applied to cause it to move.
For example, in the case of a gearbox, this may be the pressure between two mating gear teeth attempting to move the oil out of the way while the gearbox is at operating temperature.
Kinematic viscosity measures a fluid’s resistance to flow under the influence or force of gravity, measured in Centistoke (cSt) or mm2/s.
A standard kinematic viscometer is comprised of a capillary tube attached to a reservoir. Viscosity is determined by measuring the time required for a specified volume of oil to flow through the capillary restriction below it, from point A to point B (as shown in Figure 1).
Fluids with low viscosity flow quickly while those with high viscosity flow more slowly. Kinematic viscosity is calculated by the following formula:
Kinematic viscosity = flow time x calibration constant of the viscometer.
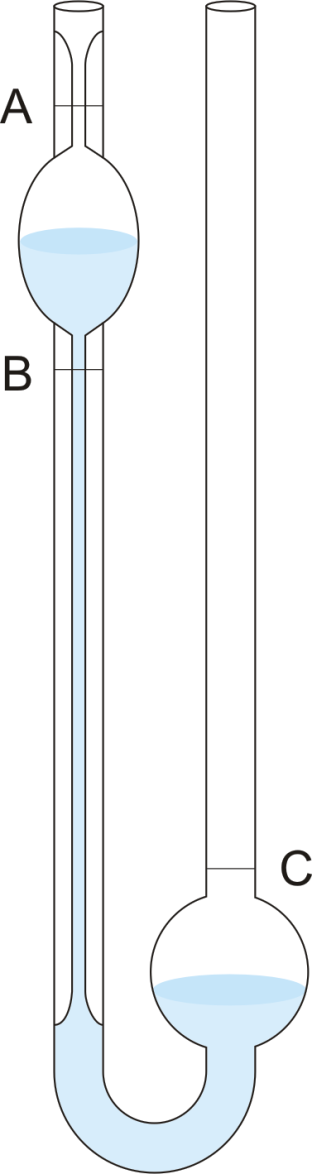
Image Credit: Cannon Instrument Company®
The majority of lubricants are graded based on kinematic viscosity. There are spaces between grades to allow for the determination of an incorrect lubricant by verifying if the viscosity is within the limits for its grade. This is the only physical property specification for lubricants that offers such an opportunity to identify an error.
ISO VG Oil Viscosity Limits by Grade
Source: Cannon Instrument Company®
ISO Viscosity Grade Oil |
Minimum Kinematic Viscosity in mm2/s at 40 °C |
Maximum Kinematic Viscosity in mm2/s at 40 °C |
ISO VG 2 |
1.98 |
2.42 |
ISO VG 3 |
2.88 |
3.52 |
ISO VG 5 |
4.14 |
5.06 |
ISO VG 7 |
6.12 |
7.46 |
ISO VG 10 |
9.00 |
11.0 |
ISO VG 15 |
13.5 |
16.5 |
ISO VG 22 |
19.8 |
24.2 |
ISO VG 32 |
29.8 |
35.2 |
ISO VG 46 |
41.4 |
50.6 |
ISO VG 68 |
61.2 |
74.8 |
ISO VG 100 |
90.0 |
110 |
ISO VG 150 |
135 |
165 |
ISO VG 220 |
198 |
242 |
ISO VG 320 |
288 |
352 |
ISO VG 460 |
414 |
506 |
ISO VG 680 |
612 |
748 |
ISO VG 1000 |
900 |
1100 |
ISO VG 1500 |
1350 |
1650 |
ISO VG 2200 |
1980 |
2420 |
ISO VG 3200 |
2880 |
3520 |
Note: ISO VG 10 through ISO VG 680 are the most widely used in industrial applications
Choosing the Correct Temperature
As temperature increases, the viscosity of petroleum increases. When observing the viscosity of ISO VG lubricants, the difference in viscosity between adjacent oil grades is around 50% at 40 °C, and decreases to only 30% at 100 °C.
At 40 °C, the difference in minimum kinematic viscosity between ISO VG 100 and ISO VG 150 oils is 45 cSt (50%). However, at 100 °C, the difference is only 3.90 cSt (33%).
ISO VG Kinematic Viscosity Limits at 40 °C and 100 °C
Source: Cannon Instrument Company®
ISO VG Grade |
KinVis, mm2/s |
Specification |
Calculated* |
40 °C |
100 °C |
min |
max |
min |
max |
2 |
1.98 |
2.42 |
~0.50 |
|
3 |
2.88 |
3.52 |
~1.00 |
|
5 |
4.14 |
5.06 |
~1.50 |
|
10 |
9.00 |
11.00 |
2.58 |
2.93 |
15 |
13.50 |
16.50 |
3.34 |
3.78 |
22 |
19.80 |
24.20 |
4.24 |
4.79 |
32 |
29.80 |
35.20 |
5.34 |
6.09 |
46 |
41.40 |
50.60 |
6.79 |
7.77 |
68 |
61.20 |
74.80 |
8.86 |
10.23 |
100 |
90.00 |
110.00 |
11.68 |
13.47 |
150 |
135.00 |
165.00 |
15.58 |
17.93 |
220 |
198.00 |
242.00 |
20.35 |
23.38 |
320 |
288.00 |
352.00 |
26.38 |
30.34 |
460 |
414.00 |
506.00 |
33.93 |
38.93 |
680 |
612.00 |
748.00 |
44.29 |
50.67 |
1000 |
900.00 |
1100.00 |
57.34 |
65.45 |
1500 |
1350.00 |
1650.00 |
74.82 |
85.15 |
2200 |
1980.00 |
2420.00 |
95.70 |
108.60 |
3200 |
2880.00 |
3520.00 |
121.05 |
136.90 |
*Assuming a VI of 120
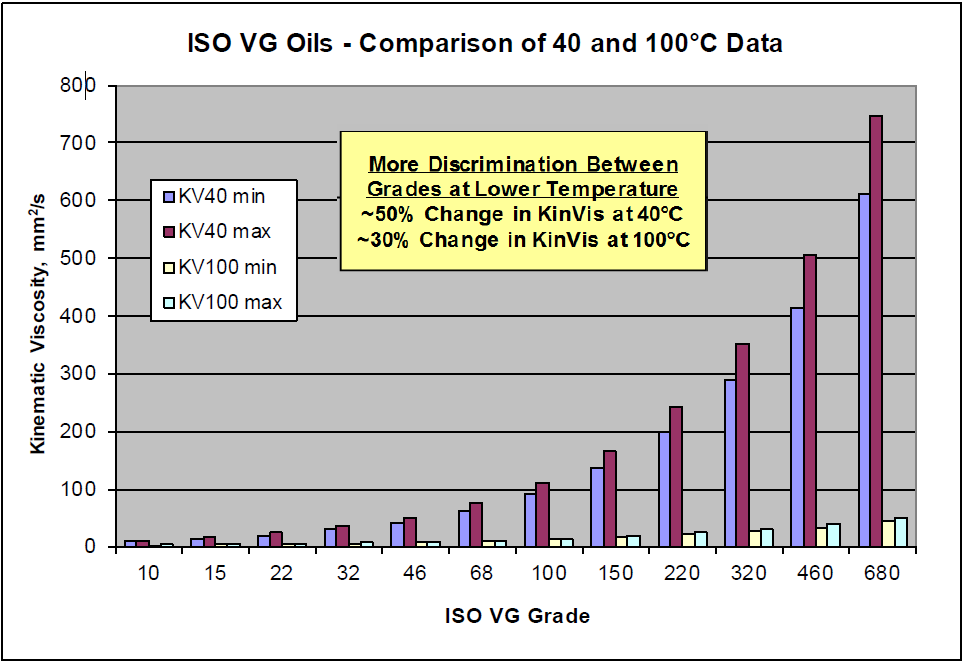
Image Credit: Cannon Instrument Company®
Choosing the Correct Temperature
The greater the separation of viscosity between grades, the higher the probability of accurately determining the grade of lubricant. For ISO VG oils, the suggested temperature is the specification temperature of 40 °C.
This is the optimal temperature for detecting when most lubricants are “out of grade” or out of specification, due to the differences in viscosity (separation) between adjacent grades being the greatest at this temperature.
Finding the Solution
For most industrial users, verifying a lubricant against its COA for all specification properties demands sending the oil to a third-party testing laboratory. When there are multiple lubricants involved, this becomes a timely and costly process.
Verifying the lubricant against its viscosity specification alone enables the user to determine if a lubricant is the correct grade. While viscosity will not offer information regarding how it was contaminated or mislabeled, it will determine if the product is not the correct grade.
Historically, making accurate field viscosity measurements has been a challenge for industrial lubricant users. Accurate measurements of viscosity have traditionally required sensitive and costly laboratory instruments.
The lubricant oil industry is reliant on a standardized test methodology (ASTM D445) for assessing the viscosity of lubricants throughout the processes of formulary design, blending, and bottling. However, D445 viscometers are costly and demand laboratory environments and trained technicians for their operation.
Most industrial users do not have labs, the capital to invest in lab-grade instruments, or the required trained lab personnel. Simplistic viscosity comparators have always had accuracy limitations, which makes them inadequate for the detection of even moderate differences in viscosity.
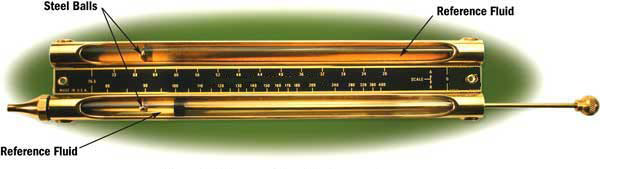
Image Credit: Cannon Instrument Company®
The inaccuracy in a comparator-type viscometer is mostly due to a lack of thermal control of the sample. The reference fluid (typically a base oil) is different from the formulated lubricant that it is being compared against.
Petroleum products have a highly sensitive viscosity to even minor changes in temperature; the viscosity changes by 2% per 1 °C change in temperature. This rate of change (or slope of viscosity versus temperature) is defined by ASTM as the Viscosity Index (VI).
Most industrial ISO VG lubricants have a VI between 100 and 120. However, modern engine oils may have a VI of at least 150, with that of some synthetics being 250. The higher the VI number, the greater the changes in viscosity as the temperature changes.
The error in measurements by a viscosity comparator increases significantly as the difference in VI increases between the test sample and the reference fluid.
A new class of quick, accurate, and simple-to-use field-capable viscometers has addressed the above issues, with built-in temperature management of the sample to precise temperatures at 40 °C or 100 °C, ± 0.05 °C.
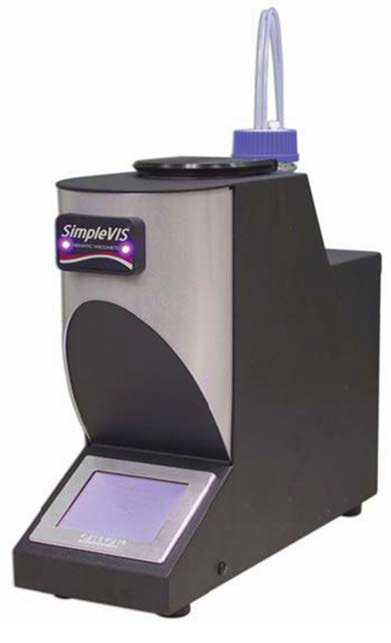
Image Credit: Cannon Instrument Company®
This provides lubricant distributors, plant maintenance personnel, and field service technicians with an affordable new tool to identify a lubricant, as well as any contamination or commingling.
Knowing precisely what lubricant is being installed in a piece of machinery is crucial to the health of the machine. The likelihood of having an incorrect lubricant or a different grade in a container or drum is a real-world problem.
The only solution is field testing of the lubricant’s viscosity. New field-capable viscometers allow the viscosity of a lubricant to be tested before it is installed, in a quick, easy, and accurate manner.

This information has been sourced, reviewed and adapted from materials provided by Cannon Instrument Company®.
For more information on this source, please visit Cannon Instrument Company®.