SRAM creates and manufactures high-quality and innovative bicycle products, such as hubs and gears, for both amateur cyclists and professional athletes.
To assess the quality of bicycle components for prolonged usage and optimize their performance, SRAM conducts both dynamic and static testing. For these tests, ZwickRoell testing machines have been used by the bicycle component manufacturer for over 15 years.
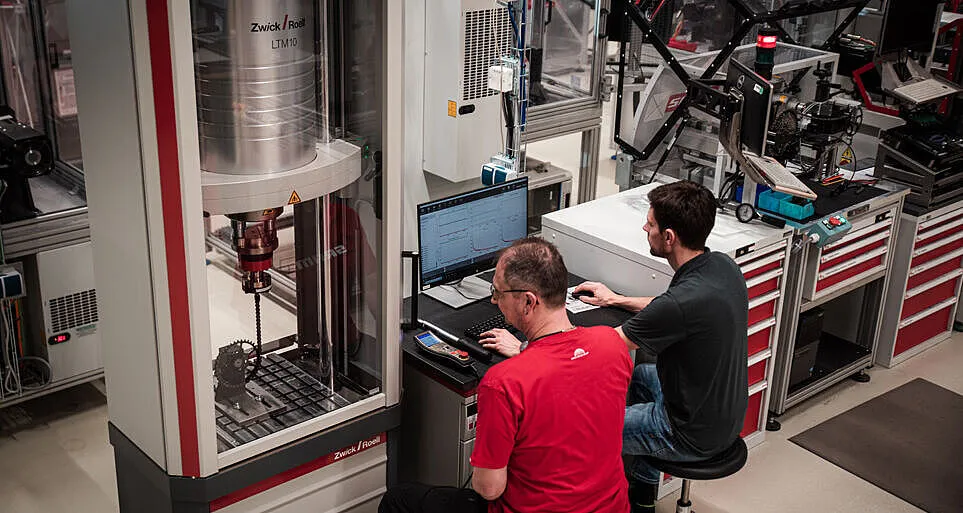
Images: copyright SRAM
Founded in 1987, SRAM is a US-based company headquartered in Chicago, Illinois. It specializes in the development and manufacturing of different bicycle components. At SRAM’s development site in Schweinfurt, Germany, SRAM Deutschland GmbH develops bicycle hubs and gears for cycling fanatics around the world.
Schweinfurt serves as the central location for development and prototyping. It also houses the measurement and testing laboratories—“all under one roof,” explains Martin Kehrer, Senior Test Engineer at SRAM.
As a result, the company is strategically positioned to swiftly and efficiently “develop innovative products quickly and efficiently and continue exciting cyclists all over the world” through faster processes.
To some extent, ZwickRoell testing machines contribute to these efforts. By using various static and dynamic machines, SRAM Deutschland GmbH has notably become more capable of developing innovative and reliable products, delivering added value to its customers.
SRAM: Dynamic and Static Testing with Zwickroell
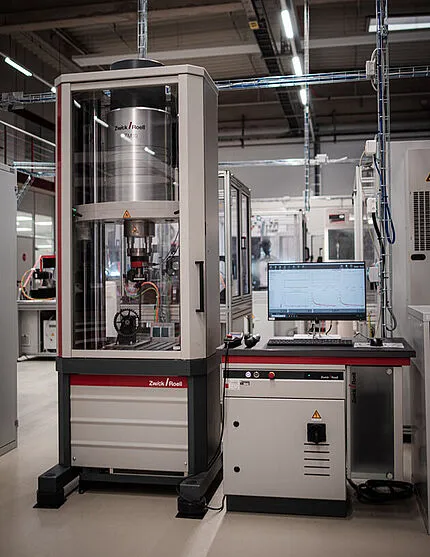
ZwickRoell LTM10 in the test environment (Images: copyright SRAM)
The testing laboratory in Schweinfurt conducts both dynamic and static tests on different bicycle components, demanding a high level of flexibility from the machines. At present, SRAM’s testing equipment consists of three ZwickRoell machines:
- A servohydraulic machine HC 25, utilized for dynamic and static testing
- The latest addition, an electrodynamic testing machine LTM 10
Dynamic testing at SRAM is primarily conducted at a component level to assess their operational durability and suitability. The components are then optimized based on the test results to enhance their robustness and to better align them with specific customer requirements.
Laboratory Efficiency: Up to 80 Percent Faster
The utilization of the ZwickRoell machines not only results in quality improvements within SRAM’s laboratory but also guarantees better performance in terms of process optimization.
Previously, certain tests were transferred from dedicated and, sometimes, aging testing machines to ZwickRoell testing machines, resulting in enhanced efficiency and “reducing test times by up to 80 percent.”
“All this took place with simultaneous optimization of the testing accuracy and improved crack detection on the specimens,” says Kehrer.
ZwickRoell testing machines are also utilized for validating finite element method (FEM) models. This widely used method in materials testing simulates and examines the mechanical response of materials under different loads.
FEM is also applied to assess material fatigue or damage, factoring in both static and dynamic loads. The adoption of FEM enhances the efficiency and cost-effectiveness of materials testing by eliminating complex and expensive experiments.
“The ability to interchange fixtures between the different machines provides us with more testing flexibility in the lab. At the same time, this leads to significantly better machine utilization,” says Kehrer.

Test arrangement for a fatigue strength test on a bicycle chainring. Image Credit: SRAM
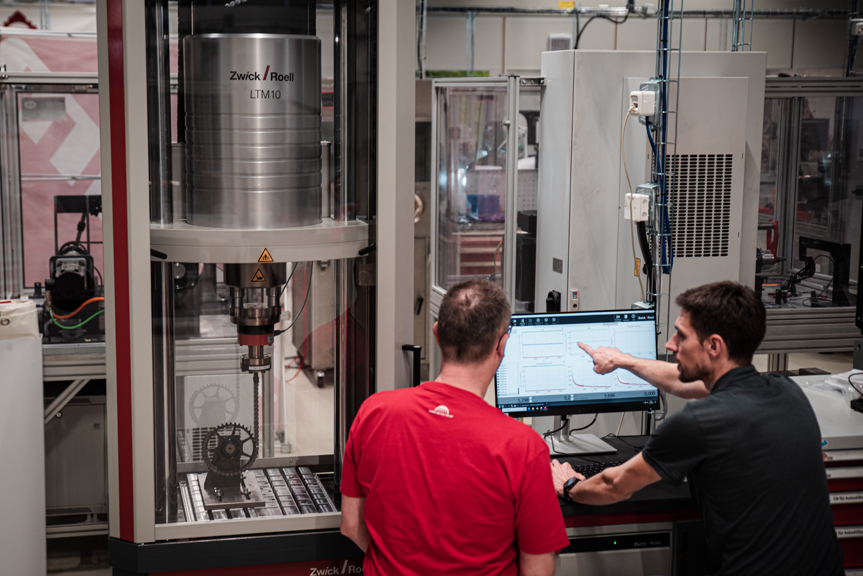
Analysis of the machine data during the test. Image Credit: SRAM
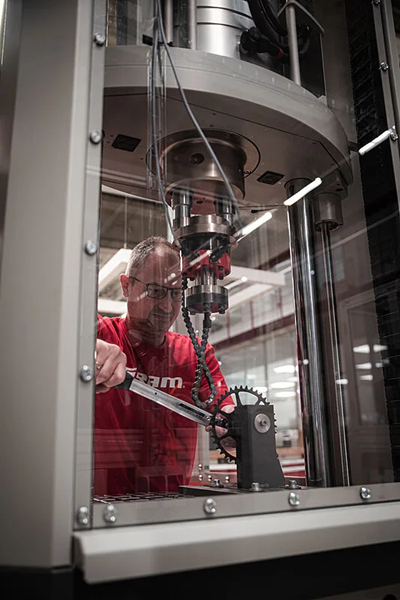
Test arrangement for a fatigue strength test on a bicycle chainring. Image Credit: SRAM
Testing with Zwickroell for Over 15 Years
For more than 15 years, SRAM Deutschland GmbH has been utilizing machines from Ulm-Einsingen and has been a contented ZwickRoell customer throughout this period.
Kehrer explains, “The static machine Z010 was our first ZwickRoell machine. And since then, we have, of course, added more machines. The reliability and precision during our product qualification process, as well as the level of customer service, convinced us from the start.”
SRAM produces the fixtures and sensors for all component tests within the prototype shop of the company.
Following the acquisition of the LTM10 in 2022, all machines were moved to ZwickRoell’s testXpert III testing software. This software significantly supports users in the laboratory, simplifying different tasks by offering a broad range of standards and pre-configuring suitable parameters based on customer-specific applications.
“Through testing, we are constantly learning and improving our products and adapting to new requirements, which ultimately also benefits our cycling-enthusiastic customers,” states Kehrer.
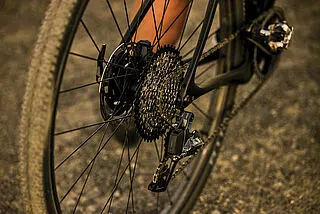
Electric SRAM Eagle AXS transmission groupset (Images: copyright SRAM)
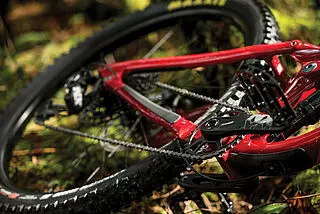
Mechanical SRAM Eagle transmission groupset. Image Credit: SRAM
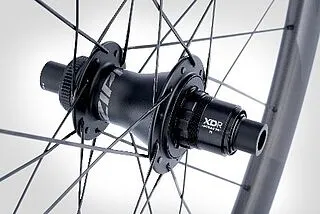
SRAM develops the Zipp hubs in Schweinfurt, Germany. Image SRAM
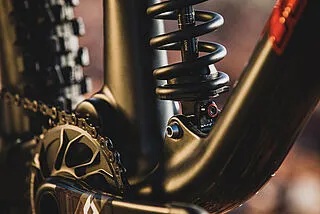
The SRAM Eagle chainrings are developed in Schweinfurt, Germany. Image Credit: SRAM
Quality Testing on Bicycle Tires: Schwalbe Relies on Know-How from ZwickRoell
As an eco-friendly, sustainable, and emission-free mode of transportation, the bicycle is gaining increasing popularity. Whether it is an e-bike, mountain bike, racing bike, cargo bike, or touring bike, you can now find the perfect bicycle equipped with optimal tires.
As various applications for bicycles emerge, the demand for high-quality and durable bicycle tires rises. As a result, Ralf Bohle GmbH, tests with ZwickRoell machines to simulate the diverse challenging loads, because nobody wants a flat tire.
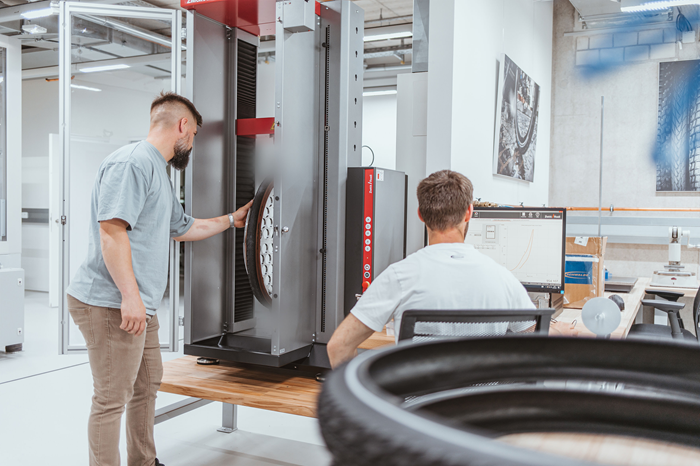
Image Credit: SCHWALBE
Ralf Bohle GmbH
Ralf Bohle GmbH, primarily known by the Schwalbe brand, is a leading German manufacturer of bicycle tires, tire tubes, and accessories, that are distributed globally.
Established in 1922 and headquartered in Reichshof Wehnrath, Germany, the company offers an extensive product portfolio with a diverse range of specialized tire models that are individually designed to meet different cyclist requirements.
Renowned for its high-quality tires, Schwalbe incorporates innovative technologies such as the SmartGuard tire protection system and the Tubeless Easy system for tubeless tires.
To guarantee that all Schwalbe tires meet the highest and, at times, changing quality standards, comprehensive tests are performed in Schwalbe’s state-of-the-art laboratory during the pre-launch phase, as part of the company standard.
These laboratory tests are complemented by rigorous practical application tests before the product development for the Schwalbe brand receives final “market-ready” approval for the launch.
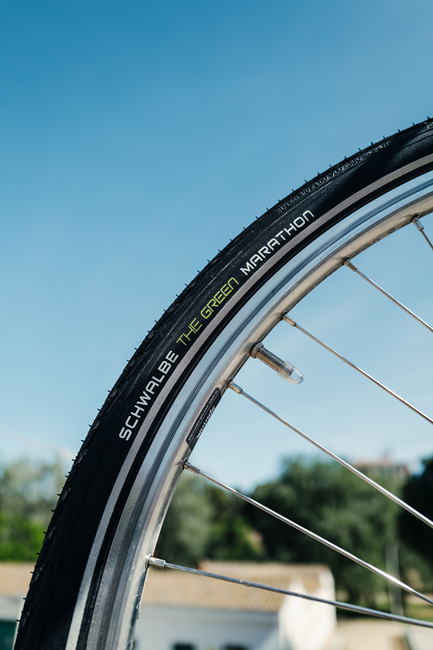
The first bicycle tire made from used tires: Green Marathon from Schwalbe. Image Credit: ZwickRoell GmbH Co. KG
Tires: The Requirements in Terms of Quality Continue to Rise
Cargo bikes have a wide range of applications and must therefore meet strict demands—especially considering that these bikes can weigh up to 70 kilograms when unloaded.
The requirements in terms of quality are multifaceted: tires must be simultaneously stable, dependable, and comfortable, both in loaded and unloaded conditions. This is how Schwalbe conducts these tests: the tire system, along with the wheel, is secured in a specialized fixture.
Numerous forces are then simulated and applied to the system through the testing machine. The tire contact area is recorded, and a corresponding force/travel diagram is developed.
To thoroughly assess the durability of all materials, the testing machines are exposed to extreme demands, operating at maximum performance. Additionally, the laboratory conducts puncture tests on tires and tire tubes to assess their quality.
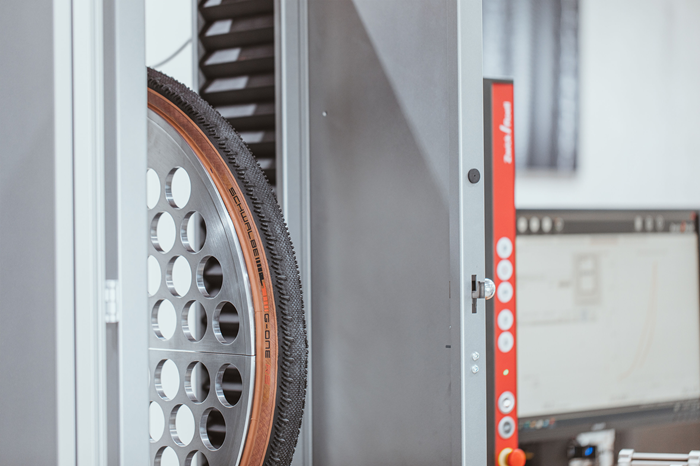
A tire is tested using a ProLine Z030 materials testing machine. Image Credit: SCHWALBE
Schwalbe: Improving Products with Zwickroell
“Quality, reliability, and accuracy of test results are very important to us when it comes to the testing machines we use. As a premium manufacturer, our goal is to develop high-quality products that set standards,” explains Sascha Ochmann, Laboratory Manager at Schwalbe.
This consideration was one of the main reasons why the company decided to use ZwickRoell machines for their tests. Recently, the company ordered a ProLine 30 kN materials testing machine.
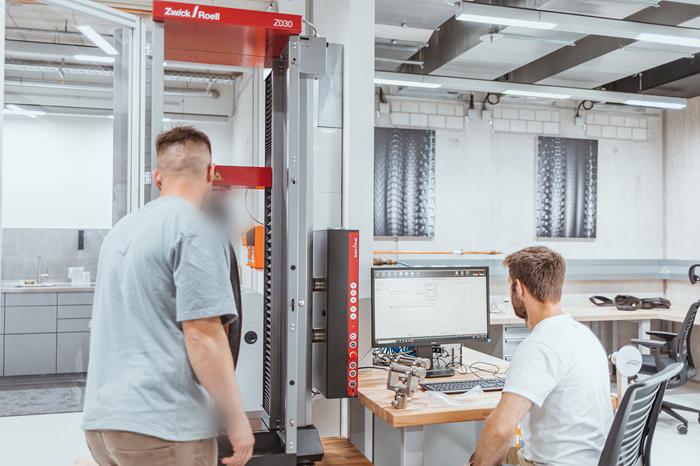
Schwalbe test engineers prepare a test. Image Credit: SCHWALBE
Our challenge in the laboratory is to apply correspondingly high loads and to document the test results in a traceable and reproducible manner. We want to provide our customers with exciting quality products and therefore rely on ZwickRoell testing machines to help us deliver our promise time and time again. And in terms of IT support, connection to our quality management system, as well as intuitive control or the simple software structure of testXpert, the testing solutions have continued to impress us.
Sascha Oschmann, Testing Laboratory Manager at Schwalbe
Schwalbe Uses Proline 30 kN Materials Testing Machine
The commissioning of the ProLine 30 kN materials testing machine has enabled Schwalbe to achieve significant improvements.
“On the one hand, the workflow is now much more convenient and the test results have become more accurate. On the other, our testing laboratory now has greater insight into how a tire behaves under high loads, which provides engineers and developers with important information and allows them to draw conclusions for quality assurance and continuous improvement of Schwalbe brand bicycle tires,” Ochmann concluded enthusiastically.
In the end, quality benefits cyclists, regardless of whether they ride e-bikes, racing bikes, touring bikes, mountain bikes, or cargo bikes. Ochmann says, “Nobody wants to break up their ride because of a flat tire!”
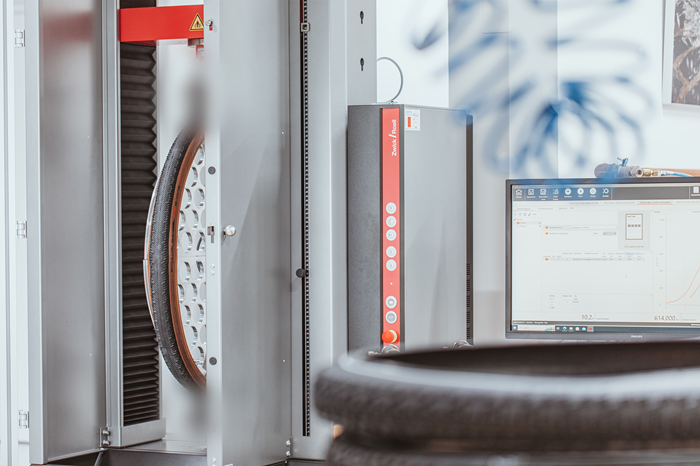
A Schwalbe tire is tested in the ProLine Z030 material testing machine from ZwickRoell. Image source/copyright: SCHWALBE
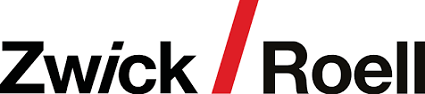
This information has been sourced, reviewed, and adapted from materials provided by ZwickRoell GmbH Co. KG.
For more information on this source, please visit ZwickRoell GmbH Co. KG.